Introduction: Turning 3D Models Into Aluminium Objects With Old Soda Cans
In this Instructable, we'll be looking at how to turn a 3D model into a physical object, using metal recycled from aluminium drink cans. While not hugely accurate, theses models provide a good size estimate and look pretty cool when assembled. You can use many types of can to make your design, Coke, Pesi etc. Drink cans are easy to use, as they cut fairly well with scissors and can be glued, riveted or even taped into shape.
So let's get to business turning your old cans into models.
You will need the following:
1) Aluminium Cans
2) A pair of decent scissors - I used "Craft" scissors and they worked quite well
3) Either tape, glue suitable for metal or rivets to put the pieces together
4) Autodesk Inventor (Other 3D modellers may work, as long as they can produce folding patterns)
5) A regular printer
If you want to just skip the design process and make the plane model above, I've included the template file for Autodesk Inventor under the "Creating a Template" Section and can be assembled to match the photos.
If you like this Instructable, please remember to vote for it in the "Mind for Design" and "Reuse" contests.
Step 1: Design the Model on Autodesk Inventor
Firstly we need a model to make. This can be literally anything you want, bearing in mind you have to physically make it later on. To design the plane model above, I created the basic parts, such as wings, frame and rotor piece separately and used the "Shell" tool to make sure the model had an even thickness of 0.2mm, roughly the same as my can.
The main concern when producing your model is size. Typically, your largest parts need to fit inside a 80x188mm rectangle for a 330ml can, or even less depending on how neatly the can is cut. When making slots or cuts, check the gap is big enough for the metal's thickness to fit.
Once you're happy with your model, and you're sure it can fit together, you can then begin to create a template.
Step 2: Convert the Model Into Sheet Metal
Firstly we need to convert the model into Sheet Metal and unfold the 3D model to produce a 2D shape.
In Autodesk Inventor, there is a button, top right under the "3D Model" tab, that will convert your part into Sheet Metal. Click "Sheet Metal Defaults" and specify the thickness of the metal to 0.2mm after un-checking "Use thickness from Rule". Then press "Create Flat Pattern". You will then see a fold-out of your model as if it were paper. If you don't, there are fold and cuts in the model that you need to make. For example, cylinders will need a slit down them to unfold and boxes will need "Bends" instead of corners to allow it to fold into place.
The best way to explain this process is to image a flat-pack dice. The six faces must be cut properly to allow it to collapse into a 2D shape, similar to a T, as shown above. If the model cannot automatically unfold, we need to manually specify where the cuts and folds are.
To make the cuts, it's easiest to create a cut the same thickness as your metal if not a little more. This will allow the model to fold together roughly in-shape, and you can add "tabs" to the flat pattern with extrusions to make it easier to fold together, especially when glueing or taping.
Once all of the pieces have been turned into flat patterns, we can make a template.
Step 3: Creating a Template
The template is what we will use when cutting the metal to produce the individual pieces.
To create the template, open a new Drawing File, ISO.idw. then right click "Sheet 1" on the left and select A4.
Then we add views by clicking "Base" from the "Place Views" tab and opening a part, for example a wing. Within the same window, we need to specify a 1:1 scale with hidden detail (the cylinder with lines through it on the right) and check the option for "Flat Pattern".
Once that's done, click on the paper to place the drawings, right-click and "Ok" and press escape to finish placing the view. Repeat this with the rest of your parts until you have them all. If you have too many pieces, create another sheet and repeat.
When this is finished, click the "I" in the top left corner and click print. Now we have a paper copy of our parts in the right size.
The template I used to create my plane can be found below:
Attachments
Step 4: Cutting Up Cans
To make our metal components we need metal. To do this, we'll recycle old soda cans into sheet metal.
Be warned, working with thin sheets of metal can be dangerous and you may get cut. Take great care when working with the metal to avoid injury and be prepared to clean up any slivers of aluminium left behind from the cutting.
Firstly,make sure the cans are empty so that no liquid spills out. To start off, we cut off the tops and bottoms of the can, leaving behind a thin cylinder. Then, one cut is made down the side of the cylinder to produce a "Sheet" of metal, albeit slightly curved. Cut the edges of the sheet straight so it is easier to work with. At this stage you'll want to clean off any drink residue with a damp paper towel to clean up the metal's appearance. The metal is then flattened by smoothing it against the curve on the edge of a desk until reasonably flat.
With any luck, you'll now have a sheet of approximately 80x188mm, or bigger depending on the can.
This process is repeated until you have enough metal for your project. To make my plane, I used a can and a half, so I prepared two cans.
Step 5: Cutting Out the Templates
Now we need to cut out our templates with the metal to produce metal parts.
Firstly, cut out the templates roughly and stick them on top of the metal (Photos 1 and 2). To do this, I rolled a piece of Sellotape over itself to produce an O shape with the sticky side outwards, before sandwiching it between the templates and the metal. Then with a pair of scissors, cut out the templates and as you do so, the metal will cut into the correct shape. Repeat this for each part and eventually you will have all of the parts you designed in the 3D modelling stage.
Step 6: Assembly
Lastly the pieces need to be put together. Referring to your 3D model, assemble the parts accordingly and join them together with either tape, glue suitable for metals or even rivets if it is a large project. When assembling, it's best to have some spare metal to "patch up" or reinforce your model in case you make a mistake while putting it together.
Once you have the model completed you can add finishing touches. For example, on my plane model, I twisted the propeller blades and shaped them to look a bit more like real rotor blades. Any extra non-sheet metal items like wheels etc can also be added. To create holes for axles or as part of the design, try using a hole punch to create a neat hole in the metal.
And now you can admire your creation.
You're finished!
You can go on to paint the object or leave it as-is.
This method could even be replicated with cardboard or other materials, as you only need a template, a material and something to hold it all together.
Thanks for reading, I hope you found this Instructable useful. If you liked this project, be sure to vote for it in the contests, and feel free to ask any questions.
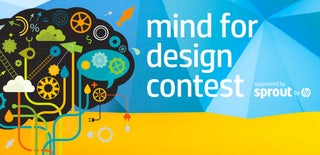
Participated in the
Mind for Design
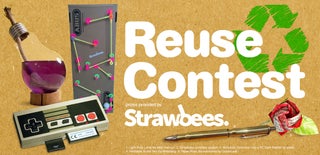
Participated in the
Reuse Contest