Introduction: Concrete Rocket Lava Lamp
Lava lamps are out of this world awesome. They're one of those timeless artifacts of design, culture, music, and retro style. They flood a room with color and are endlessly mesmerizing to watch.
I've recently taken up the hobby of not only revitalizing older vintage traditional-shaped lava lamps, but also making my own designs for lava lamps....from scratch.
My design uses cast parts (in my case from concrete!) rather than metal to make it much more accessible to fabricate for a peasant like me.
Special thanks to Reddit user Antnee83 for his comprehensive guide to making your own DIY lava lamp wax/fluid a few years ago. I found the guide exceptionally helpful in mixing my lamps and highly recommend thoroughly reading through it if you plan to build one of these. I've made several-and can attest that the recipe is pretty solid.
Be advised, it's a long journey to make one of these and there's a lot of steps and recommend reading them carefully! Keep reading and I'll walk you though the process of how I make my concrete rocket lava lamps.
Supplies
For the lamp:
The Base:
- Concrete (optionally you can use plaster or possibly resin if you later use silicone molds)
- (Optional) aggregate for concrete (shells, mica/metal powder, glass, pebbles, colored chips, etc.)
- Access to 3D printing
- Vaseline/petroleum jelly
The Stand:
- Access to a laser cutter or small scroll saw
- 3/4" thick wood (I used 6 layers of 1/8" plywood with my laser)
- Wood glue
- 3/4" Wood screws
- Stain of choice
- Finish of choice (I used floor paste wax)
- 1/8" Brass brazing rod
- Male thread cutter die and handle for #6 threads & thread cutting fluid
- #6-32 Nuts (I went with brass to match the rods I would be threading)
- 1/8" Masonry drill bit
Electrical:
- Lamp cord with molded plug
- (Optional) You could also opt for something more colorful...
- E26 bulb socket
- Rotary cord switch
- (Optional) There's also a more vintage option for switches and plugs too...
- 40W E26 incandescent appliance bulb (for less power, try looking for a 25W)
Misc:
- Foam/felt/cork pads for the stand legs and inside of the concrete base to prevent damaging surfaces and to protect the glass bottle from any damage from contacting the concrete directly
For the Globe & Lava:
The Wax:
- Paraffin Canning Wax (I used Gulf brand from my local grocery store)
- Liquid Paraffin Lamp Oil
- Brakleen Non-flammable Brake Cleaner (found in your auto parts store) Note: This is the main unsafe ingredient in the recipe. Take special care to spray into a container outdoors or in a well-ventilated area using a lid with a hole and the included straw in the spray head.
- Solid Candle Wax Dye- I've had ok luck with this brand. Seems to look mottled at lower temperatures however. Milage may vary.
- (Optional) Oil based paint
The Fluid:
- Distilled Water
- Propylene Glycol (PG)
- (Optional) Vegetable Glycerin
- Sodium Lauryl Sulfate (SLS)
- (Optional) I've ordered some high concentration SLS from a DIY lava store that I hope to test soon. It should work extremely well. They have a lot of other interesting products as well if you wish to mix a lot of lamps!
- Liquid Food Coloring (Don't get the gel kind. McCormick Brand works well.) / calligraphy ink for if you want a good Mathmos Purple or Pink
The Globe:
- A Glass Bottle (Look for one with a resealable lid-I avoid corks and stoppers due to changing pressure as the wax heats and expands) The taller and skinnier the bottle, the better the wax will flow. Also best to avoid any bottles with an upward bulge (punt) on the bottom.
- Stainless Steel (316) music/spring wire-I used .002"
- (Optional) any small high quality stainless steel extension spring should work ok too (but may still corrode over time)
Misc:
- Funnels
- Some sort of cheap tube that the funnel tip can fit into and can fit into the mouth of the globe (I found one made of plastic)
- Vessel/bottle/globe (screw top ideal since you'll need to re-seal it)
- Paper towels
- Liquid dish soap
- Various tweezers
- Turkey Baster
- Plastic Pipettes
- Large metal pan
- Glass canning jars with lids
- Digital scale (mine is accurate to .001g)
- Large glass measuring cup(s)
- Empty plastic jug(s) with lids
- Insulated work gloves
Don't feel like mixing your own lava?
You could always just purchase a replacement bottle by itself, drain the fluid, melt the wax, and transfer the coil, wax, and fluid into the rocket lamp.
