Introduction: Concrete and Wood Slab Table
First of all, this is my first instructable, so take it easy on this old hillbilly.
This instructable will outline how I made two similar concrete and cedar plank tables. This build probably isn't for the person wanting to try their very first project, but you certainly don't have to be Norm Abram to complete this. This is a fun project that incorporates different materials (wood, concrete, metal), and relatively speaking it can be a pretty quick build. I learned a few things along the way, made a few errors, but overall I'm pretty happy with the end product and hopefully I can help you learn from my mistakes. Let's get started.
Materials needed will vary based on how closely you would like to follow this instructable, but here is what I used:
Log (I used cedar, but any dry wood will work)
Varnish
Concrete mix (type can vary, I'll explain later)
steel rebar
stainless steel bolts
concrete dye and acrylic fortifier
un-sanded grout
wood or steel for legs
Step 1: Roughing Out the Wood Plank
The first step is to get your piece of wood that will go inside the tabletop. Obviously you don't have to include this piece of wood and the rest of the instructions can be used to make just a concrete table, and there are also plenty of other great instructables about concrete tables and countertops.
I used a cedar log that has been laying down in the trees in my back yard for years. You can really use any type of wood as long as it is dry, you could even used milled lumber with squared edges if you want, I just prefer the natural curves and edges of a slab.
I started by just using a chainsaw to cut the log into a couple rough slabs. If you have access to a sawmill or decide to buy a piece of lumber obviously you can skip this step. I got two good sized slabs using my chainsaw that are rough cut to about 3" thick. I want the end thickness to be 2" so I got the surfaces flat and parallel on the planer. I ran the logs through on a plank of sturdy wood so that it wasn't rocking on the planer bed due to my less than perfect freehand chainsaw cut. The nice thing about using cedar is that it smelled amazing when I was planing. I would suggest doing this outside on a nice sunny day because your dog will like to lay in the woodchips and it is friggen adorable, look at that cute little rascal.
Step 2: Finishing the Wood Plank
This step could use some experimenting, and maybe your own experience would lead you down a different path. But I found that it was easier to finish the wood plank prior to pouring the concrete around it so that you aren't screwing up the wood surface as much when you are polishing the concrete surface. The combination of wood and concrete in this table is what makes it a challenging build because the materials are worked so much differently, but this is also what makes it such a unique table.
Once you got your wood plank planed down to the thickness you want (I used 2"), and cut to length you need to prep and finish the surfaces. Don't worry about the underside or even the edges that will be encased in the concrete, you only need to finish on surface and the two end grains. Of course the first step is to sand until you get a good smooth surface, I went to 120 sandpaper on my orbital before filling the knots and holes with epoxy. I used a two part epoxy to fill the knot holes and other spots I wanted to see the character of the wood. If you're not familiar with this epoxy I would suggest experimenting with it a little first, people either love it or they hate it...or they think it's ok (RIP Mitch Hedberg). I used foil tape to plug any holes that went all the way through and to create a dam along some of the rounded edges so that I could pour the epoxy in there to prevent concrete from filling this space. Use a propane torch to remove any air bubbles when you pour the epoxy, just keep the torch moving, you don't want to burn the epoxy.
After letting the epoxy dry for a day or two I sanded everything flat, up to 220 sandpaper, then finished with several coats of polyurethane.
Step 3: Preparing the Concrete Form
The next step is to build a form and prepare to pour concrete.
I used 3/4" melamine to build the forms because the plastic coating of the melamine releases very easily from the concrete without the use of any release agent, and it makes a very smooth surface. I made the sides of my form 2" high, I wouldn't suggest going any thicker than this because holy cats this thing is heavy. As you will see in the pictures I put a dozen 8" stainless steel bolts into the side of the slab, this is to create a good connection between the wood and concrete and keep the two from separating. I suppose this is a good time to point out that I am casting this upside down, the finished part of my wood is laying face down against the form. This allows me to utilize the smooth surface of the melamine to give me an almost finish concrete when I pull it from the form. I then ran some 2x4's across the width and clamped these down to keep the wood plank flat and pressed up tight against the form to keep concrete from oozing in under the wood. The 2x4's also give me a good point to tie off my rebar so that it is hanging in the middle of the concrete. I used two #4 bars on each side running the length of the table. I would also like to point out that I made a sturdy cart with plenty of support to place this form on so I could move it around, make sure you have a sturdy base since this will literally weigh hundreds of pounds and you don't want your form sagging or breaking.
Step 4: Pouring the Concrete
The next step is to actually pour the concrete into the form. Sorry I don't have any good pictures of the actual pouring process, I was doing this as a one man operation and this stage is very time sensitive so I wasn't able to stop and take pictures. I also kinda forgot to because I'm an idiot.
