Introduction: Crazy Fast Electric Bicycle Conversion
The craving of speed and power just rushed our faces as we upgraded our electric bicycle from a greared DC motor to an outrunner Brushless motor.
Yes we have converted our bicycle twice once with a geared brushed DC motor and the other time replacing it with a brushless motor from an old hoverboard. Both the conversion were a sucess on their own and taught us alot, the gearing ratios, selection of motors and speed controller, the amount of power and much more. So we have got a bunch of recipies through our way and its time to step up the game by reconverting our electric bike into a Beast of an electric bicycle conversion.
Hang in there as we are going to share our paddled up learing and who knows you might end up converting yours...
Supplies
The list of tools and supplies for this project might go on and on but dont restrict yourself by the tools you have, the best one is right inside your head.
Materials:
- A bicycle (This one is a 20in BMX copy with fat tires to sustain those speeds)
- A Brushless motor from a hoverboard
- A BLDC motor speed controller for electric bike
- Throttle assemble
- Battery pack
- Spocket
- Chain
- Footrests
Tools:
- Drill machine and bits
- Basic pliers
- Soldering tools
- A 3D printer (Just if you want to built customized 3D printed parts)
Step 1: An Overview of the Previous Conversion
Have a look at the previous two conversions that we have done over this bicycle.
The Brushed DC motor conversion:
The Brushless DC motor conversion:
As we converted our bicycle into an electric one we learnt about the amount of torque we need to start rolling. but as we gathered the required torque by gearing the brushed DC motor which by the way offers way less torque as compared to a brushless outrunner motor of the same size, we ended by havinf very low speeds.
So later we moved towards a more, I mean much more powerfull Brushless outrunner motor from an old hoverboard and that motor literally pulled whelies over. The torque we attained was awesome and the speed was arround 40km/h, which is good for an electric bicycle conversion by thats not crazy fast. The reason behind that is a relatively small speed controller from an old RC car, that thing can not handle voltage above 22.2v and thus we ended up using high discharge lithium pollymer batteries that was also used in RC cars. For sure they provided the required power but not for that much long as they were just 100 watts/hr capacity. The maximum range on a single charge is just a miserable 4-5 km. Yes obviously we can through more of them onboard but as its a bicycle so we are really tight in terms of space and believe me they are too expensive.
Now its time for some crazy customization to push this conversion to limits.
Step 2: Replacing the Motor
With the previous upgrade using the brushless motor, we have used a brushless motor from an old hoverboard but due to the limitation of our controller we have decided to alter the winding patern to achieve three time more speed. But this time we dont need any of that conversion as we are going to switch to a relatively high voltage system that enables us to handle much low current which interns solve the heating issues and the whole system becomes more efficient. Besides we kept the hall sensors intact as the controller we are going to use requires hall sensors to drive the motor. Compared to a sensorless controller,this helps to smoothly run the motor specially as the motor beings to rotate.
So we tossed the stock brushless motor from an old hoverboard and replaced the backplate with one over the previous motor. As it has a 13 teeth spocket mounted over that to drive the rear wheel. Once the spocket is mounted over the stock motor we then mounted the motor over the bicycle using the motor coupling.
Step 3: The Brushless Motor Controller
On one of our countless visits to Shershah, the local scrapyard we found a BLDC E-bike speed controller thats rated for 84v DC and 50 A continious current draw with 3000 watts of max power. Now thats a whole lot compared to the previous controller from RC car as that can handle only 22.2v at arround the same current ratting.
The only problem was the condition of the controller. But still we took a chance,brought it home and tested in our workspace and this thing works like a charm.
As one of the end plate of the controller casing is missing it was clearly evident that this enclosure is way too big for the controller. Besides that those hanging wire were a complete mess. So we decided to design and 3D-print a new enclosure for the controller so to customize this thing to fit neatly on our bicycle.
Step 4: The Enclosure for BLDC Motor Controller
The controller is provided with a heat sink almost in the middle over which all the mosfets are mounted that are going to heat up the most. Previous enclosure was built out of aluminium and act as a heat sink to decipate the unwanted heat produced by mosfets. So to compensate that we are going to use an aluminium heat sink that seems large enough to get the job done. So the whole enclosure was designed accound the aluminium heat sink. The controller is going to be mounted using that heat sink on the other side thus sandwiching the 3d printed enclosure inbetween.
To get rid of hanging wire we have decided to use PCB connectors for the acessories like hall effect sensors, speed selection and a bunch of more usefull and not so useful options. For the input we are going to use male XT-60 connector and for the power wires to the motor we have use three 4mm bullet connectors. All there connectors are acessible over the face plate so we designed the front plate accordingly.
Besides we have also designed and printed the mounting assembly for the controller enclosure. Its a two part mount, one is going to be mounted over the bottle mounting post on bicycle and the other part is going to clip the the enclosure.