Step 1: The Lamp Design
For my homemade lava lamp design, I've long been a lover of mid-century modern styles and there's lots of great space-age designs for lava lamps from Mathmos, Lava Lite, and Schylling. The Telstar is an excellent iconic reference for design form. The rocket 'fins' make for an elegant yet very strong tripod to support the weight of the lamp.
My design is actually more closely inspired by some USSR Soviet designed lava/glitter lamps that feature a top and bottom that are connected via metal support rods to hold everything in place.
Concrete seemed like the ideal inexpensive choice for material. It can be cast to whatever form I want to mold using 3D printed parts. It's a fantastic insulator. It's very strong and can be drilled, sanded, stained, sealed, painted, and even filled with stuff like shells and crushed glass as an aggregate. So I could design the base for any shape globe I want either from an old lamp or in my case - a glass bottle. Being able to cast the base out of something gave me far greater control in the design process and allowed me a lot of freedom to play with the different shapes.
I don't consider the forms to be perfect, but they're for sure functionial and hold up quite well.
My mold parts did need to be split before printing since they wouldn't fit the build volume of my machine. I also wanted gravity to be my friend, so I took care to design the molds to pour in a way that wouldn't leave air cavities and would fill entirely from top to bottom.
Step 2: Printing the Molds
The printing took a few days and nights. I printed my mold sections with PLA and was able to avoid needing support material. I've uploaded all my files for the molds (and positives as well if you want to cast molds from silicone) to Thingiverse.
Note: Keep in mind the orientation your parts are printed, since taller/skinnier parts with smaller layer areas can be much weaker than printing them sideways.
There were a few openings in my molds where the layer didn't quite bridge across the infill all the way, but I wasn't worried about this at all since it would get filled with lubricant for the mold release. I did give everything a very light sand with 200 grit paper to take down any burrs or strings that were left on the inside of the molds as well as attempt to hide the faceted geometry to look more smooth and uniform with the cast surface. I'll be able to sand the concrete later so it's ok if it's not entirely perfect at this point.
Step 3: Casting the Concrete Parts
This part is time consuming with 3D printed rigid molds since you need more printed parts in order to remove the inner portions from the concrete molds (since they're not flexible) and the lubrication becomes critical. I used petroleum jelly liberally on the insides of the printed molds to help release the form once set. It's a bit messy. You could probably wear latex gloves if you want.
Since my concrete contained pebble aggregate out of the bag, I was worried those pebbles in the bought mix wouldn't fit in my molds. Using a dedicated metal kitchen mesh strainer, I was able to strain the pebbles out of the concrete mix, leaving just the fine concrete powder for a nice smooth finish. I've had good luck with crack resistant cement as well since it contains lots of little fibers that help hold itself together once cured and increases the survivability of the part during demolding. :)
I mix all my concrete by eye more or less. I go for a consistency of pancake batter and typically have to mix a small amount multiple times to fill each of the two molds. I also like to use a hand jigsaw with the blade removed to vibrate the mold to help any bubbles find their way to the surface. I typically pour a little over the top and scree off the excess later once it's a little more solid.
Step 4: Demolding
Once enough time has passed and your concrete is fully cured, it's time to demold. The cure time will vary depending on the mix you're using, the humidity, the temperature, and other factors - check the bag for instructions.
I typically have way better luck if I wait around 48 hours before attempting to open up the molds.
A chisel, flat head screwdriver, metal putty scraper, and a small tack hammer may greatly help with removing the mold parts. My design contains a center 'key' that once removed from the inside parts, makes the rest of the interior mold parts much easier to pull out. The outsides are pretty easy to demold if you take your time.
Once the plastic molds are removed, they can be cleaned and reused for the next casting. :)
I typically set my concrete parts out in the sun for a day to help dry them out fully. I find the Vaseline can be a little stubborn to remove or fully wipe away, but sunlight is effective for drying it off.
Once dried, you can sand the concrete parts to your liking, give them some paint, or use them in the raw and unfinished concrete look.
Step 5: Support Rods
My lamp design uses a few metal support rods that go through the concrete parts to help hold the lamp together.
- I first drill the holes through the concrete with the masonry bit- I like to take a lasercut part that has the holes evenly spaced and make a mark with a pencil or marker onto the concrete where I want to drill. A paper template can work for this too.
- I keep a container of water next to me for cooling the bit and clearing the flutes during the drilling. Always keep the bit cool and the flutes clear to ensure the masonry bit survives beyond this project.
