Introduction: Concrete Vader Mask Book End (no Spoilers)
I came across a Darth Vader mask while shopping for a pumpkin shaped bucket around Halloween to make our Concrete Jack o' Lantern. If you work with concrete, you know that everything starts to look like a mold, and I bought the mask on impulse, despite the undercuts and complexity.
What to do with half of Vader mask? Dystopian garden ornament from a galaxy far, far away, half buried in the ground was my first thought. It could have become a piggy bank or a door stop but instead it became a book end.
This piece could have been cast solid, but the problem is that there's two gaping holes in the mask where the eyes belong and it's open where the neck is. Capping off the holes is possible, but it was easier to just put tape over them and press ShapeCrete into the mask, creating a shell instead of a heavy solid piece.
Materials and Supplies:
- 7 lbs. ShapeCrete
- Darth Vader Halloween Mask (found this one at Walgreens)
- Mixing Supplies (Rubber Gloves, Dust Mask, Mixing Container)
- Duct Tape or similar
- Pliers, Snips, etc. to break plastic
- Optional Color Enhancing Sealer (Surecrete PC-12)
- 1/4" MDF A1 Walnut Plywood
- Wood Saw
- Strong Glue / Epoxy (E6000)/ Silicone
- Clamps
- Cork Pad
- 10 lbs. Play Sand
Step 1: Prepare the Mask
Before buying this mask I looked inside to see if it would even be possible to use. The inside of the mask isn't as smooth or nicely finished as the outside, but it wasn't too bad. Aside from a few holes to patch up and the manufacturer's text to scrape off with a razor blade, it was just a matter of removing the foam around the eyes and the straps.
I used blue tape to cover the openings for the eyes, mouth, and strap holes. Duct tape will work better for the eyes. While the piece was being packed, the tape moved and I didn't notice so one of the eyes had a huge bulge that had to be ground away.
Step 2: Mix and Pack ShapeCrete
Black concrete pigment is added to ShapeCrete to get this color. You can skip that step and just paint the piece after it's cured.
- Mix ShapeCrete to a Clay-Like Consistency (approximately 4 parts mix : 1 part water).
- Pack the mix into the form, making sure to fill in the tight spots.
- Be careful not to push the mix through the taped up areas.
- Smooth the top edge flat.
- Cover the piece with plastic and let it cure for 2-3 days.
Step 3: Break Away Plastic Mask
Because of the undercuts and complexity of the mask, we have to break the form away. For this reason it's also important that you wait a bit longer for the piece to cure so you don't chip or break any of the more detailed areas.
- Very carefully break away the plastic using a combination of snips, a utility knife, and pliers.
Step 4: Hopefully You Won't Need to Grind....
As I mentioned earlier, the tape over one of the eyes broke away and without realizing, I just kept packing mix down into it, so the left eyeball had a huge bulge.
The rest of the grinding needed to happen at the neck. If I'd known this was going to be a book end before I made it, I would have trimmed the plastic so it sits flush and creates a 90 degree angle against the books.
Rough grinding like this can be done with an angle grinder and the right grinding wheel. Here I've used a variable speed concrete polisher with very coarse polishing pads.
Step 5: Color... Enhance!
There are a lot of concrete sealers out there, and all of them will work with ShapeCrete, but I decided to seal this piece with Surecrete PC-12 which is a color-enhancing high-gloss epoxy sealer (basically a coating of plastic). One coat turned the piece from dark grey to black and made it awfully shiny. It can be dulled back down with #0000 steel wool, which I might do later.
Follow the directions on the sealer, adding 3 parts A to 1 part B and mixing for 30 seconds. I simply brushed the sealer on and let the piece soak it up and left it to cure overnight.
It's going to be more cost effective for you to buy a can of glossy black spray paint, but I already had this sealer on the shelf.
Step 6: Cut Wood Panel
To cap the back I used a piece of 1/4" Walnut with a MDF core. It's easy to cut with a hand saw, but you might use a bandsaw, scroll saw, or jigsaw if you have one.
A few coats of wood finish are applied before gluing the panel in place.
Step 7: Glue Panel to Back
The back panel can be glued in place with JB weld, epoxy, or a strong glue like E6000.
The back of my piece wasn't exactly flat so the panel had to be clamped in a few places. E6000 takes 24-72 hours to reach full cure, and I was impatient and removed the clamps in 4 hours, which left me with a big gap...
Step 8: Fill Gaps With Silicone
So I filled the gap with silicone caulk.
In hindsight, I could have used black.
Step 9: Fill With Sand and Glue on Cork Base
The weight of the piece was only 6.5 lbs, and because it narrows down at the neck, it was a bit top heavy.
Part of the reason for having the back panel in place is so the piece can be filled with sand. I added 10 lbs. of sand, and the piece is plenty stable to be used as a book end.
- Fill with sand
- Caulk around the neck and back panel
- Place cork base piece
- Flip over and let silicone cure
Disclaimer: I'm very careful to move the piece with the cork pad fully supported from below. I don't know if the silicone seal will hold 10 lbs. of sand, but I doubt it. It's probably best to use a strong epoxy - or to just make the piece with that part being concrete, by adding a panel in the mold-prep step at the beginning.
Step 10: The Circle Is Now Complete.
It would be reallly fun to make a gold C3PO or white Storm Trooper book end for the other side, but for now the Letter B from that other Instructable works just fine.
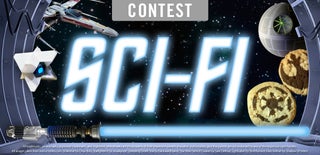
Participated in the
Sci-Fi Contest