Introduction: Resin River Table
Resin River Table made with cedar and inlaid with turquoise and black sand.
Time Spent ~40 hours, Material Cost: ~$500
What is a river table? - A river table typically takes a slab of wood and cuts it in half. The rough edges (live edges) become the middle while the cut edge becomes the sides. This allows a weirdly shaped slab to have straight edges.
Supplies
Materials:
- Cedar wood slab
- Black Sand
- Table legs
- Turquoise (Mexican Rough Chalk from eBay)
- Ecopoxy Liquid Plastic (see resin section for alternatives)
Materials for Resin Form:
- Melamine Board
- Tyvek Tape
- Wood Screws
Tools:
- Table Saw
- Random Orbit Sander
- Sanding Paper - 60 to 320 grit
- Router
- Sled with Router & Flat bit or Planer
- 45° angled bit for router
- Hot air gun, Hairdryer, or ideally small torch
- Clamps
- Drill
- Chalk line
- Large Framing Square
Step 1: Wood Selection
First select the wood you will use. There are typically many places to get wood, from a local shop to an online store. Whichever fits within price range and is the size you want. The wood slab was bought from this site: woodslabs.com The company typically will tell you the length and the lowest and largest width. The piece chosen was about $140.
Step 2: Planning the Look
Plan how you will cut the piece before you decide to buy it. Pictures of the front an back are usually available, and a little bit of photo editing can show how cutting will look in the next steps. There are many alternatives for the final look of the table. The table can be made see through, light up, or many others.
Step 3: Sanding
Sand the entire piece to remove major debris and bark. To do this, a random orbit sander was used as well as chisels and other tools. Take the time needed to get a nice edge as desired, since this will be the inside edge look when it is all completed.
Step 4: Center Line Cutting
Cut the piece down the middle as previously planned. The piece was marked according to the plans shown in the previous step. A chalk line is the most ideal tool for this. To cut it a table saw was used and a table was placed next to it to support the long length of board. The wood was slowly fed through. Rollers such as PVC pipe were placed under the wood to help this process. This center line cut will end up being the long table edges. It is critical to take this step slowly and make this cut as accurate as possible as this will heavily effect steps down the line. Alternatively, a circular saw or a track saw can do the trick if they are powerful enough to cut through the thick slab.
Step 5: Sizing
Place the cut pieces on a table to mark and size the final piece. One half slab was flipped on one side so it fits together nicely with the other half for the table. Resin is very expensive so the half slabs were offset so the pieces can be as close together as possible. This leaves a couple inches on one side of each half to be cut off. Additionally, the other side was squares first by a cut as small as possible. The final fit is shown here. In the final fit, the pieces are checked that all sides are square, and the final dimensions are taken for the next step to create the mold. If the lengths are not perfect (i.e. greater than ~1/8" difference) Then repeat the sizing step to ensure they have the same length.
Step 6: Creating the Mold
Create a mold to pour the resin into the piece. This uses melamine board since it is nice and smooth. DO NOT pour directly on the melamine board, it will stick, you need to prep it first. Typically by adding Tyvek tape. Acrylic can be used as a substitute, and it can be poured directly onto acrylic without sticking, however acrylic is more expensive. Do not expect the melamine board/mold to survive intact after.
To start, cut a bottom piece a couple inches wider and longer than the table dimensions so the sides can be screwed on. Then cut two pieces the width of the piece (the shorter side) Cut the width pieces as exact as possible. Then cut two more pieces the length of the piece + a couple inches. The height of the length and width pieces should be the thickness of the piece plus ~1/2" to 1". Add tyvek tape to one side of every piece overlapping the tape. Check the fit by placing the slabs and sides on the base board as shown here. Carefully mark the placement and place the slabs in regularly to test fit when screwing in melamine with tyvek as seen here. Make sure the tyvek tape is all facing inwards.
Note: It is important to get accurate dimensions and fit check the piece in this step as every bit it is off will take a lot of work to correct down the line.
Step 7: Sealing the Mold
Seal the mold to prevent the resin from leaking out. First remove the slabs from the form. Use a hot glue gun to create a small bead of glue on all edges. Take extra care with the corners. An improperly sealed mold will ruin your project. Assume resin will seep to every nook an cranny of the mold. You can test the seal by placing water in the mold and seeing if it leaks.
