Introduction: Design and Build an English Wheel
An english wheel is a classic hand-powered shop tool for making two-dimensional curves in sheet metal. Its used for making aircraft skins, car body parts, suits of armor and other applications where a smooth surface on the sheet is desired, something extremely difficult to achieve with a hammer. It is also very useful for planishing; smoothing dimpled or bumpy sheet metal after hammering.
An english wheel seemed like an excellent tool to build. I read up on the theory of operation to get an idea of how it worked, looked at some pictures of wheels on the internet, and I set forth to design and build it. The whole process only took two weeks, start to finish.
It works by stretching the small strip of material that comes in contact with both wheels as it is passed repeatedly between them. This stretching results in the material developing a curvature after many repeated passes. Rolling in different directions and angled results in different effects. You can see the results of my first test sheet, and all I had to go by was what I picked up from a couple of videos I saw on Youtube.
This instructable will be a rough-over of how to do most of the work, highlighting some insights I picked up along the way. You can scale the design ideas to make a benchtop model or a larger floorstanding version. The only thing that changes is the size of the "C" shape body, and the length of the adjustment screw, to accommodate larger work pieces.
An english wheel seemed like an excellent tool to build. I read up on the theory of operation to get an idea of how it worked, looked at some pictures of wheels on the internet, and I set forth to design and build it. The whole process only took two weeks, start to finish.
It works by stretching the small strip of material that comes in contact with both wheels as it is passed repeatedly between them. This stretching results in the material developing a curvature after many repeated passes. Rolling in different directions and angled results in different effects. You can see the results of my first test sheet, and all I had to go by was what I picked up from a couple of videos I saw on Youtube.
This instructable will be a rough-over of how to do most of the work, highlighting some insights I picked up along the way. You can scale the design ideas to make a benchtop model or a larger floorstanding version. The only thing that changes is the size of the "C" shape body, and the length of the adjustment screw, to accommodate larger work pieces.
Step 1: Design
The design is quite simple. The two wheels run against each other and the material is worked between them, with weight from the top one pressing down and pressure applied by the screw mechanism pressing the bottom one up, the sheet metal between is slowly thinned and curved.
I've made drawings of all the complex parts for the project. The ones not shown are just simple cut lengths of a standard size material (square tube, rod, etc) so a 2D drawing wouldn't be of any more help than just a written length. The PDF attached to this step is the design for the overall machine, showing the main lengths and their arrangement. I uploaded it as a PDF because the numbers and details are invisible as an image. The screw in red is just to show how it passes up through the bottom to allow adjustment.
I didn't have the material or lathe capability to make a 8" diameter disk for use as the top anvil, so I recommend purchasing one online or at Harbor Freight. A gigantic bearing would suffice, if you can find/get one. The bottom anvil is a curved bearing from a pillow block, these are perfect for this application because they are hardened and also run perfectly smooth and straight even if they are mounted off-center.
A bit about tools: Without welding, a mill or lathe, this project will be every difficult. Keep in mind that is project is designed for someone with access to machine tools. They don't need to be fancy, but they are virtually required to complete this project.
The following list correlates to the drawings below, and the quantities of each part you will need to make, and what material to make them out of.
In addition to these, you will also need to cut the following lengths of material:
Hardware:
I've made drawings of all the complex parts for the project. The ones not shown are just simple cut lengths of a standard size material (square tube, rod, etc) so a 2D drawing wouldn't be of any more help than just a written length. The PDF attached to this step is the design for the overall machine, showing the main lengths and their arrangement. I uploaded it as a PDF because the numbers and details are invisible as an image. The screw in red is just to show how it passes up through the bottom to allow adjustment.
I didn't have the material or lathe capability to make a 8" diameter disk for use as the top anvil, so I recommend purchasing one online or at Harbor Freight. A gigantic bearing would suffice, if you can find/get one. The bottom anvil is a curved bearing from a pillow block, these are perfect for this application because they are hardened and also run perfectly smooth and straight even if they are mounted off-center.
A bit about tools: Without welding, a mill or lathe, this project will be every difficult. Keep in mind that is project is designed for someone with access to machine tools. They don't need to be fancy, but they are virtually required to complete this project.
The following list correlates to the drawings below, and the quantities of each part you will need to make, and what material to make them out of.
- Guide rings (2) - 3/4" steel plate
- Pipe end cap (2) - 1/8" steel plate
- Lower anvil holder base (1) - 1/4" steel plate
- Gusset (4) - 1/8" steel plate
- Clamp/mounting bracket (4) - 3/16" steel angle
- Top anvil mounts (1) - 1/8" steel plate
- Threaded rod guide (1) - 3/4" steel plate
- Lower anvil holder side (2) - 1/4" steel plate
- Guide rod plate (1) - 1/4" steel plate
- Lower anvil pin (1) - 1/2" steel rod
- Anvil holder guide housing (1) 2" steel square tube
- Two bushings for the top and bottom anvils. These will depend on what you are using for anvils. They just need to be adapted for the holders.
