Introduction: DIY Subsonic Wind Tunnel - Lift/Drag Testing - for RLoop Project
Who is rLoop?
rLoop is a non-profit, open-source, online think tank. Our goal is to democratize the Hyperloop project through open-source collaborative design and development. We were recently selected by SpaceX as the 'Best Non-Student Team' at the Hyperloop Pod Design Competition, and were among 22 teams selected to manufacture our pod design to test at a track at SpaceX facilities. You can read more about our vision for the future of transportation on our website, our facebook, our twitter, and our subreddit. You can also see extracts from our Final Design Briefing here (the full package is going to be released with errata shortly).
What is the Hyperloop?
Hyperloop is a high-speed transportation system initially proposed by Elon Musk in 2013. The concept uses safe and reliable ground based transit at supersonic speeds to traverse large distances in a superior method than current modes of transportation. A pod carrying passengers and/or cargo is levitated inside a partially-reduced-pressure tube, eliminating rolling resistance and greatly reducing air resistance. To accelerate its development, SpaceX is hosting a competition for engineering teams to design their own hyperloop pods and test them at a SpaceX facility in Hawthorne, California, in the summer of 2016.
For the purpose of validating our CFD results, we wanted to build a wind tunnel and test a 3D print of an iteration of our pod design. This instructable outlines the design, construction, and results of our subsonic wind tunnel!
Step 1: The Design
We required the wind tunnel to be effective, but we also had to build quickly. While I had a fair bit of space available I didn't want to permanently devote it to the wind tunnel, so the ability to dismantle and transport was part of the design.
This design is for an open-return wind tunnel as described here, which is the same style as the original Wright Brothers wind tunnel. It has a fan at one end to draw the air in to the tunnel and to pass over your model. Sensors are mounted to tell how the model reacts: one sensor to measure lift, one sensor to measure drag. It is made up of three sections:
- The Settling Chamber/Contraction cone. This is located at the front of the tunnel and used to force a large volume of air through a small opening in order to increase the wind velocity. It incorporates some egg-crate and mesh to reduce turbulence of incoming air.
- The Test Section. This is where the model is mounted on the sensors. In order to allow visibility, it is made out of acrylic.
- The Diffuser/Drive Section. Located at the back of the tunnel, the diffuser keeps the air moving smoothly and slows it down as it extis, while the drive section is where the fan is housed.
This design totals 8'-0" in length, with the settling/contraction cone being 2'-0" in length, the test section being 2'-0" in length, and the diffuser/drive section being 4'-0" in length. Each section is built separately and attached via springs to the test section - this way they can be pulled apart for storage/transport.
Step 2: Design Measurements
1. Settling Chamber/Contraction Cone
This section forces a large volume of air through a small opening in order to increase wind velocity in the tunnel. According to the book "Low-Speed Wind Tunnel Testing", the optimal area ratio from front to back is 7:1, so the inlet will measure 32" x 32" and the outlet will measure 12" x 12". The length will be 2'-0".
2. Test Section
This section houses the test model and the sensors to measure for lift and drag. To interface with the Settling Chamber and Diffuser, it will be a rectangular prism measuring 12" wide and 12" high with a length of 2'-0".
3. Diffuser Section
This section houses the fan and wind speed sensor. Again, based on information from the book above, the drive section (large end) should be 2 to 3 times the area of the test section (small end of diffuser), with best results if ratio is 2:1. As a result it is easy to calculate the drive section at 17" x 17" (289in^2 : 144in^2 is almost exactly 2:1). This section will be 4'-0" in length to give the entire tunnel a length of 8'-0".
4. 3D Printed rPod
The 3D model printed is 1:25 scale. This represented our initial 'bullet' rPod iteration.
Step 3: Materials
A basic list of the materials needed:
- Qty:1 - Plexiglass Sheet - 2'-0" x 4'-0"
- Qty:1 - Plywood - 4'-0" x 8'-0" (thickness should be 1/4" or greater)
- Qty:1 - Plywood - 17" x 17" (likely cut from a larger board - I cut a 24"x24" board down)
- Qty:1 - Fan with blade diameter of 14" and entire diameter no greater than 17", CFM rateing between 1600 and 2000, designed for gable mounting. I used this one.
- Qty:4 - Plywood - 2'-0" x 4'-0" (thickness should be 1/4" or greater)
- Qty:2 - Egg crate mesh board
- Qty:1 - Wood corner guard - 8'-0" in length
- Qty:1 - Aluminum Screen - approximately 36" x 48"
- Qty:1 - Personal fan
- Qty:1 - Adhesive Rubber Gasket - Minimum 8'-0" in length
- Qty:8 - Springs
- Qty:8 - Small L-Brackets
- Qty:8 - Screw eyes
- Qty:1 - Threaded rod compatible with load cell sensors
Peripheral items include silicone caulking, nuts and bolts, screws, wood glue, staple gun.
