Introduction: Custom Handmade Screwdriver
About half a year ago I purchased my first lathe - a Nova Midi Comet II - and quickly began working on beginner turning projects that could assist in developing some technique and also give some instant gratification by quickly churning out finished pieces. A great example of one of these projects is to extract the hardware out of a cheap plastic screwdriver and turn it into a one-of-a-kind tool by crafting your own unique handle. This saves some cash relative to the screwdriver wood turning kits available online, and turning tool handles is a fun, straightforward beginner project that gives you something you can regularly use in your shop. These can also be quick projects to give away as gifts during the holidays, as a custom made tool will be much more appreciatively received than a pre-assembled tool purchased right off of the store shelf.
So I made a trip to my local big box hardware store and picked up a few Husky screwdrivers for about $3 a piece. These are the multi-bit models that have a long shank which holds a double-sided bit on each end and locks into a sort of collet within the screwdriver body itself. I took them back to the shop and got to work.
Tools and materials needed for this project:
Lathe and Turning Tools
Inexpensive Multi-Bit Screwdriver
Table Saw
Disc Sander
Drill Bits
Calipers
Sandpaper
Wood Blank
Copper Coupling
Finishing Supplies
Epoxy or CA Glue
Step 1: Extract Hardware
The first step is to extract all of the hardware from the molded plastic body of the screwdriver. This is easily accomplished with a vise and a chisel, though I would recommend using a utilitarian chisel that you don't mind dulling the edge of. Once secured in a vise, you can quickly break away the surrounding plastic around the collet. Depending on the hardness of the plastic, this may send some small pieces flying, so be sure to wear safety goggles and take appropriate safety measures. It only took me a few whacks to release the hardware inside. Now on to the fun part.
Step 2: Prepare Your Handle Blank
There are many options of material that you can use to create a custom tool handle. I will be making four custom screwdriver handles with various materials that all have their own unique appearance, so the sky is the limit on your design and creativity. To get the blank ready for turning on the lathe, there are a few important steps that need to be taken, and some of these will be specific to the hardware you extracted from the cheap plastic screwdriver.
First off, select the material that you wish to use for the handle. Tropical hardwoods are a great choice as they offer unique colors and grain patterns, but you want to make sure that you are using a wood with a medium to high density for a tool handle that will get heavy use. For my blanks, I'll be using a piece of padauk, a chunk of spalted beech, a piece of ash that I'll torrify with a blowtorch after turning, and a some fancy acrylic square stock.
You want to make sure that your blank is at least 6" long (something closer to 8-10" will give you more material to work with on the lathe, even if the final handle ends up being half of this length), and needs to be somewhere in the neighborhood of 2" thick. When turning on the lathe, having a blank that is the same size in its width and thickness will save time and result in an easier cut with less chance of tear out. So I ripped all of my blanks to 6-8" long and about 2" square.
Next, we need to square the two ends of the blank. This can be accomplished a variety of ways (miter saw, crosscutting on a table saw, disc sander) but having perfectly square and parallel ends is crucial in helping to mount the blank in the chuck and to drill a straight hole into the blank. After squaring the ends, we need to find the approximate center point on the two ends of the blank. On a square blank, simply use a straight edge to connect opposite corners of the ends, and the intersection of these lines will be your center point. If you're using a round blank, do your best to draw a few lines across the diameter of the ends and these approximate intersection points will be close to your center point. If you're using a particularly hard wood or an acrylic blank for your handle, now is a good time to round over the corners of your blank on the disc sander. This will reduce the likelihood of catastrophic tear out when you begin turning it into round on the lathe.
In order to mount the hardware inside the handle, we'll have to drill a couple of holes to accommodate the size of the hardware. This is a step that will vary depending on what sort of screwdriver hardware you acquired. For me, I have to drill two holes for each part of the hardware set: the collet, and the shank that holds the bits. Drilling these holes can be accomplished on a drill press, but I find the easiest method is to mount the blank in the lathe chuck and use a drill chuck in the tail stock to recess the holes (you must have perfectly square and parallel ends to use this method). This allows you to ensure that your mounting holes are in the exact same plane that your final piece will be turned to, guaranteeing that the screwdriver shank will be perfectly perpendicular to the finished handle.
