Introduction: DIY Pirate Metal Detector | Almost Fully 3d Printable
This project is focused around the Pirate Metal Detector, a popular circuit of Russian origin. It’s a reliable, cost-effective, and easy-to-build circuit design. My personal goal was to create a nice enclosure for this amazing circuit. With correct components, it can detect coins at depths of ~20cm and larger objects at a depth of about 1m. The circuit used utilizes a single coil for both signal transmission and reception.
Supplies
The entire setup can be assembled for approximately ~40 Euros. If you have a shop nearby, you might be able to save on shipping costs. The links which are provided are just examples of where I ordered; you might be able to find them at a much lower cost elsewhere. You can get the PCB from PCBWay or Jlcpcb.
- 2x 9V Battery-clip
- PCB
- Wooden Broomstick (2.4 cm, example)
- Insulated copper wire ~0.5mm diameter (Coil: ~20cm diameter, 25+ turns, example)
- some Copper cable & jumper connector for wiring
- 1x 5k, 10k, 100k Potentiometer (example)
- 1x TL072 Opamp (example)
- 1x NE555 (example)
- 1x IRF740 (example)
- 1x C1815
- 1x S8550
- 2x 1N4148
- Cable jack and adapters (example)
- EITHER: Speaker 8 ohm (example) or 3.5mm jack (example)
- Capacitor: C1 100nF, C2 100nF, C3 10myF, C4 10myF, C5 1nF, C6 10myF, C7 1myF, C8 1mF
- Resistor: 50 (R16); 100 (R2, R5); 150 (R6); 220 (R7); 380 (R8); 10k (R1, R4); 47k (R3, R9); 68k (R10, R13); 70k (R15); 120k (R14); 2M (R11)
Step 1: Description
The circuit is build based on the instructions provided by this source (and forum). Pay them a visit for additional info, or more interesting circuits.
You can use my parts freely under given licence but keep in mind the circuit has a different licence. Personal use is fine, more info from Folder in Step 3.
This project is intendet to give you a good introduction into creating of one of the most basic Detectors. Therfor feel free to join ther community of creators and experiment with different variation or even your own version of the detecting circuit. The Forums linked provide a good guidance and a Additional info you can find in Step 3.
PI Metal Detector:
The Pirate Metal Detector is a type of pulse induction (PI) metal detector. It’s known for its simplicity and affordability.
Circuit Origin:
This circuit is widely accessible through various online resources due to its well-documented design. However, it’s important to note that the information might not be available in your language, and some components might not be easily accessible. This is because only a few variations of this circuit use western parts, which could pose some challenges.
Circuit Overview:
The circuit can be divided into two main parts: a transmitter and a receiver. For PCB manufacturing, JLCPCB and PCBWay are recommended choices.
Transmitter:
In this part, a NE555 microcircuit generates rectangular pulses. These pulses are sent to a coil through a strong field-effect transistor. The coil creates a changing electromagnetic field. When metal enters this field, the changing magnetic field induces currents in the metal, called "eddy currents". These eddy currents generate their own opposing magnetic field. This interaction causes a disturbance in the coil's original oscillating signal.
Receiver:
The receiver then detects these disturbances. The generated signal is processed by the first operational amplifier (Opamp). In this setup, the Opamp is used as an inverting amplifier with a capacitor at its input, essentially operating as a differentiator. This configuration allows the output voltage of the Opamp to be influenced by the rate of change of the generated signal over time, similar to computing the time derivative of the input voltage.
The subsequent step involves further signal processing and filtering before it is passed to another Opamp. This second Opamp generates pulses from the processed signal, which can then be heard through the speaker. To fine-tune the circuit with greater precision, two potentiometers are incorporated into this section of the circuit.
Step 2: 3D Printing
You can find my STL files in the provided link or below. Print all parts with supplied posture.
The enclosure parts should be printed with a 15% infill and a 0.2mm layer height.
Screws, nuts, and bolts should be printed with a 50-100% infill at 0.8mm layer height. Temperature should be higher than usual to ensure good and strong layer bonding.
If you wish modify the design of the box-body (or create new) to fit your chosen PCB.
Hint:
COIL: Select a coil variant that suits your needs. The version shown includes a coil, a hull and a mount. The hull is not necessary, you could alternatively protect the coil wire with some tape. The new version is an improved 20cm frame with a mount included, saving some weight because there is no need for a separate hull or mount.
