Introduction: Convert Your Pickup Truck to a Flatbed
Step 1: Tools and Materials
The flat bed I built is 6' x 6' 4" steel frame with a wood deck. This configuration would fit any full size 6' bed truck. You can easily adjust the dimensions to fit your own truck. Finding the raw materials can be tough because you can't get the larger stock metal in most local hardware stores.
I ordered my steel from a local supplier.This cost $249 for 200lbs of steel. The price included cuts making the price about $1.25 US per pound. Don't be intimidated ordering from big industrial suppliers. Many of them will accept cash orders for pick-up. You may be able to get a deal buying what they consider scrap.
Things you will need
TOOLS
- drill and 5/16" drill bit
- welder
- reciprocating saw with metal blades or cutting torch
- metal clamps (I used all the clamps I own)
- tape measure
- soap marker
- circular saw
- grinder with wire wheel (or wire brush)
*optional cutting torch - I used this to expedite removing the old rusted bed
PROTECTIVE EQUIPMENT
-Welding Gloves
-Welding Hood
-Cotton Clothing or Welding apron or jacket **(Do Not Wear Synthetic Clothing as it will melt)**
-Leather work boots
MATERIALS LIST
6 - treated 2x10x6
1 - treated 2x12x6
24 - carriage bolts 5/16" 2"
24' - 2" x 4" 11 gauge rectangular steel tubing
40' - 2" x 2" angle iron
* optional 6' - steel C channel
1 - trailer light kit
4 - black spray paint
COST
trailer lights - $60
hardware/ paint $30
lumbar - $90
stock metal - $249
Total cost - $329
Step 2: Remove the Old Bed
First you will need to remove the tail lights. Since my truck does not have any tail lights present aside from the temporary. I skipped this step.
To remove the bed there are typically 6 bolts holding on a truck bed. Two found near the cab and four found toward the rear of the frame. You will need to use something to help break the rusted bolts free (I used pb blaster). I lost patience very quickly and decided to cut the bed off with a oxy acetylene torch. You could also use the reciprocating saw to cut the bed free from the frame.
Since I opted for the torch. I removed the plastic bed liner and cut through the bed with the torch to expose the bolts. I used the torch to cut the bolts off and now the bed can be removed.
At this point it is a good idea to do some maintenance on the frame while it is exposed. I sprayed it off with a hose to remove the mud them used a wire brush and a chipping hammer to knock off the rust. I then took a break to put a light coat of primer to protect the frame since I was out of time for the day. ( I added a layer of bed liner to the frame after i completed this instructable)
Step 3: Cut and Prep Your Materials
4 - 6' (2"x4" rectangular tube)
6 - 10" (2" 1/8" angle)
4 - 5' 8" (2" 1/8" angle)
After you have all of the metal cut use a wire wheel or brush to clean off the mill scale at the weld locations. I also used wood clamps and some wood blocks to hold the materials in place for welding.
Step 4: Layout and Welding
The layout for this truck bed is simple the 4 rectangular tubes are tack welded at the corners. Then the angle iron is clamped in place using a scrap piece of wood 2x4 and some miscellaneous clamps then tack welded. Once all the angles are in place horizontally I used wood blocks to level the new bed in place over the frame. I used the wire wheel and grinder to clean the rusty truck frame at the weld location. The 6 pieces of 10" long 2" angle are welded to the frame of the new flat bed and to the frame of the truck. If you plan to do this on your truck make sure you check the distance between the rubber stop that keeps your rear axle from hitting the frame. You want the clearance from the bottom of the new flat bed to be greater than the distance between the stop and the axle. This will help ensure your tires won't ever rub on the new flat bed.
After all the tack welding is completed clean the slag from the welds and then methodically go through and weld each joint with a finish weld. Make sure to do this symmetrically so that the heat does not warp the metal of the new frame.
* side note: Warping will happen when you heat metal the middle it does not have anywhere to expand but when it cools it cools uniformly and contracts pulling and warping the metal towards the weld. You can actually use this to your advantage with a torch and heat bend big metal just by carefully heating specific areas and allowing them to cool creating a curve. you can also help avoid this by minimizing the welds spacing them out evenly and welding on both sides of the stock being welded. There are many resources online for this if you have problems with your welds.
I used C channel and the leftover angle iron to build a frame to protect the cab. 6ft piece of C channel and four 14" pieces of 2" angle.
After you have completed the welds clean off all of the slag and spatter with a grinder or wire wheel. I wiped down the new frame with a little alcohol and now we are ready for paint and the Wood deck.
Step 5: Cutting and Attaching the Lumber
In this step I measured out all of my lumber and cut each piece down to six feet. I wanted to use standard lumber widths to make it easier to replace the boards if needed. This worked out to six 2x10's and one 2x12 with about a 1/16" on either edge. Then on either end of each board I drilled two 5/16" holes and bolted the wood down with 5/16" carriage bolts.
Step 6: Painting and Finishing the Frame
After the paint drys I will bolt the wood deck back down. I drilled the holes first so that I could get paint into them and hopefully delay rusting.
[Thanks to everyone's comments here I have decided to coat the whole flatbed frame with bedliner. I will add this step to the instructable once I have it completed. Thanks!!]
Step 7: Attach the Tail Lights
Drill two holes on the bottom of the 2" x 4" rectangular tube and attach the lights. Then strip and connect the wires to the trailer light harness of the truck. Black to black white to white, yellow to yellow, and green to green. If you do not have a trailer light harness you can always just mount the old tail lights horizontally under the flatbed or install a trailer wiring harness.
I have used the bed several times to pick up large loads of lumber and it has done great. I plan to build a headache rack and possibly some removable sidewalls in the future but for now the truck is ready to go for the summer.
That's it I hope you like this project.
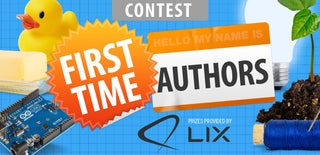
Participated in the
First Time Author Contest 2016