For testing, two 5 kg load cell sensors were used with a Phidgets Bridge Wheatstone Bridge Sensor Interface. Then a threaded rod was used to mount the sensors and the test model.
Step 4: Test Section
I started the build with the Test Section.
ONE
Cut the large plexi glass board into four portions measuring 1' - 0" by 2' - 0". If you can have it cut where you bought it, great. If not, you'll need a cutting tool to score along the measured cut lines and then bend the glass to crack it along the score line.
TWO
Connect the boards using silicone caulking to make a rectangular prism. Hold the pieces together lengthwise and perpendicular so they form a right angle at the corner, apply caulking, and hold 5-10 minutes to ensure adhesion. I did two sections separately as the silicone will take some time to dry.
THREE
Once the boards are caulked together they should be left standing on their 1'-0" edge while they dry.
FOUR
After each individual section has dried, attach the two sections together using the same methods described above. Make sure to form right angles at each piece, the test section is quite important so take your time and do it right!
FIVE
After the entire section is dry we'll need to reinforce it to improve structural integrity. We'll be using the L-brackets to do this. Measure the drill points on the test section where you will be mounting the brackets - each bracket should be the same distance from the edge (I measured 2" from the edge of the test section to the edge of the bracket, then marked my drill holes). Once all holes have been marked, carefully drill the holes by making a pilot hole first for accuracy and then a proper hole to accommodate your bolt.
SIX
Attach the corner brackets by putting the rounded head of the bolt on the inside of the test section and the nut on the outside. This will minimize disturbance of the air flow as well as serve as mounting points for the springs when we connect all the sections together.
SEVEN
Once all the boards are reinforced, you have completed the Test Section! A base will be made later to accommodate the sensors and to facilitate interface with other sections.
Step 5: Contraction Cone
I followed the test section with the contraction cone build.
ONE
Cut your 2' x 4' plywood board into equal trapezoidal shapes, measuring 32" by 12" by 2'-0" long.
TWO
Connect the boards to each other one by one, using wood glue at first and then a nail gun to secure. Remember you want them to be as flush as possible to minimize air flow disruption. I went over the outside seams with silicone caulking to ensure air tightness.
THREE
After allowing the assembly to dry, i used pieces of the wooden corner guard to reinforce further. Cut the wooden corner guard into 1'-0" lengths and you should have 8 pieces. Use four here.
FOUR
Once it is sturdy, you will need to build a base to elevate the 12" x 12" section so that it is parallel to the ground. I used scrap pieces of wood to achieve this.
FIVE
Now you'll need to build the settling chamber aspect. This consists of the egg crate mesh and aluminum screen to cut turbulence of airflow entering the tunnel. I used the silicone caulking to attach the egg crate to the outer edge of the contraction cone. As I had one piece of egg crate mesh I had to trim it in to three pieces - take care to make each piece line up as best as possible with the others so as not to introduce turbulence in the air flow.
SIX
Attach the screen approximately one inch behind the egg crate mesh. I folded the screen back and used the staple gun to attach, and then used silicone caulking to seal and secure the screen - remember to try to minimize any jutting objects or rough surfaces.
Step 6: Diffuser Section
This is the last section I put together.
ONE
First, I cut a 24" x 24" board down to 17" x 17", to be the drive section where the fan will be mounted.
TWO
Next, centre the fan and trace your circular cut. The fan I ordered came with a template, so that was handy. Just make certain the fan will be mounted in the centre of the board.
THREE
Cut the circle as precisely as you can. I took my time using a jigsaw to ensure as circular a cut as possible.
FOUR
Fit the fan in the hole and make sure it sits well. If you need to open the hole a little more try sanding. If you need to open the hole a lot you may need to use the jigsaw or another tool. Once you are comfortable with the fit secure the fan with screws - the fan I used came with mounting L-brackets and hardware. NOTE: we want the fan to blow the air out of the diffuser section, not in to the diffuser section. Keep this in mind as you mount the fan.
FIVE
Next, cut your 4'-0" x 8'-0" board in to four pieces. They will need to be of equal size and trapezoidal in shape. They should be 12" at the test section end, 17" at the drive section end, and 2'-0" in length. SAVE YOUR SCRAP WOOD!
SIX
Same process as the Contraction Cone, connect the boards together. This time is easier, as you can use the fan/drive section at the base to mount the boards. NOTE: you will need the power supply for the fan to be accessible. For this, I drilled a hole at the base of the drive section big enough for the cable to fit through, then ran the power cable out before mounting to the diffuser boards (visible in video at beginning of instructable).
SEVEN
At the drive section there will be a gap due to the way the boards will mount. This is unavoidable, but can easily be patched with some sealant or lots of silicone. As with contraction cone, run silicone along seam to ensure air tightness.
