Introduction: Customized Lithium Battery Packs for E-Bike
We recently converted our bicycle into an e-bike using brushless outrunner motor from hoverboard, and that thing have crazy amount of power. But that crazy power drains the hobby grade lithium pollymer batteries like crazy fast. As we have been previously using two 5.2 Ah 11.1v battery packs that offered a total capacity of nearly 110 watts hour. With this capacity we can barely go beyond 4km of range with heavy foot over throttle.
Now we can get more fortunate as during this whole situation we came across an old lithium ion battery pack during our visit to scrap yard and we suspected the battery to be still alive.
Now this instructable is your guide to design and built a customized lithium ion battery pack for your electric bike totally out of scratch and scrap.
Hang in there as we are going to built 600 watts hour battery pack thats going to give us a 20-25 km range on our electric bike and all that within 20 USD. So time to get hands dirty...
Supplies
As always you dont require a particular set of tools for this project but having following can get the job done as discribed:
- Soldering iron
- Sucker gun
- Soldering wire
- Knife cutter
- Multimeter
- A DC watt meter
- A nichrome heating filament to act as a load
- A 3d printer
The material required for this project are:
- A source of lithium ion cells, to name a few it could be an old electric bike or a laptop.
- Printing filament
- Epoxy
- XT-60 connectors
- A BMS (Battery Managment System)
If i miss anything here put it down in the comments below.
Step 1: Sourcing Used Lithium Ion Cells
Without any doubts, lithium ion batteries offers great specifications and the benifits such as the weight/volume saving, crazy discharge rate are a few to name here. But all that come at a hefty price specially if you are aiming to get a battery pack for you electric vehicle as you are aiming for above 100 wattshour (Wh) obviously and there the price starts to add up alot.
So, one way is built your own lithium ion battery pack using cells from old battery packs from sources such as a damaged electric bike or a laptop(although they dont offer high discharge cells) while totally customizing the battery pack to fit perfectly within your vehicle.
For this project we found an old battery pack from a rejected lot of electric scooters from an old scrap yard. Now lithium battery packs from used sources can be a good deal with a considerable amount of capacity still left in them if you are going to consider the following things:
- In case of soft pouch lithium ion battery as this one, the physical condition matters alot. The battery must be in good shape with no major dents and definately no puntuchered. Besides, if the battery pack is swelled it means that the cells are puffed up due to over charge or over discharge. So be carefull not to pick up a pack thats balloned but you can go for the one that offers multiple cells and a few of which are swelled as you might end up getting the rest of them working perfectly fine.
- Generally lithium ion cells are in good working condition if they are holding a potential above 3v as the onces below that level are usually puffed up and are supposed to be inside the bin(Should be recycled properly) and definately not over the workbench.
- Check the overall voltage of the battery pack if the individual cell voltage can't be measured. Divide the total voltage to the number of cells that battery has in series connection. If there is anything above 3v, you probably won't regret getting that one.
- Gererally lithium ion batteries are equipped with a BMS(Battery Managment System) that maintains the individual cell voltages and offers a bunch of safety features. When not used for long it might drian the battery pack slowly and when the battery drops below a certain level, the BMS cuttoff the supply and thus you might end up getting 0v over the output, to troubleshoot connect the battery to the charge source for a couple of minutes and check if it hold a potential above the mimimum limit.
So with all those precautions we get ourself the battery pack, it was scratched but not dented. The battery pack was a 10 cells 36v 21Ah that sums upto 756 wh stated battery capacity. We weren't able to measure the individual cell voltages but the good thing is that the overall unit is standing at 38v which means that idelay each cell has to be at 3.8v thats a real good sign for a healthy battery. The battery pack seems to be puffed from one side but will see that later on.
Step 2: Tearing the Battery Pack
To start with we have to get our hands on healthy cells and for that we started tearing the battery pack. Now as I mentioned earlier these are soft pouch pack unlike 18650 cells that offers hard casing, so becarefull with the knife cutter as it can easily punther the cells and a fully charge cell can easily explode with that.
Once we teared off the battery cover we found the packs to be arranged in two rows. Each row has five packs with each pack having four individual lithium ion cells connected in parallel while the pouches are connected in series. The front is equipped with a BMS.
Step 3: Monetring the Individual Cell Voltages
The next thing is to measure the individual cell voltages. To our surprise nine of them were standing at 4.20v, thats kind of an ideal condition as it the maximum voltage limit for a lithium ion cell. But as we remember the whole pack was holding a potential at around 38v which means that one of the corner cells is at 0v and thats the case. As discussed in the previous step the whole pack puffed up due to over discharge and i guess thats the reason why they throwed the battery pack.
Everything is good but there is something wrong, probably the BMS as it would have drained that pack but with one cell standing at 0v the BMS should have cutoff the battery pack but thats not the case as we measured 38v at the output, but will figure out that later.
Step 4: Capacity Testing
The individual cells voltages can be a sign for a good lithium ion battery but its just a good initial guess for healthy battery pack and there is no gurantee that its holding a good capacity.
So to test the actual battery capacity we have removed the puffed cell, jump connected the rest of them so that we have total nine packs connected in series and with a nichrome heating filament connected across a DC watts meter we are ready to test the battery capacity.
The heating filament offered nearly 500 watts of dummy electrical load. It took just over na hour to drain the battery pack during which we continiously monitored the battery pack voltages and the seems to remain balanced throughout the drain. We did a manual cutoff at 27v as 3v is a safe limit for each cell to cutoff for lithium ion batteries.
