Introduction: DONT WALK RUN Traffic Signal Sign
Background
As someone who ran cross country and track in High school, I thought the idea of modifying a DONT WALK/WALK sign to say DONT WALK/RUN would be a cool idea. For me, the sign functions as motivation to keep running, and to never give up. Being in the city of Chicago this summer, reminded me about this old idea and motivated me to make it. The way I completed the sign was a reflection of the tools available to me, the skills I had, and the money I was willing to spend. There are many different ways in which you can make your own sign, I just hope this inspires you to make something yourself!
This was the first time I have ever tried to model an existing item. I modeled my design after several pictures I found online. The look I was going for was sort of a mix of the old signs and the newer ones.
The basic shape was inspired from this newer looking sign Sign example 1
The "lens" i made with the acrylic light cover was inspire by this image Sign Example 2
Step 1: Tools and Materials
Materials used
1. a large plastic kitchen measuring container.
2. Apoxie Sculpt (mileage may vary) one 5 lb tub should do the trick. You can also look at other similar brands.
3. A sheet of Plexiglas/acrylic. Roughly 10" by 10"
4. Clear Prismatic Acrylic Lighting Panel (commonly used to cover lights in commercial buildings) comes in sheets of 23.75 in. x 47.75.
5. Cardboard scraps
6. (optional) liquid plastic
7. CTO (color temperature orange) and CTB (color temperature blue) gels. I bought 1/4 strength of each.
8.Hot glue
9. A light (one rated to be used in enclosed spaces) and preferably LED. I used an 900 lumen 5000k light source.
10. Two wire nuts
11. A power chord (if you can find one with a switch it's even better).
12. Black spray paint (Any brand suitable for plastics)
Tools used
1. Hacksaw
2. Utility knife
3. Sandpaper (80-180 grit) This type of sandpaper holder makes sanding a bit easier.
4. Orbital sander and disc sander (optional)
5. Rust-Oleum Sunbusrt Yellow Spray Paint 12-oz
6. Hot glue gun
7. Measuring tape
8. Drill and 1/4"drill bit
9. Wire strippers
SAFETY TIPS
Alongside of general warnings on product packaging, I'd like to remind readers to:
-Always use a respirator or dust mask when sanding!
- Only spray paint in a extremely well ventilated area or (best) outdoors
Step 2: Creating the Body of the Sign
The Container
To create the body of the sign I used this container.
Rubbermaid Commercial 6306 6qt capacity clear polycarbonate container
If you would rather have a sleeker sign you could use the 4 qt version which has nearly the same opening but, would make the depth of the sign just over two inches smaller..
I used this container because I know it would be strong and already resembled the shape of the signs that I referenced online. It isn't the exact size of the real signs but it was close enough for me and it seemed like a good starting point.
Once I got the container I cut the handles off with a hack saw. I started to cut the lip of the container off too but, then realized that It would make no difference if I removed it or not.
Covering the container in Apoxie Sculpt
To be honest I don't think that this step was completely necessary. I don't think that I needed to cover the whole container with Apoxie Sculpt. I probably could have sanded the container smooth and only used the Apoxie Sculpt for the ridge that goes around the perimeter of the sign.
I always like to work with new materials, and Apoxie Sculpt was a new material for me on this project. It is essentially a two part clay that you mix together 1:1 (by weight) that will cure rock hard in 24 hours. After curing you can drill, sand, and paint the material with normal woodworking tools.
Tips
Its always best to try to get your applications of your clay as smooth as possible. This will require much less sanding and filling later. One cool thing about Apoxie sculpt is that it can be smoothed out with water. I usually put globs of the mixed clay onto the container and then smoothed out the surface with wet hands. You can see from the second picture how rough it will look if you are not patient enough to smooth it out completely. You can also see how nice it comes out after several passes of filling and sanding.
Making the ridge
For the ridge that surrounds the container, I first built up a volume using scraps of cardboard and hot glue. This will make uniformity easier and use less of the Apoxie sculpt. After I liked the look of the cardboard edging I covered it in the clay, trying to make it look as uniform as possible. I found it was easier to focus on one side of the cardboard at a time and to let it dry completely before adding clay to the other sides.
The inner perfectionist in you will hate and love this part. I filled and sanded the whole sign piece well over a dozen times to make it look as uniform as I could get it. This step will take the longest but, It is important to make it uniform and smooth if you want it to look like a painted metal version. If you start to get really bored you can skip ahead and start to work on the other parts of the sign.