I used a black liquid concrete dye to give it a good dark color, there are other color options and this is totally a personal preference. The concrete mix is the part that can vary the most in this project. You can find countless sources online of what mix to use and different additives. My Menards store actually sells a "countertop" concrete mix, I used this for my parent's coffee table and it turned out great. I used the cheapest concrete mix they had for my dining table, and it turned out great. So take that for what it's worth. I think if I were to make another table I would make my own mix just using portland cement and sand, I like the smooth consistency of the monotone colored areas that don't show any aggregate. I will talk more about the agg later.
Mix up your concrete and color before pouring into the mold. I tried to use as little water as possible to give me a stronger mix, but this was a mistake. Add enough water to make your pour very workable, it will still be plenty strong, I would say you're looking for a runny outmeal texture, not the peanut butter I tried to work into my forms. Work fast, the premix concretes set up quick. When you get it all poured in you will want to vibrate to get out as much air bubbles as you can, and to get the concrete flowing into all the nooks and crannies. I used a vibratory sander without sandpaper on it, runnining it all along the outside of the form. Level it out as best you can, but it doesn't need to be perfect because you can grind it smooth later. Cover it in plastic to keep the moisture from evaporating too quickly and let it sit for a few days, if it is very hot and dry I would suggest dampening the surface with a sponge a couple times a day.
Step 5: Finishing the Concrete
After you have left the concrete to cure at least a few days in the form you can take off the form and start the concrete finishing process. Concrete finishing is another one of those things that can be done a number of different ways, so I would suggest doing a little research online to find a process that seems best for you and the tools you have available.
I started off grinding the bottom to get it smooth. I used an angle grinder with a masonry grinding wheel, if you've never used this setup it is pretty slick, it cuts through concrete like buttah. After grinding the entire bottom surface smooth you will see a lot of small air pockets and voids where some aggregates were ground out, I mixed up some black un-sanded grout with acrylic fortifier to help with adhesion. Work this grout mix into all the voids with a rubber grout float or a good pair rubber gloves by hand to give you the smooth-to-touch surface. You only need to do this on the outside few inches where people would be running their fingers under the table, nobody is going to touch the middle of the underside, and if they do they can just shut up about it...jerks. Let the grout dry for a day then use some masonry polishing pads to wet grind the surface. You will want to get a wet polisher to do this. I just got some polishing pads that fit my orbital sander and held my hose on next to it. That's right, I used an electrical tool not meant to get wet in conjunction with a hose, do not do this, I am an idiot. I was pretty careful and I didn't get shocked, but you may not have the same results. Work your way up through the grits of polishing pads until you are done, then flip that bad boy over and take a look at the top.
Finishing the top is pretty much repeating the last few steps that you just did on the bottom. You will find some small air pinholes that you will fill with the grout mixture, then polish with your pads.
Here's another "issue" I ran into, I don't want to call it a mistake because it looks kind of neat and my wife likes it so that's all that matters. On my dining table I had a couple areas where the wood plank was not completely tight against the form so the concrete was sitting a bit higher than the wood surface. To make the surface smooth between the wood and the concrete I had to grind the concrete down, but this exposed a lot of aggregate in the mix. You will most likely see some agg after polishing, but this was a lot more. My wife said she likes the character of the exposed agg so I left it like that, but if you wanted to you could probably over-grind then backfill with the grout mixture so that you don't see the agg.
During the concrete polishing process you probably scuffed up the finish on the wood, but hopefully you didn't break all the way through the finish. Either way, just fix this with by some light sanding then applying more polyurathane.
Step 6: Table Legs and Benches
I'm not going to go into too much detail about the legs because you can really do this any way you want out of any number of materials. My parent's coffee table I used 2" square steel, welded it together, then applied a blueing finish. This was my first attempt at blueing and I think I still have some experimenting to do with this.
For my dining table I used some Kentucky coffee wood that I milled up from a farm nearby. I cut the metal braces from a long piece of scrap angle iron. The wood on the benches is the same Kentucky coffee wood, and I welded some square steel for those legs then spray painted the steel black.
I also forgot to mention that I used a woodburner to include a small inscription on the coffee table for my parents. This was done before applying polyurathane with the process as follows: Print out your inscription on regular paper in the size and font that you want, tape it to your wood, burn right through the paper into the wood tracing over the letters, sand after you are done to give clean edges to the lettering, then apply your poly finish.
Thanks for following along with my instructable, hopefully it wasn't too wordy. Let me know if you have any questions/comments/suggestions. And if you decide to make something using this as guidance please send me pictures, I would love to see it.
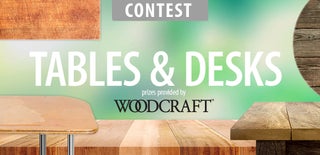
Grand Prize in the
Tables and Desks Contest 2016
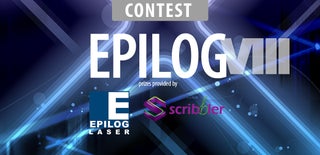
Runner Up in the
Epilog Contest 8