- I like to start each hole with the template in place and then remove it. Then I drill each hole one at a time, spinning the bit in the water container every few seconds and going easy on pressure when drilling throughout the cement.
Once all the holes are drilled, it's time to make the metal supports.
- I like to set the globe into the concrete base and set the concrete top above the globe to get an idea what length of rod I'll need for this. Since I use bottles, their height can sometimes vary slightly.
- Making a mark on the rod, I cut it to length using a hacksaw with a metal cutting blade. I typically like to cut all three at once to the same length.
- If you have a file or sand paper, it's helpful to deburr the end of the rods and add a slight chamfer to help with cutting the threads. I used my bench belt sander.
- For my rods, I use a heavy bench vice and two small pieces of plywood to act as 'soft jaws' to hold the rod steady without marring the surface while cutting the threads.
- I use a #6 die to slowly cut threads into the rod using a drop of cutting fluid. I like to cut about an inch of thread onto each end.
- Once the threads are cut, it's good to clean the threads with a brush and test with threading a nut to see if they're threaded properly.
Step 6: Adding the Socket, Plug, & Switch
This part is very simple.
- Trim the wire ends if they're tinned, strip the insulation with a knife or stripper, and twist the copper conductors.
- Take apart the socket. There may be a few parts to feed onto the cord before connecting to the socket screws, so it's best to pay attention to those first if necessary.
- It's a good idea to use an underwriter's knot for tension relief.
- Not sure which wire goes to which screw? The smooth (bare) wire should go to the brass contact. The bare wire is wrapped around the brass screw on the base and tightened-doing the same for the other wire and contact.
- Reassemble the socket and do a test with a bulb. It should light up when plugged in. Unplug it before installing the switch.
- I find the rotary on/off switches easy to install. Simply cut one of the wires (normally the smooth/bare), lay them into the plastic casing, and tighten the other half onto it using the screw. There should be pointed contacts that pierce the insulation on the cable and make contact.
- Test the bulb/cord with the switch. if it's too tight to turn the switch, back off the screw tension a little.
- Install the socket in the concrete base and add the plastic collar to the socket from the other side to secure it in place.
Step 7: Making the Wooden Stand
It helps tremendously if you have a laser cutter to make these stands. Otherwise, a scroll saw and paper template should provide excellent control needed to make the wood parts. You could also cross cut the lap joints on a table saw using a dado cutter blade and a cross-cut sled & jig. In the future, I plan to do that specifically.
I simply cut out 1/8" wood parts in six pieces per part of the base, glued them together (it's important to take your time and make sure everything is straight, fits nicely, and isn't skewed any), hit the edges with a roundover bit in my router, and used my sander to take off the burnt and rough edges. To finish, I just stained all the parts and used some paste wax. I didn't worry too much about the inside of the ring piece since it won't be visible. For the stain first and the paste wax afterwards, I always make sure to wipe away excess with some paper towels.
For assembly, I used a few 3/4" flat head wood screws and a countersink bit to fasten the legs to the ring from the inside due to the weight of the lamp. I would recommend at least using a mechanical fastener for these. If you use just glue, the joints can likely fail and cause your lamp (made of concrete, glass, and full of fluid and molten wax) to come crashing down. So yeah...screw that.
With the stand completed, you should have a finished rocket lava lamp! ....Except we now need the lava part.
Step 8: So What's in a Lava Lamp?
60's magic. Next question.
Actually, the original Mathmos (original lava lamp creators) formula for their wax and fluid is a well-guarded trade secret. So it's not public information. But the mechanics are simple to understand and recreate using stuff we know and basic science.
The nerd explanation:
Lava lamps use heat from an incandescent bulb to make a mass of dense wax melt and expand in a fluid-filled globe, thus making it more buoyant and float upwards. The wax rises in the fluid and cools, allowing it to contract to become less buoyant and sink. It then flows back to the bottom of the globe where it can contact a stainless steel coil that helps break the surface tension and allow it to recombine with the rest of the wax and the cycle repeats again and again.
To make your own, you simply need the right density wax, the right density fluid, a glass vessel (or globe) to hold the contents, and a base that will hold everything (including the bulb and socket) together.
Step 9: Preparing the Globe
In my case, the 'globe' is a glass wine making bottle with a screw on top and flat bottom - 750mL in size.