Lastly, I drilled a whole for the power chord at the back of the sign. I should also mention that the container I used does not have a perfectly square opening, therefore I decided that the sign looked more natural when the height of the sign was the larger than the width.
Step 3: Designing TheTemplate for the Lettering
Researching online, I found that the font Blue Highway was if not the same, very similar to the front used on the old school DONT WALK/WALK signs. I was able to download the font Here. If you need help installing the .ttf file on your computer you can use this tutorial. Lastly I created a template in Adobe Illustrator. Both the Illustrator file and the Photoshop file I used to get my vinyl stencils made can be downloaded above.
Step 4: Ordering Vinyl Decals
I struggled for a while trying to figure out the best method for making the lettering look as professional and realistic as possible. It would be much easier if I could have used a normal stencil but, I needed to paint around the letters rather than painting the letters themselves like a traditional stencil. I'm sure some of you could cut the letters out and get the spacing right by hand but, I took a different approach.
I remembered a website called Fiver. On this website you can pay people $5 for services and products. For additional money you can get premium features such as rushed shipping etc... On Fiver some vendors sell vinyl stickers. I sent my Photoshop file to courtneythink and she was able to make me a vinyl decal. I ordered two decals in case I ruined one (and I did) and paid for rush shipping. It cost me little more than $15 and I received my decals in 3 days.
Step 5: Painting the Body
The paint I used for the body of the sign is
12 oz. Protective Enamel Gloss Sunburst Yellow Spray Paint
It looks like the right color and I like that It has a nice gloss to it, further selling the effect that the sign is made of metal. The downside of this paint is that as an enamel it seemed to take a few days to fully cure.
The first two pictures are of coats of paint I did with the non spray version of the paint. In Chicago (and probably many other cities) they like to make it hard to get spray paint. Once back home, I was able to get a can at Home Depot for $4. You will get a much more consistent coat with the spray can. Its hard to do (especially for the impatient ;) but, several light coats is way better than one or two heavy coats. Don't try to get full coverage on your first coat. I should also mention, tying a rope to the sign through the power cord hole made it easy to paint.
Step 6: Shaping the Regular and Prismatic Acrylic
As you can see in this picture I referenced, Both the lettering and the "lens" are inset about a half an inch into the main body of the sign.
I was not very confident in my ability to size both the acrylic sheet and Clear Prismatic Acrylic Lighting Panel the exact right size. I attempted to solve this problem by casting the inside of the sign. I turned the body of the sign over and sealed it to a scrap piece of acrylic with hot glue. I then mixed and poured Smooth On two part liquid plastic into the small hole I made in the back of the sign for the power chord. It is important to note that you want to make sure that you are casting your template on a level surface. Just for insurance I bought some universal mold release. You can probably get away without it or by using petroleum jelly or other DIY mold releases. In the end, this method did not work as well as I had expected. Light still leaks slightly from the edges of the sign. It might be better to make a cardboard template and to sneak up on the exact size by lightly sanding both of the clear plastic and the "lens". It was fun using with the liquid plastic though.
The prismatic acrylic comes in large sheets and is very brittle. At first I tried to cut it with a jigsaw (bad idea). Jigsaws are generally too violent and tend to make materials vibrate a ton. The second thing I tried was using a compound mitre saw. It worked surprisingly well and I was able to cut some 10" by 10" squares. You may want to cut several in case you happen to make a mistake. If you don't have access to a compound mitre saw then I would try a circular saw. It may be beneficial to put a scrap piece of wood behind the cut to prevent bending. Another option is to try special plastic cutting devices. I can't say how much luck you will have but. I know they are a cheaper alternative. I cut the normal, clear acrylic into 10" squares on the mitre saw also.
To shape the acrylic and the clear prismatic acrylic lighting panel I hot glued them to my newly casted template. The clear acrylic sheet you can cut with a hacksaw as seen in my picture. The prismatic acrylic however, cracks really easily so you need to sand it to shape. It sands pretty quickly by hand with 80 grit sandpaper but a disk sander makes quick work of the shaping. If you have a bunch of hot glue residue on your pieces, put them in the freezer for a few hours and you should be able to chip the glue right off.
