Introduction: Copper Perfume Flask Pendant W/ Brass Accents
Intro
Making a mini copper and brass perfume flask is a fun and easy project. You can learn some great metal forming techniques if you try and follow along. This perfume flask has a striking forged shape to it with a cool concave brass "punt" (like the bottom of a wine bottle). You could also just solder a straight flat bottom on your flask but then you don't have the legendary excuse to buy a dapping set. these dapping block and punch sets are actual fairly inexpensive. you can find them cheap at harborfright tools or riogrande.com I think they are around 20-35 dollars. there is also some fancy Dursten branded dapping block and punches that are around 300-500 dollars. I think (hope) they are atleast made out of hardened steel if they are that expensive. Much like every tool you don't really need the "fancy" ones if you are just starting out. This perfume flask is made out of recycled scrap copper pipe from a bathroom sink off the curb. The brass tubes I got at the local hardware store years ago. I don't know what size they are as I just bought one of every size available. IF YOU CAN AFFORD IT.. DO THIS. its amazing to have every size tube in stock for all your projects. Just get some that will fit snugly inside of each other. The brass sheet for the bottom punt is also from the scrap box same as the silver wire small pieces of scrap from other jewelry.
In this instructable I am going to explain more about the metal forming and assuming you already know how to solder using hard silver solder. silver solder is used by silversmiths instead of soft solder used for electronics. hard solder is much stronger and requires hotter temperatures. hard solder is also nicer for your skin as less people react to it compared to lead or even lead free solder. If you dont know how to hard solder I described how the process works in one of my other instructable called Metal Steam Powered Boat. in that instructable I give more indepth description of what hard soldering is and how to do it.
Tools
You will need some basic jewelry tools :
- soldering setup: torch, flux, pickle.
- jeweler saw.
- Dapping block set.
- Mini pipe cutter.
- Flashlight.
- Files.
- Sandpaper.
- Hammers.
- Dividers.
- Needle file.
- Deburing tool.
- Chain nose Pliers.
- Round nose pliers.
- flush cutters
- ring clamp
Materials
- Copper pipe scrap I think its 1/2" size
- Brass sheet I used 20gauge
- Brass tube two: it doesn't matter what size you use as long as the two sizes fit snug into each other.
- Sterling silver wire scraps. 18ga wire about one inch total
- Sterling silver chain. I used a medium sized chain for necklaces part and then a fine one for the cap retainer chain.
Step 1: Forging the Body and Soldering the Spout
RAISING
The first step is forming the basic shape of the perfume bottle. This is done using a technique called raising. Raising is when you use a piece of steel called a stake and a hammer. It is traditionally used to make hollow ware such as vases bowls cups teapots. You hit the metal sheet thousands of times and with each smack of the hammer you are bringing the edge of the metal up and in towards itself. Normally you start out with a flat sheet and "raise" the edge up. As you bring the edge or rim up it starts to get thicker as the metal slowly compresses onto itself as the metal has to go somewhere.
HAMMER The silversmiths hammer is also a very important design with hundreds of shapes. For this simple project a basic cross peen shape is all you need. This hammer is a modified hammer from a garage sale 25 cent special. My friend sanded it down for me on his awesome elis belt sander to a really nice profile for moving the copper around (see pictures). There is a radius slightly larger than a number two pencil radius on the cross peen side and the other side has a slightly rounded face with rounded edges.
STAKE For ever shape of vessel a silversmith wants to make they need a different shaped stake. Most silversmiths have hundreds of stakes they make as they need new shapes for new projects. For this project the stake is very simple. you want to find something that fits inside the pipe with a little bit of air or room around the stake. I used the bottom side of one of the daping punches held in a vise. You are going to slide the copper pipe over the stake so the copper is overhanging above the edge of the stake. You are gonna have to smack the copper that is "floating over" or "above" the stake. I had about 3/8" overhang off the top. Rotate the pipe around the stake and continue to bonk the edges down. When you are moving the copper around it will get work hardened, it becomes brittle and difficult to move. You can soften the copper by annealing it. All you need to do is heat it up to a red color let it soak in the heat for about 20-30 seconds and then quench it in room temperature water. This makes the copper dead soft. It also gives the copper an oxidation layer on the surface. You can remove it in the pickle pot. Now that the copper is clean and dry you can do another round of raising. The next step is to planish the metal. When you were "raising" you were compressing the metal and making it thicker. It's got some bumps on the surface from the hammer marks. You can even these out by planishing or stretching the metal with a hammer against the stake instead of hitting the floating unsupported area. you just want to strike the copper against the stake underneath this flattens out and stretches the copper.
Measurements are just numbers to be used by organizations like NASA and architects. This piece of jewelry isnt going to space or hold up a wing of a hospital so everything is just kind of eyeballed to whatever I thought looked good at the time. I think the original cut of the pipe was around 1-3/4 inches long. i took a lot of pictures so look at them
FORGING THE BODY
- 1 cut the copper pipe at whatever length you desire with mini pipe cutter
- 2 de-burr the sharp end of pipe
- 3 anneal the copper pipe
- 4 start raising the edge into itself.
