Introduction: DIY Sliding Deck / Dog Gate
My brother needed a gate to stop his three puppies (and rapidly growing toddler) from accessing the side of the house. A traditional hinged gate was not going to work in the space so I designed a sliding gate that could be fully opened and matched the existing Merbau privacy screen it would butt up against.
It uses a guide box, a simple latch and has been constructed out of decking material with primarily pocket-hole construction so there are no screws showing at all from the front giving a nice clean look. The Merbau is a great outdoor material to resist the harsh Australian elements and the Kreg jig makes it a fairly easy build with only limited tools needed. As this is dimensional timber most of the cuts are very simple.
My gate was approximately 150cm wide and 90cm high (59x35" inches) but the design can be easily scaled to suit most gaps.
Supplies
For this exact version as per the plans: (You can scale the materials up and down to suit)
Materials
- Approximately 16m (53') of 19x90mm (1x4") Decking (I use hardwood, but any outdoor decking will do)
- 32mm (1-1/4") Pocket Hole Screws - "F" Class for Hardwood, "C" Class for Softwood, and preferably stainless steel or blue coat for outdoor use.
- 30mm (1-1/4") and 50mm (2") galvanised regular screws
- 3 Casters (Non-swivelling)
- Decking Oil (Water Based)
- Gate Latch
- Water Resistant Wood Glue
- Optional - Wall Plugs (If mounting to brick/masonry)
- Optional - Deck Pre-treatment (If using new Merbau or other resinous wood)
Minimum Tools Required
- Circular Saw (or Hand Saw or Jigsaw)
- Speed Square (I use a Kreg Square-Cut (Australia))
- Power Drill, Drill Bits, Driver Bits
- Pocket Hole Jig (I use a Kreg K5 Pocket-Hole Jig (Aust))
- Clamps (I use Kreg Face Clamps (USA))
- Tape Measure (Imperial) or Metric (Aust)
- Sand Paper
- Paint/Decking Oil Brush
Alternative / Optional Tools to Make Life Easier
- Mitre Saw and/or Table Saw
- Impact Driver
- Countersink Drill Bits (or Countersink Drill Bits (Aust))
- Specialty Pockethole Clamps (I use the Kreg Right Angle Clamp (Aust))
- Combination Square
- Router / Router Table with 1/4" Roundover Bit
- Power Sander
- Shop-Vac
- An Awl
- Disk Sander (Purely for aesthetics of one piece. I only include it because I used it in the video!)
(NB: The links above will take you to Amazon.com (or for Australia Amazon.com.au where available) where you can source some of the gear I use if you can't find it locally. It won't cost you any more than normal Amazon, but purchasing via that link gives me a small commission and supports my work. Thanks!)
Step 1: How-To Video and Plans
To kick off you can download the PDF plans I made in Sketch-up and watch the video above that works hand-in-hand with this build. Between the video, plans and this Instructable, it should be a fairly easy build even for beginners.
TIP: To save money and make your life even easier with joinery, use pine decking instead of hardwood. Just keep in mind the durability and longevity of your gate will be less as well.
Being a gate, there is a very good chance you are going to have to adjust it to fit your deck or space. As such, only the cutting list has the dimensions to give you an idea of how much material is needed to make my exact version of the gate. The actual joinery plans don't have the measurements on them. If you spot an error or have any questions, drop me a line. I am Australian, so material prices are in Aussie Dollars and estimate only. (AUD$).
PHOTO TIPS: During each step, check my photos for further hints and tips tagged in the pictures.
Attachments
Step 2: Cutting the Decking to Length (Cross Cuts)
One of the best bits of this build is the cutting is (mostly) very straight forward crosscuts. Once you have your lengths sorted either off the plans or modified for your space you can knock out (almost) every cut. Consistency is more important than complete accuracy. If you are off by a tiny amount it won't matter... as long as EVERY cut for that type of piece is off by the same amount.
