Introduction: Custom Live Edge Table
Bring the outdoors, indoors with a custom live edge table, a flat-cut tree slab with glossy black, welded steel legs.
This cherry wood table showcases the tree's natural grain, and the live edge gives it a rustic and unfinished look. This adds some nice character to the table, too. The legs are welded steel with a glossy black paint, further enhancing the natural feel of the table.
After months of looking for the right piece of wood, with just the right amount of bark left on (I'm very particular), I then sanded it to a smooth finish before coating the entire slab with a mirror-finish polyurethane. I managed to get this piece of scrap wood from a local furniture maker.
Follow along and I'll show you how I transformed a large slab of wood into an eye-catching "woodsman" table.
Step 1: Needed Stuff
Materials
Your Choice of Wood (I used cherry)
12ft of 1" Hollow Tube Steel (2x 6' Pieces)
4 Screws of Determined Length (See step 6)
Sandpaper (I used 80, 120, 220, and 400 grit)
Tack Cloth
High-Gloss Polyurethane (a clear resin could also be used)
Glossy Black Rustoleum Spray Paint
Flux Coated Bronze Welding Rods
4” Foam Brush
Tools
Miter Saw with Metal Cutting Blade
Angle Grinder with Metal Grinding Wheel
Bench Grinder (Coarse and Fine Discs)
Palm Sander (I used 2 sanders - Random Orbital and Palm Sander)
Welder and Accessories (see step 5)
Drill and Correct Bits
Various Files
Square
Tape Measure
Step 2: Sanding
I was able to get this nice piece of cherry wood from a local furniture maker as scrap from a previous project. It was in great shape and actually it was very smooth, but it did have a couple of pencil marks and a thin coating of wax on the top and bottom, to protect it during shipping. If you can avoid cutting the slab, that's great. Cutting it isn't needed and it takes away from the character and natural look of the table. My table is 23” long, 12” wide and 2” thick and it is the perfect size for a table.
I started with 80 grit sandpaper on the parts that had wax, using the random orbital sander.Using the same sander, I moved up to 120 grit on all sides. While still on the 120, I rounded all the edges, except for the live edge area. To finish it off and make it totally smooth, I used 220 and then 400 grit on the palm sander.
Before coating the wood with polyurethane, use the tack cloth to remove the micro fine dust. Open up the cloth and ball it up to expose the sticky part of the cloth. Quickly wipe the cloth over all surfaces, except for the bark. If you stay in one spot for too long or press down too hard, it will leave sticky residue on the wood slab. Use compressed air to remove dust from the bark. Now it's ready for finishing!
Step 3: Finishing
Applying a heavy amount of high gloss polyurethane to the wood slab makes for a mirror finish coating. It also brings out all the beautiful grain, bark and character. I did about 7 coats on the wood and 3 on the bark.
Start by setting up the work area. I slid 2 pieces of scrap wood under the slab to elevate it just a little. Drape an old cloth over the scrap wood, to protect the wood. When working with polyurethane, the trick is not to overwork it. Dip the foam brush in the polyurethane and get a good amount on it. Work from the top of the slab, down. Brush it on, and go back to it smooth out. That's it! You don't need to (and shouldn't) spread it around and keep messing with it.
Each time you add a coat use 400 grit sandpaper to roughen the surface, followed by the tack cloth. This should be done by hand. I finished the top and all sides first, and then did the bottom, which doesn't need as many coats.
When working on the bark, use the foam brush to dab on the polyurethane. Make sure to work it into all the cavities in the bark. If there are any white spots (not clear), use a rag to remove the excess. I did about 3 coats without sanding in between. While you're waiting for the polyurethane to dry, try the next few steps!
Step 4: Cut Steel
Before doing anything, there is always prep work (and post work). We're going to be cutting all our steel at 45° angles, so now is a great time to calibrate your miter saw. Install a general purpose metal cutting blade on the saw. Do not hook up a vacuum or dust collector - the sparks can catch it on fire! Wait! You're not ready to start the prep work yet. Study the diagrams, pictures and the lengths to cut below, so you understand what to cut. Measure the steel and use the awl to score the cut mark. Clamp the steel onto the saw and let ‘er rip! Pick up the steel with pliers and plunge it in a bucket of water.
