Introduction: Coffee Kuksa
Traditionally, a Scandinavian Kuksa is carved from birch burls due to their ultra-dense wood structure. This helps kuksat resist rot and generally be more durable when used as a liquid receptacle. Overall this construction is a beautiful alternative to plastic, ceramic, metal, and glass cups, but it has one crux: hot liquids will heat the wood and release woody flavors some may find undesirable. Most wood finishes, oil or water based, resin sealants, and polyurethane share this weakness to heat. Fret not coffee lovers; a stainless steel liner makes a kuksa coffee friendly and more durable. Follow this instructable if you'd like to learn how to make your own coffee kuksa.
Supplies
- Safety glasses, a dust mask or HEPA filter, and ear plugs for the routers (Safety first).
- Wood block 6" x 6" x 2.30" - I used a rough cut 6x6 cedar post chopped to size with a miter saw.
- Stainless steel bowl - found here on amazon.
- Woodworking tools
- Sand Paper - I used 100, 220, 400, and 600 grit
- CNC milling machine - I used an Inventables X-Carve. Hand carving tools would also suffice.
- Rotary tool with sanding drum - I used a 4300 model Dremel with the 407 1/2" sanding drum.
- Fusion 360 - free for hobbyists, students, and small businesses.
- Butcher block/cutting board oil - I used walrus oil.
- Coffee - I used some delectable kona coffee.
Step 1: Design
The stainless steel bowl linked in "Supplies" was chosen due to its relatively low height and 4.2" (107 mm) diameter. First of all, the bowl needed to fit under the x-carve's Z (height) clearance of 2.64" (67 mm) with room for one thickness of wood below (the floor of the kuksa). Second, the diameter of the bowl needed to fit within readily available wood sizes with room for two thicknesses of the wood (the kuksa's walls) and the handle that's a key feature of a kuksa. See photo 1 of bowl.
Once a bowl was selected, height, top diameter, and lower diameter measurements were taken with calipers and drawn in fusion 360. An offset of 10 mm was used to create the wooden wall. A handle was added with a somewhat arbitrary shape that looked ergonomic. A 3/4" (19 mm) hole was added per the diameter of my middle finger. See photo 2 of fusion 360 design.
Cedar was selected for the wooden structure due to its rot resistance, relatively low density (making the cup lighter), and regular availability in 6x6 or 4x6 beams. Time will tell if this softwood is strong enough for this application. Thickness of walls and handle could be adjusted in the future.
Help yourself to the fusion 360 file attached for CAD and CAM.
Attachments
Step 2: CAM (Computer-Aided Manufacturing)
Once the design was complete, the Manufacture workbench in Fusion 360 was used to generate gcode.
The setup shown in the first photo shows the wood block in yellow. Dimensions for the stock work piece were taken with calipers, modeled as a block, and selected in the setup menu. This is necessary to orient the kuksa diagonally.
The first step takes a bulk of the material off the top face.
The second step clears more material on the top to prepare for the scallop tool path in step 4.
The third step creates the rounded bowl pocket for the stainless steel insert. The finish of this pocket ends up looking a little like a 3d print due to the incremental step downs the bit takes.
The fourth step traces the contours of the bowl in 1 mm step downs creating a surface that can be easily sand-able.
Finally, the contour step cuts out the last 10 mm of thickness and leaves little tabs so the kuksa doesn't move on the final pass.
Be sure to simulate the tool paths and watch for any red indicating the machine crashing. I could see the last contour toolpath made the collet crash so I knew to lower the bit before carving this step.
Once satisfied with the simulation, export gcode using the easel post processor.
Step 3: Carving
The gcode is imported into an easel project.
I used an endmill to carve out some steps for the clamps to hold on to first, keeping in mind where the kuksa won't be. This project really maxes out the stock xcarve height as one can see in the third photo.
After carving steps 1-5 in the CAM process, the round-over bit is used to create a fillet around the bottom edge. See the fourth photo for how I set this up on the xcarve. I'm not sure the rough finish of this fillet was due to the low quality bit or the unconventional use of the xcarve. I'd recommend using a high quality round-over on a standard fixed router table.
Cleaning up the kuksa from the fifth to sixth photo was done with the rotary tool with a drum sander. The more ergonomic handle and hole were also created by sanding away. Wear a dust mask or HEPA filter!
Step 4: Finishing
Bonus: I tried staining a first iteration with coffee and coffee grounds, letting it soak in a pot, submerged with some weight for 12 hours. The color difference and protection seemed inadequate so I decided on another finish..
Keep your dust mask on and get out the sand paper! Start with 100 grit, working in multiple directions sanding every surface. Move through the grits you have available. I stopped at 600 grit to get the results shown in photos 2 and 3.
Wash down the surface with light soap and let dry or 12 hours. Apply butcher block oil generously, wipe away excess, and let dry for another 12-24 hours.
The stainless steel bowl should be a slight press fit. I plan to keep this removable for easy cleaning.
Finally, brew some coffee and enjoy! :)
Questions, comments, positive remarks, and feedback are all welcome. Cheers instructables community!
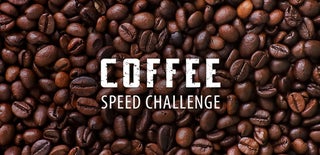
Participated in the
Coffee Speed Challenge