Introduction: Coffee Table From Reclaimed Bowling Alley Lane - for a Non-woodworker Living in Tiny Apartment
Never made anything out of wood before? Don't have wood-working tools? Or even, frankly, a garage or driveway to do woodworking on? Me neither! But I still ended up making this table, and here's how.
I first decided to make a coffee table because it seemed easy - a piece of wood, four legs - and then in typical me fashion I decided to go with something really complicated and found a 4' x 18" reclaimed bowling alley lane from BuildItGreenNYC. Make sure that you get the piece to the size you want since it is very hard to resize bowling alley lanes due to the nails in the middle.
Note that since I was new to this there are probably a lot of things that could have been done way better.
Cost for the wood piece: About $40
Cost for the whole thing: Definitely $250 - $300
Step 1: Sand the Incredibly Dirty Surfaces
First, here are two other blogposts I used for frequent inspiration: this guy is clearly a wood-worker and did something way more intense than I could, and these people, while new to wood-working, clearly have the space and ability to work on a table, both of their lessons helped. Lastly, I relied heavily on the lumberjocks.com forum. Amazingly helpful people there.
The top of the bowling alley lane is caked with years of finishing, dirt, crap, I don't know what else. The bottom is full of gross black paint. To remove these things you need a belt sander and a really rough sand paper. The lower the grit number, the rougher the paper is. I rented a belt sander from the Red Hook Home Depot and bought 50-grit paper for it.
I bought a 100' extension cord that I ran from the apartment basement to the sidewalk. It took me about 2 hours to sand the whole thing. I worried about people complaining but I forgot about the general New Yorker rule which is to always walk by anything that looks weird as if you're totally used to it so nobody said a thing (except the one guy who said I looked hot).
This trip to Home Depot: About $50 for the sander, some different sandpaper, goggles, face mask, maybe gloves
Step 2: Add Horizontal Bars Across the Bottom for Stability
The next thing that makes bowling alley lanes unique is that the strips of wood are not really adhered together very well since they normally just sit on the floor. Nails hold them together. If you don't secure the bars then over time the table will sag towards the middle. The other two bloggers I followed used a router and a square aluminum bar. A router was an additional power tool I didn't have the ability to use, so I decided to put the bars on without a router.
Problem: Home Depot doesn't cut metal bars to the size you want so getting a square aluminum bar seemed like a bad idea. Instead I bought flat aluminum bars and a $5 hacksaw to cut them. I also thought there would be holes drilled in it already, which there weren't, so I bought a drill bit that would go through aluminum.
Lastly, since my aluminum bars weren't as stiff as square ones, I should put them on diagonally so it would be less bendable. I don't know if that's true but it makes sense to me.
I cut the bars with my hacksaw on a bench outside with little plastic clamps to hold them in place ... and my husband who sat on them.. in about 30 minutes. This part I definitely couldn't have done on my own because without someone holding the bars it would have been impossible to saw through them.
I hand sanded the edges of the bars since they were now a bit jagged from the sawing.
Then I measured holes and drilled through the bars with my new drill bit. I staggered my holes so that each strip of the bowling alley lane has at least one nail in it somewhere.
I ended up putting the bars on after I added the table legs, pictures included. Screwing is really difficult, I discovered! This is supposed to be pine but I think it's very hard pine. I ended up having to drill pilot holes (using the guidelines for hard wood), AND put wax on each of my 1 1/2" long screws, and I still ended up with a few screws I can't get all the way in. One suggestion was to use brand name screws, which I didn't for these bars.
Lastly, although Build-It-Green! removed most of the protruding nails on the side of the wood they left one in which was really bothering me. I had concocted all kinds of ways to deal with it until my dad told me to use a hacksaw. So that same $5 hacksaw got rid of the nail!
Cost: $60ish for metal bars, screws, clamps, drill bit, hacksaw
Step 3: Finish the Top - Add in Lane Markers
I decided I wanted to make triangle lane markers on the bowling alley lane. This was the stressful part of the project - finishing the top.