- 5 when it gets harder to hammer anneal the copper pipe again. Use dividers to make a uniform line to follow with your hammer.
- 6 raise another round. Here the ends are starting to look like something.
- 7 anneal again.
- 8 use the hammer to move the metal on the tip of the stake to close up the diameter of the hole to a smaller size to fit the tube. Stretching the metal is also gonna even out the highs and lows of the hammer marks this is called planishing.
- 9 once the hole is slightly smaller than the brass tube you can use the needle file to remove some area around the hole to make a tight fit over the smaller sized brass tube.
MAKING THE SPOUT
- 10 cut a piece of the brass tube an appropriate size for your spout.
- 11 flare out one side of the tube using a dapping punch. If you put one side on a flat surface and hit the other side with a round punch then one side stays flat and the other gets flared out. (The flare is optional but I feel that it makes it easier to help hold the tube in place when it's time to solder).
- 12 put the tube inside the hole from the other large open side.
- 13 solder the brass tube into the copper flask using hard solder.
- 14 put the flask in the pickle pot to clean off the flux.
Step 2: Tiny Flask Cap
TINY FLASK CAP
- 15 take the corresponding brass tube that snugly fits over the smaller tube in the flask and cut off a small piece for the cap using the mini tube cutter. You can use any length you desire. The longer the cap is the more snug it will fit.
- 16 i didn't de-burr this edge as it seemed like it had a snugger fit on the flask bottle neck.
- 17 sand the oxide layer off the brass sheet scrap.
- 18 solder the tiny tube cap onto the brass sheet .
- 19 place oxidized parts in pickle pot.
- 20 cut off remaining sheet protruding past the cap with jeweler's saw.
- 21 curse the world as you drop the part on the floor and spend 10 minutes looking for it with flashlight. Woo! Congratulations on finding your part!!!! now sand or file the jagged edges from the saw cuts until it is totally flush and pretty.
Step 3: Bottom of the Flask
you could solder on a flat piece of copper onto the bottom the flask would look cool... but this curvy bottom looks way cooler. the copper is soft on the bottom still so all you need to do is hold the flask and dapping punch in your hand and gently bonk the punch into the flask with a hammer in your other hand. keep putting bigger punches in the hole until you like the look of the flare.
BOTTOM OF THE FLASK
- 22 using the dapping punches progressively push the punches up into the bottom of the flask bulging out the bottom until it has a desired amount of bulge. this is set to your own satisfactional standards of bulge. Consult your handbook.
- 23 make a educated guesstimation at the amount of metal you need to cut out for the bottom. (Look at pictures) scribe this magical sized line around the flask with a pair of dividers onto the brass sheet.
- 24 cut out the disk with the jeweler's saw.
- 25 sand off the oxide layer and de-burr the edges on both sides
- 26 place the disk into the largest concave hemisphere and give it some wacks with the largest dapping punch. Start at the edges and work your way in to the middle.
- 27 anneal with torch and pickle to remove oxidation layer.
- 28 processed with corresponding punches and dies until you get a desired size hemisphere to stuff into your bulged bottom.
- 29 de-burr the bottom of the flask, file out the very bottom edge so it matches the same shape as the brass hemisphere.
- 30 solder the hemisphere into the bottom using hard solder. Be careful not to over heat the entire copper flask body or else the top part of the bottle neck/ spout will fall off.if you wanted you could use hard solder on top and medium on the bottom. I just use hard solder and was careful to not overheat it.
- 31 saw off the excess amount of brass on the bottom. Making the bottom too big is okay. Just call it a learning experience with guesstimates and now your eyecrometers are slightly more calibrated for flat to round conversions.
- 32 file and or sand the burr off the bottom from cutting. Sand the copper off that migrated to the surface off the brass during soldering. Ohhhh so shiny & pretty.
Step 4: Adding a Chain
you could be done with the project and have a cool little bottle for your pocket.... or you could add a chain to it and wear it around your neck and show it off!!!!!
ATTACHING THE CHAIN
- 33 take some 18ga sterling silver wire and bend three small U shaped pieces of wire for the jump ring connector bails.
- 34 solder these onto your perfume flask wherever you want I thought about the top part but decided to put it on the sides. I cut out six pieces of solder. I balled up the six pieces and I melted one ball on each end of the U legs. I think this is called tinning your parts. I heated up the flask body untill the flux glasses over then I put the tinned part onto the hot flask body. Its easier than trying to line everything up and then to drop balls onto the joint.
- 35 pickle and sand all the undesirable oxide off the awesome little copper and brass perfume flask.
- 36 attach the silver chain onto the flask and cap using jump rings.
- 37 solder the jump rings closed (I didn't yet but I will once I decide how long to make the chain)
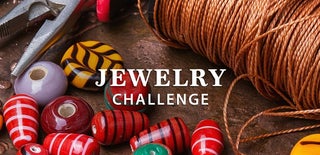
Participated in the
Jewelry Challenge