TIP: Carefully measure your long pieces of decking and plan out your cuts to minimise wastage.
If you are using a mitre saw, set up a stop block for each type of piece. If like me you are using a circular saw and Speed Square, you should be able to clamp up to 3 pieces together and cut them all at once.
Optional Video: The Kreg Square Cut - Setup and First Time Use
Step 2a: Mark up and label your boards (which board going to give what pieces?).
Step 2b: Dock off the ends (cut a few mm off) to remove the rough cut or sealant parts.
Step 2c: Cut your pieces to length. You should have -
- 7 Main Slats (For my gate, yours may be one or two different if you varied the height/spacing)
- 2 main Pieces for the Guide Box
- 1 Front Stile (will be ripped in two later)
- 2 Rear Stiles
- 1 Rear Rail (will be ripped in two later)
- The Top Cap / Middle Brace / Guide Box Cleat (will be ripped and chopped again later)
TIP: No need to cut a special piece for the castor mounts, we'll use offcuts at the end.
Step 3: Cutting the Thinner Pieces (Rip Cuts)
A rip cut is cutting a piece of wood along its length (Making wide boards thinner). This can most easily be done on a table saw, and if you have one go for it! However, this can also safely be done with just a circular saw and edge guide as I will demonstrate here.
Step 3a: Set up your saw. The easiest way is to use the edge guide that would have come with your circular saw. You can freehand it, but these are long cuts and will be very tricky to keep straight. I find a Combination Square set to half the boards' width makes setting the blade guide a breeze.
TIP: See the first photo, and don't forget to account for the blade kerf (thickness).
Step 3b: Set up for ripping. A bench with dog holes and low dogs or track saw docking station would be perfect, but if like me you have a limited workshop, see pictures 2 and 3 for my super quick ripping jig. Basically you can screw an "L" of thin scraps (I used 6mm (1/4") MDF) at one end of a spoil board (I used an old pallet piece) and some guide pieces down the length of the board to make a support to push your decking boards against. Get it close to 90 degrees, but no need to be pedantic, your accuracy comes from your saw guide.
Step 3c: Make your rip cuts! You will need to cut your Front Stiles and Rear Rails in half (45mm / 1 3/4") using this method. You can then rip the Top Cap too. CAUTION: The offcut from this piece will become the Middle Brace and Guide Box Cleat but I preferred to have these slightly narrower at about 40mm (1 9/16") and the Top Cap slightly wider at about 50mm (2") so it will fit snug in the Guide Box later. Make sure reset your saw guide before making this cut.
Step 3d: You can Crosscut the Guide Box Cleat from the 40mm (1 9/16") wide offcut to length now, but DO NOT trim the Middle Brace just yet. We'll take a 'real world' measurement for that after the frames are assembled.
Step 4: Drilling the Pocket Holes
Ok get ready for a lot of Pocket Hole action! There are other ways you could do this joinery, but for a novice making face frames like these, it is hard to beat the speed and simplicity of pocket holes. There are a number of good jigs around (you can also make your own) but I am a fan of the Kreg K5 Pocket Hole Jig. This is not a tutorial on how to set up or use pocket holes. (Plenty of good YouTube videos for that) but I will also include a video of mine on the two most popular Kreg Jigs, the K4 and the K5 and the difference between them.
Optional Video:The Kreg K4 vs K5 Pocket Hole Jigs
Step 4a: Lay out your Front Stiles (the thinner side bits) and Front Rails (the slats of the gate) on the ground and choose your 'good' sides to be the front of the gate. Use a spacer block (my design is a 30mm / 1 1/4" gap) to ensure your stiles and rails are flush when evenly spaced. Mark the spots on the back you are going to drill the holes with a pencil so you don't get confused later.
TIP: Shrink your spacer if the stiles are too short, find a bigger spacer if you stiles are too long (Trimming the stiles will affect your gate height!).