I decided to use a stencil to stain the shape I wanted. This seemed easy, according to the internet. I bought a Minwax stain and made a little stencil out of stencil material I bought at Michaels. The first picture shows how much that did not work when I tested it on the back (the square blob).
I realized you're supposed to put some varnish on first, otherwise the stain bleeds, and to use painter's tape instead of a stencil. That still didn't work (the small triangle in the same picture).
With both of these failed experiments, I was going to skip the lane markings altogether but got two suggestions:
- Use Frog Tape instead of generic painting tape
- Use Minwax gel stain which is thicker
This worked beautifully on the back - you can see the picture with the painter's tape! I applied the Minwax gel stain liberally, rubbed off the excess almost immediately with an old rag, and presto!
On the front though, I left the stain for a couple of minutes which resulted in a thicker paint-like stain (described below), but it still worked.
Before staining, I added 2 layers of Minwax water-soluable varnish to the front, sanding all over by hand with 220 sandpaper between applications.
Then I measured out the triangles. Regulation bowling alleys allow triangles of at most 1 1/4" width at the base, and 6" long (but can be smaller than this). The placement of them are every 5 wood strips and they form a triangle of 7 in total that from top to bottom are about 3'. With all this in mind I figured out where to place each triangle and used my Frog Tape to create stencils.
When I added the stain, I decided to let the Minwax gel sit for about 5 minutes and then tried to rub it off. The Minwax gel is already goopy and it was like trying to rub off almost completely dry Elmers glue. It's also not water soluble. I tried to sand it down a bit after it dried - bad idea. It was a bit sticky so sanding it just made it look dirty. I ended up doing another layer of stain to get rid of the dirtiness and decided that I like the look the way it is :)
One thing that happened in all of this is that I accidentally got a glob of the gel paint on another part of the table. I wiped it off but since it's not water soluable it smeared. I sanded down the stain and completely got rid of it, and then I added 2 layers of varnish to the area I sanded so it wouldn't have a different colour.
Lastly I did 3 more layers of varnish (so there are now 5 layers total, 3 on top of the triangles).
Cost: $60ish for Frog tape, gel wax, varnish, stain that I didn't use, stencil that I didn't use
Step 4: Add the Legs!
The last part was the legs. I chose these tube legs from hairpinlegs.com
Lumberjocks adviced me to NOT use regular screws for these legs since over time, if I drag the table back and forth, the weight of the table will cause the screws to move and the legs to become less secure. I was advised to use lag screws or structural screws and I chose structural screws since they seemed easier to use. I couldn't find what I needed at Home Depot so ended up buying them online.
Largely the legs went well - the structural screws were way easier to screw in for reason that are beyond my knowledge than the regular screws were for the horizontal bars. I didn't need to use a pilot hole even.
However, my very first screw that went in went in near a seam of the bowling alley lane at the end and I cracked it! This was pretty upsetting so I went to have a beer. For now, I'm not going to do anything about the crack except for some wood putty on the bottom (not in the image) and clear epoxy on the top to avoid crumbs getting in it. My rationale is that because I have the horizontal bars going across, the crack won't result in the wood cracking off completely. My other rationale is that this is pretty good for a first table. I might fix it all later though.
Lumberjocks tells me that the way I put on the table and bars I may be causing future warping with weather changes. This, and the screws, are the two things that I would research first before making this type of table again.
Cost: $30 for the screws.
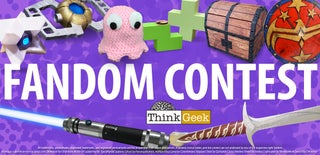
Participated in the
Fandom Contest
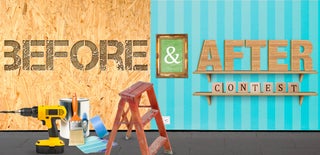
Participated in the
Before and After Contest