Introduction: Cheap and Easy Solar Heater
Converting electricity into heat is one of the most expensive uses of energy. If you’re not convinced, look at the power usage of electric appliances like microwaves, space heaters, water heaters, ovens, or coffee pots. The difference can be seen between your electric bill from a cold month, when you have to continually run your central heating, and during summer months, when the ambient temperature does not need to be heated.
If you live off-grid, you tend to be far more aware of what it takes to create electricity; you can literally watch your batteries’ voltage drop lower and lower when using an inefficient appliance. However, if you are tied into the grid, you should almost be extra vigilant as regards your power usage. Not only do you have to pay for it each month, but also the power plants that produce your electricity are rarely sustainable or environmentally conscious.
When considering the issue of heat, there are several green options, the best of which is the sun. Solar thermal energy can be harnessed in many ways to heat your water, food, or home. For the purpose of this article, we will be concentrating on an active thermal space heater to heat a room or house. The unit takes one person two days to construct, one day to install, and costs under $100. The temperature inside the unit easily reaches 160 degrees Fahrenheit on a 50-degree day, and can be blown into the house using a fan that pulls less electricity than a light bulb.
Please note that the unit should be installed on a south facing wall (if that is not possible, then a west facing wall will at least give you heat in the afternoon).
An additional advantage for rural Mexico is that the production of these units can create a local business. A couple of people could start making them with very few tools and initial outlay. Any new business in a rural area will increase the wealth of that community, as there will be more money being circulated locally. Furthermore, people can apply to their municipal’s Presidency for aid in putting them in schools and community buildings, to reduce the amount of firewood that parents have to provide. If you are interested in starting an environmentally conscious business in Mexico, please see our Spanish version of this Intructable.
For more information, view How To: Solar Heater
Please visit VelaCreations.com if you're interested in seeing more of our how-to guides. You can also follow our projects through the blog or our books.
Step 1: Materials & Tools
Materials
One 8’x4’ sheet of ½” foam insulation, with foil backing
One 8’x4’ sheet of transparent, corrugated plastic
Three 10’ pieces of 4” metal channel
Two pieces of 24” x 13.5” sheet metal (for shorter room-see step 1)
Four 8’ pieces of molding (1”x1/2 “)
16’x4’ of black screen (metal or plastic)
One 8’ length of 4” dryer vent tubing (for shorter room-see step 1)
Two 4” hose clamps 4” 100CFM fan (if fan is 12 VDC, you will also need a converter from an old computer or printer)
Screened vent Snap switch (45C action, 30C reset, Normal Open, Thermostat Temperature Control Switch, we use model KSD301)
10’ of 12 gauge stranded wire
Cheap extension cord (to reach your nearest plug)
½” metal screws
1” wood screws
12 x 2” screws and concrete anchors
Staples
Silicon
Black paint
60” of 1” wide metal, 1/8” or ¼” thick
Insulation for the dryer vent (optional)
Tools
Tape measure
Marker
Tin snips
Chalk line
Wood saw
Clamps
Drill
Scissors
Staple gun
Caulk gun
Paintbrush
Chisel
Hammer
Masonry drill bit (long as possible)
Gorilla Glue
Electrical tape
Wire strippers
Step 2: Considerations
There are a few variations on this design, depending on the materials you have available and the type of room you will be heating.
FAN AND VOLTAGE
For the fan, you need to find a small, quiet unit that is capable of delivering at least 100 CFM. If you can find one of these that uses 110 VAC, then you don’t need anything else. Most small fans of this type are 12 VDC, which means that you need a converter from 110 VAC to 12 VDC. These converters are readily available from junk or surplus electronics, and are commonly referred to as “wall warts.” The converter should output at least 12 volts DC, and double the amps your fan is rated for. This gives enough room for the fan’s startup surge.
SIZE OF PLASTIC
The first problem you may encounter is the size of your transparent, corrugated plastic. If you can find a 4 feet sheet, so much the better, as that will match the size that the insulation comes in. However, if you can only find a 3 feet wide piece, don’t worry. You can still use this design, but you will have to cut your insulation down to fit it, and then adjust the metal channel walls, so that they too match the new size.