Step 4b: Set up your pocket hole jig for your material thickness (19mm / 1 1/4" in most cases but check your decking thickness carefully). Put two evenly spaced pocket holes in the ends of the backs of each Front Rail. (These can be quite long, watch you don't hit the ceiling or lights hanging down :D )
Step 4c: Repeat this pocket hole drilling for the 2 Rear Rails. (Remember these will be the thinner bits of the rear frame). Ignore the Middle Brace for now, we'll get to that later.
Step 4d: Grab the TOP Front Rail. On the same side you drilled the first pockets, drill pocket holes along one long edge that will be used to secure the Top Cap. Start about 50mm (2") from each end and evenly space the pockets every 200mm (8") or thereabouts.
Congrats, that was a lot of drilling. Now that's done, it's assembly time.
Step 5: Front and Rear Frame Assembly
If you've done your holes right this stage should be fun and quick! Grab a box of 32mm (1 1/4") Pocket Hole screws and let's get cracking. For hardwood decking, you need Fine Thread screws or it may split. Coarse Thread is best for pine decking. Stainless steel ones for outdoor use will improve the lifespan of your gate. I went through about 48 screws (7 Front Rails x4, 2 Rear Rails x4, 1 Mid-Brace x4 and the Top Cap x8).
Honesty Time: I used normal Fine Thread Zinc coated screws. As I'm also using waterproof glue, they will be hidden from the elements and oiled over, plus my gate won't see direct rain as it is half covered so I didn't bother getting the more expensive stainless ones. The gate is a year old now and not showing any issues so far but for full outdoor use, Stainless or BlueCoat would be the best option.
Step 5a: Assemble the rear frame by securing the top and bottom rails to the stiles with a water-resistant glue like Titebond II or III and pocket screws. If possible get the frame up on a bench for easier assembly than on the floor.
TIP: Kreg Face Clamps are ideal here but really most clamps styles will be fine, whatever you have on hand. Clamping multiple slats at the same time on the front frame increases efficiency.
Step 5b: Repeat the assembly for the front frame, ensuring you use your spacer block from earlier between each slat as you clamp it. Start with the top and bottom rails and work your way towards the middle. IMPORTANT: Ensure your pocket holes for the Top Cap are facing the correct direction!
Step 5c: Now it is finally time to trim the Middle Brace to size. Find the centre of the rear frame rails, position the offcut we saved from earlier, ensure it is centre and square, then make a real-world marking where to crosscut it. Trim it to length, add pocket holes like before, and glue and screw it in position. Make sure the pockets face the same way as the others on the rear frame.
There we go! It is starting to look like a gate with the front and rear frames complete. Next Step, the Top Cap.
Step 6: Shaping and Fitting the Top Cap
A quick step to attach the Top Cap to the now completed Front Frame. I created a 3mm / 1/8" reveal (overhang) at the front of mine for looks and feel, but this number is flexible to a point, whatever you feel looks good.
Step 6a (Optional): I used a 6mm / 1/4" Roundover Bit on my router table to create a hand-friendly smooth profile on the top edges of the Top Cap. A round over is just what it sounds like, it takes the sharp corner off. If you don't have a router you can achieve a similar result simply by going to town on the edges with some 60 grit sandpaper either by hand or with your power sander.
Step 6b: Choose an appropriate spacer for your reveal. I went with 3mm / 1/8". I had some thin sheet steel lying around but anything like MDF, plywood or shims will do. You could even use a few stacked coins or washers, anything to lift the front Top Slat a little off the bench as you attach the Top Cap. The size of the reveal is up to you, but any is better than none as I can guarantee your decking won't be perfectly straight, so the reveal hides this a little compared to a flush fit where the unevenness will be noticeable.
TIP: Remember the 19mm / 3/4" back frame has to be attached yet, so leave at least that much overhanging at the rear.
