Introduction: Caldera Table
The undisturbed planar surface of the table top provides a starting point for intervention with the Caldera Table. Typically of a constant depth, the extruded top literally offers little room for play. By introducing a grouping of volumetric aberrations which deform not only the top surface, but also bloat the 'interior' space, Caldera exposes a deep interior dimension.Amplifying these distortions further is a set of unfamiliar inserts which sit within the craters nearly perfectly. At first the paired formations may seem functionally ambiguous, but by simply removing and flipping the lids to rest on their stubby protrusions one reveals a smooth convex underside and potential for any number of uses.
In terms of fabrication, the Caldera Table was used to explore precise double-sided milling, a variety of toolpathing / operations, and interface or joints between complex parts.
Step 1: Overview
Tools/Materials:
8/4 Walnut 6061
Aluminum
Mild steel
Various hardware
DMS Mill (for wood)
HAAS VF2 (for metal)
Scotchman cold saw
TIG welder
Various sanding and finishing tools and supplies
I wanted to pursue several projects when I began my residency at Pier 9 with one of them being an exploration into the interface between multiple materials, while maintaining formal continuity (ideas I began exploring in some previous projects - the VICE Table and STALASSO Table) While the options for exploring this idea are varied and many, I wanted to give myself a few constraints - I wanted to keep it small-ish so I could get more into the details/finish instead of spending a lot of time on dealing with moving/storing a large piece while I worked and I really wanted to do what I could in-house at Pier 9 rather than outsourcing certain aspects (i.e. - the insert/bowl on the STALASSO table was printed through Shapeways). I had done a few projects on the HAAS VF2 and I wanted to incorporate it’s capabilities as well as the DMS 5-Axis router - a machine I hadn’t yet used at the time I began this project.
Step 2: Pre-design / Testing
I had some loose ideas of what I wanted to explore formally - so I began sketching ideas and testing techniques in Rhino and diagramming and writing in my sketchbook. I began to develop a workflow that began parametric design aspects, but then used ‘manual’ 3D modeling to get the forms perform the way I wanted. Initially ideas centered around a ‘nesting’ of parts/functions - a matryoshka concept under the ‘surface’ and within the volume of the table. For numerous reasons this ‘nesting’ idea evolved into a series of more refined ‘craters’.
<iframe allowfullscreen="" frameborder="0" height="315" src="//www.youtube.com/embed/73KMPUm0b5E" width="560"></iframe><br>
Once I was headed in a satisfactory direction, I ran some milling tests in foam on the DMS to get a feel for the particulars of this beast of a machine. It’s notoriously finicky and if I was to run into any issues I wanted it to be in foam rather than in an expensive hardwood! I also wanted to test a few different machining roughing and finishing operations - i.e. parallel passes for the top surface vs. contouring within the ‘craters’. I also wanted to try out some 3+2 milling to potentially get at deeper and more complex geometries (it was a good test since the 3+2 portion wasn’t able to be machined since the new dust collection hood on the DMS head was too bulky and would have been damaged with the way I had the stock setup on the bed - the collector would have been damaged on the bed of the machine! That’s why you run tests though and why you always need to keep a close watch on your job!)
Step 3: Stock Prep
Before getting to any sort of final design, I wanted to get my material/stock so I knew what thickness, length, width, etc. I had to work with. After a trip to MacBeath Hardwood, I had a beautiful 8/4 16” wide plank of American Walnut. After a fellow resident took a share of the board and I had measured the remaining piece (there were a few blemishes in the wood I needed to work around) I now knew what i had to work with. I then modeled a blank stock volume to work within. There was some back and forth between 3D modeling and machining (joining, planing, and sawing) before I was at a point where I was ready to glue up the final parts. I won't go into the biscuit joining, planing, gluing and clamping here as it was pretty straightforward and standard practice. What wasn’t standard was the overall configuration of the stock assembly - I wanted to limit the amount of milling time and material waste, so I glued extra pieces of stock only at the areas of the design where extra depth was needed. This made the milling process more effienct, but setup of both the toolpathing and the physical clamping of the workpiece much more difficult.
In between the glue-up of the stock pieces, I was finalizing the geometry of the table top to fit within the stock bounds but still maximize the features I was interested in foregrounding. Once that was done, I was ready to setup my toolpathing. I won’t go into the specifics of this either as I made an instructable on the general use/overview of HSM for Inventor. One point worth making now is that I didn’t yet have a base/frame fully designed, but I wanted to accommodate a way to mount to the table top. I modeled 4 dowel holes that I could just mill out for future frame mounting potential.
Step 4: Milling the Top
Milling the wood on the DMS was relatively straightforward and there were no major setbacks. There was probably a total of around 4 - 5 hours of actual machine time with another 4-5 hours of total setup, fixturing, cleanup, etc. This made for one long day of milling, but it was worth it in the end!
