Introduction: Designing and Building Beautiful RC Airplane
Hello everyone this is my first Instructable but I am excited and eager to share with all of the great people on here how to design and build a remote control airplane. Aviation has been a passion of mine all my life, and has led me to pursue my aerospace engineering degree. As a engineering student I know that I still have much to learn, but that there also a lot that I can teach since I have been flying, building, and designing airplanes for about 10 years.
To design any airplane the first task is always to define what its mission will be. This will be the guiding force behind all research that is conducted and all design choices that will be made. For me I choose to design a fighter styled after the great piston engine fighters of WW2. Therefore my research began with finding various parent aircraft to look at for design inspiration. These included the P-51 Mustang, BF-109, P-40, Spitfire as well as several WW2 fighters turned racers. These aircraft were all designed in different environments worlds apart and yet were effective in their mission through unique solutions.
This Instructable will go through the design process as applicable to many different airplane configurations, and the trade offs associated with different designs. I will then show how I built my airplane showcasing the many different wood working and fiberglassing techniques required to build a similar airplane. From this Instructable you will see all of the techniques used and the challenges overcome to build a beautiful airplane. This Instructable should therefore be considered a reference of various building techniques, that will allow a moderately experienced RC enthusiast to design and construct a custom RC airplane. I hope that this will provide the knowledge and serve as a guide to anyone designing and building a custom airplane.
9-13-2015 UPDATE
I have finally had to opportunity and the nerves to fly the airplane. I have linked a video of the maiden flight in the last step, and am please to say she flew beautifully. Thank all of you for your support and kind reviews of this instructable.
In Regards to the Epilog VI Contest
This Iinstructable is entered in the Epilog VI contest to win a laser cutter. If I were to win a laser cutter it would provide me with the ability to expand my craft and share it with others. Designing and building has always been a passion of mine, and a laser cutter would allow me to turn my ideas into reality very quickly. A laser cutter would be my most prize piece of equipment in my toolbox.
In Regard to the Remote Control Contest
The macbook and the GoPro would go a long way in ensure this airplane will reach its full potential. Just think how awesome it would be to have a GoPro mounted on the wing of this airplane cruising around at 80mph. It would complete this airplane.
Step 1: Mission Planning
The first step in designing an airplane is always determining what the airplane will be used for.
Examples of missions could be
- Training
- Acrobatics
- Racing
- Gliding
- Scale
Additional considerations could include size, budget, time to build to name a few.
Step 2: Airplane Definitions
- Aileron-Control surface on the outboard wing section to control roll
- C- The discharge rating of the battery
- Canopy-Covers the cockpit of the airplane
- Chord- Then length of the wing when measured from leading to trailing edge
- Chordwise- In the nose to tail direction
- Cowling- To cover to the motor immediately following the spinner
- Elevator- Control surface on the horizontal stabilizer used to control pitch
- Engine Cover- Covers the upper portion of the fuselage flowing the cowling
- Flap- Control surface mounted on the inboard section of the wing to increase the lift and drag generated by that portion of the wing for landing or takeoff
- Former- Members inside the fuselage that provide the cross sectional shape, similar to a bulk head on a ship
- Horizontal Stabilizer- Provides pitch stability for the airplane
- Inboard- Towards the center line of the airplane
- Leading Edge- The front most part of the wing
- mAh- Milliamp hour a measure of battery capacity similar to fuel tank size
- Main Gear- The landing gear designed to support the majority of the weight of the aircraft
- Pitch- The nose up / nose down orientation of the airplane, rotation about the wing of the airplane
- Outboard- Toward the wing tips
- Rib- Provides the airfoil shape to the wing
- Roll- Rotation about the centerline of the airplane
- Root- the inboard most section of the wing
- Rudder- Control surface on the vertical stabilizer to control yaw
- Span- length of the wing from tip to tip
- Spanwise- The direction going from wing root to wing tip
- Spar- the central structural member in the wing, designed to carry the bending load produced by life
- Spinner- The cover that goes over the motors driveshaft and propeller hub to give a streamlined shape to the nose
- Tail Gear- The gear positioned on the tail of the airplane to allow it to be steered on the ground. Generally on RC airplanes it is linked to the rudder
- Tip- The outermost portion of the wing designed to streamline the end of the wing.