Step 6c: Apply a bead of glue to the front of the Top Cap (or even better the top of the slat, the point being you don't want glue anywhere except at this join). Clamp the Top Cap in place, ensuring the Top Cap is resting on the bench, not on the spacer, to give your reveal, but is flush with the gate frame at both ends.
TIP:While not essential, the Right Angle Pockethole Clamp was designed exactly for this type of job. If you are going to be doing a few projects with pocket holes, I highly recommend it. Otherwise, other clamps will work too.
Step 6d: Starting either side of your clamp position, drive your screws home to secure the Top Cap to the Gate Frame. Remember to move the clamp and fill the hole each time for the best results.
Ok done. Let's bring the two halves together.
Step 7: Join the Front and Rear Frames Together
Time to bring it all together and join the Front Frame to the Rear Frame. This will strengthen the gate up, make it sturdy and rigid. I did NOT apply any glue during this step. There are 33 screws in my frame holding things together, and this means if there ever was an issue, I can take it apart to repair more easily.
Step 7a: Place the Front Frame face down on the bench (pocket holes showing) and the Rear Frame on top of it pocket holes down and line them up. You should now have pretty much covered all the ugly pockets without the need of filling any of them.
Step 7b: Grab your Combination Square set to half the boards' width, a long ruler, or a straight offcut and mark centre lines down each piece of the Rear Frame. These lines will guide your pilot holes for your screws.
Step 7c: Double check everything is lined up, and clamp the Rear Frame securely to the Front Frame. Drill pilot holes through the Rear Frame into Front Frame. 3 holes for each slat (Left Stile, Middle Brace & Rear Stile) and a few evenly spaced every 200mm / 8" or so along the Top Rail and Bottom Rail.
CAUTION: Be careful to avoid your pocket screws AND not to drill through the front face of your gate. Set the depth of your bit to just under the total gate thickness (about 30mm / 1 1/4") or use a bit of tape on the drill bit to tell you where to stop.
Step 7d (Optional): Countersink all the pilot holes. A countersink bit creates a cone shape for the screw head to sit flush with the wood surface. Not strictly needed, but makes things look nice. My sink bit is separate to my drill bit. But I really want these cool 2-in-1 Countersink Drill Bits that save a lot of time!
Step 7e: Get as many clamps on as you can close to your pilot holes and get driving. Here it is important to use galvanised or other weatherproof screws. I like to quickly start all the screws in a row by hand, then come through and sink them. Not only faster, but fun too.
Step 7f: Give everything a good sand to knock off the sharp edges. I only went with 120 grit on everything, except the Top Cap which I followed up with 180 and 240 grits too as it is the only part that will be regularly touched.
If you now have a coffee table, you've done it wrong. Otherwise, you should have about 80% of a sliding gate done!
Step 8: Building the Guide Box
Let's take a break from the gate for a moment and assemble the Guide Box which will hold the finished product to the wall or deck fence and keep it running in a straight line. We have already crosscut and ripped our pieces earlier so this should be pretty straight forward.
Step 8a: Drill 4 pocket holes in both the Wall Cleat and Front of the Guide Box to attach them to the Top of the Guide box. (Don't worry that the holes in the thinner cleat will look a bit funny, it's fine).
Step 8b: Here you need a little forward vision. We need to pre-drill the mounting holes in the Wall Cleat that will be used to secure it to the wall or deck rail when we install the gate. In mine, I was going to use 3 mounting screws and so put one pilot hole between each pocket hole.
Step 8c: Apply glue to the Wall Cleat, clamp, and screw it down into the top of the Guide Box. Make sure the pocket holes face outwards and the ends are flush.
Step 8d: We will attach the front of the Guide Box now so we can test it all works. IMPORTANT: Do not add glue here, this piece needs to come off later to mount it to the wall! Just Clamp it in place (pocket holes facing inwards) and screw it into the top of the Guide Box.
