Introduction: Concrete Chicken (or Anything Else) With Polymorph
Concrete is the world's most abundant material, and chicken is the world's most abundant domesticated bird. Therefore, seems only right to bring the two together in this instructable .
Having made my concrete chicken, I'm not too sure what I'm going to do with it, but I'm sure it will become apparent in the coming months.
More importantly, this instructable is about technique; specifically the use of Polymorph to create concrete moulds. The construction of the mould (or formwork) is often the trickiest part of concrete construction. I am a structural engineer by profession, and have seen lots of complicate ways of forming smooth or intricate forms for buidling construction. On a domestic, and particularly hobbyist, scale, the concerns are cost, convenience and achieving a good, high definition finish. I think Polymorph is a good way of achieving this specification for small scale casting.
You will need:
Some polymorph (approx £10 per 250g pot, fully reusable, so you only need to buy this once, ever)
Some concrete (I have chosen a concrete repair mortar, approx £6 for 5 kg, more on this choice later)
A kitchen mixing bowl (not for mixing concrete)
Something to reproduce in concrete (A chicken ornament is my choice)
Water (generally free, comes out of the tap)
So, let's get casting a chicken (or whatever else you have to hand..)
Having made my concrete chicken, I'm not too sure what I'm going to do with it, but I'm sure it will become apparent in the coming months.
More importantly, this instructable is about technique; specifically the use of Polymorph to create concrete moulds. The construction of the mould (or formwork) is often the trickiest part of concrete construction. I am a structural engineer by profession, and have seen lots of complicate ways of forming smooth or intricate forms for buidling construction. On a domestic, and particularly hobbyist, scale, the concerns are cost, convenience and achieving a good, high definition finish. I think Polymorph is a good way of achieving this specification for small scale casting.
You will need:
Some polymorph (approx £10 per 250g pot, fully reusable, so you only need to buy this once, ever)
Some concrete (I have chosen a concrete repair mortar, approx £6 for 5 kg, more on this choice later)
A kitchen mixing bowl (not for mixing concrete)
Something to reproduce in concrete (A chicken ornament is my choice)
Water (generally free, comes out of the tap)
So, let's get casting a chicken (or whatever else you have to hand..)
Step 1: Prepare the Chicken
I have selected this fairly ugly looking chicken clock as my artifact from which I will make the concrete replica. We firstly remove the clock mechanism (as this will not cast well).
This clock is make of ceramic, which makes it good for producing a mould, as it is not particularly flexible and doesn't contain many sharp corners (always vulnerable in concrete).
This clock is make of ceramic, which makes it good for producing a mould, as it is not particularly flexible and doesn't contain many sharp corners (always vulnerable in concrete).
Step 2: Melt the Polymorph
Polymorph comes in beads in its raw form (or whatever shape you moulded it into last time). It is a low melting thermoplastic, which is manually reshapable in hot water.
Fill the bowl with just-boiled water and add the polymorph beads, and they will start to go transparent and stick together. When most of the beads are clear, remove them from the hot water, either with tongs or a nearby fork. Shake the excess water off to avoid scalding your hands and manually reshape the beads until you get a flatish sheet.
Repeat this as many times as you need to. It took me about 4 or 5 goes to get the thickness I wanted (about 7mm approx).
Fill the bowl with just-boiled water and add the polymorph beads, and they will start to go transparent and stick together. When most of the beads are clear, remove them from the hot water, either with tongs or a nearby fork. Shake the excess water off to avoid scalding your hands and manually reshape the beads until you get a flatish sheet.
Repeat this as many times as you need to. It took me about 4 or 5 goes to get the thickness I wanted (about 7mm approx).
Step 3: Filling Any Gaps in the Mould, and Overlaying Onto the Artifact
You can stretch and reshape the polymorph as much as you want, but it may produce holes. The concrete will seep through these if you're not careful, so we need to pulg them.
Lay your sheet over you artifact to see where you have excess material, and where you have gaps. I found the easiest way of moving the material around is waiting for the sheet to cool a little, then using side cutters to cut the material off.
Place these offcuts in the hot water bowl and wait for them to go transparent again, then remove them from the bowl and stick them in the place you need them on your mould. They will reattached very easily, particularly if you've reheated you mould by giving it a quick splash of hot water.
I found a useful way of finding holes in mould was to hold it up to a light and see where the light shines through.#
Through process of reimmersing the mould and overlaying it on the artifact, the sheet should take a 3D shape. Press the sheet hard against the artifact, particularly at areas of detail. Make sure you have a small amout of excess material all the way around the edge of your artifact object.
Lay your sheet over you artifact to see where you have excess material, and where you have gaps. I found the easiest way of moving the material around is waiting for the sheet to cool a little, then using side cutters to cut the material off.
Place these offcuts in the hot water bowl and wait for them to go transparent again, then remove them from the bowl and stick them in the place you need them on your mould. They will reattached very easily, particularly if you've reheated you mould by giving it a quick splash of hot water.