You will need:
- 1x pirate-box-base
- 1x pirate-box-body (needs support)
- 1x pirate-box-mount
- 1x pirate-coil-mount_v8 (needs support)
- 1x pirate-handle-grip (support might help)
- 1x pirate-handle-mount
- 1x pirate-stock
- 1x pirate-stock-mount
- 4x pirate-mount-nut
- 4x pirate-mount-screw
- 6x pirate-wingednut-default-8mm (or ringnut)
- 7x pirate-screw-default-8-30mm
- 10x pirate-screw-default-8-20mm
- 11x pirate-ringnut-8mm
Coil (either):
Standard 18cm (shown) :
- 1x pirate-coil-hull
- 1x pirate-coil-frame
- 1x pirate-coil-mount-base
Improved 20cm:
- pirate-coil-frame-improved-20cm
Attachments
pirate-box-base.stl
pirate-box-body.stl
pirate-box-mount.stl
pirate-coil-hull_v2-18-light.stl
pirate-coil-mount-base_18-light.stl
pirate-coil-frame-18cm-light.stl
pirate-coil-frame-improved-20cm.stl
pirate-coil-mount-v8.stl
pirate-handle-grip.stl
pirate-handle-mount_v2.stl
pirate-mount-nut-v2.stl
pirate-mount-screw-v3.stl
pirate-ringnut-8mm.stl
pirate-screw-default-8-20mm.stl
pirate-screw-default-8-30mm.stl
pirate-stock-body.stl
pirate-stock-mount.stl
pirate-wingnut-default-8mm.stl
Step 3: Assembling PCB/Circuit
The circuit is build based on the instructions provided by this source (and forum). Pay them a visit for additional info, or more interesting circuits.
You can use my parts freely under given licence but keep in mind the circuit has a different licence. Personal use is fine.
There is a more information on the Google Drive Folder. The design was chosen because it’s ideal for beginners. The larger PCB should assist you in experimenting with and measuring your completed circuit.
After assembling a prototype according to the shown circuit schematic, I designed a compact PCB layout using Fritzing (access Drive Folder; Gerber & .fzz Files). For production purposes JLCPCB and PCBWay are my recommended choices. From given link you can access my Fritzing project (PCB & circuit view). I've also attached the Gerber files. You'll need the .zip folder containing all the files except the .fzz file and upload it to the manufacturer page.
I recommend to not directly solder the switch, audio and power connection, instead use pin connectors. This way you can assemble the housing later more easily. As a guide for populating the board, here's the schematic diagram and a brief component list:
Resistor:
- 12 (R16)
- 100 (R2, R5)
- 150 (R6)
- 220 (R7)
- 380 (R8)
- 10k (R1, R4)
- 47k (R3, R9)
- 68k (R10, R13)
- 120k (R14)
- 470k (R15)
- 2M (R11)
Capacitor:
- C5 1nF
- C1 100nF, C2 100nF
- C7 1myF
- C3 10myF, C4 10myF, C6 10myF
- C8 1mF
Others:
- 1x S8550
- 1x C1815
- 1x IRF740
- 3x Potentiometers
- 2x 1N4148
- NE555 DIP
- TL072 DIP
- Connector pins
It's recommended to use sockets for the IC's (NE555 & TL072). An IRF740 is used to generate the rectengular pulses. The C1815 generate audio pulses.
Choose R16 (12-50 Ohm) depending on the sound level you want, where lower values result in higher volume.
Regarding the potentiometer I recommend to go with 5k (fine) and 100k (coarse) for the tuning. Regarding the frequency potentiometer I would choose 2k or 5k instead of 10k.
To ready the PCB for the next step, you’ll need to solder some wires for connecting the coil, switch, and power source. In the picture, these are represented by yellow wires. For the power supply, you can connect two 9V battery clamps in parallel.
Step 4: Assemble Circuit Box
When it comes to the circuit enclosure box, you’re free to choose a design that includes a 2.5mm headset jack and/or an 8 ohm speaker. The first image presents the completed design (using both).
- Carefully slide the PCB into place, ensuring that the potentiometers align with the respective holes (2nd image). Carefully bend back the potentiometers might help you when inserting the PCB, like shown in the picture. It can be necessary to sand a bit off the side wall or the PCB.
- Insert a power cable socket adapter (with a screw block on the back) into the hole at the back of the box. This is where you'll plug in the coil cable. Use the cables from the coil pins and connect them to the adapter. Polarity doesn't really matter here. I suggest using female-male jumpers, as they are easier to connect to the PCB, and you can fix them to the screw block with the male end.
