Introduction: DIY Cargo Plane Troop Seat Couch
Of the few times I’ve ever sat in one, someone always yelled “Stand up” and everyone had to shuffle to the open door. All geared up, this was the most comfortable seat in the house, well, next to this one… So no use in arguing with the gentleman that it was a perfectly fine airplane, you do as you are told. Hooah!!! Not sure if this is what I signed up for…
So for the upcoming Veterans Day and to help honor Veterans who served, make this piece of functional furniture suitable as a conversation starter so all you all can relax and tell the great stories garnered from your time in the service, fact or fictional.
I actually just went to a reunion of sorts with a cast of characters from my college cadet years. It's hard to believe it's been more than 30 years since I've seen most of them. Man, am I old, like Caitlin says.
The completed product here is not exactly mil-spec but close enough for government work. I just wanted to whittle down my scrap wood pile a bit and this is what you get. As usual, this project was built as I went along but I will note what you should do better if you want to make one.
Step 1: Get Your Sticks in Order...
OK, I had to get some parts for this project but I did use my military discount at the Big Blue box home center. Sign up and theirs is good 24/7 unlike Big Orange.
I got some standard dimensions of a small couch from products on the market. Roughly the seat height should be 16-18 inches high, seat depth about 22 inches, and width about 60 inches.
The length was perfect to use 5 foot sections of precut electrical metal conduit. 1. It is easy to get in the car after you buy it at the store and 2. It simulates the look of the aluminum tubing of the real troop seat.
Since real troop seats have machined, welded or cast fittings for the tubing, I needed to improvise since I have none of the fabrication tools for that. I do have a tiny HF welder still in the box, bought it on sale a long time ago with coupon but afraid to plug it in at the house and blow the breakers.
I'll just make a wood frame for the side supports and use pipes or conduit for the long runners.
I had some 1x4 stock and a few furring strips that were kinda the same size. I could put together some side supports for a small couch. I used all the odd cutoffs to bolster the single wood strut for the legs. They are needed to beef up the location where the conduit clamps would screw in. Glue pieces with the wood grain going in a different direction to increase strength like they do with the layers of plywood. Try not to screw into endgrain which has no strength in holding.
I used pocket hole screws to attach the legs to the cross runners but furring strips seem be be dimensioned smaller than the proper kiln-dried 4S squared sides more expensive lumber. The furring strips are also pretty rough since they are not meant for appearance. The furring strips I had were laying around so long I think they dried somewhat so they shrunk in size and warped a little. Anyway, the pocket screws burst out a few times because things weren't perfectly aligned so I just patched over with popsicle sticks. It would also provide a bit of support when glued up.
Paint in silver to make it look like metal parts to match the metal conduit.
Step 2: Can Do It Conduit...
There are different types of metal conduit for electrical work. I am using EMT which is bendable with a pipe bender tool. I used both 1/2 inch and 3/4 inch EMT conduit.
There is an assortment of other parts to get while using conduit. I got some conduit clamps and parts to cap the ends of the bare metal conduit. For the 3/4 inch wire connector plug, I clipped off part of the plastic plug so it would fit compressed in the EMT conduit. It's really meant to fit a real 3/4 inch opening in an electrical box. The 1/2 inch plastic bushing fit over the 1/2 inch conduit. I tapped it on with a rubber mallet.
I made some wood bases that would act as cross adapters for the top crossbar piece. I cut a V-groove to better fit the conduit. I used the miter saw to streamline and sculpt the shape of the wood a bit. 3/4 inch wood screws are used to attach the clamps. I couldn't find a box of round head wood screws so these will have to do.
Step 3: Brace Yourself...
Because we know from engineering that we have an indeterminate structure for the base, I wanted to add a cross piece to make keep the sides from bowing out and wobbling. I could have made a wood cross brace like you find on the bottom of an outdoor picnic table or have a metal sway bar across the bottom. I got out my conduit bender and a piece of 1/2 conduit (I do not have the bigger 3/4 EMT bender). I tried to make a crosspiece that looked like angular tubing braces but found the tubing bender only made big smooth bends. This EMT tubing is really mild steel and not aluminum so it was tougher to bend. So, 1. Bending metal tubing is an art and 2. It's not my MOS so I am not skilled at it. I finally wrangled it into some shape where I could pin it down on the center support beam and on the front side legs.
Step 4: Static Lines...
I found some red utility fabric in the clearance bin at the discount fabric store.
Purchased online was a 50 feet roll of 1-1/2 inch wide red webbing and tri-glide buckles to attach the straps to the upright crossbar. I did end up using all of it to make the webbed seat back.
The first thing I did was to hem all around the piece of material for the seat. It would be suspended between the front and back rods. I cut X slits at the points where the seat bars were mounted into the supports. Pull back the fabric and sew all around to reinforce the opening.
You can then seam that side forming a channel to pass the seat tube through. Do for front of the seat and back.
With the seat fabric pulled on to the front and back seat tube it looks like a camp cot or medic's carry litter. Hmmm, maybe I should have started out by modding one. Since the fabric was longer front to back, I was able to pinch the excess material and sew it so it formed a portion of the seat back. Mark it out in tailor's chalk which I did not do. I had to take apart a seam that drifted while sewing by eye. Test fit to make sure it will go on the seat bars.
I then cut a bunch of straps long enough to reach from the seat back to the top crossbar. Make sure to add enough length to use the buckle. 7 vertical straps looked about right to be the webbing back grid. I then had enough webbing on the roll to cut 4 cross straps. Sew the vertical straps spaced evenly on the seatback piece. You can then lay out the rest of the grid.
Since marking with tailor's chalk doesn't work to well on slick webbing, I just stapled where the straps crossed in the layout. You can then sew the horizontal straps to complete the webbing gridwork. Use two staples for it to hold as you wrangle the spaghetti mess in the sewing machine. Tack down the connection down with a seam, pull out the staples and sew a box with an X pattern in the middle.
The free ends of the cut polyester/nylon webbing needed to be sealed so that they do not unravel. I roasted the ends gently in the flame on my gas stove. Do this only if you are a professional...and it's your stove. And let the napalmy melted ends cool before touching. Don't let the hot ends contact anything else while it cools.
You can then put on the tri-glide buckles forming a loop at the top of each strap to attach to the crossbar. Pass the metal bar through the loops when installing or put the buckles on later when you add the fabric seat to the framework.
Step 5: Parting Shots...
Screw in the rest of the conduit clamps after all the parts have been aligned. I just used a popsicle stick as a reference measure to gauge everything to the right spot. Get squared away.
I guess all of this can be disassembled and packed flat in an IKEA box and air dropped anywhere in the world...
Seeing it fully assembled, I think I need to tighten up the fabric suspended between the seat bars. Get a heavier duty canvas or outdoor fabric to use for your seat fabric. The seat will also sag with a heavy load on it so try to pre-shrink the fabric so it doesn't stretch as much and make to fit. So the couch fits, what, 4 - 6 people? 3 with full gear?
You can make a fold-up wall mountable version for the mud room or entry foyer.
Essayons! (Let us try! Motto of the Corps of Engineers)
Victory! or whatever your unit motto was.
Ain't no use in looking down. Ain't no discharge on the ground...
Misery loves company. And Company builds character.
Enjoy!
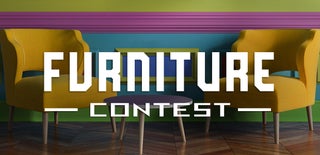
Participated in the
Furniture Contest 2018