Introduction: Custom-made Keg Cooler for Camping!!
First of all, thank you for checking out my Instructable!! I've created it as an entry into the Make a Box contest sponsored by Rockler! If you like this Instructable, PLEASE VOTE FOR ME!! I'd love to win this contest!
Last year, just a few days prior to going up North to go camping, I decided to make a custom cooler that can withstand rough conditions and keep beer cold for extended periods of time!
The pics shown on this step are of the final product before and after hauling it up to the camp site! Check out the rest of the Instructable for step-by-step details on how I put this thing together!
Step 1: Make a Plan!
As it turned out, I had some Oriented strand board (OSB) laying around from another project that ought to work perfect for this!
My plan was to make a dual-compartment cooler that will be ideal for transporting a keg long distances over rough terrain in the scorching heat of summer and have it insulated enough to keep the beer ice-cold for days! Easy-peasy, right?!
Furthermore, I wanted to be able to transport it on the luggage rack I have for the trailer hitch of my vehicle, so I knew the approximate size that I needed to make it.
Step 2: Materials!
So, this is a rough list of the stuff I used to get the job done, most of which was laying around in my garage already. I think the only thing that I actually had to purchase was the paint/sealer and the handles! Not bad, eh?
1 sheet of 3/4 inch OSB
1 sheet of 1/2 inch foam-core Gatorboard (used for spray-mounting posters)
1 tube of Liquid Nails construction adhesive
2 cans of clear FlexSeal silicon sealant
3 - 4 cans of really cheap white spray paint (~$1.00 @ HD)
8 rugged handles for carrying this monster like pallbearers -- fully loaded w/ ice and beer, this thing is HEAVY!
You'll also need various tools such as:
Drill & drill bits/screws/etc
Clamps for holding things together while the glue sets
Circular Saw
Saw-horses for painting off the ground
Measuring Tape
Razor blade for cutting the foam-core board
Step 3: Get to It!
Grab your measuring tape and make sure you leave a few inches of room on all sides of the keg to allow space for the foam-core board to be inserted with leftover room for ice!
Using an empty keg as your guide, measure and make a division in the box that will separate it into two sections: one for the ice, the other for the keg!
Sorry that I didn't have more pics of the process of doing this, but it was really just a matter of marking a line and ripping the board where necessary w/ the circular saw!
Step 4: Screw It!
Once you've measured and cut all of the boards to assemble the box, grab a friend and have them help you hold them as you screw them all together!
As you may notice, I've made inner lids for each of the two sides that will fit within each compartment. You may be wondering why!
Well, here's how this box is going to work! The larger of the two compartments is for the keg, but only while it is being transported from one location to another. The smaller of the two compartments will hold all of the dry and wet ice during transportation. Upon arrival at the location where the keg will be tapped, it will then be placed vertically in the smaller of the two compartments and surrounded by as much ice will fit, then the rest of the ice will be stored in the larger of the two compartments until needed. The additional insulated lids will rest right on top of the ice within the compartment, thereby eliminating the air space allowing the wet ice to be kept cold by the dry ice longer than it would otherwise be able to! The larger chamber will only be opened when it is necessary to replenish the ice that goes around the keg to keep it cold! Nifty, huh?!
Step 5: Insulate It!
Now, I used 1/2 inch foam-core Gatorboard that had been leftover as cut-off scraps from work. You can use any other insulation board including the stuff that is used to insulate houses and buildings. You want it to be tough and insulative, but beyond that, there are no other requirements!
I carefully measured and cut out the pieces that I needed to line the entire inside of the cooler. Be careful in making your measurements and cuts because you're likely working w/ a finite amount of material and there's no undoing mistakes when cutting foam-core!
Step 6: Glue It!
Grab your caulk gun and get to gluing the foam-core in place w/ the Liquid Nails construction adhesive! Make sure that you've dry-fitted all of your pieces together and know where each goes before you start gluing things in place. I used the clamps and weights to apply pressure to make sure that the pieces stuck well to the boards. I left them over night to set up well and these are the pics of the results!
Step 7: Paint It!
At this point, it's time for paint! I went with white, which, in retrospect, was a poor choice bec it shows every bit of dirt and mud that gets on it. I might someday repaint it to more closely match the dark blue exterior of my vehicle!
Step 8: Seal It!
We've all see the commercial w/ the guy w/ the screen door on the bottom of a row boat, right?! Go get yourself some of this stuff and spray the entire inside of the cooler using thin, even coats. Repeat as many times as you have material left that allows you to do so! The point is to waterproof the foam-core boards as much as possible to prevent them from becoming waterlogged and ruined faster than they would otherwise be!
Note: It's hard to tell that the box has several layers of FlexSeal on it because, well, it's clear! You'll just have to take my word for it! Let this stuff cure for at least 24 hrs before you attempt to get it wet!
Now would also be a good time to secure the handles to the sides of the unit! I got handles very similar to the one in the pic shown here from the Home Depot for $4 each x 6 handles = ~$30 after tax. This was by-far one of the most expensive components of this build! However, I definitely wanted tough, ergonomic handles because the weight of the cooler plus a keg and ice is nearly pounds! 160 lbs keg + 90 lbs Ice + 50 lbs cooler = 300 lbs total! You'll want to get handles that are big enough for large hands to haul comfortably, so don't get cheap and buy small ones!
Step 9: Get Loaded!
Ok, so in my haste to get this cooler packed up so we could get on the road headed toward the camp site, I neglected to take pics of it full of ice and beer! Schwoops! My bad! :)
As you can see here, I've got my new custom-made cooler strapped really well to the back of my Traverse! Inside of the larger compartment resides the keg packed in as much ice as would fit around it (which was quite a bit actually!). In the smaller section is 4 x 22lb bags of (wet/normal) ice plus another 10+ lbs of dry ice (to keep the wet ice frozen longer!). This was enough ice to get us through a 4 night/5 day camping trip with ice-cold beer on 90 degree days!
Unfortunately, I hadn't had the presence of mind to take pics of this thing all set-up and in-action! My mind was on... other things... when we arrived at the camp site, so I failed to get good pictures of it. The custom cooler can be seen here in the one pic I did find of a few of my buddies sitting around giving me the bird when I decided to take pics! As you can (barely) see, the keg is now upright in the smaller section and the ice is sealed into the larger one! We kept the keg buried in the ice we'd brought for it and covered it all w/ a wet towel to keep it cold.
I cannot stress how well this rig worked at keeping my beer cold! There had been enough room in the larger compartment upon arrival to throw in the ice that other people had brought up to the site too, which basically made this thing into a deep freezer!
I really hope you liked my Instructable on how to build your own custom-made cooler! I would love to see what you guys build based on my Instructable, so please post pics in the comments if you build one!
Also, please don't forget to VOTE FOR ME to win the Build A Box Contest! I would greatly appreciate it!!! :)
Cheers!
Steve
HelluvaCook.com
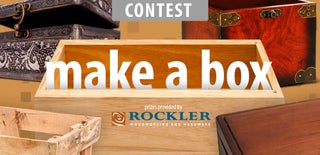
Participated in the
Make a Box Contest
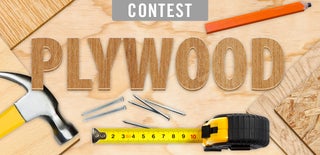
Participated in the
Plywood Contest