Step 8e: Grab your completed Guide Box and run it back and forth along the whole length of the gate's Top Cap. It should run freely and not bind or jam anywhere. Ideally, it should also not twist too much. If things a little tight, sand or plane the Top Cap edge down until you get smooth operation.
Step 9: Attaching the Gate Casters (Wheels)
Ok, let's make this thing mobile. I suppose you could almost hinge it, but with the weight, you'd want some big hinges! As this wouldn't be practical in my brother's space I went with fixed casters (non-swivelling wheels).
Step 9a: Grab some decking offcuts and cross cut 3 even Mounting Blocks just wide enough for the screw plates of the castors. Ideally, your casters screw plates will be equal to the width of your gate but like mine, they may be a touch wider.
TIP: When selecting your wheels, make sure they are Non-Swivelling Casters, can take the weight of the gate (about 20kg / 45 pounds in hardwood), and suitable for outdoor use if they will get wet. Most casters are Zinc plated (like the ones liked above) and off some water resistance. Galvanised ones are superior in this regard but harder to find. I used 50mm / 2" casters. Keep their height in mind when measuring up your overall gate height.
Step 9b: Grab an Awl (or long screw/nail), position the 3 casters by eye in the middle of your 3 Mounting Blocks and mark the screw holes. You can also mark the 4 mounting pilot holes in each block. (In the video I started with just 2, but added two more mounting holes to increase strength).
Step 9c: Drill the pilot holes for the casters, then drill (and countersink if you can) the 4 mounting holes (these should go all the way through the Mounting Block.)
Step 9d (Optional): Round over the edges and corners of the 3 Mounting Blocks. I used a combination of my router table and DIY Disk Sander, but you could again just use a sander. It is purely an aesthetic step and small detail.
Optional Video: Turning an Angle Grinder into a Disk Sander
Step 9e: Take care with this step, you want the wheels as close to parallel with the Gate as possible for a smooth rolling action. Clamp the Mounting Blocks in place to the underside of the Gate and use your drill to extend the mounting pilot holes at least 25mm / 1". Grab some 50mm / 2" galvanised screws and secure the blocks to the Frame.
Step 9f: Screw your casters into the pre-drilled pilot holes, flip the gate, and give it a test roll! Be careful as by now the gate will be getting pretty heavy.
OK time to get some decking oil, protect and pretty it up.
Step 10: Preparing and Oiling the Gate Timber
While you could call this whole step optional, your gate will last much longer with a coat of something on it. You can paint it, stain it, oil it, do whatever finish takes your fancy. As this is decking material (and I had to match my brother's existing privacy screen) I went with water-based decking oil, Cabot's Aquadeck. (A similar product I can see in the USA is Owatrol Aquadecks).
Step 10a: Remove the casters, we don't want decking oil on them.
Step 10b (Optional): I used new Merbau decking which is a very resinous hardwood. It's very weather resistant but one drawback of it is it will leech bright red tannins for a long time when wet unless pre-treated. If this is something you need to consider Click here to check out my video on how to Pre-treat resinous woods before proceeding. You'll thank me for it later as tannin stains are nearly impossible to remove.
Step 10c: Apply the recommended number of coats of your chosen finish as per the instructions on the side of the can and set aside to dry. Don't forget to also do the Guide Box.
Step 10d: Re-attach the casters.
TIP: Decking oils should be reapplied with a touchup coat every year to maintain their protection, so don't worry if you have leftovers, you'll need it in 12 months to keep your hard work looking its best.
Step 11: Install the Guide Box
Now, this step may vary a little for you depending on where you are installing your gate. I was using the back of the house and had to deal with bricks. Your life may be easier if you are just screwing into a wooden deck fence or other wooden structure. The main difference is if you have masonry to deal with, you'll need a Hammer Drill (and Masonry bits) to get through the bricks, a normal drill will struggle a lot.
Step 11a: Stand the gate in the "Closed" position and pop the Guide Box on top where it will attach to the wall/fence. Lift or shim the Guide Box up roughly 3mm / 1/8" and test the gate slides smoothly underneath without binding or jamming. Mark the height with a pencil once happy, then double-check, you really don't want this too low!