HEIGHT OF THE ROOM
The next issue is the inside height of your room. You will have two holes through your south facing wall, one at the top and one at the bottom. Air will be drawn from the bottom hole into the bottom of the heating unit outside. This is because it will take less energy to heat the air from inside the house than from outside, as it will already be warmer than the external temperature. The air that has been heated by the unit will then blow down into the room from the top hole. The problem with this is that, in order to make the most out of your heater, you will want the distance between the outside edges of the two holes to be about 8 feet (a little less is OK).
If your room is eight feet tall, construction of the unit will be easier, cheaper and more efficient. Easier, because you will be able to cut a hole through the bottom and top of the heater’s backing (insulation), instead of having to go out through the sides of the heater’s wall, which is more complicated. Cheaper, because you will need less 4” dryer vent, as it will be going straight through the house’s wall, instead of having to curve to the side before going inside. More efficient, because the temperature inside the unit will match the air coming into the room, whereas if you have to go to the side, you will lose a little heat through the extra dryer vent. You can compensate for this by painting the exposed vent black, or, even better, wrap it with insulation.
During the course of this article, we will be mostly describing how to attach this unit to a smaller room. For a start, it is probably more common to have rooms that are less than eight feet tall. Secondly, it is more complicated, and therefore requires a little more explanation. However, wherever the instructions differ for a tall room, we will add notes in bold.
Step 3: The Metal Sides
- Mark a piece of 10 ft. metal channel at 104” from one end (8’ 8”).
- Using the tin snips cut off the remaining 16” and put it aside for now.
- Measure and mark 4” in from each end of the 104” channel.
- Cut the sides of the channel off along these 4” parts, leaving a 4” tab on each end of an 8 feet length of channel.
- Mark one tab with a B for bottom, and the other tab with a T for top.
- Repeat 1-5 for another piece of 10ft. channel. These are the two sides of the heater box. Place them side-by-side, with both tabs marked B at the same end.
- Pre-drill holes, every 12” or so, along the inside edges of the 4” part of the channels. These holes need to be a little smaller than the 1” wood screws you will need to attach the metal to the insulation. The holes should be 1/4” from the side of the channel.
- Pre-drill holes, every 12” or so, along the 1” upright part of the channels that is on the outside (with the two channels side by side). These holes need to be slightly smaller than the ½” metal screws you will use to attach the plastic, and should be about 1/4” away from the edge of the metal.
Step 4: Insulation Box
- Using the wood saw cut two 8 ft. pieces of molding.
- You want to clamp these pieces of molding to the 4” part of the pieces of channel, but at a diagonal. The ends near the B tabs want to be ½” in from the inside edge, so that when the two channels are side by side, the molding from one channel will be close to the other at the B end. The insulation (which is ½” thick) will eventually slot into this ½” space.
- The other end of the molding, near the T end of the channels, wants to be 1” from the outside edges. This is where the corrugated plastic will eventually slip in.
- Once you have the molding tightly clamped to the metal, turn the metal over and screw it into the wood (through the metal). You may need to pre-drill through the metal. Your screws should be every 12” or so.
- Turn the two channels up on their sides, facing each other, so that the molding that is ½” in from the side is on the bottom.
- Place the insulation in between the channels, slipping it inside the metal and the bottom molding.
- With the 1” wood screws, screw it in place using the holes you pre-drilled in the previous section, going through the metal and into the side of the insulation.
- Cut a piece of molding, 47” long (this is the width of the insulation, 48”, minus the thickness of the two side pieces of molding, ½” each).
- Place this 47” piece inside the two side pieces of molding, in roughly the center of their 8 ft. length, and screw it in place.
- Paint the whole inside black.
[If you have an 8 ft. tall room, as described in Step 1:Considerations, you will need to do the following steps at this stage:
11. Cut two 4” holes through the insulation (you can put your 4” dryer vent in place against the insulation and draw around it to get the right size). One hole needs to be in the center at the top, with its top 2” down from the edge, and the other in the center at the bottom, with its bottom 2” up from the edge. The distance between the top of the first hole and the bottom of the second hole should be 92”.
12. If the unit can fit inside the house, place the unit up against the wall where you want it to go, and mark the two holes, through the insulation, onto your wall.