- Trailing edge- The rear end of the wing
- Vertical Stabilizer- Provides yaw stability for the airplane
- Yaw- Turning right to left as in a car
Step 3: Research
Once a type of aircraft has been chosen it is wise to look to the past to see what others have done before. Parent aircraft are aircraft that are similar to the one that is being designed. These airplanes will allow you to see what configurations are common for the mission. Additionally they can help provide a starting point in the general shape and sizing of the various surfaces on the aircraft.
Step 4: Configuration
- Configuration
- Conventional- Wing produces the entire lift for the airplane plus the lift required to balance out the negative lift being produced by the tail. Efficient because the larger main wing is more efficient than the smaller tail at producing lift
- Canard- Both the wing and the canard produce the lift for the airplane. The canard will often stall before the main wing, and will therefore require a larger wing than a conventional wing since the wing will not be able to reach its highest lift coefficient before the canard stall.
- Delta-efficient for high speed flight. The wing can reach higher lift coefficients since a vortex will roll over the leading edge, this occurs at high angles of attack.
- Flying wing- The tail is integrated into the wing. This is achieved by means of using reflexed airfoils to counter the airfoils nose down pitching moment. Yaw control can be obtained through use of a drag rudder or through wing tip rudders if the wing has sufficient sweep. Flying wings are very sensitive to the location of the center of gravity.
- Wing- All wing characteristics are considered with no wing twist. Wing twist will change the lift distribution across the wing, and also the stall characteristics
- Rectangular- Easiest to build since it will have the same shape along the entire span. This wing shape is very forgiving and will stall from the root outward.
- Tapered- A slightly tapered wing will be more aerodynamically efficient than a rectangular wing. It may be more challenging to build based on the desired taper. This wing will stall from the midsection and move in towards the root and out to the tip.
- Elliptical- Planform of minimum induced drag(drag from lift). Fabrication is difficult since all ribs are different sizes and do not uniformly change in size. Complex curves will develop on the aircraft skin that will be difficult to cover. Just think how few commercial and military airplanes have use this planform. This wing will stall violently all at once.
- Double or triple tapered wing- Used to increase the efficiency of a tapered wing by making its lift distribution closer to that of an elliptical wing. Stalls similar to an elliptical wing.
- Tail
- T-Tail- Raises the tail above the downwash of the wing, and away from possible ground hazards. This type of tail requires a reinforced vertical stabilizer since it must take the loads from the horizontal stabilizer as well as the rudder
- Cruciform tail- Raises the tail partially above the base of the vertical stabilizer for many of the benefits of the T-tail but with reduced structural loads.
- H Tail- Excellent for twin boom configurations or for when increased vertical stabilizer area is required.
- V Tail/ Inverted V- Less efficient than a conventional tail since lifting forces are pointing in a direction other than the desired on increasing drag during maneuvers.
- Conventional tail- The standard for most airplanes. Efficient and light this is a good choice in most applications
Step 5: Construction Techniques
- Composite- constructed from materials such as carbon fiber, Kevlar, or fiberglass this allows for very strong and very light airplanes to be fabricate. However the time and cost to produce a one of a kind airplane can be restrictive. Furthermore this technique will require specialized tools and processes for constructing molds and parts. Radio interference even with modern 2.4 ghz transmitters can be in issue for aircraft utilizing carbon as a primary building material.
- Traditional wooden- Requires only basic tools for a basic airplane. Material cost can be reduced along with time since the material is easy to work with and commonly available. Additionally since the required techniques have been used for many years an abundance of information exists on the subject from build to covering the model.
- Foam- Fast to build and durable, however the airplanes are generally heavier since the foam requires substantial reinforcements to to be able to with stand the flight loads of a substantially sized airplane.
Step 6: Sizing
The sizing of the airplane depends on the objective of the airplane design. This can include construction techniques, transportation to and from the flying site, flight capabilities such as range, ability to handle wind, runways (water, grass, paved, hand launched….). These are just among the factors that will set the size of the aircraft.
From this point sizing becomes an iterative process of working with the components for which the weights are known, ie electronics, and then working to take a first guess of what the airframe will weigh. This can be difficult to do so it is best to itemize the components and then work to build up an entire airplane. For example the weight of the wing could be approximated by approximating the weight of the material that will be used to make the spar, then guessing how many sheets of balsa it will take to build the wing ribs, and cover the wings. Additionally components such as the leading edge and possibly a drag spar must be considered. It is best to have some of the materials on hand at this stage because it will allow for accurate measurements of weights.
Step 7: Stability
To have a successful airplane it is paramount to calculate a few stability terms to ensure that the airplane will be stable and thus flyable. They are a fast to check and are worth calculating rather than just eyeballing the design. I have provided the values I calculated for the airplane I designed.
