Introduction: Chevron Pattern Plywood Corner Desk (motorized)
Disclosure: As an Amazon Associate, I earn from qualifying purchases at no extra cost to you.
A beautiful table top made of 3/4-in baltic birch plywood and mounted on an adjustable motorized corner desk frame. The end grain and top finish makes this table an amazing piece of art.
If you are looking for a very unique corner desk without breaking the bank, this is an option. Use an adjustable frame or just some hairpin legs and you will wow everyone visiting you!
The same table frame (picture below) with table top included cost upwards of $1900. The frame alone is available for $550 from different sellers on Amazon. Click on the desk frame picture below to see all options on Amazon. They also have standard frames if you don’t have the space for a corner desk.
Supplies
Supplies:
- 1 to 2 Baltic Birch Plywood Sheets (depending on the planned size and desk top thickness)
- 1x Titebond III (wood glue)
- 1x Wax Paper
- 1 bag 3/8 in wood dowels
- 1x ProMarine Table Top Epoxy
- 1x T-88 epoxy
Tools:
Step 1: Cutting the Strips
Before getting to work, I researched the possibilities of using plywood to make incredible patterns. I settled on the idea to make some kind of herring bone pattern. The issue was that all projects I found where small and joint techniques used were just not feasible for the size of table top I planned.
The first thing I did, was building a sample I could use to test out different finishes and also to see the pattern in small scale.
So I got to work. I did a short trip to my local lumber yard and got 2 8’x4′ baltic birch plywood sheets. I used my Festool Track Saw to cut 1-in strips from the plywood sheets.
Why 1-in strips? The width of the strips determines the table top thickness (since we want to see the end grain, the strips will be flipped around to end grain up). When flipping the strips 90 degrees your strip width becomes table top thickness. You can make it thicker or thinner, but bare in mind that with a large table top you definitely want 1in+ thickness.
I know it would probably easier to use a table saw but I only have a regular job site table saw with no large fence or out feed. Space limitations in my garage also prevent building something stable for my table saw.
Step 2: Alignment and Glue Up
For the glue-up I tried as best as possible to align the pieces in a 45 degree angle to reduce waste when cutting them later in 45degree. So use a triangle and align the strips so the outside is 45 degree.
After you did your dry run, carefully flip the pieces 90 degree so you have the glue side up without messing up your carefully aligned 45 degree edge. Now spread glue over maybe 5-6 strips and flip them back 90 degree so the glued sides touch each other. Repeat that until you have all strips glued to each other.
As you can see the phrase “you can never have enough clamps” is true. I actually had to order some. After reading some reviews I went with 6 Dewalt 36in Bar Clamps, 4 Rockler Sure-Foot 48in Clamps, 8 large Rockler Bandy Clamps (for the thinner end)s and 4 Bessey pipe clamps in addition to the Irwin and no-name clamps I already had, just for that project. To reduce clamps needed, I used some scrap pieces to able to tighten 2 strips at the same time (as shown in the 4th picture above).
Step 3: Cutting 45 Degree 3 Inch Strips
Waiting 24hrs for the glue joints to cure I could move to the next step of cutting 3 inch wide strips in a 45 degree angle. Now you can see the reason why aligning your glue-up in a 45 degree angle pays off. Use the right angle triangle and the track of the track saw to make your 45 degree cuts. You do not have to make them 3 inch wide, the narrower you do them the more glue up you will have, and opposite if you choose wider strips.
After the cutting I laid them all for building sections. That step lets you adjust pattern lines and mix and match different 3 inch steps.
Step 4: Glue Up of 3 Inch Strip to Form Sections
Now I had 31 of 3 in strips in 45 degree angle which I glued together to sections with 4 strips each (12in wide). I have a 12 inch planer and keeping those sections below 12 inch will enable me to make use of the planer later. I did use the PowerTec dowel jig to install dowels for a bit of extra strength in the joints. Then I clamped them down to the table, if you used dowels the alignment shouldn't be problem. To prevent accidentally glueing the support to the workpiece, I used wax paper which is easily removed after the glue cured.
I did run all sections through a planer to remove excess glue and have them all in the same thickness. Do not take off to much and make multiple runs through the planer.
Step 5: Glue Up of 12 Inch Sections
I repeated the previous step until I had 7 ( + 1 backup) sections and half a section to reach my desired table top length. Will all sections ready, I went on to focus on one side of the corner desk. Here I joint 2 section vertical. It was tricky because the sections where not good aligned and I had to play around which section fit best into each other. I used 8 dowels per section to add a bit of extra strength and keep them aligned during the glue up.