Later we printed all the parts and everything seems to fit right in place.
The STL files for the 3d printed part are listed below:
Step 5: Speed Controller Modification
To get the new enclosure in place we took the controller apart. We then carefully marked and tagged the wires for each sensor and later we plot a wiring diagram corresponding to their positions on the PCB and the function they are made for. Later we trimmed all the wire to their lengths, glued the connectors on the faceplate and sottered them in place.
Once we are done with the face plate we pushed the controller PCB in place with the heat sink placed over the other side with the help of four allen screws. Later we mounted the face plate using four cut screws to keep everything in place.
Now with this conversion we are able to reduce the footprint of the controller by almost threee times as much compared to the previous enclosure with hanging wires. Besides that the onboard connectors is was neat and safe as compared to the previous setup.
Step 6: Mounting the Speed Controller
The speed controller is mounted in the middle of the bike over the bottle holder mounting using our custom made mounting clip.
Once the controller is in place we then connected the power wire to the bullete connectors and connected the male connector for the hall sensors over the PCB connectors. Later we connected the hall sensors.
Step 7: Battery Packs
The biggest challange we faced with the bicycle conversion is with the limited space. Although we managed to use the motor on a sweet spot with very limited modifications but still with the controller mounted inbetween the middle of the bike we are left with very limited space to fit sufficient battery capcity considering the compromises of using a stock battery pack.
So we have designed and built our customized battery packs by using a old lithium ion battery pack from scrapyard as well. Now as its a complete procedure to built a custom battery pack specially with used lithium ion batteries, we have done a dedicated project video and an instructables article over the topic.
Now we built two battery packs, each one offers 42v and 300 Wh capacity. So we are going to use two of them connected in series to operate the controller at 84v. This high voltage system enables us to achieve sufficient output power without dealing with insane amount of current which helps to avoid overheating and thus the whole system operates much more efficiently.
Now these two packs combined provides an onboard capacity of 600 Wh, thats six times more capacity than the previous setup. Thanks to the customization and the 3D-printed enclosure to help us design the battery unit as per our requirments.
The STL files for battery enclouser is listed below:
Step 8: Battery Holder
We have designed the battery packs to go under the bicycle seat over the rear end. For that we have designed the battery holder thats going to house both the battery packs side by side. Both battery packs weights arroud 3kg so we have to be careful to make the battery holder to have sufficient strength to handle the weight over the bumps during the ride.
To keep the deisign simple yet effective we designed the battery holder to mount over metal pipe under the bike seat. Followed by that is a verticle plate to provide the whole structure required strength.Now to stop the battery packs from sliding sideways we have designed the top plate with a pair of arms that are going to be glued over the top plate. Once the battery packs are in place the top plate is then mounted in place with the help of four allen screws.
While the battery holder is kept in place over the metal pipe beneath the seat with the help of three allen screws.
The STL files for battery holder are listed below:
Step 9: Fixing the Footrests
Next we fixed the footrests as previously we mounted them using a single allen screw across a metal sheet. So we welded the metal bar along with the footrest holder, painted the whole thing and screwed it in place using a pair of allen screws.
The holder goes righ in place adn doesen't seems to mess arround. Now with that being done its time to charge the battery packs and take the beast to the ride.
Step 10: Testing the Bicycle
Now this conversion ended up way better than what we have expected, the torque is amazing and the top speed was a bit over 60km/hr. With the heavy pull over throttle the bike seems to consume 30 wh/km which means that with the current battery capacity we can easily get over 20km of range on a single charge or even more if we ride at moderate speed.
Next me and my brother hopped on the bike and to our surprize it seems to handle the load preety well. The acceleration felt almost same although we didnt hit the top speed as it wasn't safe to do with me standing over the rear wheel.
All those specific modification for the speed controller, Battery packs and the Battery holder really paid off as we managed to squeze alot of power from the battery packs, through the soeed controller into the brushless motor. We ended up with some preety good onroad specs for a bicycle conversion and using all these things from scrap and reconditioning them for our purpose doest cost us alot as compared to a specifically made kit avliable online. That brushless motor from the old hoverboard, that BLDC motor e-bike controller that we picked up from scrapyard and those customized lithium ion batteries all that costed us under the price of a conventional brushless motor for that conversion.
Guys vote us in the 3D printing contest if you think that all that customization using 3D-printer really worth thr hustle for mkaing such a neat and powerful bicycle conversion. Stay tuned for more DIY projects like this one by subscribing to our youtube channel.
https://www.youtube.com/channel/UCC4584D31N9RuQ-aE...
Consider supporting us on patreon:
https://www.patreon.com/DIYKing
Regards,
DIY King
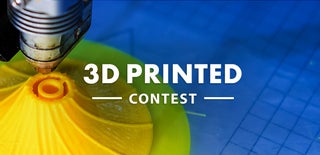
Participated in the
3D Printed Contest