So I first used a 5/8" forstner bit to recess a 1 1/4" deep hole, and then swapped this out for a 1/2" drill bit and drilled this to 3 3/4" deep. Again, these exact hole diameters and depths will likely change slightly depending on your hardware. Make sure that you test drill a hole for the collet on a piece of scrap wood. You want this fit to be tight but not excessively so - too loose and it will be tough for the adhesive to hold the hardware in place, but too tight and you'll be trying to hammer an epoxy covered collet into a hole on your finished handle.
Step 3: Make the Ferrule
Ferrules are an important part of wooden tool handles. Aside from offering a decorative element, these improve the strength of the handle and reduce the chance of the wood splitting if the tool is put into heavy use or dropped on the floor. While you can buy premade ferrules online, it's easy to make your own in only a few minutes.
I find the best material for handle ferrules is copper pipe. Copper is easy to cut, doesn't require any special tools, and allows for several decorative options. I picked up a few 1" wide, 2" long copper couplings from the hardware store and these offered enough material to make several ferrules. I usually look to make my ferrules between 1/2' and 1" long, depending on the look I'm going for. So once you've figured out the length you desire, place the copper piece in a vise and use a hacksaw to cut it to size. Begin by taking a few light passes on the copper tube to strike a line, and and then begin cutting down. Remember, hacksaws are designed to be a two-handed tool - using only one hand makes it difficult to get a straight, controlled cut. Only light pressure is needed to cut through the copper tube, so focus on keeping your cut as straight as possible.
Once the desired length of copper tube has been cut off, I like to take it to the disc sander to clean up and square the cut end. Copper is very thermally conductive, meaning that it can heat up very quickly. Use a pair of pliers to hold the ferrule while you press it into the disc sander. Very light touches will remove a good amount of material, and holding the copper against the abrasive cutting wheel for too long can produce so much heat that it can actually alter the color of the copper (more on that later...), so go at it easily until you're happy with the shape and finish. (NOTE: if you have a jagged edge even after hitting it on the disc sander, a deburring tool can quickly clean up the edge so that it's nice and smooth to the touch.)
Step 4: Initial Turning
There are two solid options for how to turn your blanks on the lathe: turning between centers, or turning in a chuck. With a project this small, you will have no issues turning your blank between centers. To do this, take your spur center out of the lathe and place it on the center point on one end, hammering down with a dead blow mallet to seat the spurs (if you're paying attention to grain direction in your handle, the spur center side will be the butt end of your handle). After remounting this on the lathe, you can line up the live center on your tail stock and do your best to place this right in the center point of the hole that you drilled for the hardware. (NOTE: it can be difficult to seat the live center perfectly in the hardware hole, and if you're off by just a couple of millimeters you will end up turning a handle that is not perfectly perpendicular to the holes you drilled, which results in the screwdriver shank coming out of the handle at an angle. This is one of the reasons I prefer drilling and turning in the chuck). Since I elected to mount the blank in the chuck and recess my holes with a drill chuck, I swapped in the live center on the tail stock and after tightening down, I'm ready to roll.
I'll be using carbide insert turning tools on this project, as they are a quick and easy way to rough out and detail small pieces on the lathe. I begin with a roughing tool to quickly turn the blank into round. I usually start initially at a slower speed (400-500 RPMs) to avoid getting too much tear out on the corners. Another option here is to remove the corners of the blank on the bandsaw, disc sander, or a hand plane to get the piece approximately round. One way to determine how round your blank is without turning the lathe off repeatedly is to lightly rest the arm of your cutting tool on top of the blank while it's spinning. A perfectly round blank will let the tool ride smoothly on the top of the piece, while something that isn't quite round yet will produce a lot of chatter. (NOTE: when turning acrylic blanks, you need to have the lathe speed turned up much higher - in the neighborhood of 2500 RPMs. Otherwise it can be very easily to get a ton of chip out.)
