Introduction: Custom Epoxy Scales for Victorinox
For several years my collection of Victorinox knifes has been growing. I like colorful models especially. Although there are many of them on the market, not all satisfy my aesthetic expectations. So I found a way to make my own linings by casting them from an epoxy resin. In this way my love for Victorinox is combined with the satisfaction of their appearance. And now I have a freedom to create one that looks exactly how I desire. Thin, tick, wit grippy pattern, mix of colors... and many more.
Step 1: Supplies
- Victorinox knife
It can be any Victorinox model you prefer or have. I'm using model called Spartan.
- Building blocks
Obwies choice here is Lego but any brand will do.
- Non-sulfur plasticine
Is a plasticine for using with silicones. Maybe you can do it wit any other plastic mass but I didn't try it yet.
- Epoxy resin
This one is very important, you want to chose Epoxy that has long curing time. Its because I'm using the technique witch does not require vacuum pomp. If you have one - great (just add degassing as one of step of the processes). But to the rest of readers I have tips how to get desired results without using vacuum.
If you want to dive a little bit deeper into the topic and find similar to mine here are my expoxy parameters:
CRYSTALLICALLY COLORLESS EPOXY
Viscosity (resin + hardener): 500 mPas
Mixing proportions resin: hardener 100: 50 (by volume)
Mixing ratio resin: hardener 100: 40 (by weight)
System density: 1.15 g / cm3
Gel time at 25 ° C: 50 min
Cure time 25 ° C: 16-24 h
Bending strength: 88 MPa
Deflection temperature under HDT load after heating: 94 ° C
Tipp: Epoxy is critical! If you choose wrong type you can have problem with the shrinkage of the casting. So ask the seller what procent of shrinking resin have and choose the one with lowest one.
- Epoxy dye/pigment
You have a lot of grate options to chose. I'm using powdered one with metallic shine in this project. But in the past I also experimented with liquid ones and even with makeup powders (in last photo in this instruction pink one is done that way). It was the gift for mother's Day since my mum wanted a pocket knife (more purse knife) with feminine look.
Tipp: Be patient and first experiment on a very small test cast to see if the color is good for your project.
- Mixing sticks
Good for mixing resins are ice cream sticks. But any other kind of tool will be good. Remember that when you working with resin you may not be able to use that mixing tool again. You will be using two of them, one for resin one for silicone.
- Mold release
I'm using the liquid waxy type. But any mold releaser will be good.
- Liquid silicone rubber
Soft to medium softness is proffered but any kind will do the job.
- Plastic rigid card
I'm using some shopping card.
- Glass pad/stiff pad (metal, plastic, ceramic)
I'm using a glass coaster. But every stiff, smooth, flat object will do. It is helpful in sculpting processes.
Step 2: Preparing Bottom Side of the Scales
You have to fill the empty spaces with plasticine. It seems to me that the more resin will be in the cast, the more solid it will be. I like to feel the weight of scales in my hand also. It's more premium feel.
- Carefully remove scales from the knife.
- Place the plasticine in the holes that we want to fill.
- Smooth surfaces using a plastic card and toothpick.
Tip: Do not let the plasticine stick out higher than the edge of the scales.
Step 3: Finishing Bottom Side of the Scales
- When you have everything smooth, place the scales on to Victorinox.
This replicates the shape of the rivets from the knife so you don't have to do it by eye.
- Next make the dents from the rivets a little dipper (just in case).
- Fill the tool channel with plasticine. But leave an empty place where the tool has a plastic head.
This will allow the channel to be maintained after casting.
Tip: The toothpick from Victorinox is perfect size for this tasks.
Step 4: Sculpting the Shape
This step requires the most patience.
- Apply an even layer of plasticine over the entire scales.
- Slowly add materials in places where it is not enough.
Smooth the model by rolling it on the glass pad. In my case it was a glass coaster. But all you need is a hard surface that can be easily maneuvered (small enough). A good replacement will be a book.
