Introduction: Compact Skateboard
The growing strains placed on transport infrastructure as a result of increasing population and travel demands spurs a need for unique travel solutions. Basic designs like the skateboard, bicycle and scooter have taken off in population centres for short-range travel in response to this, but each sacrifice certain design aspects like compact-ability for speed with the bicycle.
A skateboard specifically is convenient when travelling, allowing for high speeds in dense areas whilst needing only small amounts of energy. When it is not in use though, it becomes heavy to carry (weighing on average around 4.5kg) and is quite long (between 50-150cm long).
The potential for a solution like the compact skateboard to further the ability for vehicle-less travel whilst not impeding day-today operations through easy storage could act to reduce congestion and the necessity for inefficient travel by car in suburban/city regions.
Supplies
Materials
- Trucks
- Veneers (roarrockit.com)
- Push fit ball bearing locks
- Recycled steel components (square tube, 25x25 right angle piece)
- Tube and rod
- 3D Printer suitable PLA
- M3 bolts
- Grip tape
- Paint
- Adhesive film
Tools
- Angle grinder
- Milling machine
- MIG welder
- Screwdriver
- Square and tube file
- Plasma cutter (optional)
- Skateboard compression mould
- Jigsaw
- Mitre saw
- Clamps
- Glue
- Drill bits
- Cold cut saw
- M3 Tap
Step 1: Research
All the design features of the board had to be thoroughly fleshed out in order to make this product, notably: the mechanical and service properties of wood & mild steel, and the shapes of skateboards.
The CAD drawings seen above reflect the outcome of this research.
Attachments
Step 2: Manufacture and Shaping of Deck
1. The first step is to make or find a template of the board shape you want to create. I made my own using Fusion 360.
2. Strip of pine were then cut out using the template (or the side view of the drawing). When all of these are combined they will form the top and bottom of a skateboard shape.
3. The plywood veneers were then layered with glue in between and compressed in the mould.
4. Once dry, the deck has another template (topview of drawing) stuck on and was cut to shape using a jigsaw.
5. The edges were then sanded and refined using an orbital sander. To ensure smooth continuous edges, continually raise the grit of the sandpaper until you reach 240 grit.
6. Next, the board was split into three pieces, with tabs in between each piece. This makes the three core components of the board and later allows for the compacting.
Step 3: Construction of T-Joint
The degree of difference in this board relies on this component, the T-Joint. As seen in earlier CAD drawings, the telescopic rods slide into a core module on the trucks. This module is called the truck attachment, and performs two roles: firstly the housing of the rods and secondly it allows for the attachment and detachment of any set of trucks. It does this through its rectangular housing, which allows for a truck to slot in, and then it locks them in through 4 push button locks. The manufacturing process can be seen below.
1. The metal materials had to be ordered from Edcon Steel, all dimensioned as seen in the CAD drawing of the final piece.
2. The baseplate was made from galvanised mild steel and was cut using the plasma cutter.
3. The baseplate then had to have the holes for the: pivot pieces; push lock bearings; and bolts all drilled using a drill press.
4. The tubes that were to be attached to the baseplate were then cut to size from a 6m piece (12.7 in diameter) using a cold cut saw.
5. The angled piece of the T-Joint was next to be manufactured. It was dimensioned carefully using a set of trucks as a reference piece.
6. The piece was then milled to shape from an ordinary right-angle piece (25x25x2.5).
7. Another channel was milled in the piece so as to allow room for the pivot pieces.
8. Next to be cut to shape were the rod. These had to be dimensioned firstly according to the CAD drawing.
9. The 9mm diameter rods were then cut using a cold cut saw.
10.The cross beams were then cut using a cold cut saw as well.
11. At each end of the rods, a 3mm hole was tapped to allow for an M3 bolt to be screwed in.
12.They also had two holes drilled in each the diameter of the crossbeams so that the crossbeams could slot in.
13. In order to construct the joint, the risers were printed and used as a joining piece in order to keep each component aligned.
14. The tubes were first welded onto the baseplate.
15. The push fit ball bearings were then inserted as they would not be able to be inserted after the next step.
16. Next the angled pieces were welded onto the baseplate. Here the trucks were used to ensure each piece was correctly aligned.
17. A thin strip of mild steel was then welded onto the back of each set of T-joint trucks (front and rear) to prevent the trucks from sliding out the back.
18. The rods were then constructed. Using the t-joints to keep them in line, the crossbeams were inserted and then welded to the rods.
19. The welds were then cleaned up using an angle grinder.
20. A 12x12 mild steel square tube was cut into 4 lengths of 20mm long.
21. A 3mm thread was tapped in the centre of the base of each of these pieces.
22. For the rear locks, two strips of mild steel were bent at right angles.
23. These were then welded onto the square tube.
24. For the front locks, two mild steel strips were bent into an arc.
25. These were then also welded onto individual pieces of the tube.
26. These were then attached to the trucks by way of the screw then, a bolt slotted through the bottom of the trucks.
Step 4: Cleaning and Painting
1. The wooden board was wiped clear and then a lacquer (Cabothane clear) was applied to protect against weathering.
2. This lacquer was then lightly sanded to remove any bumps and air bubbles.
3. All the metal components were then spray painted with black Rust-Oleum or coated in silicon spray, to protect the steel from corrosion.
4. The bottom of the board was then also spray painted black. Before this was done, all the edges were taped up to prevent the black from spreading.
Step 5: 3D Printing and Graphics Printing
1. Using the final model of the risers, clips and truck slips a series of 3D printings were done.
2. The clips were nailed onto the middle section of the deck so that it could clip onto the rods.
3. The truck slips were tested and worked effectively.
4. The risers replaced the old risers which were used for welding. The new ones were black (matching the colour scheme) and the old ones had been tarnished in the welding process.
5. A graphic was created using Adobe Photoshop. The first was a logo to be placed on top of the board.
6. This was printed onto an adhesive film using a large art printer and then stuck onto the board. Then it was covered up with spare film so as to prevent them being scratched etc.
7. Finally the grip tape was measured, cut and applied to the top of the board.
Step 6: Final Evaluation
The board turned out to be a massive success, allowing for the compact storage of skateboards whilst not impeding on the functionality of a skateboard. The video below shows this.
The truck slips are not shown here, but they allow for different trucks to be used by reducing the dimensions of the T-Joint.
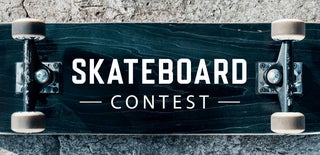
Second Prize in the
Skateboard Contest