Introduction: Cedar Glider
This is the glider that I'm going to make.
I made the original glider back in 1996 to welcome the birth of my daughter. After being outdoors in the harsh winters, it's still functional, but not that nice to look at anymore. In this project, I will reverse engineer the glider and rebuild it from scratch.
The new glider is made from Spanish Cedar, but you could also use Western Red Cedar, Mahogany, or an African wood like Sipo/Utile or Sapele, or even Teak.
Step 1: Rough Cut All the Lumber
The first time I made the glider, I used dimensional lumber. I'm pretty sure it was Western Red Cedar. This time around I am using rough cut Spanish Cedar.
After milling up the pieces (68 pieces total) my workshop smelled amazing!
It was a lot of pieces to keep track of, so I labeled them all to prevent any confusion and to avoid making a mistake.
To give you an idea of dimensions, the seat of the glider was 48" wide. It would normally be made with 1" and 2" dimensional lumber (actually 3/4" and 1.5"). Since I had more control over the dimensions, I made the 1" pieces closer to a true 1" (maybe more like 7/8") and the 2" pieces were about 1 3/4".
Step 2: Measure Up the Original Base
I took measurements of all the pieces that form the base -- 11 pieces in all. The base is 46" wide, 25" deep, and 11 1/2" high. The entire base is made from the 2" cedar. As long as you respect these dimensions, you can create a design to suit your taste. It just takes a bit of planning.
Step 3: Cut the Pieces to Form the Base
I cut each of the pieces on the table saw. Then I used the band saw to round some of the corners and to cut the profile of the base.
Then, back at the table saw, I used a dado set to cut half-lap joints.
Step 4: Glue Up the Two Ends of the Base
All of the pieces for the ends of the base fit well. I glued them up and clamped them, and then screwed them together using deck screws. This photo will give you a good idea of how you can design the end pieces. Just remember that each end piece needs to be 25" deep, 11 1/2" high, and made from 2" material.
Step 5: Finish Assembly of the Base
The new base is exactly the same size as the old base, but it looks a lot cleaner with the new cedar.
Step 6: Construct the Seat Ends / Arm Rest Support and Arm Rests
The seat ends are 22" high and 21" deep. They will connect to each end of the seat and will be used to connect the seat to the base using a steel bar with a bearing in each end of the bar.
The arm rest is 26 1/2" long (deep) x 4 1/2" wide. The arm rest will be attached near the end when almost everything else is in place.
Step 7: Cut the Seat Supports
Now it's time to work on the seat. I cut out the front edge of the support for the seat slats on the band saw. I started with a 2" piece that was 48" long x 3 1/2" wide and then used the band saw to cut away some of the material to give it a nice look.
The piece at the back was made from a 2" piece that was 48" long x 1 3/4" wide. It was cut simply on the table saw, with no need to cut out any kind of a design on the band saw.
Step 8: Assemble the Seat Slat Support
The support for the seat slats is comprised of four other pieces. One piece is rectangular and straight on all four sides. The other three pieces were all cut on the band saw. The overall dimensions of the seat support are 48" wide x 22" deep.
I used the pieces form the old glider to trace out the profile before cutting, but you can create your own design as long as it is something like this to give a comfortable sitting position.
Step 9: Prepare the Seat Slats
I cut the seat slats to be 1 3/8" wide using the table saw. Using a bit of math, I figured out the size of the gap between each of the seat slats and then cut some spacers on the table saw. This helped to ensure equal spacing. Each slat was just a little more than 1/4" apart.
Step 10: Apply First Coat of Finish
Before screwing in the seat slats, I applied alight coat of finish to the seat support and to each seat slat. his will make it much easier to finish later, especially on the bottom and between each of the slats.
I used Behr Premium transparent weather proofing all in one wood finish. It was tinted with Cedar Naturaltone to help accentuate the cedar color.
Step 11: Prepare the Back Slats
The back slats are made from 1" material and come in two widths. Three of the pieces are 5 1/4" wide. The remaining 12 pieces are 2" wide.
Each end piece is 5 1/4" wide and roughly 15" long. The center piece is also 5 1/4" wide and roughly 21" long. The remaining pieces that are 2" wide can be cut to be ranging from 16" - 20" long. Just plan carefully to be sure each piece is long enough. After the pieces are screwed to the back support, you can use a jig saw to fine tune the length of each piece.
After the center piece has been cut, you can optionally trace out a pattern. I'm using the letter "M" for "Mommy". I used a tool that has a serrated wheel that makes little dots through the paper to transfer the pattern onto the wood.
I've had the set for at least 20 years and they're really helpful for transferring patterns. I don't remember where I bought it, but they are available from Amazon. You can find one by clicking here.
Step 12: Trace the Outline
Next I used a pencil to trace along the dots to make the pattern more visible prior to cutting.
Step 13: Cut Out the Pattern
I used a scroll saw to cut the "M". I definitely need a new blade. It was smoking while cutting, which was surprising since the cedar is pretty soft.
Step 14: Round Over the Slats and Arm Rests
I used a roundover bit to round over the edges of each of the back slats and each of the seat slats.
Step 15: Attach the Back Slats
I used spacers again to equally space the back slats. In this case, the slats are roughly 1/2" apart.
I assembled the back on a 48" x 48" sheet of MDF. This made it easy to assemble because the back is exactly 48" wide. All I had to do was position the two end slats along the edges of the MDF, and then space the remaining pieces with the help of the spacers.
Step 16: Assemble the Back
I temporarily clamped the arm rests into position while I set the back into the correct position.
The back is held in place with a board behind the back that attaches to each arm rest with a half-lap joint.
Step 17: Reinforcing the Back Support
I modified the original design by cutting a slot in the arm rest to help support the back. This will take some of the stress off the half-lap joints, and it adds a bit of security in case the half-lap joint fails.
I never had a problem with the old one, but it doesn't hurt to play it safe.
Step 18: Round the Corners of the Arm Rests
I used a jig saw to round the corners of the arm rest. It would have been too hard to do this on the band saw because I needed to cut through the half-lap joint.
Step 19: Round Over the Rounded Corners
The rounded corners were finished off with the roundover bit.
Step 20: Attach the Seat to the Base
My original bearings and bars were made at a machine shop. I got the bearings from a bearing manufacturer and then had the machine shop insert them into some custom made steel bars. That was 20 years ago. It's easier now just to get them from Amazon. You can find them here.
The last step is to attach the seat to the base with the steel bars and bearings. The bearings are fastened to the wood using 3/8" bolts. You'll need to drill a 3/8" hole at the bottom of each end of the seat, both front and back (a total of four holes). Those holes will be for one end of the bearing bar. Then you'll need to drill a 3/8" hole at the top of the base, both front and back. Those holes will be for the other end of each bearing bar.
Step 21: Try It Out!
After the bearing bars have been installed, the glider is ready for use.
You can visit YouTube and watch me make the glider.
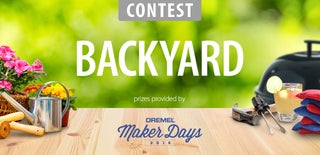
First Prize in the
Backyard Contest 2016
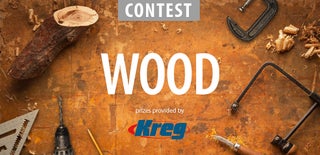
Participated in the
Wood Contest 2016