Regardless of what you use, you'll want to really clean the inside out first. Use some hot water and dish soap. I like to squirt in some soap, add some screaming hot water, and shake it while holding my thumb over the opening. Rinse. Repeat a few times. You want to make sure to rinse all the foamy soap bubbles out, so I like to fill the whole thing up with water and drain it a few times. Once nice and clean, set it aside.
Note: The cleaner the bottle, the less chance the lava will stick later.
Step 10: Making the Wax
The Lava:
Lava lamps use paraffin wax for the 'lava'. My local grocery store has it in the canning aisle. The problem with using straight paraffin wax is that paraffin wax naturally floats in water. Not what we want - we need our wax to sink.
To do that, we need a way to make the wax more dense- or have a higher specific gravity than water in order to sink in straight distilled water once melted.
In our case, we'll be using tetrachloroethylenealso called perchloroethylene or 'PERC'. It's commonly used in spray on non-flammable brake cleaner as well as in dry cleaning. It's very dense and I've had a lot of success with Brakleen from the auto parts store.
Safety:
Perc is used to clean automotive brakes, to dry clean clothes, and is more dense than water. You'll want to keep the liquid and it's fumes out of your eyes, mouth, and respiratory. Wash your hands after using and don't use kitchenware you also use to prepare food for this. Use a junk dedicated or thrift store glassware for this to avoid contamination and health problems. If possible, some adult supervision is recommended.
Collecting the PERC:
I recommend getting a hammer and nail and making a hole in a metal lid of a glass canning jar (and keeping a second lid with it). This will allow you to use the spray straw on the can to spray the brake cleaner into the jar (do this outside or in a well-ventilated area) without it spraying all over the place. Once you've filled up the jar with a substantial amount, swap the lid with the hole with the solid lid so it doesn't leak out everywhere.
The Binder:
We'll also need a binder to help prevent the paraffin and PERC from settling above the lava in the lamp, so for this we'll be using liquid paraffin oil (LP). This will greatly help the mix hemogenize with the paraffin and also increase your yield. I find that 225g of paraffin requires enough PERC/LP to make a couple lamp globes. :)
Based on ratios in the Reddit guide, I ended up using-
- 225g Paraffin Wax
- 187.5g PERC
- 37.5g Liquid Paraffin
I use a digital scale to measure out the different wax ingredients by weight. I typically put the wax in a canning jar and set it in a pan with a few inches of water on the stove that's simmering hot.
I don't mix in the LP/PERC until I'm ready to pour the wax into the bottles since I don't want the PERC to evaporate and lower the density too much from just sitting on the stove while I'm still doing other steps.
Optional:
I've found that a grain of rice sized blob of oil paint (color depending on how you plan to color the lava-but typically white) can really help add more opacity to the lava once it's flowing. It's good to mix this into the lava wax before adding it into the globe. If you plan on using solid wax dye chunks, I would add them to the wax while it's on the stove and fully melted in order to adequately hemogenize the dye. If you're using liquid dye, we'll add the color later when the lamp is running. :)
Step 11: Making the Fluid
The reddit recipe I've been referencing is fairly simple and works pretty well with good clarity and flow.
We need our fluid to do three things:
- To fill the volume of the globe
- To be close enough in density to the lava wax mixture so the wax will float when heated/sink when cooled
- To have a lower surface tension to help the wax 'pinch off' into blobs.
The mixture is straightforward:
By volume: I use 7 parts pure distilled water as the fluid base. To increase the density, I add 3 parts propylene glycol. Bascially a 70% / 30% mix. Lastly, we'll need a surfactant to help the blobs flow and also prevent any wax from sticking to the inside of our globe. For the surfactant, I use a sodium lauryl sulfate (SLS).
How much surfactant do you need? For my experience, a few mL for a 750mL globe should be enough to keep the lava from sticking. If you need a second opinion...
From Reddit:
- 20 oz globe - 2-5ml
- 32 oz globe - 6-10ml
- 52 oz globe - 11-17ml
- 250 oz globe - 45-60ml
Note: When adding SLS, make sure it's not settled out of solution or if may affect performance!
I like to measure my fluids in an empty plastic jug and add a few mL of SLS to it to help the rest mix into it. This jug with the 7:3 fluid will be our starting place with our lamps.
Step 12: The Metal Coil
If you've ever looked into a lava lamp towards the bottom, you might have noticed a coil-like object at the bottom of the globe-possibly partially encased in wax if the lamp is cooled.