After the edges are sealed, put the slabs back in place. Push the slabs as close to the sides as possible.
Step 8: Resin Selection
Select the resin type you will use for the pour. When looking up resins there are two major applicable options: A slow setting versions designed for thick pours that's more expensive or a fast setting resin that is designed for thin pours such as counter tops that's cheaper. The fast setting requires many separate pours typically about 1/8" at a time between multiple hours. This can be tedious because you have to pour after usually about 4 hours later and no later than a half a day without having to re-prep. This can take maybe 6-20 times depending on thickness. Read instructions for exact thickness and time to pour. If you pour too much it will crack because it gets very hot because it sets quick. If you're worried on the time commitment and can pay more for slow setting stuff, you can save a lot of time. You can do a single prep, then single pour, saving a lot of time and effort. The slow setting stuff is almost unlimited thickness.
Here are some options:
Fast setting: Pro Marine Epoxy
Slow setting: Glass Cast 50 or Ecopoxy Liquid Plastic
Ecopoxy Liquid Plastic was used for the main pour, and the Pro Marine Epoxy was used for a surface finish pour, mainly because Ecopoxy Liquid plastic ran out. Different types of Epoxy's can be typically switched between separate pours with little visual effect. Other than setting, the differences aren't very much, some are little better quality and age better.
Determine the amount you will need to buy. The amount of resin is estimated by approximating the volume of the center separation. The best method to do this is taking measurements from one side of the slab to the other along the center edge for each half then average and multiply by thickness and length to get volume. It is suggested to order about 25% more than is estimated using this method to account for crack fills and inaccuracy.
Step 9: Details/Inlay/Prep
Decide on inlays you will use, if any. For the table here it was decided to inlay it with turquoise sitting on top of painted black sand. This was done to make it not completely see through, and add an artistic touch. Turquoise cost $60 from eBay for 2lbs. It was rough chalk Mexican turquoise. From testing it was found the epoxy brings out the color so rough stone can be bought for a lot cheaper.
Before you pour, make sure slabs are pushed as far to the side as they can go. Place all inlaid objects between the slabs or wherever it is planned to go. In this case the black sand was placed, then the turquoise was placed on top. This was experimented with a bit to see how it looks, in the end it is up to the designer. It can also be a see through table, in which case skip inlays.
Test making a small pour in a clear disposable cup with the resin and spare inlays to practice mixing the resin, practice applying, and to see how it will turn out. Before starting, read all the instructions of the epoxy manufacturer. Make sure to keep in a warmer location since the resin will not set in the cold.
Step 10: Resin Seal Coat
Seal the surface of the piece with a small coat of resin. Regardless of which resin you get, you should start with a seal coat, shown here. Notice how this first coat will demonstrate how the color will turn out. This is simply a brushed on coat to seal most cracks in the wood. Let sit for the time suggested by the resin manufacturer then move onto the flood coat. Bubbles will form, and a good seal coat will help to avoid them, but cannot stop all of them. Potentially, multiple seal coats could help prevent more bubbles.
Step 11: Resin Flood Coat
Clamp down the pieces as shown here for the flood coat. The slabs can also be screwed in from underneath if it is easier. The top will be planed so the effect of clamping will go away. Use small pieces of wood covered in Tyvek tape to be the main interface between the clamping boards and the slabs. This ensures they will be able to be removed later since resin will flow around them
Pour the resin for the flood coat. This step varies depending on which resin you get. If you have slow setting resin, you can pour all at once. However, first time users are not recommended to do the full amount all at once, and is recommended to separate mixing into stages to get a hang of it. If using fast setting resin, read the manufacturer label to see how thick you can pour. Using the volume estimated above and multiplying by (thickness pour/thickness of the table) you can get the amount to mix of each time. Fill all the way up to the top and fill over the top. The resin will lower in height as it fills in the cracks of the slab. A small torch or hot air gun can be used to pop the bubbles.
