Introduction: DIY Concrete Toothbrush (and Friends) Holder
My bathroom has been cluttered for years now. As a person whose room is rarely messy, his school bag has only one notebook and pen and his computer desktop is completely empty, my sink clutter was no exception; it made me anxious.
In the past, I had few plastic toothbrush holders, but I've never liked how they looked, and that, made me even more anxious then simply putting my things on the sink. Few months ago, I've decided that I must end this source of anxiousness, I've looked online for toothbrush holders that I would like, and Ive found this, I liked the core design elements of it (like the toothbrush slot), but it still wasn't quite there.
That same evening that I've searched for a holder, I've decided that nothing was good enough for me, and that I should just built one myself, based on the one I liked. From the moment I've decided this, to the moment I started designing it, passed no more than 5 seconds, and in less then an hour I had physical sketch and 3d model in fusion 360. I wish I could've said the same about the time between designing it to building it, it took me about 2 months to build it! you might ask yourself: "if he was so detriment to kill the source of anxiousness, why had it took him so long?" and the answer is simple: I was afraid, I was afraid from failing, I was afraid from not doing it perfectly, I was afraid because I've never used concrete before. I learned three things from this first of all concrete isn't scary it is really fun and I will most certainly use it again, don't expect perfection,the fact I feared from concrete so much, made me make one of the only decisions that I was right about in the first try, Ive decided to make two molds and thinking about the first one as an experiment, this decision made the process far more enjoyable and stress-free, how the saying goes: "practice makes perfect" as concrete is cheap, I highly recommend you to make at least two if not three molds.
Supplies
Materials:
- Foamboard 1 cm (~0.4 in) thick
- Cement (I've had 1 kg bag and it was left with a lot of concrete after 2 pours)
- Sand (if you're using premixed concrete you don't need sand and water)
- Water
- Hot glue sticks (1.5 per mold)
- Packaging tape (or any kind of tape that is strong)
- Concrete sealer (preferably spray)
- Recycled plastic container/bucket (for mixing the concrete)
- (Optional) Newspaper/nylon map for easy cleanup
Tools:
- Hot glue gun
- Box cutter/utility knife
- Speed Square
- Ruler
- Printer (optional)
Step 1: Sketching the Design
If you are using my design skip to step 3
Think about how you want you're holder to look like, if you can't imagine how you want it to look, you can ask yourself the following questions:
- What products will be in my holder?
- How many compartments do I need/want?
- Which products will be together in one compartment, and which will have their own?
- Do I want any special features like angled slot or weirdly shaped compartment?
after you can vision the general look of your holder start to place the products on a piece of paper and play with the position of the products until you get a desired look afterwards start to draw the outlines of your compartments (according to the way you layed out your products) you'll might have to go back and forth between placing the products and sketching to get a great design
What I would've done if I did it again (tips):
- Place tall products in the back for taking out products easily
- Leave room for error, originally, I've planned that all my sides would be 5 mm thick, I worried that it won't be strong enough, turns out that 5 mm of concrete is plenty strong enough, but it doesn't leave room for error which will result in too thin walls as you'll (so would I) make something imperfectly
Step 2: Making a 3d Model (optional)
I recommend you to make a 3d model as it helps in several things:
- It helps with visualising the final look and making adjustments to make the best looking option
- You won't loose the design so if you would like to revise it later you'll find it easily (and in good condition)
- You'll be able to get super exact measurements (In the next step you'll understand way its good)
- You won't have to use math to get every wall size
I used Fusion 360 to model this (and I highly recommend you to use it too) but you'll be able to model this in most modelling softwares.
I won't get into how I modeled it, as it highly depends on the software you are using, but I can tell you, that it doesn't require any special skills, its pretty basic.
Don't forget to also model the form! To model the form, just make new set of walls, that sits inside the compartments (and outside the external walls) that is the thickness of your foamboard. (take a look at the pictures above for clarification)
Step 3: Cutting the Form
Instead of measuring every cut on the foam board, I've decided that I'll print them in actual size, and then cut according to the drawing. I've decided this, because I knew that it will make the cutting faster, more accurate and will reduce the amount of headaches I'll get from measuring every piece.