I found a useful way of finding holes in mould was to hold it up to a light and see where the light shines through.#
Through process of reimmersing the mould and overlaying it on the artifact, the sheet should take a 3D shape. Press the sheet hard against the artifact, particularly at areas of detail. Make sure you have a small amout of excess material all the way around the edge of your artifact object.
Step 4: Mix the Concrete
I have chosen a concrete repair mortar as my desired concrete mix. This was for the following reasons:
1. It comes in a sensible size (I don't need to buy 20kgs of it, for a small mould)
2. It comes in its own bucket which is convenient for mixing
3. Concrete repair mortars are typically fairly strong, which is helpful for robustness
4. Concrete repair mortars don't contain large aggregate, which is more likely to give us a good finish
5. Concrete repair motars are ofsten shrinkage compensated, which means they contain admixtures to prevent shrinkage of the mix as the concrete goes off, and possibly prevent some cracking
6. They cure quite quickly. I wasnt particularly pressed for time, but it's a nice-to-have.
The bucket contained two separate 2.5kg bags. I only needed one of them. The instructions suggested adding 400ml of water, but I added more like 800ml-1L to improve the workability of the mix. This is not recommended for structural concrete, as the water-cement ratio has big consequences for the concrete strength, but given that this is not load-bearing, it's ok. I added water until the mix was fairly sloppy, enough such that it would work itself into the different parts of the mould without any additional persuasion. I used an old wooden spoon for mixing in the bucket.
A couple of saftey points. Avoid breathing in the cement dust - it's carcinogenic, and wear rubber gloves to avoid chemical burns from the wet concrete. other than that, you'll be fine!
1. It comes in a sensible size (I don't need to buy 20kgs of it, for a small mould)
2. It comes in its own bucket which is convenient for mixing
3. Concrete repair mortars are typically fairly strong, which is helpful for robustness
4. Concrete repair mortars don't contain large aggregate, which is more likely to give us a good finish
5. Concrete repair motars are ofsten shrinkage compensated, which means they contain admixtures to prevent shrinkage of the mix as the concrete goes off, and possibly prevent some cracking
6. They cure quite quickly. I wasnt particularly pressed for time, but it's a nice-to-have.
The bucket contained two separate 2.5kg bags. I only needed one of them. The instructions suggested adding 400ml of water, but I added more like 800ml-1L to improve the workability of the mix. This is not recommended for structural concrete, as the water-cement ratio has big consequences for the concrete strength, but given that this is not load-bearing, it's ok. I added water until the mix was fairly sloppy, enough such that it would work itself into the different parts of the mould without any additional persuasion. I used an old wooden spoon for mixing in the bucket.
A couple of saftey points. Avoid breathing in the cement dust - it's carcinogenic, and wear rubber gloves to avoid chemical burns from the wet concrete. other than that, you'll be fine!
Step 5: Pour the Concrete
Pour the mix into the mould, and float (finish flat) the top surface of the concrete as level as you can.
Then leave for a few hours. I left mine overnight as it was just more convenient that way.
If you're wondering what I did with the rest of the concrete, look for the 'Lend a (concrete) hand' instructable
Then leave for a few hours. I left mine overnight as it was just more convenient that way.
If you're wondering what I did with the rest of the concrete, look for the 'Lend a (concrete) hand' instructable
Step 6: Surface Finishing
The ease of removing the mould is dependent on the artifact shape, so in this case it was quite easy, just apply a little torque to the mould with your hands. In more complicated cases, either cut the mould off with a craft knife, or use steam to make it more soft and pliable.
Some surface defects may be apparent, holes (known as blowholes) may be present where an air bubble has been caught. Common causes for this are the mix being too stiff and not allowing air to escape, or inadequate vibration, which allows air buble to work themselve free. In this case I didn't have a way of vibrating the mould, so I tried to make sure the mix was fuild enough not to trap too many air bubbles.
Other surface defects, such as small protrusions due to mould defects and 'flashing' due to leakage of the concrete beyond the formal bound of the mould, can be removed using sandpaper.
The finish/decorate to your requirements. Remember the mould plastic can be re-melted and used for another project.
Some surface defects may be apparent, holes (known as blowholes) may be present where an air bubble has been caught. Common causes for this are the mix being too stiff and not allowing air to escape, or inadequate vibration, which allows air buble to work themselve free. In this case I didn't have a way of vibrating the mould, so I tried to make sure the mix was fuild enough not to trap too many air bubbles.
Other surface defects, such as small protrusions due to mould defects and 'flashing' due to leakage of the concrete beyond the formal bound of the mould, can be removed using sandpaper.
The finish/decorate to your requirements. Remember the mould plastic can be re-melted and used for another project.
Step 7: Finished
Final concrete product, ready for, er, something.
Happy concreting!
Happy concreting!
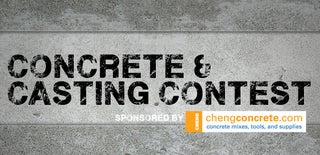
Participated in the
Concrete and Casting Contest
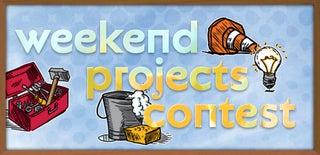
Participated in the
Weekend Projects Contest