The battery pack delivered arround 540 Wh (watt hour) thats arround 80% of the original stated battery capacity. So we are good to design the battery elcosure.
Step 5: Designing the Battery Enclosure and Holder
One of the main challange for converting the bicycle is to pack it with punch of power to make it fun to ride. The Brushless outrunner motor that fulfilled our power needs now require a good deal of battery capacity and we have very small space to get a sufficient amount of battery capacity.
Now customizing the whole battery pack helped us to design two battery packs. We later replaced the puffed pack with a working one from another battery, so we had 40 individual lithium ion cells to work with. Thus we decided to built two seperate battery packs, each one of which is a 10 cell pack with each pack having two cells in parallel and thus forming a 36v 300 Wh battery pack.
The design of the enclosure was simple, ten compartments to separate the packs with a bit of head room for BMS and holders for a pair of XT-60 male and female connectors for discharging and charging the battery pack.
Both the battery packs are designed to fit below the bicycle seat and for that we have designed the battery packs holder. The holder is designed to slide over the seat holder and tightened with three allen key screws with nuts on the other side. Once the battery packs are slide in place the top holder helps to keep the battery packs in place.
Battery Enclosure and Holder design files(STL files):
https://drive.google.com/open?id=1WAdiVWc7L_svBRvM...
Step 6: Dissassembling the Battery Pack
Later we dissassembled the battery pack and we started by desottering the connection over the PCBs, yup Printed Circuit Boards and here I would love to take a moment and thank Stariver Group for making this project possible. With over 20 years of experience for manufacturing and assembly of customized printed circuit boards they are providing some of the finest services out there at an out standing price right at your door step. So take a moment and head up to their website to order your customized PCB for your upcoming project.
Now once we removed the PCBs, we than carefully took cells apart using some alchol dipped cloth and a ruller. Be carefull during this step as you can easily puntcure the cells if you are not carefull.
Step 7: Assembling the Cells
The individual cell voltage is measured and then we mentioned the polarity of each pack before throwing them inside the enclosure. In total there are ten packs each one of which has two cells connected in parallel while all the ten packs are connected in series. For that we have to place the packs alternatingly inside the enclosure.
Once all the packs are in place we sottered the tabs carefully as there are a whole lot of exposed terminals ready to bite anything that shorts them, so again be carefull.
Next we placed the male and female XT-60 connectors within their holders and sottered the positive terminal directly while the negative terminal will be connected through the BMS.
Step 8: The Battery Managment System
Have you guys noticed how many times I have discussed the voltage of individual cells, yup alot and its because of the face that lithium ion cells are very sensitive with the voltage. The maximum charge potential is 4.2v, the minimum cutoff voltage limit is 3v while the nominal voltage is 3.6v.
Now with this much cells arround we need an intermediate unit that manages the individual cell voltages that occur due to various charge and discharge cycles with sligh variation within the resistance of each cell. For that we are going to use a BMS (Battery Managment System) and for our battery pack we needed a 10 cells BMS as they are ratted for the number of lithium ion cells that are connected in series and also the maximum discharge current that you are planing to drain. As the original battery pack was a 10 cell too so we have used the same BMS.
First we connected the individual cells to the BMS and then we have connected the charge negative, discharge negative and battery negative terminals. Next we mounted the BMS to the top cover using a couple of screws.
Step 9: Retesting the Battery Pack
Before we glue the enclosure we ran a complete charge cycle followed by a discharge using the same nichrome heater and wattmeter setup as previously. During the whole test we took a close eye over the battery voltage and individual cell voltages. The battery provided the same capacity except that the BMS failed to cutoff the battery power as it went below the minimum cutoff voltage. Luckily we were monitoring the unit so we did a manual cutoff and later replaced the BMS to the one from the hoverboard battery pack and that worked absolutely fine.
Step 10: Gluing the Enclosure and Finishing Touches
Once the BMS was replaced we glued the top cover using epoxy to make the enclosure water proof. Next we printed and glued the face plate mentioning the specifications of the battery pack.
Step 11: End Results
The outcome of the project is just way too good. Those little buddy boxes have 600 watt hour of power to offer and thats just insane as this whole thing is built out of an old battery from scrap. We have tested the battery packs with our electric bike thats still under finishing work but the results were promising. We are upgrading the bike to achieve 60 to 70km/h of top speed and with that conversion the bicycle pulls arround 30 Wh with the maxmimum pull over the throttle which means that now with these two battery packs we can easily get upto 20 to 20km of range on a single charge depending upon the throttle we pull off during the ride. Isnt thats too good for an electric bicycle conversion.
The whole project was a good learing curve and cost us 20 USD including eveyrything and in the end we have an awesome pair of battery packs the fits right under the bums :P
Our electric bike conversion with this battery pack, a crazy motor hack and with a 3000 watts BLDC Motor controller will be coming this weekend on our youtube channel so do vist, subscribe and break that bell icon to get notified the moment we publish the built video.
https://www.youtube.com/channel/UCC4584D31N9RuQ-aE...
Will be there with another awesome project video.
Regards,
DIY King
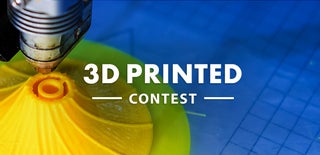
Participated in the
3D Printed Contest