<iframe allowfullscreen="" frameborder="0" height="315" src="//www.youtube.com/embed/RHWYmzW_qlQ" width="420"></iframe><iframe allowfullscreen="" frameborder="0" height="315" src="//www.youtube.com/embed/X3mdH7caANs" width="420"></iframe><br>
Step 5: Sanding
I used a pretty fine stepover (.015”) on my surface finishing passes so sanding was pretty easy - a combination of random orbit (on the flat parts) and hand sanding (on the organic forms) with grits ranging from 180 to 320 did a nice job. 2 applications of tung oil achieved a nice satin finish. While the CNC mill took the wood to a pretty good level of finish, there were parts at the edge where there was some tear-out. This was due to the design of some pretty fine corners/edges. I could have done more to alleviate this by building a more complete workpiece holding fixture, but I didn’t have much time, so I dealt with the tear-out as best I could. One area in particular took more hand work , which wasn’t an issue in itself, it did mean that I needed to add in material to the 3D model of the ‘lids’ I was also designing to make up for the lost amount of wood. I’d have to reconcile the difference by hand when I was finishing the lids.
Step 6: Base Fabrication
Other than the angles/geometry, the base for this table is really standard/straightforward. It was easy enough to just get dimensions and angles from the digital model, make a cutlist, and cut the parts (on a cold saw) in a matter of an hour or two. Probably the most difficult aspect of the base fabrication was end drilling 17/64” holes into the ½” x ½” stock. It made for an interesting setup on the drill press, still it was not that hard to do. I added some tapped holes for set screws (for fine adjustment to the stainless dowels which plug into the table top). After that, basic TIG welding and grinding of the joints made for some clean joints. Lastly I gave the steel a black (birchwood Casey) patina and a clear lacquer coat for finish.
Step 7: Lid Design and Fabrication
While designing this table, I was working with two ideas for inserts or ‘lids’ which would fit/cover the openings in the table. One was a fairly simple ‘smooth’ design and the other slightly more complex with three protrusions each which would allow the lids to be used as concave trays or dishes when flipped. The nubby and slightly more functional design won out. In either design, fit was of utmost importance and the edge geometry that governed the interface between the tabletop and the inserts was quite irregular/complex. A substantial amount of time went into precise modeling of these edges and parts.
I tried to mill the design out of maple quickly one day, but the design and tolerance I needed proved a little too thin and fine for wood and the DMS. I ended up taking them to the HAAS and making them out of aluminum which was the original plan all along. The HAAS is incredibly rigid and precise. Aluminum is also better for milling a thin shell part from. However, this was still quite an endeavor as the parts I need to get were completely organic and had no parallel edges to clamp to. Without making any custom workholding tools I needed to design in tabs which would hold the parts in the stock as I machined material from around them. I would later cut and remove the tabs by hand.
The stock I used was a solid 2”x6”x24” solid 6061 aluminum. There still wasn’t too much clearance for the pieces though and this created a few issues where the tools I used were a bit large for removing all the material I wanted at the edges. Consequently, I had some material remaining that I had to remove manually. If I had extra time, or I was to mill similar parts in the future, I’d run a preliminary finishing pass with the larger tool and a final finishing pass with a smaller one to get into the smaller pockets. All those issues aside, the lids parted out of the stock fairly easily with a pneumatic reciprocating saw and cleaned up really nicely with a combination of pneumatic tools, files, and scotchbrite. It was with these manual processes that I was able to get the edges to match the area on the walnut where I had issues with tear-out.
Step 8: Lid Finishing
With the lids cleaned up and fitting well in their counterpart craters, they only needed a finish. I decided to have them clear anodized. The only issue was that anodizing requires clamps to hold the parts when they’re submerged and because of their freeform geometry, there were no good places to clamp to. A small pin point sized mark was left on each piece. Not a huge deal, but definitely a consideration.
Step 9: Conclusions
For the most part, this project turned out how I had hoped. It was an exciting and educational process. If I were to do it again, there would be several changes or modifications I could do to make it go a little smoother and require less finish work. This is the case however with most one-off or custom pieces where the prototype is the final piece! One can only really get better at surmising all the necessary steps or predicting hiccups in the process. I can’t wait to build on this project!
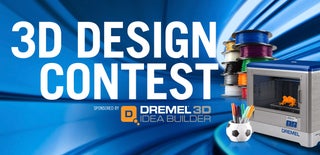
Participated in the
3D Design Contest
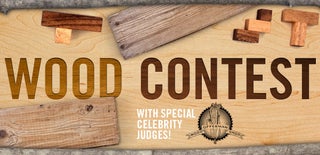
Participated in the
Wood Contest