In addition to these, you will also need to cut the following lengths of material:
- 9-1/2" length of 3/4" diameter threaded rod
- 4" length of 1-1/4" diameter steel pipe
- 2" length 1/2" solid rod
- 24", 26.75" and 26" lengths of 2" square tube, 1/8" thick wall
Hardware:
- 5x 3-1/2" long 1/2" bolts
- 5x 1/2" nuts
- 5x 1/2" lock washers
- 9x 1/2" washers
- 4x 8-32 1/2" flat head screws
Step 2: Lower Anvil and Holder
The lower anvil in my project is a pillow block bearing, which has a curved outer edge perfect for this application. The anvil is held on a pin which is placed on a U-shaped holder made of 1/4" steel plate. This holder is welded to a 4" long steel pipe. The other end is connected to another small plate with a rod welded to the bottom of it. This rod, along with the two guide rings at the top, allow this entire assembly to move up and down inside the guide housing when the handle is turned.
At the bottom of the guide housing there is the threaded rod guide. This plate with a 3/4" threaded hole in it is the only part that holds the adjustment rod. The adjustment rod presses directly against the guide rod that is connected to the moving assembly.
At the bottom of the guide housing there is the threaded rod guide. This plate with a 3/4" threaded hole in it is the only part that holds the adjustment rod. The adjustment rod presses directly against the guide rod that is connected to the moving assembly.
Step 3: Top Anvil Mounts
The top anvil is attached to the frame with two pieces made from 1/8" plate. The anvil I purchased came with bearings that required a 3/4" rod, so I turned a bushing to allow me to use the 1/2" bolts that I had. I put washers between the mounts and the anvil. When welding the mounts to the end of the frame, I took the wheel off and bolted the bushing in place so that they would be correctly spaced and lined up.
Step 4: The Frame
This step is just welding all the tube segments, mounting pieces, and gussets together. You can use your preferred welding style, I used MIG since I am best with it. The bottom tube length needs holes drilled through it for the 1/2" bolts that hold the mounting brackets on. You can see them in the picture below.
What you can't see is the other 1" hole drilled through the bottom tube beneath the lower anvil guide housing at the bottom right corner of the frame. This is a hole for the 3/4" threaded rod to pass through from the handle to the anvil holder that it has to move.
In order for everything to line up it is important that the frame is welded straight. If the cuts on the ends of the square tubes are not straight, then the tubes should be clamped and tacked in place at the correct angle and the gap filled with weld. Using a carpenter's square is a definite must. It is also important that the correct tube ends are placed against the correct tube sides or else the two wheels won't line up.
If there is an issue with alignment, one way to iron out any inaccuracies is to weld the three main tube lengths, then mock everything up and find the right place to put the anvil holder guide housing below the top anvil, and tack it in place. Remove everything that you mocked up and complete the remaining welds and gusset welds.
Pipe end caps cover the top-left and bottom-right pipe openings. I left the bottom-left opening uncapped since it will be facing the table, and the top anvil holder covers the top-right pipe opening. The gussets are welded into the inside of each of the four corners to increase rigidity in the frame.
The mounting brackets are drilled with a 1/2" hole to match the holes through the bottom of the frame.
What you can't see is the other 1" hole drilled through the bottom tube beneath the lower anvil guide housing at the bottom right corner of the frame. This is a hole for the 3/4" threaded rod to pass through from the handle to the anvil holder that it has to move.
In order for everything to line up it is important that the frame is welded straight. If the cuts on the ends of the square tubes are not straight, then the tubes should be clamped and tacked in place at the correct angle and the gap filled with weld. Using a carpenter's square is a definite must. It is also important that the correct tube ends are placed against the correct tube sides or else the two wheels won't line up.
If there is an issue with alignment, one way to iron out any inaccuracies is to weld the three main tube lengths, then mock everything up and find the right place to put the anvil holder guide housing below the top anvil, and tack it in place. Remove everything that you mocked up and complete the remaining welds and gusset welds.
Pipe end caps cover the top-left and bottom-right pipe openings. I left the bottom-left opening uncapped since it will be facing the table, and the top anvil holder covers the top-right pipe opening. The gussets are welded into the inside of each of the four corners to increase rigidity in the frame.
The mounting brackets are drilled with a 1/2" hole to match the holes through the bottom of the frame.
Step 5: Paint and Assembly
Since this whole project is made of steel, its a good idea to paint it so it doesn't rust. You'll want to clean the welds using a wire brush to get the soot and scale off, and grind off the splatter if you care how it looks. Getting rid of sharp edges on the welds and cuts is definitely a good idea.
Assembly is pretty self-explanatory. Be sure to use lock washers for the mounting brackets otherwise they might come loose, and this thing is pretty top-heavy. Once the lower anvil holder assembly is in place the guide rings can be screwed into place with the 8-32 screws.
Assembly is pretty self-explanatory. Be sure to use lock washers for the mounting brackets otherwise they might come loose, and this thing is pretty top-heavy. Once the lower anvil holder assembly is in place the guide rings can be screwed into place with the 8-32 screws.
Step 6: Operation
How to use: simply hold the material and push it back and forth between the rollers. You can push down on the sheet while you roll to control how quickly the process goes, but the bends in the material will be smoother if you take your time. Please keep in mind when looking at the pictures below that I have never used one of these machines before, I had no clue what I was doing! I was totally winging it but it turned out pretty good for a first time, I feel.
Step 7: Complete!
My machine is designed to be clamped down (instead of bolted) since I need to be able to move it around and off of the workbench. If you want to bolt yours down, simply drill some additional holes in the mounting brackets to bolt to the table with.
Thanks for reading and if you have any questions please let me know.
Thanks for reading and if you have any questions please let me know.
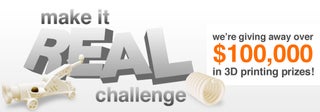
Participated in the
Make It Real Challenge