- I recommend incorporating a generic I/O switch. Insert the switch into the box and solder the wires from the sw-pins to connect it. To do this, simply cut the female jumpers in half and solder them to the switch.
- For the audio output (SPKR1 on PCB) you can either use an 8 ohm speaker or a 3.5mm jack plug. I simply used jumper connector pins here because they allow easier switching. The + pole of the speaker should be connected to the upper pin and - at the bottom pin (closer to the transistor).
- The headphone socket, in my case socket 1 is GND, 3 is the left channel and 4 is the right channel. Combine the left and right channels and connect them with a jumper to the top pin (SPKR1 on the PCB). GND is connected to the bottom pin.
As depicted in the first image, I utilize both options. The pins allow me to switch between the desired audio outputs. For practice purposes, I recommend using the headphone jack as it provides clearer audio feedback when something is detected.
Other parts:
- 2x female-female jumper wires
- 2x female-male jumper wires
- 8x OhmSpeaker or 3.5mm headphone jack
- generic Switch
- 2x 9V Battery-clip
- 2x 9V Battery
3d printed parts:
- 1x pirate-box-body
Step 5: Prepare Broomstick
You’ll need a broomstick or a similar object for mounting. A wooden one is recommended due to its ease of handling.
You’ll need to drill three holes into the stick using a 12mm wood drill bit. I suggest to use mounts to mark the correct locations for the holes. You can refer to the introductory image for guidance on where to place the mounts.
The cable connecting the coil to the circuit should have a larger diameter than the coil wire itself. The dimensions are for guidance only, adjust to suit your requirements:
- Prepare the handle: Start with a staff that is 1.2 meters long. Cut off any excess length from the end.
- Attach the spool mount: On one side of the handle, attach the mount for the spool and mark the hole.
- Mark the other hole positions: From the end piece, measure and mark two spots on the handle - one at 85 cm and another at 115 cm.
- Next, you’ll need a cable between 80 and 100 cm long. The diameter should be larger than the coil wire diameter. You’ll also need power cable jack adapters, one female and one male. Solder these to the ends of the cable. Here, shrink tubing or insulating tape is advantageous for insulating the solder joints.
- Afterwards, wrap the finished connection cable around the rod, with the male end in the middle of the rod and the female end at the beginning. Start about one hand’s width from the lower end hole and go up to about two hand’s widths from the middle hole. Secure the cable with insulating tape as shown in the picture.
Other parts:
- 1x Cable (about 1m)
- 1x male power connector cable
- 1x female power connector cable
Step 6: Finish Grip
Finally, position the pirate-box-mount under the pirate-box-base and connect them. Secure it in the right place using the pirate-screw-default-8-20mm and pirate-wingednut-default-8mm to stabilize the base.
Once this is done, close the box and fasten additional screws on the outside of the box.
Take the handle and insert it. Then, also insert the pirate-handle-mount and fix them using again the pirate-screw-default-8-20mm and the pirate-ringnut-8mm.
3d printed parts:
- 10x pirate-screw-default-8-20mm
- 6x pirate-wingednut-default-8mm (ringnuts also work)
- 4x pirate-ringnut-8mm
- 1x pirate-handle
- 1x pirate-handle-mount
- 1x pirate-box-mount
- 1x pirate-box-base
Step 7: Crafting Coil
The coil should consist of at least 25 turns of insulated copper wire with a diameter of 0.5mm diameter. A diameter of 0.7mm with around 20-25 turns is also acceptable. The Coil diameter of around 20cm is suitable. Two options have been tested: 18cm and 22cm diameter. The larger one seems to be better for detecting objects at greater distances. The smaller one seems to be more sensitive to small objects. When winding the coil, it is advisable to begin with more turns (28 or more!) and subsequently reduce them if necessary.
Take the coil frame and wind the wire around it. After winding, insulate both wires and feed them through the small hole at the bottom of the frame as shown. Make sure the wires are secured with tape to prevent the coil from unwinding.
If you choose the 20cm variant, protect the wound coil with some electrical tape, like shown in the picture.
3d printed parts:
- 1x pirate-coil-frame-18cm (variant)
Step 8: Finish Coil Case
- After you’ve finished creating the coil, you can proceed to attach the remaining parts. Place the pirate-coil-cover over the pirate-coil-frame and position the pirate-coil-mount on top.
- The spool wire should be put through the hole in the middle at the lower end (side of the mount). Using insulating tape to enhance the insulation of the wires is a good idea in this case.