Step 11b: Remove the front face of the Guide Box (this is why we didn't glue it on earlier.)Place a spirit level on top (there's one on your Combo-square) and line it up level to your mark. The end of it should also be flush with the passage opening. Using your drill while holding the Guide Box firmly against the wall, make 3 quick marks through the pre-drilled mounting holes on the wall.
Step 11c: For wooden surfaces, simply extend your pilot holes to an adequate depth. For masonry like my bricks, using a 3mm / 1/8" masonry bit, set your drill to HAMMER TIME... I mean mode, and extend the pilot holes to the depth of your wall plugs. Then change bits to the appropriate width of your plugs and clear the holes again. Use a hammer to tap the wall plugs in.
Step 11d: I like to start all 3 mounting screws (I used 50mm / 2" screws) until they just poke out the back of the Guide Box Cleat. Then you can easily line them all up with the wall plugs/pilot holes and drive them home.
Step 11e: Clamp the face back on the Guide Box and with a long driver bit replace the pocket screws. This can be a little tricky.
TIP: If you just can't get the drill at the correct angle, a screwdriver will work fine.
Step 11f: Slide the gate all the way through the Guide Box, give it a few tests runs and we are nearly done...
TIP: You DO have enough room to slide the gate in right!? If not, don't panic! In the situation where there is not enough room to roll the gate into the Guide Box like I could, simply remove the face of the Guide Box again, Position the Gate correctly, and clamp the face back on the Guide Box. Drill 4 pilot holes at even intervals through the Top of the Guide Box into the Face, countersink and secure the Face with 4 screws. It won't look as clean, but it will get you out of trouble!
Step 12: Install the Gate Latch
There are lots of different styles of latches available, find one at the hardware store that will work in your situation that is not too big for the gate and that won't pop open if puppies bounce against it. I like the style I chose because it will also act as a stop to prevent the gate from sliding into the Guide Box, but will still allow the gate to open all the way.
Step 12a: Close the gate, and find a good position on the back for the latch. Like me, you may need to get creative and screw a support piece of wood in if there is no obvious place already existing.
Step 12b: Follow the instructions on the packet for your particular style of the latch and install. Don't forget to drill pilot holes.
Step 12c: Open and close the gate a few times to ensure the latch engages, and everything is still running smoothly.
ALL DONE! ...just in time too... Who let the dogs out?! (Who? Who? Hoo-Who?) ...God, I'm old.
Step 13: Release the Hounds!
This is where you hope your dogs are like my brother's King Charles Cavilers and not too bright. Let them run free and see what they think of your handiwork. They could possibly jump this if they really wanted to, but these particular puppers are not that clever. (Banner did try to dig under it... through the concrete... he's a bit special). It also acts well as a toddler gate though with those horizontal slats it is climbable so be careful with any regulations in your local area regarding using this as a child gate design.
TIP: One last one... the Guide Box is also now a great place to rest a beverage! (or display some small pot plants)
I hope you enjoyed my very first Instructable and found it clear and useful. I had great fun with this project and it came out really well. It's been in place nearly a year now, still looks and works great, and there have been zero Puppy Escapes.
If you have any questions, need clarification or spot an error, please don't hesitate to contact me.
I release regular woodwork and DIY content on myYouTube Channel - Fixit Fingersincluding lots of content for beginners. I'd love to have you come check it out and join me.
Otherwise, you can see what I'm up to in between videos on my Instagram @FixitFingers and Fixit Fingers on Facebook.
Cheers! James(as well as Bruce, Banner & Max)
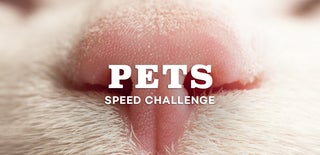
Participated in the
Pets Speed Challenge