Once your blank is round, it's time to cut the tenon for your ferrule. While it's best to shoot for cutting a tenon that is the exact length of your ferrule, it's better to have a slightly longer tenon than a shorter one. You can always sand this down to size at the disc sander after assembly, if needed. Holding the ferrule so that it's lined up flush with the tail stock end of my blank, I use a pencil to scribe a small line where the end of the ferrule is. Then I place the pencil right on that line and manually turn the lathe spindle to transfer this mark to the entire blank. I use either digital calipers or a manual inside caliper to get the exact diameter of the inside of the ferrule, and then take this to the lathe.
Using a parting tool or square carbide insert cutter, I begin bringing the tenon down to size right up to the line I just drew. It's VERY easy to cut the tenon down too small, so stop to regularly check your tenon against the calipers. Once you're almost there (we're talking at most a millimeter larger than the inside diameter of the ferrule), stop there. Again, it's better to have an ever-so-slightly thicker tenon than one too thin.
Turning the shape of the handle is all about feel. Having a handle that's too thick can make it difficult to grip properly, but too thin can mean that it wont feel beefy enough to put a lot of pressure into. Curves are always a nice detail to impart, but improperly placed ones will make the handle feel uncomfortable in your hand. I recommend taking a moment to grab some small hand tools sitting around your shop (other screwdrivers, chisels, handsaws, etc) and see which ones feel the most comfortable in both their size and shape.
One of the great things about turning is that you don't really know what the final shape of your handle will be until you start cutting. The finished piece is hiding somewhere inside that chunk of wood. It's up to you to find it. Using your preferred cutting tool, remove material slowly and consider both the aesthetic and tactile shape as you turn your curves.
Step 5: Final Turning and Sanding
As you approach your finished shape, you want to determine how long the handle will end up being. Stop the lathe as you come to a shape you like, and grip the piece on the lathe. Make sure that you're pleased with the feel and comfort of the handle, and determine where you would like the butt of the handle to be. I find that I like my handles to extend around a half of an inch past where my palm grips it. Use a pencil to strike a line while manually spinning the spindle to encircle the blank with this mark. Using a parting tool, bring down the diameter of the waste wood behind this mark to a small cylinder - something less than an inch. A round carbide cutter is great for removing material on both sides of this area, rounding over the butt of the handle as much as possible.
With your handle shaped and approximately brought down to length, ramp up the speed of your lathe and use a scraper or square radius cutting tool to shear off material very slightly, trying to make one pass across the length of the handle. This should give you a very fine surface free of tool marks and small imperfections. Now it's time to grab your 100 grit cutting tool (aka sandpaper) and begin easing the surface to a super smooth finish. I like to use a scotch brite pad with sandpaper wrapped around it to sand my pieces progressively through the grits. This gives you a cushion to press into your piece while preventing your fingers from getting too hot through the sandpaper. Work through the grits quickly (100/150/180/220/320) and flip between forward and reverse mode (if your lathe has this) to make sure that the grain is evenly removed in both directions. One consideration toward the end of this process is what sort of finish you're going to be using. If you prefer water-based finishes, it's important to lightly wet the piece before you sand at 180-220 grit to raise the grain. Not doing so will result in a rough-feeling surface once you've applied your finish. This isn't as much of a consideration when using oil-based finishes.
Step 6: Final Shaping and Finish
With the turning and sanding steps done, you can now remove the piece from the lathe. You will likely have a candlestick-looking piece similar to the one above. In order to release the waste wood from the butt end of handle, use a bandsaw or handsaw to carefully cut away the little spindle on the bottom of the handle. You now have a rough unfinished butt end that needs to be addressed. I like to use a disc sander to very lightly shape the butt into a round surface that follows the bottom contours of the handle. Then, using the same grits that you did on the lathe, hand sand this surface going gradually higher up onto the handle at each grit. The finished product should be evenly smooth and feel great in your hand throughout the length of the piece.
In order to prep the handle for finish, take a shop towel or rag lightly wet with mineral spirits and rub the handle down. This will remove any surface dust from the sanding process, and will give you a chance to examine the surface to ensure that there are no unseemly tool or sanding marks that you may have overlooked previously. Address any if needed.