As you can see in one of the pictures, not everything worked out well! Since the project stretched over several weeks, the pieces started to warp and deform. After testing the joint for the last 2 vertical joined section, I found they are not perfectly fitting and there was a huge gap. Bummer! Well I started to carefully sand down the other edges until the gap was so small that I could fix it with some wood filler.
After the hiccups mentioned before, I went to work and joined the finished 2-piece-sections together (parallel).
The PowerTec dowel jig definitely came in handy for that project. Every time I joined pieces I used dowels to help keep them align. The jig works well if you take your time and make sure you perfectly aligned the guide line on the jig with the line you made on your workpiece.
Step 6: Forming the Final Shape
After the glue cured on the larger pieces in the previous step, I started adding small sections to form a L shape. Same methods were used, dowels between the sections and Titebond III. You will need the pipe clamps in this step.
After the final piece glued up and curing, I used again the Festool Track Saw to cut the top to final dimensions and remove the serrated edge. Now the table top slowly took its shape.
When cutting the last edge I leave the triangle on the inside corner. I used a duct tape role to draw a half circle for a round cut. Using my Ridgid jig saw and extra thin blades, which made the round cut way easier.
With the cuts done I went on to use my Ridgid router with 1/2in round over bit to form the top edge. For the bottom I used a 1/4in round over bit from my round over bit set.
After starring at the table for like 20min I felt bothered by something. The corners! Since I made a round inside corner I decided it would look way better if all corners have the same radius. So I applied the same duct tape role method to each outside corner. Using my jig saw I got to work and rounded all outside corners.
Step 7: Adding Some Strength
Now I paid my attention to the bottom side. The whole piece is wobbling if you move it. I didn’t expect anything else to be honest. To add more strength to the table top I choose to add a 1/8in layer of epoxy to the bottom side.
First I started with sanding down the surface in preparation for the epoxy. I cleaned carefully all the dust with a air pressure hose and wiping off with clean rags.
With a clean surface I added a really thin epoxy seal layer first. Just mix a small amount and brush the epoxy over the whole surface, covering every inch.
The next day I did the flood coat. I used ProMarine Table Top Epoxy and needed around 25 fl oz. Keep in mind, that is the bottom, so it didn’t need to be super pretty. How ever, I still went over with my heat gun to burst any bubble building up in the epoxy.
Step 8: Mounting Holes
Against the product instructions, I continued to work on the table top after 24hrs (the cure time for that epoxy is 72hrs, so make sure you follow the instructions if you use it for a visible area). The next morning back in my drive way (taking the risk and ignoring the 72hrs cure time) I went on to install the threaded inserts on the bottom side. I placed the table top on the desk frame, aligned it perfectly and marked locations to pre-drill the holes.
With the holes pre-drilled I used the Big Gator drill guide and the drill bit included in the EZ-Lok threaded insert kit to prepare for the threadedinserts.
At the beginning, I created a sample before I did anything else. That sample I also used to test out the threaded inserts. It failed miserably. I mounted the sample on the desk frame and was able to rip the sample of the desk frame. So I went to the Facebook woodworking group and asked for advise. The suggestion I got was to use T-88 epoxy in the hole before screwing in the threaded inserts. So I tested it again with the sample and the result was impressive, I was not able to rip out the sample.
To make sure you don’t gum up the threads, use painters tape and close the bottom end of the threaded insert. Tighten the tape after you cut the excess off with a cutting knife. Then fill the prepared hole half with T-88 epoxy and screw in the insert. Wipe off any excess immediately and move on to the next hole.
Step 9: Final Touch
With the threaded inserts done, I flipped the table top and focused on the finish.
First I filled any voids in the table top with wood filler. Patiently (after weeks of work) waited for the filler to cure and sanded down to 150 grit using an orbital sander to prepare for the epoxy.
I used the same ProMarine Table Top Epoxy and just did a seal layer. Brushed it on carefully and removed any excess. I didn’t want any shiny area (those would need to be removed by carefully hand sanding).
I let it cure, sanded carefully and added another seal layer (very thin).
After the epoxy was cured I used a buffer and mineral oil and buffed to the final finish.
Step 10: Mount the Table Top to the Frame
Well, you made it! Now just mount the table top to the frame and enjoy your hard work. I do enjoy my work every time I sit on that desk, it feels very nice and it's unique.
If I was able to bring you some inspiration for your next awesome project, please consider inviting me to a beer 🍺 😎
Visit my blog: https://woodcraftly.com
Thank you!
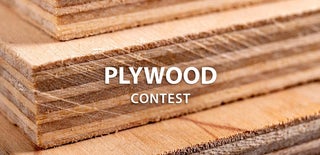
Grand Prize in the
Plywood Contest