Introduction: DIY Pinewood Derby Track
I am on the constant lookout for inspiration for new projects for my students. The inspiration for this one comes from my work as a Cub Scout Den Leader.
Recently, my son competed in the Cub Scout Pinewood Derby. He designed and built a car using limited resources and tools. He was unaware at the time, but there are hundreds of videos available to show kids (really dads) how to tweak the car design to create the fastest car while staying within the rules.
That got me thinking......what if they had to design the SLOWEST car instead of a fast one?
I thought this would be a perfect engineering design challenge for my students. The only problem....how was I going to test their prototypes without a track?
Attachments
Supplies
In my classes I stress the importance of recycling, reusing, and renewing existing resources. While there are much sturdier materials I could have used, I vowed to create the track out of leftover materials from my garage.
All materials used in this build were things I found in my garage after a recent kitchen remodel. However, I included links to new materials in case you are not as much of a pack-rat as I am.
MDF Boards: Need 4 panels measuring 4'x16" each
Pine Furring Strips: Need 32' total
Hinges: You will need two sets, one set to attach the decline boards and one set for the starting mechanism
1" Screws: approximately 4 dozen. I used old 1.5 in. deck screws and ground each down to 1 inch.
1"x4" Boards: approximately 24'. I used leftover cedar panels from a recent fence project.
2"x4" Boards: approximately 3 feet.
3/8" Wooden Dowels: approximately 1 foot.
Nylon Straps: approximately 3 feet.
3D Filament: I really like that PolyTerra PLA comes on a spool made from recycled materials.
Tools:
Drill with bits
Screw Driver
Brad Nailer
Stapler
Miter Saw
Router
3D Printer: I use the Lulzbot Sidewinder 747
CURA (or any 3D slicing software)
Step 1: Step 1: Make Your Cuts
I started by making 2 identical panels for the end of the track. The following cuts were used to create both panels:
Two 16" x 4' MDF panels
Four 4' lengths of pine furring strips
Six 16" lengths of 4" x 1" boards
The foldable upper half of the track is much more complex. Below are the cuts I used. I recommend referencing the attached photos to see each of the pieces in detail.
Two 16" MDF panels
Four 4' lengths of pine furring strips
Two 16" lengths of 4" x 1" boards - one for the starting mechanism (A) and one to guide the spine into place (B)
Two 11.5" lengths of 4" x 1" boards - These go on either side of the support spine (C)
Nine 6" lengths of 4" x 1" boards (D)
One 4' length of 4" x 1" board - to be used as the support spine (E)
Two 6" lengths of 2" x 4" boards (F)
Two 11.5" lengths of 2" x 4" boards (G) (to attach the guide straps)
Step 2: Step 2: Assemble the Lower Panels
I will do my best to describe the assembly process, however, I highly recommend looking at the pictures for additional clarification.
I started with the two lower panels. I lined up the furring strips 5.5" apart and 3.5" for each side. I used a brad nailer to hold these in place and then went back with countersunk 1" screws. Be sure to fully countersink the screws or they will affect the race cars. On the back I attached the three 16" supports equally spaced apart.
Step 3: Step 3: Assemble the Upper Panels and Starting Mechanism
Again, I recommend looking through the pictures for clarification.
I originally constructed the upper panels without the support spine. After seeing how much the track bowed, I went back and added the support spine. Since then, I only had to wrap the guide straps with masking tape to reduce the friction which made installing the spine much easier.
I used 2" x 4" for pieces (G) and (F) to protect the inner mechanisms when folded.
The starting mechanism went together with surprising ease. Once assembled, I marked out the openings required to allow the wooden dowels through the board, routed out the holes, and then installed the starting mechanism. The only hiccup occurred when I tried to retract the support spine and it hit the starting 'flap' (A). I took a small notch out of the flap, making sure to not remove too much weight, and now it works perfectly. One last piece of advice, be sure to make the starting dowels fold forward to release the cars. Otherwise, you will have very wonky starts.
Step 4: Step 4: Design and Print the Transition Pieces in Fusion 360
Once the panels were constructed, I arranged them together to form the complete track. I then took a piece of paper and traced the gap at the transition point. I uploaded that image to Gravit (you may use any design software), traced it, and created a SVG file.
I uploaded this SVG file to Fusion 360. Using the EXTRUDE feature, I was able to create a 3D rendering of the SVG file. I downloaded the STL file into the CURA slicing software. The resulting g.code was uploaded to my Lulzbot Sidekick 747 and printed using PolyTerra PLA.
Step 5: Step 5: Enjoy Your New Racetrack
I'm very pleased with the way this project developed from an inspired idea to a functioning track.
As I stated earlier, I wanted to see if my students could design the SLOWEST car (capable of completing the race) using limited time and resources. I attached a copy of my project brief and scoring rubric in case there are any other STEM teachers out there looking for a fun project. I threw a few monkey wrenches in the directions (need to include a golf ball 'passenger' and I only allow them three pre-fabricated wheels, they can make more). Please share any cool modifications you make to the directions. I'm always looking to improve.
The kids responded very positively to this project and race day was an absolute blast! Thank you for taking the time to learn about this fun project.
Stay well,
Dave Coster
Twitter: @CosterMath
Attachments
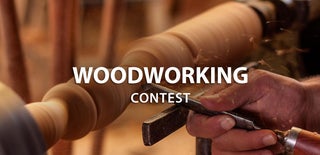
Participated in the
Woodworking Contest