Step 7: Painting the Lettering
When Applying the decals to the acrylic, I found it was best to apply it in the sun or in front of a light so that you can get your alignment correct. After you have applied the decal and taken out any bubbles with a credit card, you can spry paint the acrylic. I used Rust-Oleum 249127 Painter's Touch Multi Purpose Spray Paint, 12-Ounce, Flat Black I did two coats to make sure I covered everything. Once the paint is dry to the touch you can start to peel off the vinyl decal. I used a utility knife and picked at the edge of the letters but i'd recommend using something else so that you don't scrape off any paint. You might find that the sticker left some of the adhesive on the acrylic sheet. You can try to clean it off if you want but, It isn't noticeable once you put the clear prismatic acrylic lighting panel "lens" in front of it. I was very happy with the results and how clean the lines came out!
Step 8: Adding Color!
I decided that instead of the old school orange "DONT WALK" and white "WALK" I would make the WALK part blue like the more modern signs. To change the colors of the words I decided to use film gels. They commonly come in different strengths of CTO (color temperature orange) and CTB (color temperature blue). I decided to order both in 1/4 strength so that I could control the colors easier by layering them. I simply used hot glue to layer them. Super glue might be cleaner and you won't have to clean up all of the hot glue "cobwebs" you made.
Step 9: Installing the Light
For the light I decided to use a spare light that my brother had lying around. It is the type of light that gets recessed into the ceiling. I preferred this type over using a normal light bulb socket because it is very low profile and easy to mount to the inside of the sign (and because it was free! ) I took apart the light and decided to cut off the reflector with an angle grinder to make it more compact, the same could be done with a normal hacksaw if needed.
PLEASE PROCEED CAREFULLY, AT YOUR OWN RISK. WORKING WITH ELECTRICITY CAN BE DANGEROUS AND DEADLY!
First, I clipped the orange connector off of the wires going to the light. I cut the standard E26 male end that would normally thread into a light socket because, I wanted to wire the light directly to a power chord. I used epoxy to glue the light to the back of the sign. To power the light I cut a chord with a switch off of a broken lamp. I poked the power chord thru the back and tied a knot into it to ensure it never pulled out of the sign. Lastly, I striped the ends of the four wires inside of the sign and connect the neutrals together and the Hot wires together using wire nuts. For added security you can tape the wires so that a short never occurs.
Step 10: Affixing the Sign to the Body
To attach the signage to the body I am making a lip using an old bendable ruler that I have. You could also use wood or cardboard or plastic. I simply hot glued the flexible ruler about an inch down inside of the sign, all around the sides. When you are attaching these make sure that you are taking into account the thickness of both the plastic sheets. They added about 1/4" for me but, that may vary depending on the thickness of acrylic/Plexiglas you use. Once the glue is dry you can insert the signage and the "lens". Congrats! you have finished. The next step has a few optional upgrades.
Step 11: Optional Add-ons and Improvements
Reflection
I am happy with how the sign came out BUT, there are still a few more things I want to make it a bit better. I still need to touch up the paint. It has chipped in a few areas. After I am happy with the paint I might spray it with a few coats of polyurethane to protect the finish. Additionally, there is still some light leaking from the edges of the plastic. I will try to use some pieces of foam to make a baffle and update you guys when I find a good solution.
Optional Add-ons
Add faux hinges. No matter what style, almost all of the pedestrian crossing signs have hinges on the bottom of the sign (as seen in the first picture) and mirrored clasps on the top to hold it shut. If you are looking to add more realism you can add them using cardboard or wood and Apoxie sculpt.
Additionally, you could make a stand for the sign with some metal pipe. A couple of elbows and pipe flanges and you can replicate how the signal lights are typically hung.
Lastly you can make the sign blink. This is fairly simple to do, you just need another light, an arduino and duel relay module. Additionally, you would need to make a dividing wall to go horizontally to block the lights from lighting up both the DONT WALK and the RUN part at the same time. Initially, I was going to go this route, and even got the relay working with a light but, decided that I would rarely use the light in my room if it were constantly flashing and ticking with the sound of the relay. If you are interested I will point you to a video I used to learn how to wire an arduino to a relay.
How To Add Relays to Your Projects- The BASICS
Thanks and Happy Making!
I found this short film when looking for reference photos. It's really cool so I thought i'd share it with you all.
Attachments
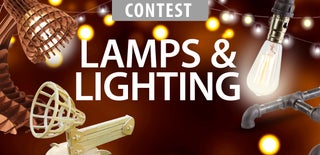
Runner Up in the
Lamps and Lighting Contest 2016
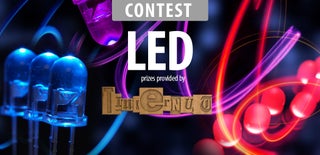
Participated in the
LED Contest