Introduction: Design and 3D Print a Modern and Cozy Reading Light!
This mesmerizing, 3D printed light fixture is made around a pendant light cord and Edison light bulb.
It includes a fully functional, 3D printed ball and socket mount!
In this Instructable, I'll take you through the entire design process in Fusion 360, as well as the 3D printing and assembly process!
You can also purchase the STL files on my website and skip right to the printing and assembly.
Make sure to check out the full design/build video here!
Alright, let's get started!
Supplies
STL Files - https://morleykert.com/shop/3d-printed-light-fixtu...
3D Printer (I have a Prusa i3 MK3S)
Pendant Light Cord Kit with fabric-wrapped cord - https://amzn.to/2PdmLk1
Vintage-style LED Light Bulb - https://amzn.to/33cqC9e
Calipers (These are super handy thing for designing all sorts of 3D printed items!) - https://amzn.to/3hRfH92
White PLA Filament - https://amzn.to/2XTl7IB
120 grit sandpaper - https://amzn.to/3nPNguQ
Gel Superglue - https://amzn.to/3oUDKrK
Four (4) M3x20 screws and Four (4) M3nS square nuts to assemble the ball joint mount. I got these from the spare part kit that came with my 3D printer, but you can also get them at the following links:
M3x20 Screws -https://amzn.to/3nVLA2Q
M3nS Square Nuts - https://amzn.to/39HM9Zc
5-minute epoxy - https://amzn.to/38VdBn9
Needle nose Pliers - https://amzn.to/2N8VdhW
Clamp - https://amzn.to/3ir1t05
2 wood screws (for mounting to wall) - https://amzn.to/3oRY50J
Stud finder - https://amzn.to/38VmYTG
Drill/Driver (for mounting to wall) - https://amzn.to/38Cjbbj
Allen keys - https://amzn.to/3qvP65D
Note: Some of the above links are affiliate links, meaning, at no additional
cost to you, I may earn a commission if you click through and make a purchase.
Step 1: Measure Real-World Components and Import Dimensions As User Parameters
Before doing any 3D modeling, the first step is to take some measurements!
I used my dial calipers to measure the pendant light cord kit, lightbulb and hardware.
Then, I inputted all of these measurements into Fusion 360 as User Parameters.
This will make it really easy to model the light fixture around existing components, and change dimensions if necessary!
Step 2: Model Socket and Lightbulb
After inputting all of the dimensions, modelling the socket assembly and lightbulb was a simple process!
These bodies didn't have to be incredibly detailed - I just used them to size the light fixture and get a sense of what the finished piece would look like.
The socket is a simple cylinder, with one end filleted. I represented the cord attachment by lofting between two circles.
To model the lightbulb, I sketched one half of its profile and then revolved it around a center axis. The most important dimension here is the total length of the lightbulb and socket - I wanted to make sure that the lightbulb wouldn't stick out of the bottom of the lampshade.
Step 3: Create Lampshade Profile
Now we can draw the lampshade profile around the socket assembly.
First, create a construction plane through the center of the lightbulb, cutting through it the "hotdog" way.
I used fit-point-splines to sketch one half of the profile for the inside edge of the lampshade. I made sure to place the sketch inside the screw-on rings, as these are what I will use to hold the lampshade on the socket assembly.
The great part about splines is you can play with the control points and modify the curve to your heart's content!
Once I was happy with the shape, I created a new sketch on the same plane, projected my original curve onto this new sketch, offset the curve outwards by my "ShadeThickness" user parameter, and drew lines to close the profile.
Why offset the curve on a new sketch? Well, if you're not happy with the final lampshade, you can edit the shape in the first sketch. Then, the changes will propagate through the timeline and change the final lampshade! The way the timeline works in Fusion 360, I find that it's easier to split a design into many sketches, rather than cram a bunch of operations into a single sketch.
Finally, I revolved this profile around the center axis to create the lampshade. Again, if you're not happy with the shape, you can edit the spline in the first sketch, and this will propagate to the second sketch as well the revolve command.
Step 4: Split Lampshade Into Rings and Add Spacers
User Parameters strike again!
This time, I created a parameter called "RingThickness" (Final dimension = 0.3 inches).
I started by creating an offset construction plane, "RingThickness" from the bottom face of the lampshade.
Then, I used this as the cutting plane in the "Split Body" tool.
Next, I created a sketch on this plane drew a pie slice from the center of the lampshade, with the outer arc equal to "RingThickness".
Finally, I selected the part of the cross section that is outside of this wedge, and used the extrude tool to cut the lampshade upwards by "RingThickness".
