Introduction: DIY Halloween Party Table Props
Hi, I made these props a few months ago and put a slide show here: https://www.instructables.com/id/Halloween-party-table-props/.
Now, i take this opportunity to give more details of how they were made.
This creation was a highlight of the birthday party of my youngest daughter. I would like to share with yours.
The party theme was Halloween. Various materials such as recycled plastic bottles, and cardboard were used.
I hope you enjoy.
Step 1: Materials:
- sheets of A4 paper;
- cardboard sheets sized A4;
- four acrylic tubes with lids (can be found at craft stores);
- white glue and hot glue.
- 2 cable ties;
- a bamboo barbecue skewer;
- extensions to servomotor;
- scraps of cardboard;
- a piece of balsa wood an 8 x 2cm (you can use a strip of cardboard, popsicle stick ... etc.).
- 5 screws, 4 nuts and 4 washers (can not remember the dimensions)
- 1 mini servo;
- 1 Servo standard;
- One arm to the servo (I used a red);
- a programed Arduino board (I used the Duemilenove);
- two rubbers to hold the microcontroller in the breadboard;
- a breadboard;
- pieces of wire for the connections or jumpers to the breadboard;
- extension for servomotor (you can use a 3 thin wires also. Taking care of no more than 2 meters as there may be signal interference);
Step 2: Support for Candy
I did the drawing in CorelDraw. But can be easily done in Word.
I cut the pieces to best take advantage of the area of cardboard and pasted them.
I made several pieces as many were candy.
Unfortunately the pictures do not show very well the parts because the line was very thin. After being cut, is much better to understand.
After cutting the pieces, Just glue into place.
The circles are the most difficult to cut.
I suggest putting a thicker piece cardboard on top, or increase the space between the edge of the circles with the wall as part of the time, tends to give a bent. Another suggestion is to support the tubes at the base.
Step 3: The Owl
The owl, I download for free on the canon site: http://cp.c-ij.com/en/contents/2022/03266/index.html
Print it on A4 paper.
The tips of mounting are in the file in PDF. The assembly is not too difficult since it was my first papercraft and I do not come out so bad. But has several parts (14 pages) and requires a good assembly time. Especially for beginners.
The owl was set at candy holder by two plastic clamps and a barbecue skewer.
I put a servo head and managed it for a Arduino.
Operation: The owl is stopped and suddenly, for a random time, she moves the head quickly to the left and then back to look to the right slowly, giving the impression of being on a recognition . I lost count of how many people took with her a scare.
Step 4: Witch in Cauldron
This witch moves the arm as if you were cooking in the pot.
I did the drawing after searching the internet for witches, shadows, shades witch, ...
After that, simply print in A4, paste and cut the cardboard.
The witch was made before buying the pot. After it was found that she was very small. Simply was cutted a strip of cardboard and put down, hitting the other takes time and to complete the wooden spoon in her hand. After the painting, almost did not to saw the difference.
The arm that moves was separated and subsequently fixed with the aid of a screw, nut and washers.
The Servo was fixed to a piece of cardboard with the aid of two screws and then the cardboard was secured with hot glue at the base of the witch to support it, allowing it to stay standing. Take care not to get too close to the body of the witch, reserving a room for the servo arm to move freely.
The linking between the servo arm and was done with a piece of balsa wood that I had at home but can be done with a simple popsicle stick. The holes in the shaft ends are meant to be loose. That is, the screws are only fixed link between the witch and the servo.
The other screw is arrested only in a movable arm in order to connect the rod to the servo arm.
The witch works as follows: The microcontroller sends a command to the servomotor to rotate 90 degrees and then return to its initial state, causing the arm's movement. Simple as that.
Step 5: Using the Arduino
IInitially, fix the Arduino with the help of rubbers, then connect the power wires (5v red wire black wire and GND). In Arduino, has a stabilized output of 5 volts. I used this point to feed the servo. The signal comes from pin 0 and is connected to the Matrix via a white wire. Then simply plug the wire extender to connect the Witch's Servo. On the software, the witch is connected to pin 1.
For others, just repeat the above process using the other output ports of the microcontroller. I put five more cause I intended to put more props. But the table would not accommodate everyone.
OBS.: As a security measure, the software was not meant to trigger more than two servos at the same time.
I hope I have helped to sharpen your imagination. And this tutorial can be a starting point for something bigger.
Criticisms and suggestions are always welcome.
Software:
Software:
int servoval = 0; // variável do servo
int tmp= 1500; // variável fixa de temporização
int randomval2 = 0; // variável do tempo de pausa
#include <Servo.h> // biblioteca servo
Servo coruja; // criando o objeto coruja
Servo bruxa; // criando o objeto bruxa
Servo voando; // criando o objeto voando
void setup (){ // setup
coruja.attach (0); // atribuindo a coruja ao pino 0
bruxa.attach (1); // atribuindo a bruxa ao pino 1
voando.attach (2); // atribuindo o voando ao pino 2
}
void loop (){
randomval2 = random (4); // variável para escolher o tempo de pausa
randomval2 = randomval2 * 1000; //ajustando o tempo para segundos: 0, 1 ou 2 segundos
for (servoval = 0; servoval < 180; servoval += 1){
coruja.write (servoval);
delay(15);
}
for (servoval = 180; servoval>=1; servoval -=1){
coruja.write (servoval);
delay (15);
}
delay (randomval2 +1000);
for (servoval = 0; servoval < 90; servoval += 1){
bruxa.write (servoval);
delay(15);
}
for (servoval = 90; servoval>=1; servoval -=1){
bruxa.write (servoval);
delay (15);
}
int bruxa = LOW;
delay (randomval2 +1000);
for (servoval = 0; servoval < 180; servoval += 1){
voando.writeMicroseconds (1550);
delay (tmp);
}
int voando = LOW;
delay (randomval2 + 1000);
}
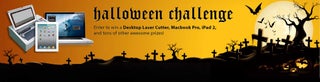
Participated in the
Halloween Decorations Challenge
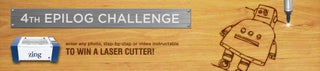
Participated in the
4th Epilog Challenge