Introduction: Casting Replacement Vehicle Emblems
Hey Instructables crew, in this writeup I'll be teaching you how to make replacement vehicle emblems, using epoxy resin. Initially, the focus of the Instructable I had in mind was to show how to vinyl wrap a vehicle emblem but, partway through wrapping, I ended up dislodging the red insert of the GMC badge I was working on, from the bezel in which it normally sits. I figured hey, why not make my own replacement emblem that I can personalize and make whatever colour I want, I will also show how I made the mold for casting the emblem.
Now that this project has turned into a repair project, this will double as my entry to the Fix-it contest. Let's get to it!
Supplies
- A container to make the mold in that will leave about a half-inch to an inch around the outside edge of your emblem
- Amazing silicone mold kit
- 2 part Epoxy resin (I used Art resin)
- The pigment of your choice (I used powdered iron oxide) **More on pigments below in step 7 'adding pigment'
- Dental wax (orthodontist wax)
- Vehicle badge/ Emblem
- Hot glue
- Double point scale
- Mixing cups (10 should be good)
- Mixing sticks
- Nitrile gloves (a few pairs)
- Dropcloth
- Handheld torch
- File (I used a cheap metal nail filing tool)
- E6000 adhesive or 3M emblem adhesive
- Isopropyl alcohol 70%
- Lint-free cloth
Optional Supplies:
- NIOSH respirator (For those sensitive to epoxy resin)
- Clothes you don't mind wrecking
- Fishing line
Step 1: Prepping Your Emblem to Make the Mould
So, as I previously mentioned, I accidentally dislodged my G from my trucks GMC badge, so I had to carefully pop out the M and the C as well. If your emblem isn't one that has a bezel like mine, your best bet will be a piece of fishing line, wrap the two ends of your piece around your index and middle finger on either hand and use your thumbs to gently push the line under the badge/ emblem, going back and forth, work your way from top to bottom and you should have your badge come off. The fishing line will cut through the adhesive that secures your badge like butter and will not damage the paint of your vehicle.
Once you have your emblem off the vehicle, clean it with some isopropyl alcohol and remove any remaining adhesive residue from the badge and the vehicle. This can be done with alcohol and a non-abrasive lint-free cloth.
Now with your emblem all cleaned up, you should have your container that you'll be pouring your mold into, at the ready. You want to put a dab of hot glue on the back of the badge and stick it flat, face side up in your container. This will keep it in place while you fill the gap between the container and the underside of the badge with dental wax. Take small pieces of dental wax and roll it into long snake shapes. form these around the bottom edge of the badge, so the mold making material doesn't seep into where it shouldn't be
Once you've sealed around the entire base of the emblem, you can set this aside and move onto the next step.
Step 2: Determining How Much Mold Maker You Need
To figure out how much mold maker you will be needing you can either use your best judgement and guess roughly how much you'll be needing (this is normally what I end up doing, buuuuut...) I know some don't like to live on the edge like that, If you happen to be one of those people, then you'll have to use some good old fashioned math to find the volume of your mold. Here is a volumetric calculator by Alumillite to help you do just that !
Step 3: Measuring and Mixing the Mold
***Please note the following ratio is for The amazing mold rubber kits, this is not the mixing instructions for other brands of mold making kits. If you are using a different mold making kit, follow the instructions for your specific kit.
The mixing ratio for the Amazing mold rubber kit is 10:1, so 10 parts of the base to one part of the catalyst. I find it easiest to use a double point scale to get the measurements by weight, but you definitely can measure by volume as well if you don't have a scale, most mold kits will come with small graduated cups for measuring. If you used water to determine the volume of material you would need for your mold, you'll want to grab the cup you poured the water into and set it next to another empty cup, pour an equal amount of the base into the empty cup. You can set the water cup aside, you no longer need it. This is where a scale will come in handy, but as I mentioned beforehand, it's definitely not needed. You want to take an empty measuring cup and set it on the weighing surface, with the cup on the scale, turn the scale on. It should read zero if it doesn't just press the tare button. This will zero the scale, eliminating the weight of the cup from the reading. Now replace the empty cup on the scale with the cup you poured the base into, make a note of what the weight of the base is, then divide that number by 10. This will give you the weight of the catalyst needed. Now you can swap the empty cup back onto the scale, hit tare again if the scale doesn't already read zero, then measure the catalyst. I use small 2floz disposable cups for measuring and I ended up almost filling three of them with the base, they weighed as follows: 43.67grams, 54.40grams, 51.87grams. for a total of 149.94grams of mold maker base. Divide that by 10 and you get 14.99grams of catalyst needed. before I could mix in the catalyst, I had to dump all of my cups of base into one bigger cup. (A bigger cup that I should have used off the get-go, oops)
Pour the catalyst into the silicone and give it a good thorough mix, scraping the sides and bottom, a full minute of mixing should suffice. Try to minimize the number of bubbles you work into the silicone mixture.
Step 4: Pouring and Finishing the Mould
You want to pour slowly, into the lowest part of the container, from a height of 4-8inches above the container. This will ensure the silicone flows around the badge and any trapped air escapes.
Leave to set up for 6 hours. After 6 hours has elapsed you can press on the surface, if it is still soft, leave it for a few more hours. If it feels stiff, it is cured.
