Introduction: Ceiling LED Light
The goal of this instructable is to create a tailored ceiling lamp with a modern look, using mainly aluminium sections and LED strips. I made mine because I wanted a continuous ceiling light in a L shaped corridor using the only two hanging points available.
Materials needed
some U shaped, 20mm aluminium sections,
some LED strips (a 12V strip, along with an electric converter, is safer),
some fixing lugs if you choose to assemble several sections,
some electric cables and wire connectors,
a 3D printer,
- screwdrivers, a saw, a soldering iron...
Notes
The amount or length of materials will depends on your needs. The 3D printer is used to print the end caps, the hanging supports, and the translucent diffuser. If you do not own one, the caps and supports can be manually made using other materials, but I could not give any advice about the diffuser...
The choice of aluminium is to ensure a good rigidity, while keeping the weight low (you are going to suspend it over your head). It acts as a good heat sink, which helps the LED strips to last longer.
The LED strips can be cut in pieces, at some intended places, usually every 5-10cm. Ensure you buy a strip with enough cut marks for your chosen design. I strongly suggest to buy LED strips with a glued face to help the assembly. Finally, it far safer to use a 12V strip instead of a 110 or 230V, in case a wire gets loose inside the light fixture.
Step 1: Light Design
The first thing is to choose the shape of the ceiling light. You can choose a simple straight line, or get more creative. Due to my L shaped corridor, I had to assemble a least two aluminium sections; I then chose to add some extra sections across the two main ones to get a more pleasant design.
You can make your design on paper, or like me, create a simple view of the corridor in a 3D tool. To be honest, I amended my initial design while building the light... twice.
Once the design roughly known, you can measure the aluminium section and LED stripes lengths required. In my case, I needed a section length of about 7 to 8 meters.
In order to obtain a sufficient lightning, you will have to know the surface to be light up, and the use of the room, as the required light intensity will vary. Here are some figures :
- Circulation zone : 50 - 100 lux
- Living space : 80-100 lux
- Reading / working on a task : 400 - 500 lux
I had to light a corridor up, so I chose a 100 lux. The corridor being about 7,5m2 wide, this meant I had to ensure at least 100*7.5=750 lumens. Having 750 lumens on a 8 meters LED stripe is easy to achieve; I actually bought only 5 meters that I cut and distributed along the aluminium sections. This needed more soldering, but allowed me to lower the cost and obtain an adapted luminosity.
One important thing about the 12V LED stripes : check the power they require and ensure the converter is able to feed them. As an example, the power of my stripe is 24W and it runs on 12V, so it needs 24W/12V=2A.
Step 2: Sections Cutting and Assembly
The first thing is to place the sections on the floor, according to your design. This will allow you to better visualize the final result and to tune the design. Note that I chose to work on my floor, as I do not have a sufficient working space elsewhere. If you have to/can work elsewhere, then place frequently the parts back on the floor to detect mistakes early!
Place some tape marks on the floor to help you to keep the position of the aluminium sections during your work. Use a plumb line to know where the hanging points are. Then place the sections, amend your design, and cut them. It is better to cut the longest sections first, as a slight cutting angle error will produce a large shift on the extremities. If it is the case you will be able to (try to) correct the other sections angles.
If your design needs several sections attached together, use a fixing lug. Locate and pierce two holes, assemble the parts, then drill the other holes using the lug as a guide. That way you will minimize the risk of gap error.
Once the sections assembled, if your design contains crossing sections (like mine), use a saw to cut a path for the wires through the U section walls, and smooth the edges of all your cuts.
Drill holes for each of the hanging points (I had two hanging points), plus one more next to one other to pass the power supply wires. Once done, grab the sections at the hanging points and check the balance of the assembly. It is likely that it is going to tip; that means you will have to put 'crutches' to the opposite side to maintain the assembly horizontality.
Step 3: Power Supply
This part might be useless for those who do not have the same electrical socket as me. Mine is a standard IEC 61995-1:2005; I adapted an old spare electrical inlet to get a nice connector for my light.
I opened the power supply to replace the main socket pins by a white wire. I also replaced the output wire for a shorter one, and painted the box in white, so it blends with my ceiling.
I shortened the IEC connector, and soldered the supply's white wires. I printed a little cap to make things nicer. The file for this cap is included in this instructable's files in case you need it.
The result is a nice power supply with an IEC connector at one side and an output wire at the other side.
Attachments
Step 4: LED Strip Setup
If you use a 12V LED strip, connect the two strip wires to the power supply wires, using a connecting terminal (Wago alike). If you use a 110-230V LED strip, connect the two wires to the main socket, and, it is extremely important, screw the earth wire (yellow-green wire) to the aluminium section. If the earth wire is not connected, you could get electrocuted if a wire gets loose.
If needed, cut the strip in pieces distributed along the sections, then solder wires to connect each pieces together. Take care of the polarity, as the LED will not work if one connection is reversed. Do not forget to use heat-shrinkable sheath to protect solders and avoid short circuits!
Once the layout done, glue the LED strip inside the aluminium sections.
I buffed the aluminium sections using a cloth and some buffing cream for a better looking.
Step 5: Hanging of the Light to the Ceiling
Grab the sections at the hanging points and check the balance of the assembly. It is likely that it is going to tip; that means you will have to put 'crutches' to the opposite side to maintain the assembly horizontality.
I 3D printed the hanging parts and crutches using ABS, and inserted nuts in them to be able to screw them to the aluminium sections. I believe these parts could easily be made of painted wood (20x20x150mm sticks).
Screw the crutches to the aluminium sections, then screw the hanging parts to the ceiling, then screw the sections to the hanging parts. Connect the power supply and check all the LED are working.
The light diffuser I am using are 3D printed parts, made of transparent PETG. They might be build from transparent sheets, but I have no advice in that case.
I hope this instructable is clear and helpful; do not hesitate to leave a comment if you have a question!
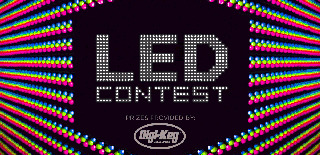
Participated in the
LED Contest 2017
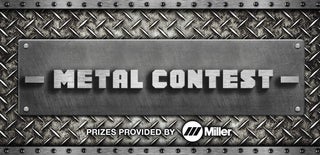
Participated in the
Metal Contest 2017
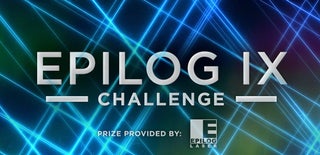
Participated in the
Epilog Challenge 9