13. If the unit doesn’t quite fit inside the room, but almost, drill a hole through the wall from the inside, a little up from the floor. Make sure you drill straight, not sloping up or down.
14. Then drill another hole through the wall, exactly 92” straight up from the first, but near the ceiling.
15. Hold your unit up on the outside of the wall, so that the very bottom of the bottom circle is just below the drilled hole, and the very top of the top circle lines up with the top drilled hole. Make sure the unit is level up and down, and then mark the wall through the 4” circles.]
Step 5: Screen and Plastic
- Lay the 16 ft. x 4 ft. screen out inside the box (you will have 8ft. of it that is on the ground outside of the box.)
- Staple one edge of the screen to the underside of one piece of molding.
- Pulling the screen taut, staple the other edge of the screen to the underside of the opposite molding.
- Fold the excess screen into the box and staple one edge of it to the top of one piece of molding.
- Pulling the screen taut, staple the other edge of the screen to the top of the opposite molding.
- Place the corrugated plastic on top of the screen. Clamp one 8 ft. edge under the lip of one piece of channel, and screw them together through the predrilled holes, using ½” metal screws.
- Clamp the other 8 ft. edge under the lip of the opposite channel and screw them together through the pre-drilled holes.
- Bend the 4” tabs of the channel at right angles, in toward the center of the heating unit.
Step 6: Top and Bottom Manifold
- Out of the last piece of 10 ft. channel, cut out two 4 ft. lengths. These are the top and bottom of the box.
- Cut four pieces of molding, about 12” long each.
- Screw two into the inside of one 4 ft. piece of channel, about 6” from either end, and 1” down from the top (for the plastic to rest on).
- Do the same with the remaining pieces of molding and 4 ft. piece of channel. [If you have an 8 ft. tall room, as described in Step 1:Considerations, you can skip to the next section]
- Draw two rectangles on the inside of each piece of channel. The rectangles should be about 2” x 4”, centered both horizontally and vertically, and about 1.5” apart.
- Take one of the 24” x 13.5” pieces of sheet metal and lay it of a flat surface.
- Along one 24” length make marks at 2”, 6”, 7.5” and 11.5” from the right-hand side.
- Do the same along the other 24” length, also from the right-hand side.
- Make a chalk line along one 24” length (parallel with the marks you just made), 2” in from the edge.
- Do the same along the other 24” length, but only 1” in from the edge.
- Draw a line from each of the marks you made to the chalk line closest to it.
- Cut out the two rectangles that have been formed on each edge, the first being 4” wide and 2” from the end, the other being 4” wide and 1.5” from the first.
- Place the side of the sheet metal that has deeper rectangles on the back of the channel, lining up the rectangles of the two materials.
- Clamp and put some ½” metal screws in along the 4” length of the rectangles.
- Now bend the sheet metal so that it forms a tube, and line up its shallow rectangles over the holes of the channel.
- Clamp and put some screws in all around the rectangles, including the overlap.
- Now you want to make two caps, one for each of the manifolds you just made. You will be using left over pieces of channel to make a roughly circular shape (it’ll actually be more pill-shaped). It wants to include pieces of the upright parts of the channel, as these will be uses for tabs. You also want to make two extra tabs on the flat part, which you can bend up. Look at the photo above for clarification.
- Place these caps on the end of the manifolds that you want sealed (the opposite end of where the dryer vents will be entering the house). Make sure all four tabs are on the outside of the manifold.
- Screw the cap in place with ½” metal screws.
Step 7: Completing the Box
- Slot the two 4 ft. pieces of channel into the heater box, making sure that the insulation and plastic are inside. You want the tabs from the 8 ft. lengths to be on the outside.
- Put a few screws from the channel into the plastic, and from the channel into the insulation.
- Screw the tabs on the box’s sides into the top and bottom channel.
- Run a bead of silicon around every seam, to make sure that it is all airtight. Make sure you get the cap and sides of the manifold, as well as all around the plastic and insulation.
Step 8: Holes in the Walls
This step is largely dependent on the type of walls you have and how thick they are. The principals are the same, but solid concrete walls, for example, will be a lot harder than adobe, and will take you longer. If you have loose fill inside your walls, you will have to be prepared to support the fill as you chip out the wall, as they do in mines, so that the fill doesn’t all fall into the room.