You can now peel the mold out of the container, don't violently rip it out. Be gentle!
Set the mold aside.
Step 5: Epoxy Resin Safety and Best Practices
Epoxy needs to be measured by volume, don't use a scale for this step as the hardener and resin parts almost always have differing weights.
Whenever you're working with epoxy resins you should wear nitrile gloves, I recommend against latex gloves as some latex will inhibit the curing of certain resins. Nitrile gloves not only protect your hands from getting sticky nasty resin on them, but it also prevents dermal toxicity. Dermal toxicity is when you absorb harmful ingredients through your skin into the bloodstream.
Most crafting epoxy states it is safe to use, non-toxic and no VOC's (volatile organic compounds) but there is evidence that these claims are only half true and that resin components have the potential to be harmful until fully cured. If this is a concern to you, you may want to use a NIOSH respirator too.
You should wear clothing that you don't mind wrecking for this part of the project as well, droplets of resin will not come out of your clothes.
Step 6: Measuring and Mixing the Resin
Now that we've gone over epoxy resin safety its time to measure the epoxy. I used Art Resin for this project, This resin is a 1:1 mixing ratio, so you need two cups one for each the epoxy and the hardener. You want to pour the exact same amount of each into their respective cups. You really want to be exact, if you are off with your measurements the epoxy might not set up and will remain tacky.
Now pour part A into part B, scraping as much as possible out of partA's cup as possible, mix, mix, mix, scraping the sides and bottom, try to work as little air into the mixture as possible. You'll notice the mix has a weird appearance, it almost looks as though there are blurry streaks throughout, this is normal. Mix until the streaks disappear, they will gradually disappear as the two parts bond to one another.
Now you want to pour the mix back into the cup you poured part A from, make sure to scrape as much from the cup as possible. Give it a good mix for about a minute. The reason for going back and forth between the two cups is to make sure we get as much of both parts as possible, to ensure its as close to a 1:1 ratio as possible.
Step 7: Adding Pigment
Now we can colour our resin, you can use the following:
- Alcohol inks
- Powdered pigments
- Resin pigments
- Glitter
- Glow in the dark powder (THIS one is my favourite)
- Acrylic paints( The rule for colouring resin with acrylics is no more than 10% paint in the resin. this should be plenty. Any more than 10% can result in your resin not setting up properly)
- DO NOT USE ANY WATER BASED PIGMENTS
Add in your pigment, start with a little and work up from there until you achieve your desired colour. Remember you can always add more, you can't take pigment out once its in. Give it a good stir
I poured a small amount of my resin into a separate cup, then mixed in my Iron oxide pigment, I find with powdered pigments it's easier to get the pigment distributed into a smaller amount of resin that can then be added back into the rest.
Step 8: Filling Your Mould
Once you've got your resin the colour that you want. Grab your mold.
Drizzle the epoxy into the mold, try not to overfill the mold as this will create more sanding work for you once its cured. once you have filled your mold you can remove bubbles with a handheld torch lighter. Holding the flame roughly 8 inches from the epoxy surface, do a couple of quick passes over, then you can repeat this process in a few minutes once more bubbles have risen to the surface.
Leave the epoxy to set up in the mold for about 24 hours or whatever the manufacturer suggests for your epoxy.
Step 9: Removing Your Emblem From the Mould
After 24 hours your resin will be set, now you want to gently pull the mold edges away from the cured epoxy, this shouldn't be difficult and the mold should break free fairly easily. Once you have done this for all the edges, you should be able to easily pop the badge from the mold.
Step 10: Cleaning Up the Cast and Final Coat
I used a metal nail file, since its small I figured it would be great to fit into small spaces to lightly take off any casting imperfections there might be.
Once I was happy with how they looked, I wiped the dust off using my lint-free cloth and iso alcohol, then layed them out again face side up.
I mixed a bit more epoxy, not nearly as much this time, I added pigment and added a thin coat over the front side of the badge, try to only add epoxy onto the very front face of the emblem and not on the sides, it may make it appear lumpy from certain angles if you do, or in my case, the GMC inserts would not have fit into the bezel.
This additional resin layer will give a durable gloss finish.
I left that to cure another 24hours.
Step 11: Installing the New Emblem
Now I can install them back onto my truck, originally I was going to use E6000 adhesive to secure them back on because that's what I had on hand, but thankfully I found my 3M acrylic auto attachment adhesive. If your emblem is one that sits directly on the surface of the vehicles paint, I advise against using E6000 as it will damage the paint. Use the 3m emblem/badge adhesive, this is what most vehicle manufacturers use to secure their badging.
The 3m adhesive is fairly straight forward to use you just cut small pieces and stick the sticky side to the back of your emblem, with the red protective liner facing outward.
Now you want to give the spot the emblem if being installed on a good wipe with iso alcohol and your lint free cloth.
Now you can carefully peel off the red liner and push the emblem down where you want it to go. and Voila!
You've just made your own personalised vehicle badge replacements.
Now go show them off!
Let me know what you think of this instructable in the comments below! If you have any questions or suggestions about this project I'd love to hear them as well!
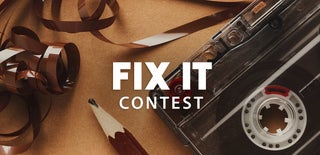
Judges Prize in the
Fix It Contest