Introduction: Candle Holder With Two Secret Compartments
This project started off as one thing and ended up as another. I am new to the lathe and I have been experimenting making different things on it. I wanted to try my hand at making a large vessel of some sort but wasn't sure what exactly to make, that is until I saw the Secret Compartment Challenge. I figured I would try making a simple stash box or some type of decorative container. I mentioned earlier this started off as one thing and ended up as another. I initially started making some type of urn looking piece, which I hated, so I let the project sit for awhile then the idea to make it a candle holder struck me. I was just going to buy a candle and set it on top but then I had the idea to make a candle which would give me a second hidden compartment. I feel like this double secret compartment kind of saved my project. Here's how I made it.
Supplies
Large Bowl Blank
Small Bowl Blank or Turning Stock
Lathe
Lathe Tools
Sand Paper - Various Grits
Paper Towels
Epoxy
Hacksaw or Equivalent
2 inch PVC Pipe
Blue Tape
Casting Resin
Disposable Cups
Stir Sticks
Sharpie Marker - Black
Lacquer Clear Coat
Small Piece of Jute
Super Glue
Spray Paint - Your color choice
Small Threaded Eyelet
Step 1:
This is a bowl blank that I had prepared a while ago from some silver maple. It measures roughly 6 inches wide by about 5-ish inches tall. For this piece to work as a secret compartment it needs to have some height, you don't want a short squatty piece otherwise you will not have much room for the secret compartment. This will make more sense in later steps. The first thing I did was use my worm screw and live center to mount the piece in the lathe then I trued up the piece and made it a round cylinder.
Step 2:
With the piece rounded I started to remove some of the material from what would become the bottom. Here I wanted to make a lip sort of like you would make for a lidded box. Then I used the largest Forstner bit that I had a 1-3/8 inch and drilled about 3 inches in to the bottom of the piece. I did not drill all the way through to the other side. I knew I would have to remove some of the wood on the opposite end because of the hole left by the worm screw, so I left enough wood to allow me to clean up the other end.
I then used my hollowing tool to increase the size of the cavity as much as I could. This cavity will be the hidden compartment in the candle holder section. Even if you don't have a hollowing tool you can still make a decent size hole with just the Forstner bit.
Step 3:
I made a cone shaped jam chuck so that I could still use my live center to turn this piece. Being new to the lathe it freaks me out whenever the piece is only supported on one side. The jam chuck might not be necessary but I rather be safe than sorry. I was sure what shape to make I just kind of free styled what I thought looked good. The pictures show where I started and where I ended up.
Step 4:
With the bottom drilled and shaped I flipped the piece over and this time used my chuck jaws to hold the piece in place and shaped the top. You can see a concave shape in the top this is the side that the candle will sit in. When I was happy with it I sanded the piece starting with 120 grit and went through the different grits up to 2000. This may have been a bit premature, I probably should have waited to sand.
Step 5:
The piece had some cracks in the wood which I was going to leave but decided to fill with epoxy. So I mixed up some 5 minute epoxy and blue pigment and filled all the cracks. Once the epoxy dried I reshaped everything with the lathe tools and then sanded the entire piece once again up to 2000 grit.
Step 6:
Now I needed to make the pedestal for the candle holder. This piece will also act as the "lid" for the secret compartment I drilled in to the bottom of the first piece. Basically I made an upside down lidded box.
I first turned the bottom and created a recess for the chuck jaws to lock on to, then I flipped the piece over shaped the lid section. I would remove material a little at a time to get a good fit with the mating piece. You can see from the pics one of the times I was checking the fit. Once I was happy with the fit I refined the shape a little more then sanded the piece up to 2000 grit.
Step 7:
I applied several coats of acrylic lacquer to the larger piece I would wet sand the piece with 2000 grit every few coats to get a nice smooth surface.
For the bottom piece I used a black sharpie marker to first color the piece black then I sprayed it with several coats of acrylic lacquer as well. I applied about 3 coats of sharpie before applying the clear coat. I used a paper towel to buff the piece after the clear coat was dry.
The last pic shows what the piece will look like once assembled.
Step 8:
To make the candle I used a 6inch long piece of 2 inch PVC. I used my Portable Bandsaw Table to cut the 6 inch piece but if you don't have one you can just use a hacksaw to make the cut.
Step 9:
I needed to make a removable bottom for the candle so I thought about using a PVC cutoff ring and some wood to cast a piece of plastic that would fit the bottom perfectly. The wood pieces would result in a sort of handle in the finished piece or rather a couple of places to grip the bottom so you could remove it.
I think I used too much mold release and it affected the resin, to make a long story longer I didn't end up using this first casting.
Step 10:
So instead I used the same PVC cut off and cast a solid piece instead. Once it cured I pre-drilled a hole and added a threaded eyelet to act as a handle. This not only looked a lot better but worked out great too.
Step 11:
Now that the bottom of the candle was sorted out I started on closing off the top of the candle. I used the bottom of a plastic cup that fit inside the PVC snugly to act as a catch basin for the resin. Basically I needed a way to seal off the top section of the candle so I could fill it with resin. I also used a piece of scrap wood to support the plastic cup from the bottom.
In hindsight I could have just taped off the top and poured the resin in from the bottom which may have been a little easier, maybe next time.
As you might have noticed from the last pic I didn't mix enough resin to fill the pipe all the way to the top. So I would have to do a second pour.
Step 12:
Luckily this resin will stick to itself even after it has cured so a second pour isn't a big deal. However I was trying to make the top rounded or slightly domed shaped and poured a little too much resin which resulted in a couple of small drips or runs.
I was going to remake the candle but instead I figured I would add more drips and runs to give the candle the appearance that it had melted. I thought it might look more realistic than just a perfect solid candle.
Step 13:
My candle was going to need a wick. I drilled a 1/16 inch hole in the top center of the candle. Then I cut a small piece of jute twine and super glued the bottom 1/3 of it. I needed it to be stiff enough to be able to plug in to the hole at the top of the candle. Once the glue dried I used a black sharpie to color the wick to give it the appearance that it had been burnt.
Step 14:
Originally I thought the candle would look best if I painted it a bright color. In the pic I was painting it a flat light blue, but once it dried I didn't like the look so I tried maroon, then a dark blue and none of them looked quite right. So I ended up painting it an ivory white color which to me looked the best.
Step 15:
Here is a photo of what it looks like in its final resting place. I think it looks pretty darn good and blends in quite well with the other items on the shelf.
Step 16:
There is quite a decent amount of storage in the candle. I did add two small pieces of electrical tape to the bottom cover so the fit would be a little more snug, you can see the tape in the second pic. The candle fits snugly in the candle holder, it can be removed with a slight twist. Then the bottom cover pops right out to reveal the first secret compartment.
The black base and the main body also have a friction fit and are separated much the same way as the candle, with a slight twist to reveal the second secret compartment.
While some folks might expect one secret compartment surely they would never expect two! This was a fun build and I am thrilled on how it turned out. I hope this can serve as inspiration to make your own version of a secret compartment.
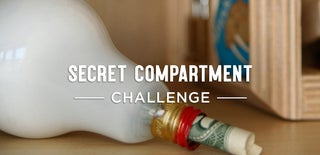
Runner Up in the
Secret Compartment Challenge