- At every corner of the mount, insert a pirate-screw-default-8-30mm and secure it with either pirate-wingednut-default-8mm or pirate-ringnut-8mm.
- Place the pirate-coil-mount within the rings of pirate-coil-mount-base and insert the pirate-mount-screw fix it with a pirate-mount-nut
- Once your coil is done, a male power cable jack adapter is needed. Solder it onto your spool wires and isolate it with some tape or shrinking tubing. Fix it at the mount with some tape.
The new 20cm version is shown in the last picture, you can skip 1, 2 and 3 as it already has a mount integrated. All you have to do is insulate the outside as shown and solder the cable socket adapter.
Other parts:
- 1x male power connector cable
3d printed parts (18cm):
- 4x pirate-screw-default-8-30mm
- 4x pirate-wingednut-default-8mm or pirate-ringnut-8mm.
- 1x pirate-coil-cover
- 1x pirate-coil-mount-base
- 1x pirate-coil-mount
- 1x pirate-mount-nut
- 1x pirate-mount-screw
Step 9: Assemble Stock
Assemble the stock according to the picture given. Of course, it is possible to turn the mount by 180 degrees if you desire the detector to be shorter.
3d printed parts:
- 1x pirate-stock-mount
- 1x pirate-stock
- 2x pirate-ringnut-8mm
- 2x pirate-screw-default-8-30mm
Step 10: Assembling Detector
Once all tasks are completed, we can begin assembling the project. As shown in the picture you need all parts to be completed (bin mir nicht ganz sicher mit dem Satz).
Place the parts on the stick and use pirate-mount-screws and pirate-mount-nuts to secure them in place.
The assembly of the stock is straightforward. Simply position the pirate-stock onto the pirate-stock-mount, then use screws and ringnuts to secure them in place.
The assembly process should be self-explanatory. If you’re unsure, the images should provide some assistance.
3d printed parts:
- 3x pirate-mount-nut
- 3x pirate-mount-screw
Step 11: Usage & Calibration
- After the assembly process, you can power on the detector. Upon powering up, allow a few seconds for the voltage levels to stabilize. During this phase, the detector might produce some noise. While tuning keep the detector away from metal.
- Once the transition into the operating mode is done, you’ll need to adjust the potentiometers. The frequency can remain constant in generall. I usually keep it around 1-2k ohm (varies with Voltage).
- Tune the 'coarse' potentiometer until you’re on the verge of not hearing any signal. Following this, adjust the ‘fine’ potentiometer until it is barely producing any noise. If you can't find a spot where it produces no sound adjust the frequency.
- Now, when you hover over metal with the detector, it should immediately start ringing. Different soil types may require readjustment of the detector’s tuning.
If you encounter any issues, decreasing the number of turns on the coil may also assist in problem-solving. Having more turns is beneficial because it provides more flexibility. You can always reduce the number of turns if needed.
Step 12: Capabilities
The images illustrate how the signal levels from the audio vary. The intensity of these signals is influenced by the distance from the metal object, as shown in the images. This demonstrates effectively how proximity to the metal can alter the signal strength. Additionally, the orientation of objects, such as coins or nails, can impact the signal. This is primarily due to how the surface orientation affects the way the magnetic field interacts with the object.
The detector appears to be largely dependent on the quality of the coil. It can detect small objects like coins within a range of approximately 15-20 cm, depending on their orientation to the coil. The keychain which can be seen in the pitures can be detected from a max. distance of about 20-30 cm. Larger objects, such as metal sheets, can be detected up to a meter away.
If you like this project and want to support my work, feel free to leave a tip here. I appreciate your generosity and feedback. 😊
Step 13: Simulation (by Yvon Tollens)
Yvon Tollens, from the comment section, created an amazing simulation for the circuit. Information on how to install and utilize the simulation is included. (access Drive Folder)
This simulation greatly aids in understanding the internal workings of the circuit. I have included the folder containing the LTSpice file in the drive folder. The image displayed shows the activation of the transistor base in red (audio). The green line represents the non-inverting input of the second Opamp, while the blue line represents the inverting input. It is evident that the base is triggered when the blue line dips below the green line.
Furthermore, you can also find his calculation sheet belonging to the inductance (L) of the coil.
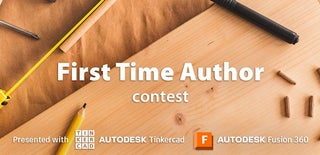
Second Prize in the
First Time Author