Introduction: Bluetooth Cedar Speaker Box
I had a gaming chair just sitting around collecting dust and decided to make a box to hold the speaker system using cedar logs I got from a friend's house. I intended to just place the speaker system into the box as is and make it as painless as possible, but it evolved into adding Bluetooth, creating a new mount for the speaker faces for a supreme musical experience, and overall better design features. My friend Chris convinced me that the user interface and the fabric screen should be recessed, both of which I wasn't planning to do in my quick and dirty fabrication.
It took about a month to complete from planking the logs to the last coat of finish, working for only a couple hours a day. This entire project was me making it up as I went along. I had zero planning until I ripped the logs into the planks and saw what I had to work with.
Step 1: The Speaker System
These are all of the parts that I pulled from the chair, which include: a woofer and two tweeters, a toroidal transformer from 120v ac to 16v ac, an amplifier with a heat sink, and two rumblers that add a hilariously unreasonable amount of vibration for bass.
Step 2: Design and Prototyping
As I said before, I didn't plan anything until the logs were ripped so there were a couple prototypes. This was the finalized prototype, small enough that I could use all of my wood and large enough I could fit everything in. The first prototype was much larger so that I could place the interface on the same side as the speakers but I didn't have enough wood to do so, which turned out to be a good thing because this size box is already pretty heavy. At this point I was planning on keeping the bass and tweeters in their cases from the chair and mounting them as such but that changed down the road.
Step 3: Planking the Logs
I first ripped the logs into 1 inch planks on a band saw, then jointed and planed them to 3/4 inch. After they were to the desired thickness and smoothness I ripped them on an table saw to cut off the live edge and leave as much wood as possible.
Step 4: Biscuit Jointing
I played with the idea of jointing the planks on edge by dove tail or similar fashion. After much discussion with my friends Chris and Tim, and painful cost-benefit analysis for every option, I decided on biscuit jointing them together, which worked extremely well. It was pretty simple and quick to do after I did a couple of tests. The front face where the speakers are is mitered like a picture frame.
Step 5: Gluing It All Together
I ended up not having enough clamps so I made do with what I had. I intended to box joint all of edges because I thought it would've looked pretty awesome, but decided on the safer and easier option of miter jointing and applying a generous amount of glue.
I wanted the lid to be removable so I could service the system when I needed and did this with 2 1" x 3/4" maple strip glued to the underside of the lid on two sides that fit along the inside of the box walls. I drilled and countersunk holes for a 1/4" stove bolt and a t-nut through the walls of the box for a strong and flush fastening.
For the bottom I used 3/4" plywood and routed a notch 1/2" into the sides to recess it flush with the bottom of the sides. I didn't see any reason on making a cedar bottom since the box only works in one direction.
Step 6: Cutting Holes for the Hardware
In the prototype I sized the hole for the user interface's control board and applied it here and then routed a recess so the metal sits flush. I then slowly cut and filed a hole for the heat sink to slide into and carefully cut slits near the bottom on the back for ventilation with a circular saw. Later I added an IEC plug receiver in the back.
Step 7: Adding Bluetooth
My friend Tim had a small MPOW Bluetooth adapter that he wasn't using and generously donated it to the cause. I took the board out and replaced the on-board power button with wire leads to a larger button that mounts to the user interface plate.
The interface originally had the ability to switch between two audio inputs with a rocker switch: an aux cord or the RCA jacks. I wanted to wire the outgoing audio from the Bluetooth adapter to the board, so first I removed the RCA jacks and wired to those contacts, but for some reason the volume coming from this route was half that of the aux cord. I like my music loud so I wired to the back of the aux cord input and it worked fine and dandy. The Bluetooth board is powered from a 5v adapter, which I wired onto the incoming 120V from the IEC plug receiver.
Step 8: Finalizing the Innards
After much convincing from Chris, I removed the speakers from their boxes and CNC'd a face for the speakers, since I didn't have any hole saws that were the right size. This freed up basically the whole box for wire management into a nice and orderly jumble.
I sanded the aluminium face plate to remove the lettering and spray painted it black for a sleek new look. Chris wanted me to use the CNC to engrave upgraded lettering onto the face plate, which I thought would have been cool to do, but after I saw the solid black I decided that looked better.
Step 9: Handle and Sealing
I made a handle out of 1 inch pipe I found lying around. First, I was going to use plates to bolt the handle to the lid but every single one of my countersink bits were dull and refused to cut cleanly, so I welded 3/8" nuts inside the pipe and sanded it smooth and flat. Coupled with a washer and nut on the inside of the lid it holds on pretty tight. I like this look way better than I think I would have with the plates. It looks like the handle isn't attached at all or is held on my some sort of magic since there are no visible fasteners and seems almost out of place.
I used polyurethane to seal the box and 5 coats worth later, with light sanding in between each, a nice smooth and shiny finish brought out a nice warm color in the cedar. I did a single thick coat on the inside to seal all wooden surfaces to protect from moister and swelling/shrinking as much as possible.
Step 10: The Finished Product
I had a bit of fabric from the chair that I used to make a screen to cover the speakers that sits into a recess I routed. Overall, I had a great time learning these new skills while making something awesome. I'm pleased with all of the recesses and how everything sits flush, and the contrast between the flat black and the shiny wood came out better than I anticipated.
Step 11: Bloopers and Adaptations
There were a few hick-ups during this project. One of the largest was breaking an entire side in half before gluing the box. After biscuit jointing, a crack formed along the entire length along the grain on one of my sides. My solution was to attempt a butterfly spline, which ended very poorly. I failed to take a picture because it was embarrassingly bad. After breaking the side I didn't have enough cedar left for a whole side so I used some maple that I found lying around, seen above. I put it on the interface side because I felt it was less jarring with some kind of transition between the two colored woods than having it on the other side of the box by itself.
Another major mistake that ended up becoming a nice feature was the angle cuts on the lid. When ripping the miters for the sides I was in the zone and ripped two sides on the lid before realizing what I did. I embraced it and ripped the angles on the other two sides and I think it looks much better than it would without the angle. It provides a nice transition from the lid to the sides.
The last mistake I made happened while I was finishing. I applied the first couple of coats of poly with a cheap brush. This was a pretty large mistake because there were large brush strokes that were tough to sand out, causing large scratches, and what seemed to be fuzz getting trapped in the second coat. I think the dried poly on the brush from the previous coat was flaking off into the new coat and causing all sorts of trouble. I ended up sanding to the wood and starting over and used paper towels to wipe on thinner coats and finer sand paper for smoother surface, avoiding a disaster.
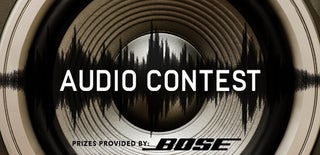
Second Prize in the
Audio Contest 2017
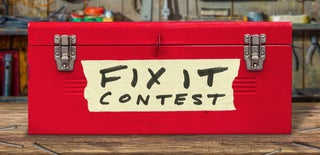
Participated in the
Fix It Contest