One could easily mistake it for the source of the heat in the lamp..... but no. It's not the heater. :)
The coil actually serves two functions: to help more evenly distribute the heat from the bulb into the wax and to help with breaking the surface tension of any melted wax blobs that touch it to help them recombine.
If you can find a coil from an old lamp....fantastic. If you can find a stainless steel extension spring, you can stretch the middle and mesh the ends to make a coil.
Or you can just do what I did and use some high-quality 316 stainless steel or music wire to make a coil. I chose spring steel/music wire since I didn't want to deform my finished coil after compressing it to fit into my bottle.
Using a 1/4" piece of allthread and some scrap wood, I made a little turning jig for making coils by drilling a hole through the allthread with my drill press and some cutting oil, adding some nuts and a handle, and a frame to hold everything. I also cut a small block with a countersunk hole in it to help guide the wire tight to the threads.
Once I've turned some wire, I can trim the ends, and form the coil. To do this, I use a flat screwdriver or metal chisel to separate 5-6 turns from each end from the middle of the spring. I then stretch the middle out while leaving the ends still tightly coiled. The last step is to loop the ends and mesh them together. I typically go by eye and find that you want around an 1/8" - 3/16" gap inside the glass from your coil.
The better the coil sits in the bottom of your globe, the better it will contact the lava wax and the quicker it will be able to help transfer heat from the bulb to heat it up.
Note: The quality of steel you use for coils matters. Mild steel may corrode and oxidize over time in the lamp which will taint the color of the lava and possibly allow residue to form on the bottom of the globe. Zinc coated steel will likely corrode.
That's why I use 316 stainless steel for mine for corrosion resistance.
Step 13: Adding the Wax and Fluid
This step involves a little choreography and HOT water. Definitely read through all the steps of the dance and memorize them since timing matters with this.
- Your wax mixture should be in a glass container. If not already melted in a boiler, go ahead and immerse it and turn on the heat until boiling. Once boiling, set the heat to low.
- Your bottle should be adequately cleaned and rinsed from earlier. Pop your metal coil inside (I often need to use a wire to push it to the bottom).
- You should have your 70/30 fluid mixed in a jug. Go ahead and use a funnel to add 1/4" of fluid to the bottom to cover the metal coil. Look for any bubbles/frothing when you swirl the bottle. Feel free to add another mL or two of SLS to the bottle until some bubbles form when agitating the fluid. This extra SLS will help coat the inside of our bottle and provide a 'non-stick coating'.
The longer you wait, the more the surfactant will drain to the bottom of the globe and the more likely you may encounter stickage with the wax on the glass later.
- When the wax is fully melted to a liquid, cap the bottle and rotate it around from side to side, end to end, top to bottom to make sure the fluid has adequately coated the inside.
- Be sure to stir the melted wax mixture to make sure it's homogenized nicely.
- Take the funnel with the tube on the end and carefully add the molten wax into the funnel without burning yourself. Keep the tube 1/4"-1/2" above the surface of the wax to prevent it from touching the glass without touching the fluid first.
- Add between 1/4 to 1/3 of the volume of the bottle with wax. If any molten wax touched the inside of the glass, don't immediately fret. You can pour some of the hot water from the pan on the outside of the glass to heat up the area where the wax stuck to the inside and it should melt and sweat to the bottom again.
Once you reach this point, it's important to let the wax cool and solidify fully before adding the fluid.
I recommend filling the bottle until 3/4 full to allow for some room for adding more fluid later when balancing the lamp.
Once you've done this, you can put it on the stand and turn on the lamp.
Note: If any of the wax appears to stick inside the globe, unfortunately there's not an easy fix I can recommend at this time outside of trying the process over again with a different bottle and more surfactant / more coverage before adding the wax. A solvent (Acetone as a last resort for example - use care when handling) that can dissolve paraffin may be necessary to clean the residue spot left behind from the area where the wax stuck to the glass.
Step 14: Balancing the Lamp
Note: This is the most time consuming part of the process and results can vary wildly due to variables in the coil size/spacing/diameter, size of the globe, wattage of the bulb, amount of PERC/LP in the wax, amount and quality of surfactant in the fluid, and even the temperature of the room, airflow around the lamp, and even color of the wax and fluid. This is a big, fat, long step and personally gives me the most headaches!