Dimensions:
6' Bar (72”)
3x 20" (Legs)
1x 12" (Floor Base)
Other 6' Bar (still 72”)
1x 20" (Legs)
2x 18" (Tabletop Base)
1x 12” (Floor Base)
When cutting, it is a good idea to test fit and visualize how the pieces will be assembled. Labeling the joints with corresponding letters will make welding easier. After cutting every piece, use the bench grinder (moving from coarse to fine) to smooth out the sharp edges. Use the files to smooth out the inside edges. Be careful not to take too much steel off or round over the edges a lot. Big gaps between the pieces will not weld.
Step 5: Weld the Legs
You can use any type of welder for this project - MIG, TIG, Arc, or gas torches such as an oxy-acetylene torch. I used a super affordable oxy-mapp gas torch. Gas welding is a lot like soldering - heat it up and feed in the welding rod. If you decide to use this torch, remember to buy plenty of extra oxygen bottles - it runs out quickly because it is compressed. You will also need flux coated bronze welding rods, which I purchased from Lincoln Electric. I used this welding technique so everyone could build this project without investing truck loads of money in new tools.
I decided to set up my welding rig using metal C-clamps, bricks, and push clamps, to keep with the theme of anyone can make it! Lay a large brick on the surface you're welding on - this is the work area. Position the joint to be welded on the brick and use other bricks and clamps to secure it in place. Use the pictures for an idea of how to set it up. After positioning the joint, use the square to make sure it is at a 90° angle. Adjust if needed.
Follow the instructions with your welder and get started, using the pictures to guide you. I was able to do 2 sides of the joint at once. Then unclamp it and turn it over to do the remaining sides. Now, carefully plunge it in a bucket of water to cool it down.
Weld In This Order:
Attach Legs to Table Bases (after this, you will have 2 “U” shaped bars)
Add Floor Base to Legs Done!
Now I could lie to you and tell you the welding was totally easy when it really wasn't, but I'm not going to do that. The last weld I made was unfortunately about a ¼” away from being square. All you have to do use a clamp to sandwich it together while you're welding. The unlevel tabletop you'll have later can be fixed with some felt or rubber feet.
Step 6: Finish the Legs
Now it's time to add that glossy black color to the steel, which gives the look of a high-end piece of furniture purchased from the furniture store. Start by grinding down the gold-colored material, using the angle grinder, until the joint is flush with the rest of the steel. Round over the sharp edges like we did with the tabletop. Repeat this for the rest of the joints.
After smoothing the joints, flip over the tabletop so you're looking at the bottom where the legs will attach. Position the legs how you would like them, using the tape measure to center it. Now is a good time to select the screws you will be using. I used shorter wood screws in the front, because of the live edge, and longer ones in the back. Use the drill and a metalworking drill bit (correct size for the screws you chose) to drill through the steel bars. It is important to keep the drill very straight.
Bring the frame outside and place it on a scrap piece of wood. Start spray painting the piece, being careful not to apply so much that it drips. If this does happen, use 220 grit sandpaper to make that area flat again, by hand. I did about 3 coats to get it glossy-looking. Let it dry overnight.
Step 7: Assemble Table
After the table is completely dry and doesn't feel tacky, it's time to finish the table. Orient the legs so they're how you want them on the table. Stick a nail through the holes and use a hammer to mark where the hole should be drilled in the wood. Using the tape measure, determine how deep the pilot hole needs to be for each of the screws. Remove the metal frame and set aside. Using the appropriately sized drill bit, drill the pilot holes right where the nail made a mark on the wood slab.
Position the frame on the slab how you would like it. Start by screwing in the back screws, leaving them a little above the metal surface for wiggle room. Screw in the front screws and tighten. Now tighten up the back screws.
Right the table and place it where on the ground. If it is not level, you can add sticky felt pads to the legs. And you're done!
Step 8: Use Table
The custom live edge table is now complete. Now it's time to find an awesome spot for it, wherever you may be. Whether you're in a rustic cabin, or in your home, this custom table will always be both stylish and functional. Step back and take in the beauty of all your hard work!
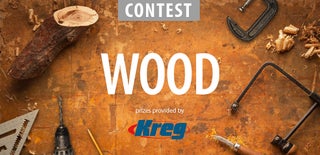
Participated in the
Wood Contest 2016
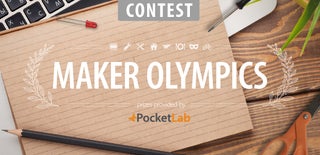
Participated in the
Maker Olympics Contest 2016
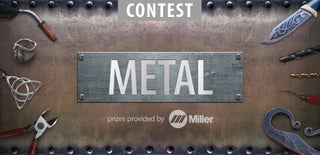
Participated in the
Metal Contest 2016