EIGHT
As with contraction cone, build a base so the diffuser runs along same axis as contraction and test section. I used scrap wood to achieve this. Some measurements should be taken to ensure you are as close to aligned as possible. The diffuser base will be a bit more difficult as both ends will need to be raised, where the inlet of the contraction cone can rest on the floor.
NINE
In order to get an idea of how fast the air is moving in the test section, an economical method is to mount a personal fan just inside the diffuser section (where it would interface with test section). Instead of connecting batteries, wire a multimeter to the fan. Later, as you are testing your fan the multimeter will give you a voltage output. You can use this number to convert to airspeed. Each fan is different so you'll have to determine how to convert voltage output to airspeed on your own ;) Our tunnel had an average wind speed of 42.5 km/hr (11.8 m/s).
Step 7: Rubber Gaskets and Springs
In order to attach each section together and try to make as airtight as possible, the edge of each section was lined with a rubber adhesive gasket. This also serves to compensate for lack of accurate fit.
Peel the back of the rubber gasket, attach to each edge, and cut to fit. Take care to have them mounted such that they do not stick in to the wind tunnel - gasket excess should be on the outside of the tunnel to minimize airflow disruption. Also make sure the corners of the gasket meet with as little separation as possible.
Now we can line all the sections up and connect them with the springs. The springs will mount to the bolt ends on the test section, and I used screw eyes threaded into the contraction cone and the diffuser section to mount.
NOTE: The deadline for submitting the Final Report to SpaceX for the competition was rapidly approaching at this point, so I started taking less photos and less frequently. I apologize for the lack of visuals, but if there's interest I may take more photos to upload at a later date.
Step 8: Sensors
Now that the wind tunnel is complete, you will need to mount your sensors. You want to be very careful and precise at this step so that your readings are accurate.
First, drill a hole in the centre of the base of your test section just large enough to accommodate the threaded rod that will mount your test model to your 'lift' sensor. You want to make sure the rod won't touch the test section even when the fan is in operation.
Next, determine the best way to mount your force sensors to the base of the test section. Again, I used scrap wood to achieve this. One sensor will connect with the threaded rod going vertical in to the test section to measure lift, and the other must be mounted at a right angle and perfectly aligned with the threaded rod to measure drag. The image above gives you an idea of how they should be mounted, but was not my final mounting position. You can see the threaded rod for my drag sensor is not perfectly perpendicular. I also sanded down the sides of the threaded rod for the drag sensor so it was smooth on the end and wouldn't catch on threads from lift sensor rod.
Once you have them satisfactorily mounted, you need to calibrate the sensor before performing any tests. Plug the sensor interface into your computer using a USB. I used a FlowBotics app to set up and record data from sensors. These sensors have a rated output of 1.0+/-0.15mv/V and a precision of 0.05%. To calibrate each sensor, a reading with no force is measured and plugged in to the following equation:
B (offset) = 0 - 5 * Measured Output
To convert the measured mv/V output from the load sensor to the measured force:
Measured Force = A * Measured mv/V + B (offset) Where A is equal to the capacity of the sensor, in this case 5kg.
Another method to check calibration is to define the weight of the model on the rod as 0 lbs/Newtons, then put a known weight on the model (such as a 100g weight which exerts a .98 N force on the model) and define the force measured by the sensor. As this force is pushing downward on the lift sensor, you should define it as a negative number so your test results will come back positive.
Step 9: Testing
Now that we're all set up, we are ready to start testing! I used a FlowBotics app to record all the data to .csv to later use in a spreadsheet. Before starting the wind tunnel and collecting data, make sure:
- Wind tunnel is held together by springs.
- Wind tunnel is air tight such that air can only enter through the contraction cone and exit through the diffuser/fan.
- All equipment is plugged in.
- Force sensors are properly calibrated.
- Model is mounted on the threaded rod in the test section.
- No one is near the fan as there is no safety cover.
Now plug in the fan, record data for certain lengths of time (try to stay consistent), and save your data appropriately. Use a spreadsheet to monitor data acquisition and perform statistical analysis (average force, standard deviation, etc.). Make sure the data makes sense (do you have negative average drag?). If so, you can repeat the process above to test over and over again! When you are done, detach the springs and separate the wind tunnel in to three sections for ease of storage and transport.
Step 10: Thanks!
If you want or need to build a wind tunnel, I hope this little guide helps. It was a fun and challenging little project - as they should be! The results from our testing agreed with the classical predictions for cones and blunt bodies, and we intend to test further iterations of our pod in this tunnel. Improvements will be made to the tunnel, mostly material in nature, to make it efficient for accuracy and repeatability.
Please post any questions you have here and I'll do my best to respond! Also, if you're interested in learning more about rLoop I encourage you to visit our website, our facebook, our twitter, and our subreddit.
Cheers,
Brent
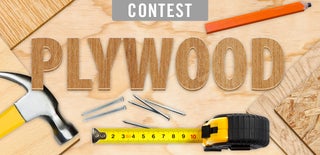
Participated in the
Plywood Contest