Step 12: Removing
Wait for the full set according to the resin manufacturer and then remove it from the mold. This could be a day to a week. Once the Resin is set remove it from the mold. Remove clamps and unscrew any screws that are holding the mold together. Remove sides, this can be accomplished by hand or by hammer if necessary. Do not worry about the look of the top or scuffing it using a hammer, these will go away in the next step. Once the sides are removed, remove the bottom. A pry bar can help or clamping one side while you break off the bottom in pieces if it gives you a hard time. If you covered it properly with Tyvek tape, it will stick slightly but you should have little issue removing it. The picture above shows how it looked right out of the form. There were lots of Bubbles and poor edges which get fixed next. This step will most likely destroy the mold, so don't worry about that.
Step 13: Surfacing and Planing
Surface the top and bottom of the piece after removing. A setup using a flat bit router and a sled was used shown here, alternatively a planer can be used if available. The sled was built from leftover melamine board. To make one, simply create a box around the object with constant height then make a sled that can slide over the box with enough space in the middle for a router bit. Height is just a little higher than the thickness of the board so the sled slides over freely. Take time to carefully go over each side, or just the top if the bottom is unimportant. It was cut as deep as needed to get rid of the imperfections, in this case about 1/8". It takes some time, however this was carefully done in one pass. Take multiple passes if needed. Sanding will get rid of the lines created.
Square the sides of the piece. To square the side, the piece was put through the table saw one last time for each side using the fence. Short sides can be cross cut.
Use a router to finish all edges and corners. Because the corners are sharp at this point, an angle router bit was used to make a 45 degree cut edge around all edges and corners. depending on preference different type of bit may be used.
Step 14: Final Sanding
Sand the final piece until smooth before the final coat. The piece was sanded from 60 grit up to 320, however 220 may be sufficient for the final coat. 60 grit is the most important and will likely take the longest. Alternatively, a drum sander can be used. Using a random orbit sander the lines from the finishing cuts/planing are slowly removed. Do not move on to the next grit size until all lines from cutting have disappeared. Once the lines are gone slowly move up to a higher grit size until you reach the highest grit.
Step 15: Final Coat
Finish the piece by adding one last coat of resin on top. This was brushed on with a much cheaper faster setting resin. However, before this was done, there was still a few bubble crevices at the surface with wood dust in them. A mini pick and air canister helped clean them out before pouring. Be sure to keep the piece in a warm dry place with minimal FOD (foreign object debris), such as wood dust. The piece was lifted up from the center of the bottom so the bottom edges could get covered with resin. Simply brush on the resin across the whole top and edges like in the seal coat phase. Take care to pop bubbles, and watch as the final form sets.
Optionally, it can be finished by polishing. This requires a lot higher grit sanding and eventually getting into polishing sets. It can be more time consuming and expensive if polishing tools are unavailable to start. It will give a less glossy look on the wood if that is desired.
Step 16: Support/Legs
Add legs to support the table. Simple Ikea legs were bought to support the table. There are many other ideas for support, please see references for more ideas. The entire table can support me sitting on it ~160lbs no problem.
Step 17: Final Notes & References
Bubbles were not originally intended, however they end up looking quite unique, see the picture here. To avoid them, maybe avoid sand, and take extra care during the initial seal coat.
The Resin was the biggest investment ~$300. Doing this over again, a larger piece of wood that costs not much more could have yielded a much larger table with the same amount of resin and minimal increase in price.
To see other cool projects of mine check out my website: https://ryanogilvie.weebly.com/
References:
[1] DIY Epoxy River Table with Waterfall, https://fixthisbuildthat.com/diy-waterfall-epoxy-...
[2] How to Make a Live-Edge Resin River Table: https://www.easycomposites.co.uk/downloads/How-to...
[3] How To Make a River Table Using Clear Epoxy Casting Resin and Reclaimed Wood, www.smooth-on.com/tutorials/river-table-clear-epo...
[4] Epoxy River Coffee Table, https://www.instructables.com/id/Epoxy-River-Coff...
[5] How to Make an Epoxy Resin River Table: do-daddy.com/epoxy-resin-river-table/
[6] What Is Epoxy? epoxycountertopdiy.com/
[7] How to make an Ocean Table // Concrete and Epoxy Resin, www.youtube.com/watch?v=xfqY0DTPlVg
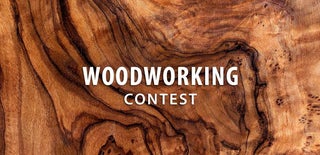
Participated in the
Woodworking Contest