Since all of these dimensions are fully defined by a single user parameter, I could change "RingThickness" at any point to change the height of the rings and the width of the wedges. You can see in the pictures that my first choice for "RingThickness" was too small!
I repeated this process all the way up the lampshade, until I was left with a shallow "cup" at the top.
Step 5: Add More Spacers and Clean Up Geometry
I used the circular pattern tool to create three spacers for each ring.
Then, I joined each set of spacers to the ring below.
Step 6: Model Ball & Socket Mount
This might be my favorite part of the project - a fully functioning, 3D printed ball and socket mount!
First, I modeled a "structural" ring that slips around the light socket between the two screw-on rings. This will connect the light fixture to the ball & socket mount. Then, I added a rectangular piece to the structural ring, making sure to extend it far enough so that the base of the lampshade won't hit the wall.
Next, I created a sphere at the end of this extension, and used the extension to cut a slot in the sphere. I'll print these pieces separately, and attach them with epoxy.
The socket began as a simple box that I created around the sphere.
I split this box through its middle, and then used the press/pull tool on both cut faces to create a gap in the center. This will allow the socket to clamp down on the ball with pressure from the screws.
I created sketches on the top face for the screwholes, countersinks, and outlines of the square nuts. Make sure you add tolerance for a slip fit! This is another great opportunity to take advantage of user parameters, I used 0.02 inches for my "SlideFit" user parameter.
Creating the slots for the square nuts was a bit tricky, but the Section Analysis tool came in handy to access hard-to-reach faces.
I added a backstop to the socket assembly to keep the upper half of the socket vertical. This also creates a spot to add mounting holes.
Finally, I used the "Hole" tool to create two countersunk mounting holes.
Step 7: Time to Print!
I printed the 15 pieces with white Sunlu PLA on my Prusa i3 MK3S.
Everything is printed using 0.15mm layer heights, and the "generic PLA" preset in PrusaSlicer.
I printed the lampshade rings with 100% infill, and the ball & socket/mount pieces with 15% infill.
I printed the lower 10 rings in their final orientation (spacers up), and none of them needed any support material!
However, I printed the top, cup-shaped ring upside down with support material, using the "generate support material on build plate only" option in PrusaSlicer.
The ball also requires support material, and I printed it with the slot facing up.
Step 8: Assemble the Lampshade
Now, it's time to stack!
First, I gave the top of each spacer a light sanding with 120 grit sandpaper. This is just to remove any burrs and create a flat bonding surface.
Starting from the bottom, I glued the rings together with gel superglue, arranging the spacers so that they spiral up the lampshade.
It may look difficult to keep track of which ring goes where, but even with the compound curve that makes up the shade profile, each ring is smaller than the one below it. So, you just have to go from big to small!
Step 9: Assemble Ball & Socket Mount
First, remove the bottom screw-on ring from the light socket.
Then, slide on the 3D printed structural ring, followed by the lampshade, and replace the bottom screw-on ring.
Finally, install the lightbulb.
Before attaching the ball to the structural ring, I gave it a light sanding with 120-grit sandpaper to remove burrs and artifacts from the support material.
Then, I mixed up some 5-minute epoxy, applied it to the slot in the ball, and slid the ball onto the structural ring.
Next, we can install the nuts into the socket mount!
The nuts were a bit of a tight fit, and I found that needlenose pliers, a squeeze clamp and a small allen key were useful to seat the nuts in the correct position.
I also gave the inside of the socket a quick sanding.
Step 10: Mount the Light Fixture!
Finally, I was ready to mount the light fixture over our bed!
Luckily, there was a stud right in the middle of our headboard.
After screwing the bottom socket into the wall, I dropped the ball mount into place, dropped the four screws into the top mount, and got the top mount positioned evenly over the ball.
Then, I gradually tightened the four screws with an allen key, working my way around and tightening each screw a little bit at a time. This way, the pressure is evenly distributed and the top socket stays horizontal. This took a few tries to get right!
I kept tightening and testing the movement until the ball & socket held the light fixture at every angle.
Finally, I ran the cord around an adhesive hook, plugged it in, and this project was done!
If you make this project yourself, I would love to see your results! You can tag me on Instagram @morleykert.
And be sure to subscribe to my YouTube channel for all sorts of other projects!
Thanks for following along, and have a great day!
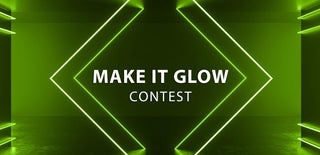
Participated in the
Make it Glow Contest