You should have a perfectly smooth model now.
Step 5: Making a Pattern
Many everyday items can be used for making a pattern.I found big spool of thin cord and I liked a sample.
- Test the pattern on small piece of plasticine.
- Transfer the pattern by pressing the item to plasticine.
- Make enough space for the scales tools (tweezers, toothpick). I remove excess material using a toothpick form Victorinox.
Tip: You can collect excess material with your finger, then you can be sure that the new scales shape will fit the shape of your hand.
Step 6: Making First Part of Two Part Mold
In this step I'm making first part of the mold. I'm short on my silicone supplies so I'm making everything I can to save as much as I can.
- Lay your scales on a flat surface. I use a piece of stiff paper arranged on the table. Make sure its perfectly flat.
- Then build a frame of Lego blocks. My frame is located close to the scales model in order to save a lot of silicone. You can be more generous with your mold volume. Additionally, put additional blocks in the corners to reduce the volume of the mold.
- Then mix the silicone according to the instructions on the packaging.
- When you have your mix its time to pour it into the mold.
- Control the flow of silicone so that the stream is narrow.
- Pour it in one corner and let the silicone spread out thru the mold.
Tip: If you want to be sure that your silicone will not drain out of the mold you can secure it using hot glue or plasticine. With Lego bricks it's not necessary.
Step 7: Finishing the First Half of the Mold
In this step you will make sure that you remove imperfections and additional plasticine.
- Use a toothpick to clean both scales tool channels (one for toothpick, one for tweezers).
- After the removal you should have empty tool channel. After you pour silicone in it it will create prefect mold of bottom side of the scales and you can use tweezers and toothpick.
- Clean any access of silicone by gently cutting it of with sharp blade.
Step 8: Preparation for the Second Part
Now to quick task you have to do before pouring second half of the mold.
- With sharp blade cut away some hols as shown in first photo. This holes will be acting as locking system for the form. I did four hols per mold.
- Put your mold release. My mold release must be applied with brush.
Tip: If you have cured silicone from molds you don't longer need you can cut it in small pieces and use is as filler in your new mold.
Step 9: Making Second Part of the Mold
- Build another layer of Lego to create frame for second part of the mold.
- Mix another batch of silicone and pour it top of first half.
Tip: If you leave a stick from the ice cream based on the wall of the vessel in which you mix, then you can easily remove the whole silicone that's left.
Step 10: Releasing the Mold
Now after silicone is cured you can release the mold from Lego bricks.
- Dismantle the Lego frame.
- Pull out your scales. As you can see, the pattern is as detailed as on the original model.
- Clean the edges of the mold. Any excess material can affect the final effect of the casting so don't miss this step! You want your mold as flat as it can get.
Step 11: Making Cast
This is the most important part of the project.
- Protect the surface on which you will put silicone molds (for example with cardboard). Epoxy resin may leak from the molds.
- Place your silicone molds on a flat, protected surface.
- Mix the epoxy resin according to the instructions.
I work with a resin that hardens for a long time, so I add a dye only after mixing.
Tip: After adding the dye, tap the container with the resin on the table top. This movement will allow bubbles to get to the surface.
- When you see no more bubbles pour resin into molds.
Tip: The level of resin should be slightly above the edges. In this way, when you close the mold part of the resin will flow out of the sides.
- When the resin is hardened, take out the castings.
- Mount new fancy scales onto your Victorinox.
Tip: If the scales have a little play you can glued them on to knife using few drops of epoxy.
Step 12: Joy of Results
I use the same technique to cast off a few other patterns. As you can see, all look great.The two middle patterns are the reflection of the metal mesh.
It's also a great conversation starter! Have fun creating your own designs.
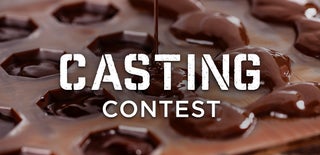
Runner Up in the
Casting Contest