- The first term is the to be found is the mean aerodynamic cord (MAC). It can be found geometrically by adding the root cord in front of and behind the tip, and also by adding the tip cord infront of and behind the root. These points are then connected to make an X. The cord length at the intersection of the X is the MAC.
- The aerodynamic center of the wing section is simply 0.25 times the MAC.
- The aerodynamic center must be found for both the wing and tail surfaces.
- The neutral point of the aircraft must be found next. It is used to determine the location of the center of gravity of the airplane, and is calculated with the aerodynamic center.
- Next the static margin of the airplane must be determined. The static margin is a measure of stability of the airplane, the higher it is the more stable the airplane, and the lower the less stable. However if the airplane is too stable it will not be maneuverable and thus not controlable, and if it is too unstable then it will be to maneuverable to be controllable by a human. Therefore for most aircraft it ranges between 5 and 15 percent.
- Lastly the tail volume coefficients should be calculated. These terms are used to compare the effectiveness of the tail in reference to the size of the wing and the distance the tail is from the wing.
- The tail volume for the vertical tail generally ranges between 0.35 and 0.8
- The tail volume of the horizontal tail generally ranges between 0.02 and 0.05
Step 8: Electronics
- Transmitter- The controller held by the pilot and used to broadcast the radio signals to the receiver on the airplane.
- Receiver- Receives the signals sent from the transmitter and relays them to the servos and esc.
- Electronic Speed Controller(ESC)- Controls the power going to an electric motor(throttle).
- BEC- Reduces the voltage from the flight pack to a safe level for the receiver and other radio equipment to operate on.
- Flight pack- The main battery pack used to power the motor and possibly the BEC
- Receiver Pack- A battery pack separate from the flight pack that is used only to power the receiver and servos. It adds a level of safety rather than using a BEC built into a ESC which could fail if the ESC fails.
- Motor
- Brushless- most commonly used on remote control airplanes. These motors has increased efficiency over brushed motors do to reduced friction and increased electrical efficiency.
- Brushed- Older type of motor, commonly used on cheaper beginner airplanes and in very small applications such as micro helicopters
- Servos
- Analog- Cheaper and sufficient for all but the most extreme cases
- Digital- By using a faster frame rate these servos are able to provide increased speed, torque, and accuracy. However this comes at the price of a higher current draw, and the BEC or receiver pack must be carefully sized for the number and size of servos being used
Step 9: Weight Estimation
This is a critical step in the planning of your build. It will tell you if the design and sizing is feasible or if the design needs to be revised. I recommend making a spread sheet to aid in this step since it will allow the design to be iterated quickly(My spreadsheet can be found on the my design process step). First begin with components that are fixed in weight for the airplane such as servos and receivers. Then begin estimating the weight of either the entire airplane and then try to break that over down into the weight of the wing, tail, fuselage, gear, and power system. At this stage the mission of the airplane will determine how much power is required and therefore the weight of the power system. If at this point the airplanes weight has resulted in an excessive wing area then it is time to reevaluate the design, sizing, and fabrication techniques. Additionally at this stage it is important to verify that the take off speed will be acceptable. To do this use the lift equation below and either enter Cl max for the airfoil or a conservative value of Cl which would be in the ballpark of 1.1.
L=1/2*rho*v^2*s*Cl
Step 10: Power System Design
Designing a light and efficient power system is a must for any aircraft to take to the skies. For an electric powered model the best setup that is available is a brushless motor with a lipo battery. However, there are a thousand possible combinations leaving us with the question of where to start.
- Determine the level of performance that you desire out of the airplane. From here there are general guidelines for how many watts of power per pound are required. Check out the link below for the most common rule of thumbs
- Once the power required is found the next step is looking for motors that are capable of putting out that much power. While comparing it is important to look at the current and power limit to ensure that you will stay within the Spec.
- Brushless motors speed are measured by kv. kv stands for rpm per volt, so a high kv motor will spin faster than a low kv motor. High kv motors are often limited to smaller models and ducted fans. Lower kv motors will produce higher torque but will spin slower, to compensate these often run a a higher voltage. As a general statement to produce the same power a high kv motor will spin a smaller prop faster while pulling a higher current(higher current=lower battery life) compared to a low kv motor that will spin a larger prop much slower and with a much lower current draw but at a higher voltage. The final motor setup is a trade off between efficiency and battery size.