More often than not, if you were to throw the bottle of fluid and wax you just mixed right on our concrete stand and turn it on, you will likely find that the lava doesn't flow well if at all yet once melted fully. It may sort of melt and stay at the top, never sinking back down. It may just melt and....sit there. It may form one ball of lava that is content to hover in place, not really moving up or down. I may flow a little but not very often. This is usually because the lamp density for the fluid and wax need some adjustment to get the wax to flow instead of staying at the top or bottom.
Here's the basics of balancing and troubleshooting:
- If the wax stays at the bottom of the lamp after it's fully melted, either the wax is too dense or the fluid isn't dense enough. Add more propylene glycol to the fluid to increase the fluid density.
- I typically add 20mL - 40mL at a time of PG
- Alternatively, Vegetable Glycerin is much more dense and can be added a few mL at a time if you have super heavy wax (or you're restoring an old lamp with super dense wax - which many of them have compared to this recipe)
- If the wax floats to the top and never sinks after it's fully melted, either the fluid is too dense or the wax isn't dense enough. Add distilled water to the fluid to dilute it and decrease the fluid density.
- You can also pipette a few drops at a time of the PERC/LP solution into the flowing wax at the top to get some to sink. You don't want to add too much or else you'll need too much PG to get it to flow. Adding too much PG can make the fluid 'cloudy' when heated. A little goes a long way and defintely give plenty of time after attempting this to allow it to mix.
- I add a few drops until a large blob of wax sinks to the bottom and then allow it time to reheat. If the wax moves back up and stays there again, I repeat the process.
A few things to look for that tell you you're on the right track:
- Any 'spiking' or 'pillar' behavior for the wax during warmup is a good sign. It indicates that the wax becomes buoyant when heated and after breaking through or around the cool/solid 'cap' at the bottom, it will hit cooler fluid and cool quickly-growing organic pillars, spikes, clouds, and solid blobs. Note - Some bottles may not spike as easily due to their shape.
- If the lamp spikes, look for a little water above the very top of the solid wax. This indicates that the cooler wax can sink again. Ideally, the spikes and columns will collapse and melt again at the bottom.
- If you have a nice 'bell curve' of lava at the top and a nice proud bubble of lava at the bottom, you're definitely close. The taller the bubble on the bottom, the more it wants to float.
A few things to beware:
- Needing to add too much PG to the fluid can make the fluid become cloudy when heated. Vegetable glycerin can be a useful substitute here since you can use way less to get the same density in the fluid.
- Even two lamps from the same batch of wax may balance a little differently. The melted wax can settle somewhat if allowed to sit in the jar on the stove before adding to the globes with the heavier more dense wax on the bottom and the lighter wax towards the top.
- It takes time for additives to homogenize inside the fluid and wax, so it's best to run the lamp for a cycle or two to get a better idea of what's going on.
- Always make adjustments to a cold lamp. Adding ingredients to the lamp when it's running won't allow you to stir the fluid to properly mix everything. Trying to mix the fluid or pour it out before the wax cools can cause the wax to break up, emulsify, and cloud the lamp. Possibly permanently. Don't do that.
- It can take several 'rounds' to get the right balance. I've had some lamps balance in as little as a single adjustment. I've had some require four or five adjustments to really get flowing nicely. I've even had a few where I tried a different ratio, made the wax too dense, etc. and either couldn't get the lamp to flow well if at all.
- It definitely takes some practice and patience. At the time of writing this, I've botched just as many lamp bottles as I have made them successfully - mostly because I'm still learning, I'm not a scientist, I'm still experimenting with improving things, and this step is very hard.
Step 15: Color
If you survived balancing your lamp, congratulations. You made it to the most fun part!
Coloring the lamp is probably the most rewarding step of the process and is definitely my favorite!
Solid Wax Dye Chunks:
- These work best when the wax is still melted in a jar on your stove top. The brand I use tends to still show little specks in the lava when flowing. The hotter the lamp is on warmup, the better they melt and mix with the wax.
- I use a pair of fine tweezers to just drop a few specks in and let them mix.
Liquid Wax Dye:
- This stuff can be added to the lamp after it's flowing and the wax is melted.
- The nozzle on a new bottle needs to be cut before adding one drop at a time. It's very potent.
Liquid Food Dye / Calligraphy Ink:
- I always test what these do to the fluid in a separate glass bottle/globe before coloring the fluid I worked so hard to balance. That way I can experiement to get the perfect color every time.
