Introduction: Customizable 3D Printed Wallet !!!
My wallet never stops growing. I am sure that many readers will also find that their leather wallet has grown over the years with membership cards, loose change, bus passes, or anything else that finds its way inside. My wallet troubles led me to start browsing for new options. This is where I found some pretty cool designs, but I didn’t want to drop $30 for a new wallet. However, this inspired me to make a customizable 3D printed wallet. Not only does it have the minimalist function desired, but you can also customize colors with filaments and add your own designs on the front for no extra charge.
This project will be fairly easy as long as you have a 3D printer and some sewing experience.
Supplies
Fusion 360 (or any other software that you find to work)
3D Printer and Filament (obviously)
3/4" Polyester Elastic Bands
Needle and Thread
Glue (Super Glue or Hot Glue)
Dye (Optional)
Step 1: Designing
The coolest thing about this project for me is the wide range of customizability the wallet has. I linked the file of my design so that you can use it to add your own designs. For the logo, you can find .svg files that you like on the internet and put them on the front of the wallet.
To add your custom design to your wallet, you first want to download a .svg file to your desktop. Go to Fusion 360 and open up the linked design. Select "Create Sketch" and select the empty face. Near the upper right of the screen, you should see the word "Insert". Click that and select " Insert SVG". Click the small file icon next to the words "Select SVG File" From there find your .svg file and it should come up. Then you use the prompted icons to scale, move, and rotate your logo to where you want it on the wallet. Select "OK", then "Finish Sketch". Select the "Extrude" option. Select all the lettering and symbols you want on the wallet and select "Cut" under the "Operation" tab. Finally, fill in the "Distance" box with -0.05 in. Push "OK" and you will have your own design imprinted on the wallet!
Also, for anyone who wants to print out a wallet who don't have Fusion 360, I have linked an stl file to a blank wallet, where you can hopefully export it to whatever file you want and modify it to your liking.
After this is done, you can start messing around with colors in Fusion 360. Go to the "Modify" tab and select "Appearance".You can now choose your colors. I found that the plastic colors work the best. Once you have the right colors planned out, make sure you have the correct colored filament.
A quick side note. The color of your elastic band will also come into play. I bought mine from a sewing store, but as I browsed online stores I noticed that they are only sold in black and white. If you want to have another color, I would recommend buying white and dying it to the appropriate color.
Step 2: Printing
Before exporting your files as STLs, you might have to change the units of your wallet. Don't worry. It is a lot easier than it sounds!
In the left hand corner, you should see your Part Browser. From there, go to "Document Settings" and select "Change Active Units". Under the "Unit Type" drop down menu, select Millimeter and push OK.
You can now select "File" - "Export"- "STL Files".
Now for supports.
Most of the pieces can be easily oriented without needing any supports. If the front of your wallet needs support, I recommend printing with the design up. Most of my designs were able to be bridged with the printer.
The only other piece that needs to be supported is the money clip. I printed it in the orientation shown above.
I used 10% infills on all the parts except the money clip, which I used 20%.
Step 3: Assembly: Sewing
The first thing you want to do once you have all your parts is measure out all the elastic you need. Because each elastic is different and sewing abilities may differ, you will have to measure what you need by your own judgement. You will need two separate pieces. One will be longer to loop around the 2 inner pieces. The other will be shorter and be sewn to the first and looped along the bottom of the two inner pieces. Some tips that can help you get the right length are:
1) Start with a measurement of 5" and 4"
2) If you are an experienced sewer, stay at 5" and 4", and make as small of an overlap as possible.
3) If you need extra elastic, do so, but don't go above 5 1/4" and 4 1/4" (You still want it stretchy(: )
After you have your elastic, and you have checked that they will fit and hold together your wallet, you can start sewing. Take the longer piece (5") and sew it into a loop. Try to get the smallest overlap as possible. Next, take the shorter piece (4") and sew it perpendicularly to the first loop. This next take the open side of the second piece and loop it up and sew it DIRECTLY across from the first side. After you're done, you should have a diaper for a rat.
Step 4: Assembly: Glue!
Many different glues can be used to bring this project together, but I would recommend super glue or hot glue. Personally, I used super glue, but anything that is instant bonding and incredibly durable should be fine.
Note: Before you start gluing, put your parts together and make sure they fit. If the elastic is pushing the pieces out of place, sand the T-shape in the outside covers, and you should be fine.
First, you want to get one of your two identical inner pieces and put the elastic on it like shown above. Put glue on the inside surface (except the T-Shape) of your custom design outer cover. Also put one drop of glue in the center of the elastic. Line up the two parts and press them together, making sure all the edges are flush and the elastic is in the T-shape. Let dry.
Next, slide in the second inner piece into the elastic making sure that the the thumb holes are oriented correctly. Repeat the process in the paragraph above, but make sure the clip hole is facing the same way as the finger holes are.
Finally, put some glue on the bottom surface of the clip and slide it into the clip slot. Make sure that it bonds to the other plastic.
And just like that you have created your custom 3D Printed Wallet!!!
Step 5: Innovation and Improvements
The most important part of manufacturing is innovation. Without innovation, we would live in a completely different world. This is why whenever I finish a project, I take a step back and look at what I could have done better. A couple things that I noticed that can help you at home are:
1) Plan for overlaps in sewing
2) Lower T-Shape indents for better grasp on cards
3) Make larger thumb holes
4) Sanding and Painting is never a bad idea
I would love to hear feedback on ideas to make this project better! Criticism is the start of progress.
Keep Creating!
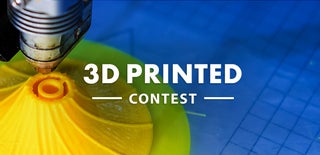
Participated in the
3D Printed Contest