Introduction: Concrete Bench Inspired by Roman Aqueducts
I needed a bench into my garden and so I decided to make a bench out of concrete which would look like a Roman aqueduct.
Step 1: Starting the Project
First you have to decide how big you want the bench to be. Then you can calculate how much material you need. The one that I made is 950 mm long, 455 mm high and 200 mm wide.
Then you have to find a material to make the model for casting. I used 50 mm thick EPS foam board (large pearl one) because I had it. After making the bench I would now suggest a combination of materials. The 2 inner larger pieces should be made out of the regular EPS foam ( easier to get it out afterwards ) and the smaller pieces that form the shape of the sides should be made out of Styrofoam, which is denser. It is harder to damage the denser board and you can cut it with a sharp carpet knife ( although this takes a lot of time ) and it will also hold its shape better when pouring the concrete.
You also have to figure out how much material you need for the mold. I used a melamine covered particle board from an old cupboard. Regular plywood or boards would also work.
I quickly assembled a temporary hot wire cutter to cut the pieces. The surface of the regular EPS foam board will not come out smooth otherwise. For cutting the pieces it makes sense to make a pattern out of something. I used plywood.
So, now cut out the pieces.
Step 2: Gluing It Together
When you have all the necessary pieces then glue them together with hot glue. It is easier to place the pieces if you use something to distance them from each other. I used 50 mm wide slats. Then glue together both assembled sides.
Step 3: Making the Mold Box
The mold is a simple rectangular box. It must be a tight and secure fit to make sure that concrete cannot find its way to cover the sides of the mold. Use long enough screws.
It is important to make it as rigid as possible to achieve straight lines. Also make sure that you have about 50 mm space to form the ends and the top of the bench.
If you have some silicone sealant then cover the inner edges of the 3 sides with silicone. It prevents the flowing out but this is not mandatory and there is no point to buy it only for this project.
Step 4: Adding Concrete Armature and Closing Everything Up
In this fun project it is not mandatory to use armature but I decided to add it. On the pictures you can see how to place it. It is important to make sure that the armature is staying in its place and not touching the surface of the board. It will end up being visible otherwise.
Then you can lift the assembled model into the mold box and close it. Use long enough screws and make sure that you close it tightly.
If you decided to use silicone sealant then put it onto the outside edges of the side that you closed. Allow it to dry.
Step 5: Pouring the Concrete
Use clamps to make sure that the upper edges will stay in place when adding concrete. I recommend using regular concrete and not a quick drying version just to have extra time to work.
Make the concrete a bit watery/fluid to allow it to fill all the smaller slots. Use a stick to make sure that there are no air pockets. Be gentle. Usually you can see in how to videos that a orbital sander is used to remove the air bubbles from the concrete but in this case the contact surface between the mold box an foam board is so large that it will absorb the vibration. That is why it is important to proceed slowly with the pour.
If you want you can add some color to the concrete using the special powders/liquids that are used for this purpose. Smooth up the upper surface and allow it try.
Step 6: Opening the Concrete Mold
Allow it to dry for 48 hours. If it is hot outside then cover the upper surface with something and water the surface from time to time to prevent it from drying too quickly. Otherwise cracks might appear.
Be gentle to avoid damage to the surface. There might be some areas that haven't fully dried yet.
If you have opened it then allow it to dry for another day. If possible then turn it onto its side, this allows the underside to dry, it most likely isn't fully hardened. Be careful not to damage it..
Step 7: "The Fun Part"
Now its time to remove the foam board. This is a messy job and if possible do it on a smooth surface, it makes the cleaning up a lot easier. I had to use the side plates of the mold to block wind.
Use a cheap knife that can be damaged. If you have removed the board then clean the inner surfaces with a wire brush and use some sand paper to smooth the edges and corners.
Step 8: It´s Done
And this diy concrete project is finished! The outcome is a decorative garden bench with a rather unique shape.
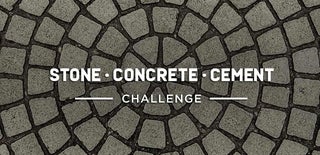
First Prize in the
Stone, Concrete, Cement Challenge