- This step is likely to make a mess, so it’s a good idea to put sheets over your furniture against dust, and tarps on the floor for the chunks.
- If you have an 8 ft. tall room, you will already have marked your holes on the wall (in the section headed “Insulation Box”). If you have a short room, you will need to mark your walls now. Know roughly where your panel will be hung, as these holes will be to one side of it.
- On the inside of your room, hold a piece of dryer vent up to the wall close to the floor (about 1” or 2” up from the bottom). Draw around the tube onto the wall.
- Do the same up near the ceiling. The two holes want to be in line with each other.
- Using a long masonry bit, drill some holes on the inside of the circles you have marked. Make sure you always drill straight, not angling up, down or to the sides. You can also drill some in the center.
- With a chisel and hammer, start tapping out the material of the wall. You want to go all around the circles you marked, and then the center.
- Once you have chipped out a circular tunnel as far as you can, you’ll need to go to the other side of the wall and begin there. If your drill holes were straight, you should have a pretty good idea of where that circle is. If not, drill a hole through the center and look through it to make sure it is straight. Then draw a circle around this hole with a 2” radius.
- When the two holes are complete, try putting your dryer hose into them. You will probably need to chip little bits out.
- Take your fan and center it over the top hole. If it is square or larger than the hole in any way, draw its shape onto the wall. Chip out this shape a little more than the thickness of the fan, so that it can sit inside the hole without any part of it sticking out.
- Your major mess making is now over. You can clean up the worst of it, just to get it out of the way, but don’t worry about dusting the house just yet!
Step 9: Mounting the Unit
The unit will be almost upright, although the bottom wants to be held a couple of inches out from the wall and the top touching the wall. This slight angle means that the bottom wall braces will be slightly less than right angles.
The heater is not that heavy, so the weight to be supported is not much. The braces are more to protect it from wind damage.
- Cut the 1” metal strip into two lengths of 12”, two lengths of 10”, and two lengths of 8”.
- Drill two holes, evenly spaced, into the last 4” of both ends of each piece of metal. The holes should be large enough for your masonry screws to pass through.
- Bend the 12” strips at less than right angles. The upright part (which will attach to the wall) wants to be about 4” tall, and the horizontal part (the last 4” of which will attach to the heater) will be about 8”. These are your bottom braces.
- Bend the 10” strips of 1” metal until they are at right angles. The upright part (which will attach to the wall) wants to be about 4” tall, and the horizontal part (the last 4” of which will attach to the heater) will be about 6”. These are your side braces.
- Bend the 8” strips of 1” metal in the middle until they are a little greater than right angles. These are your top braces.
- Place these two bottom braces up against the wall where you want to mount the heater, about 36” apart. Make sure the two braces are level with each other.
- Through the holes in the brace, mark the wall.
- At these marks in the wall, drill holes, 2”deep and just large enough to squeeze your concrete anchors in.
- Put a dab of gorilla glue on each concrete anchor and push them into their holes.
- Place the braces back against the wall, lining them up with the holes in the wall and screw them into place with the 2” masonry screws.
- [If you are making a unit for an 8 ft. tall room, you will now need to attach your dryer vent to the holes in the back of your insulation.
- The top one wants to be the thickness of the wall and the bottom one wants to be the thickness of the wall plus 2” or 3”. Dryer vents are like accordions – once you have cut your pieces, stretch them out a little so that they are a little longer)
- Put the shorter vent into the top hole of your heater, and push it in about 1”. It’s a good idea to attach it by cutting a couple of 4” x 1” strips out of some left over channel, bending them into right angles, and then screwing one part of the “L” into the vent and the other part into the insulation.
- Put a bead of silicon all the way around the dryer vent.
- Do the same for the bottom hole, using the longer dryer vent.
- Now, as you put your heater onto the bottom wall braces, you will want to feed the dryer vents gently into the holes in the wall. This will require two people.]
- Lift your heater onto the bottom wall braces and center it over them.
- Using self-tapping screws, screw the horizontal parts of the braces up into the bottom of the heater.
- Position the side braces about half way up the heater, one on each side.
- Mark the wall through the holes in the braces.
