Introduction: Car Rust Repair - 1981 VW Rabbit Floor Pan
Rust sucks. It just totally sucks.
I've been meaning to write this up for a while, but I don't even want to talk about it.
I will try to give any useful tips I have.... it will be short.
I've been meaning to write this up for a while, but I don't even want to talk about it.
I will try to give any useful tips I have.... it will be short.
Step 1: Safety
Do a google search for: angle grinder injuries photos
Then put on this face sheild: Bionic Face Shield
(or a motorcycle helmet)
Also - get some heavy gloves for welding Gloves
And an auto-dimming welding mask .... I can't find the one I have, but it is great. Here is a link to one at harbor freight -- link to welding mask-- I think I have the same one but without the decals
Then put on this face sheild: Bionic Face Shield
Also - get some heavy gloves for welding Gloves
And an auto-dimming welding mask .... I can't find the one I have, but it is great. Here is a link to one at harbor freight -- link to welding mask-- I think I have the same one but without the decals
Step 2: Take Out the Bad... It Is All Bad.
Rust offers no protection, it has to be removed. Any pockets of rust left in place with spread.
I go in this order:
I am working on a VW rabbit that has a thick layer of tar over everything. It is like roofing cement. This has to be removed because it will melt into the welds, it is also sticky and catches on fire.
I go in this order:
- Hammer
- Pointy Hammer
- Metal snips
- Wire brush
I am working on a VW rabbit that has a thick layer of tar over everything. It is like roofing cement. This has to be removed because it will melt into the welds, it is also sticky and catches on fire.
Step 3: Make a Patch -- MOST USEFUL STEP --
This is my one good technique.
I cut a the bottom out of metal serving tray, then I jam that into the spot so it covers the rust. It is easy to trip with light shears or heavy scissors. I trim and check this until it is just right. Then I flatten out the foil and trace it onto the sheet metal. Now you can cut out the shape, knowing that it will very likely fit in place, sort off.
I cut a the bottom out of metal serving tray, then I jam that into the spot so it covers the rust. It is easy to trip with light shears or heavy scissors. I trim and check this until it is just right. Then I flatten out the foil and trace it onto the sheet metal. Now you can cut out the shape, knowing that it will very likely fit in place, sort off.
Step 4: Weld
I use this wire feed welder from Harbor Freight (always on sale) -- link to welder. A better welder would be nice, but it is usable if you don't care what the weld looks like and you do these things:
Also:
- Replace the tip with a name brand tip
- Replace the wire with a brand name wire
- Test the wire feed tension before you start welding
- Get some nozzle gel and put it on the tip of the nozzle. It is like the opposite of flux, anything you put it on can not be welded.
- On the welder, start with the lowest settings. Slowly increase the wire feed rate until you get good results. For sheet metal you can use the lowest power level.
Also:
- Get an auto dimming welding mask
- Use a very bright light, the auto dimming lens is dark even when not dark.
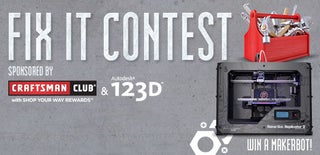
Participated in the
Fix It Contest