When I made the template, I made few mistakes so I made new version after every mistake.
v2: After the first mold, we've realised it will be better if the pieces will have shared sides, as it will make cutting faster and more accurate.
v2.1: Turns out we forgot to print one piece.
v3: We made the external walls go further by 5 mm, for making the mold make-able, in addition, we added letters for easier assembly.
To cut the foam board, attach the templates to the foam board using double sided tape (or tape rolled over itself), use Speed Square to make a 90 degrees for the utility knife to cut against.
If you use my design, I recommend you to download and print all the v3 files. When printing, print one page and check with a ruler if it's true to size. In my Mac, when I printed it, I just made sure that the scale is 100% and it printed correctly. I believe that windows has some similar feature, but I am not sure how to do this.
Step 4: Assembling the Pieces to Create a Mold
This is presumably, the most important step in the whole process, so take your time to check things are sealed good.
Before I've assembled, I've sorted the pieces I have according to the different compartments. This step is crucial to not make any mistake later.
The next step, is to attach the inner compartments. I attached them with hot glue for convince. As for making a good seal, I took the hot glue, and smeared it on the side in such way it won't affect the look of the final product too much, but will still close the gaps between the pieces.
Using the same techniques as above, join the outer walls and floor together.
At the first mold, we (my father and I) have tried to attach the compartments at the normal way up, and pushing the concrete using one compartment which wasn't attached yet, this technique doesn't work well! It resulted in unfilled walls. At our second try, we decided to try a different approach, we've decided to attach the compartments upside down, and pour from above (covering the compartments). This method resulted in much better holder.
After you attached the compartments upside down, wrap the outer walls with a lot! of packing tape, it helps to eliminate leakage and it improves overall strength.
What I would've done if I did it again (tips):
- Think about the orientation of pieces after the mold flips
- make sure that the external walls are squared
Step 5: Making and Pouring the Concrete
When using the upside down approach, pouring isn't that complicated, all you have to do is mix water, sand and cement (ratio below) and then lightly tap the mold on the table (to make sure it made into all the nooks and crannies and for popping air bubbles).
We've used 1.25 cup of water, 2 cups cement, 3 cups sand ratio but it will might change if you are using different materials, generally speaking, you want the mix to be pourable, with the least amount of water possible.
We found that mixing by hand is much easier than mixing with a stick.
Mixing the concrete and sand before you add the water is recommended.
What I would've done if I did it again (tips):
- tap harder to pop more bubbles
- make sure the bottom (top when pouring) is level
Step 6: Demolding and Finishing
Demolding is really simple, the foam board pulls out easily, using the flat edge of the utility knife. You'll might have to cut the bottom of the inner compartments few times to take it out, as the opening isn't big enough to just pull it with your finger.
Finishing isn't hard either, to finish the holder, I sanded it with 320 grit though I haven't felt any noticeable difference, it was mainly used to get rid of things I didn't like (as the edges of the foam board which leaves weird texture).
After I sanded a bit, I used sealer. You want to seal the concrete for obvious reasons, as this holder will live near water, which over time, will ruin the concrete if sealer isn't applied.
I applied a sealer which isn't specifically for concrete, the reason for it is pretty simple; the store didn't have anything different. When you buy sealer, try to search for one which is spray, as it will help applying it in hard to get corners. If you don't have spray, you can do what I did, and repurpose old spray bottle (windex or something) for spraying sealer.
What I would've done if I did it again (tips):
- use better sealer
Step 7: Enjoy Anxious-less Bathroom
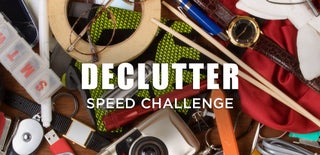
Participated in the
Declutter Speed Challenge