Introduction: Cutting and Reconnecting Hue Light Strip Plus Segments
In the shop they told me it couldn't be done: I wanted to use a Hue Light Strip and cut it in pieces in order to reconnect it according to my own wishes.
In this case I wanted to replace two TL-Tubes that were end-of-life with up-to-date (color able) Hue Light strips plus. These would nicely blend in with the rest of my lighting. And taking a shower with colored light proved quite entertaining.
The LEDS needed to be bright and because the Hue strips produced 1600 Lumen they did qualify. It proved more than enough light for replacing two 56cm TL tubes. And as a bonus, these strips can nicely produce warm white, cold white and all comfortable colors in between. Really relaxing.
But now my problem: for it to work I would need to split the 2m strip into parts and reconnect those. Cutting is supported, as well as extending, but according to the Philips sales person and website, you need to throw away the cut-off part. This implied I would need to buy 6 times 2m of strips and use only 33cm per strip and throw away these 6 times 167cm "unusable" strips. Also it would imply 6 power connectors. What a waste....
Well you don't need to throw away anything and as you can see in the lighted examples: it still works!
Not for the faint hearted and you have to be confident with your soldering iron skills.
I am quite curious to find out how many people actually have cut the Hue Lightstrips Plus successfully. So.... if you did it, leave me a comment, that would be great!
Step 1: Preparing the Cut and Split the Strip
Remove the plastic at the place where the soldering pads are visible.
We will split where the soldering is and not where the cut marker with the scissors are displayed!!!
I started with the last segment of the strip, just in case when it wouldn't work, I'd still have 5 working segments left...Chicken, I admit...
Now comes the second advice: do not cut!!!
By applying heat to the soldered connections, you can split the strip into segments, without cutting anything... By doing this, you end up with the maximum area for re-soldering cable to it! If you were to cut, you would have less then half the length of the soldering pad left, mechanically not a good idea...
And... if you cut where the cutting line is displayed, then you render the remaining part useless, just like the manual says. Not so economical if you ask me.
The picture shows the split strip, just after de-soldering it. I used a reflow heater for this, but a soldering iron also works. Remove the tin, you will apply new tin and create nice and shiny new soldering connections.
Step 2: Connect the Segments
Now it is time to reconnect: I used an CAT5e network cable for this. This has 8 wires, I only used 6 of them.
Initially I aligned the cable like on the pictures, using a clamp to fix the position of the 6 network cable wires. Lateron I just soldered the wires one-by-one, this allowed me to work cleaner. Use a "third hand" , or better use two of these to align the tinned wire with the pad, then apply a small amount of new solder and let it flow nicely.
Important: cut, strip and tin all 6 cables that you use to the same length and match the stripped length of the cable with the soldering length of the soldering pad on the strip. Around 3 mm or so.
Also... Align the segments "as if they were still attached" and make sure the pads are connected as they were originally. Do not mix up / cross over wires. They must all be connected as they were originally, use the color coded wires to make sure! I always combined the two outer pads using a twisted pair of the network cable, I thought these were "ground" and "plus" but do not take my word for it... Needless to say, the segments are "direction" sensitive. They have an incoming and outgoing end. Always connect the "in" side to the "end" of the previous segment. Start with the segment where Philips connected the controller unit. The other end of that segment is your first "end". Mark your segments with a marker if you find it hard to orient them.
Alternatively (when you do not want to solder cables), you can buy pins and headers on ebay or aliexpress. Make sure you go for the 2mm separated headers and not the more common 0.1inch headers. These are the same ones the Philips uses for the extension strip, so you can connect en reconnect individual segments easily, without needing to solder then. (Only for attaching the headers obviously).
The result is a cable connected segment. After making the photo I cleaned soldering pads with a flux remover, so it looked even better.
Take your time for the soldering, do not rush, and make sure you do not introduce any shortcuts. If you do, remove all the soldering tin from the faulty connection(s) and start again. Use as little tin as possible, but make sure it flows properly.
For connecting 6 strips, you need to solder 2x5x6 = 60 connections, so you will learn on the job!
I already mentioned I started with the last strip... I was curious to learn whether it would work, so I first soldered a 3m network cable in between the separated segment and the strip with the remaining 5 segments... Pffffff.... it still worked, my soldering skills were confirmed and 70 euro was not wasted!
Step 3: Mount Strips to Your Convenience
Now the idea proved to work, I installed 3 strips next to each other, slightly shifted to use all the space where the 56cm TL tube used to be. The HUE controller was at the back and I made two units that were connected to each other.
So... I managed to split all 6 segments of a 2m Hue strip and reconnected them in two units with one meter bridged by network cable in between them.
I "broke" one strip in bending it after soldering, this strip is now at the end. I can still use it, but not extend it at that end (only at the beginning of the strip, but in my case this is not necessary).
I did learn that you must be careful manipulating the soldered strip. They are quite thin and not wrapped up in their protecting sleeve.
Oh... and do not start this, unless you are confident that you can calmly make these needed tiny soldering connections (6 on one cm). I found out that if you have a short, the light will work, but not display the desired color. In that case inspect your connections and fix it where you have the bridge between two pads. I had to redo a few that I made in a hurry, and when it was getting late. Better to work on this when you are relaxed and... work one segment after the other and check after connecting each segment. If you find an error, you know it is with your last soldered segment.
I am pretty sure it will void your warranty for the five segments that you attach in this not supported manner. Your only option to claim a faulty unit, is to "cut off" after the first segment (including "your" soldering) and prove that the HUE controller with only one clean strip segment attached is faulty.
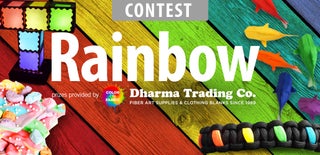
Participated in the
Rainbow Contest 2016