For finish, you have a TON of options. Do you want to feel the wood grain in the final piece, or have a super smooth, hardened surface that looks like glass? Do you prefer a satin finish, or something glossier and shiny? How much protection do you want the handle to have, as opposed to having a finish that's easily repairable? My go-to finish for almost all things woodworking is Arm-R-Seal from General Finishes. It really highlights the color of the wood, serves as a highly protective and highly glossy film, is easy to apply and feels great to the touch. But your options include lacquer, natural oils (danish, walnut or tung oils), an oil/wax mixture, or even CA glue if you want to finish your handle super quickly. Regardless of your desired choice, do your best to avoid getting any finish on the outer diameter of the tenon or the inside of your hardware hole. This will make it more difficult to install your hardware. For a tool that will get handled quite a bit, it's a good idea to do at least three coats of your desired finish to give it as much protection as possible, sanding lightly with 400-600 grit sandpaper in between coats.
Lastly, you need to decide what (if anything) to do with your copper ferrule. A natural, untouched copper ferrule can go great with your handle, but there are a few options you can explore to give your ferrule a more artistic look. In the examples that I've made for this Instructable, I created three distinctly different ferrules to help you see what some options look like (the acrylic handle didn't receive a ferrule). For my padauk handle, I left the copper unfinished, which produces a very clean and sleek appearance that matches the tropical hardwood. For my spalted beech handle, I used a flat black spray-on paint/primer that helps attract the eye to the dark spalting lines in the wood. And for the torrified ash handle, I used a blow torch to heat the copper to a high temperature, resulting in a striking mixture of color. These are only a few options you can choose from, but you can see that there are many directions you can go that help to highlight and compliment the appearance of your handle.
Step 7: Assemble Hardware
Now that you have a beautiful and functional wooden handle all finished, it seems like the perfect time to goop it up with a bunch of epoxy! I dread this step because it's so easy to mess up a piece that has taken a lot of time to create, but with some careful attention to detail, this step is pretty straight forward. First, lets talk about adhesives. My go-to adhesive for almost every project is epoxy, as it is void filling and will never come off... But you can use CA glue (aka super glue) if you don't have epoxy sitting around - this process can just be a little messier and doesn't give you as much working time to get everything perfect.
For both pieces of hardware, it's important to scuff up the face that will be glued to the handle with sandpaper to give a better surface for your adhesive to bond to. Prep your epoxy or CA glue and have some wet shop towels on hand. I began with the collet so that I could leave it in place while attaching the ferrule. Based on the diameter hole I drilled to insert this, it's pretty friction fit and doesn't need much epoxy. After spreading a small amount of epoxy on the interior edge of the hardware hole, I slid in the collet and pressed it against my workbench to ensure that it's perfectly flat with the end of the handle.
For the ferrule, it's important not to apply any epoxy to the area that's between 1/8"-1/4" from the handle end of the tenon. This will help avoid having to deal with any squeeze out on the handle end. Slide the ferrule onto the tenon, rotating it to spread the adhesive around evenly. Once it's fully seated, now is the time to wipe away any squeeze out with your wet shop towel. Find a way to hold your handle upright while this dries. I find a small quick clamp gripping the butt end of the handle is a great way to hold the piece upright sitting on the workbench.
Step 8: Finishing Thoughts
Assuming your glue up went smoothly, you're done! If you're going for a super shiny look, you can take the handle to a buffing wheel and polish up the surface to bring out the sheen in both the handle and the ferrule.
These instant gratification projects are a blast. I made each of these screwdrivers on separate days, and it took me less than an hour between grabbing my blank off the scrap wood pile and putting on the first coat of finish. When there are lots of long-term projects going on in the shop, sometimes it's nice to bang out a quick one from time to time. Now the only hard part is to decide whether to display these all in my shop, or whether I like anyone enough to give these away as gifts!
If you enjoyed this Instructable, please give it a vote on the Build A Tool contest! For more of our projects, check us out on IG @Resourced_Woodworking, and let us know if you have any questions or suggestions in the comments section below.
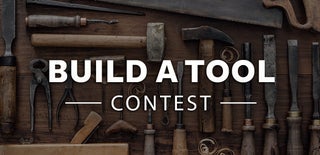
Participated in the
Build a Tool Contest