- When adding the dye to the fluid, it's best to do this when the lamp is cold so you don't get little bits of color trapped in the wax that will eventually release into the fluid during operation further altering the color.
- Purples and pinks tend to look 'muddy' if using food coloring, which is why I like using the ink for those.
- If you need something light, you can dilute the dye in a bit of distilled water (like a teaspoon up to maybe a cup).
As for what colors to use? That's really up to you. :)
Colored wax with clear fluid is easy since you only need to dye the wax. For more colored light, coloring the fluid a nice, deep, rich color and using white dye on the wax always looks amazing. For two colors, I usually reference classic Mathmos/Lava Lite combinations, but making your own color combo is absolutely part of the fun.
Step 16: Go With the Flow
If you've followed along thus far, congratulations! You should have a flowing paraffin lava lamp made of cast concrete.
A few pointers to keeping it happy:
- Don't run this (or really any) lava lamp for more than 8 hours consecutively without cooling. Ever. It can burn the wax and leave residue on the bottom of the globe. It can also affect the wax negatively and cause it to separate in a way.
- A dimmer will greatly help prolong the amount of time the lamp can operate before overheating depending on how well it's balanced. When the lamp overheats, it will look most of the wax is stuck at the top in the form of small blobs that don't want to recombine.
- A smart speaker and smart outlet or dimmer are great ways of making sure you never leave it running too long or too hot. Even a mechanical timer could work for this.
- Keep in mind, airflow and ambient temperature can affect warmup time and performance.
- It's a good idea to never run the lamp when you're not home and it's left unsupervised.
Step 17: Final Thoughts
So I think I love this hobby so much because it is such a beautiful intersection of so many of my own interests and skillsets: 3D design, 3D printing, mold making, concrete, laser cutting, woodworking and finishing, electrical wiring, mid-century modern design, color and fluid motion, and lava lamps in general.
- Ever since making this design, I've come up with several different designs and have lots of fun ideas for different colors of lava and fluid, different materials for the cast lamp base, experimenting with metallic wax, making glitter lamps, and even may look into a ceramic heater and diffused laser diode for a rich color illumination.
- I've built a camera rig for observing and operating the lamps remotely using my phone (maybe good for a future instructable) since balancing lamps takes a lot of time and I work in an office 40 hours every week.
- I've thought about creating a small local side business where I could sell these at craft fairs, but I would need insurance and likely need to form an LLC to further insulate my assets should a problem arise since it's both an electrical product that's DIY and the lava lamp isn't exactly non-toxic due to the PERC. For now, I sell them and give them as gifts to family, friends, and the occasional coworker who I trust will take good care of them. :) So if you want to make these for income, just make sure to do your homework first.
- I'll also note that there are some design improvements to the form I may make sometime soon regarding the support rod nuts resting against a slope instead of a flat form. I'll update the files once I do so.
- If you find it's always having trouble getting to an operating temperature, you could try putting a bit of aluminum foil inside the bulb cavity to help direct heat upwards.
- If you ever need to start over or remove the wax/fluid from the bottle, make sure to clean it adequately before trying again. Currently untested, but I've read that acetone can help dissolve any residue from the paraffin that may be stuck to the inside of the glass which will prevent a new surfactant coating from keeping wax from sticking in that spot.
But anyway, I hope you've enjoyed my lengthy documentation and I encourage you to read Antnee83's Reddit guide in full as well as check out the r/lavalamps community and the Oozinggoo forum if you wish to dive deeper into this odd and very fun little hobby!
Also please consider voting for my instructable in the 2022 Stone, Cement & Concrete contest!
This instructable and hobby was inspired from when I bought some USSR lava lamp parts from Ukraine and wanted to learn how to make them into a flowing lamp once again without buying and sacrificing a new lamp.
So, special thanks to Yuri (Юлис) for the spark to discover this colorful and fun new hobby during such dark times and for hopeful peace and brighter days in Ukraine. Slava Ukraini.
Отож, особлива подяка Юрію (Юлісу) за іскру, щоб відкрити для себе це барвисте та веселе нове хобі в такі темні часи та за надію на мир і світліші дні в Україні. Слава Україні.
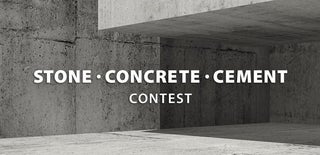
Grand Prize in the
Stone Concrete Cement Contest