- At these marks, drill holes, 2”deep and just large enough to squeeze your concrete anchors in.
- Put a dab of gorilla glue on each concrete anchor and push them into their holes.
- Place the braces back against the wall, lining them up with the holes in the wall and screw them into place with the 2” screws.
- Using self-tapping screws attach the side braces to the heater.
- Position the top braces, about 36” apart, on top of the heater.
- Mark the wall through the holes in the braces.
- At these marks, drill holes, 2”deep and just large enough to squeeze your concrete anchors in.
- Put a dab of gorilla glue on each concrete anchor and push them into their holes.
- Place the braces back against the wall, lining them up with the holes in the wall and screw them into place with the 2” screws.
- Using self-tapping screws attach the top braces to the heater.
Step 10: Dryer Vents
[For the 8 ft. tall room model, your dryer vents should already be through the wall. Gently stretch or pull the accordion to bring them flush with the wall on the bottom or flush with the beveled out part for the fan at the top. If you find that you have to push hard, get someone to hold the vent on the outside of the wall, and push against them rather than against the insulation of the unit.]
- Take a section of dryer vent and gently put it around the open end of the bottom manifold on the heater.
- Once you’ve got it on properly, about 1” overlapping, put a 4” hose clamp over the join and tighten it.
- On the top manifold, take your snap switch and fix it against the side of the solar heater. The switch should be firmly pressed against the metal, you can use some wire or a screw to hold it in place. Attach 2 wires to the snap switch, with the length being long enough to go from the switch to the fan on the inside wall.
- Feed the wires through a dryer vent, and attach the vent like you did on the bottom manifold.
- Feed the two dryer vents into the holes in the wall. Dryer vents are like accordions, so you can pull them apart or push to change the length. You want the bottom vent to be flush with the inside of the wall, and the top vent wants to come to the beveled out part for the fan.
- With a little mortar, stucco around the vents against the wall, both inside and outside.
- Paint the part of the vents that are showing on the outside black. Even better would be to wrap them with insulation, especially at the top, to prevent wasted heat.
Step 11: Fan
- Pull the wires from the snap switch through the dryer vent from the top manifold. These will attach to your fan on the positive line.
- Fit your fan in place, and attach one of the wires from the snap switch to the positive wire of the fan.
- If your fan is AC rated, then cut the extension cord, leaving enough wire to go to a wall outlet and then connect to the fan. Connect one wire of the extension to free wire of the snap switch, and the other wire to the fan. Skip to step 5.
- If you are using a converter, then cut the appliance-end adapter from the converter cord. Plug the converter into a wall outlet, and with a multimeter, test the voltage coming from the converter. This will also show which line is positive and which is negative, as your multimeter will read a positive voltage if the leads are on the correct wires (red to positive, black to negative). Attach the positive to the free wire of the snap switch, and the negative to the negative of the fan.
- Plug the converter into the wall to test. It should come on, if the solar heater is in direct sunlight. If it does not come on, then unplug the converter, and wire the positive line from the converter directly to the fan’s positive line. Plug it in again to test. If it works this time, then you may have an issue with the snap switch (either it is too cold, or it is not making good contact with the solar heater).
- Once the fan is tested and working correctly, unplug the converter, and insulate all connections well with electrical tape. Push the wires into the dryer vent, and then put the fan in its place. Secure the fan against the wall with screws. The fan needs to blow air into the room, so make sure you put it in facing the right direction (blowing, not pulling, air).
- Attach the vent cover over the fan and screw firmly into the wall.
- Attach the bottom vent cover over the bottom hole and screw into place.
So now you have a brand new solar heater installed. As long as there is sun, the fan will run and heat up your room. The air coming from the fan will be nice and warm, but it won’t get hot enough to burn or damage anything.
During the warmer months, you can unplug it and remove the top dryer vent from the manifold to prevent hot air entering the home. Alternatively, just cover the solar heater with a thick blanket to prevent any solar gain.
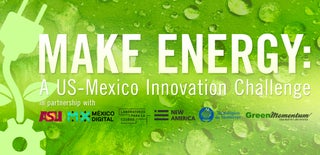
Second Prize in the
MAKE ENERGY: A US-Mexico Innovation Challenge