- I highly recommend using a motor calculator to find the performance of the motor prior to buying it. Ecalc is a easy to use subscription web app that contains many motors and propellers and allows you to essentially try different combinations before ever buying one. This will also tell you the current draw of the setup you have chosen as well as thrust measurements.
- An ESC must be selected that can handle the desired voltage and current of the motor. Additionally if the airplanes electrics will be powered off of the BEC built into the ESC, then it is important to ensure that it is capable of providing sufficient current for all of the servos. Be sure to oversize the ESC by at least 20% to provide a safety margin for operation.
- Lastly the battery must be selected. Selecting too small of a battery for the application is dangerous and will result in damaging the batteries cells on the of best days. Lipo batteries come rated by the number of cells in series, ie higher "S" count the higher the voltage. The capacity of the battery is rated in mah, and the discharge rate in C. To find the max current able to be extracted from the battery take the capacity in mah divide by 1000 and then multiply by the C rating. Be sure to add a margin of safety in the discharge rate because some batteries are "overrated" and as cells age performance is lost. Lastly never over discharge a lipo battery and always "break in" a new battery by being gentle during the first 10 flights.
Step 11: Tools
- Razor or x-acto knife
- Razor saws with various tooth count
- Coping saw
- Sanding bars
- Sanding block
- Rotary tool
- Drill
- Rulers
- Gloves
- Pliers
- The flattest table you can find
- Printer
- Squeegee (clam shell packaging works great)
- Scale (optional)
- Soldering iron
- Heat Gun
- General hand tools
Step 12: My Design Process
From the outset I knew that I wanted to design a warbird that was different from all those that came before it to make it one of a kind. I also knew that I wanted to make it fully sheeted with balsa and fiberglass, because I love the look of wood. Additionally, I wanted to include retractable landing gear to not only reduce drag, but also to make the airplane look more complete in the air. From the outset these requirements made it the hardest but most rewarding airplane that I have ever designed and fabricated. I encourage anyone who has been flying to try to design and build at least one airplane of your own, whether it is simple or complex it is a great learning experience. Below is the preliminary steps I took to design the airplane.
- Sketch the airplane- First I drew my preliminary design sketch on graph paper without any dimensions. This allows you to scale the sketch to any size that you want and will allow the wing area to be found for different wingspans.
- Weight estimation- Once the preliminary wing area was found I then started making a weight build up of all of the major components. This stage was very much a reality check. My initial plan was to have a 45 inch wingspan however with the components, and the weight of the wing sheeting I quickly found that the airplane would have too high of a wingloading. Therefore I re-scaled my preliminary drawing to have a 60 inch wingspan (Wing area=630in^2) not counting the wingtips. This proved to be a much more sound design and have attached the preliminary weight build up spreadsheet to this step. As you can see I measured the weight of the materials that I was using with the following averages listing below. These allowed me to estimate the weight of the various components. For example the weight of the balsa sheeting was found by multiplying the wing area times 2 (for the top and bottom of the wing) by the weight of balsa per square foot. This same method was used on the rudder and elevator. For the fuselage I found the side area and added it to the top area of the fuselage, then multipled that by 2 and then by the weight per square foot.
- Basswood .24oz/in^3
- Balsa 1/32" .42oz/ft^2
- Balsa 1/16" .85oz/ft^2
- Stability-After I estimated the weight I calculated the stability criteria as describe in the stability section to validate that my airplane would be stable and that they tails were adequately sized
- Airfoil selection- Choosing the correct airfoil for the airplane being built will ensure the airplane will fly exactly how you would hope it would. Below is a link to a very simple to use airfoil analysis tool. For the planform that I have designed tip stalling could be an issue since the tip chord is half of the root chord. If at all possible bad tip stalling characteristics should be designed out of the airplane, since tip stalls will result in the wingtip dropping rapidly with no way to regain role control until airspeed is raised. I have achieved this through the use of washout (twisting the wing tips down) and through careful selection of root and tip airfoils. At the root I have selected the S8036 it is 16 percent thick meaning that the wing thickness will be 16 percent of the chord. This will allow for a large spar for increased strength and also for landing gear to easily fit inside of the wing. For the wing tip the S8037 was selected. It is also 16 percent thick. It stalls at a higher lift coefficient and also at a higher angle of attack than the S8036 at the same Reynolds number (Reynolds number is a fluid mechanics term used to compare specimens that in our case are different sizes. The higher the Reynolds number the larger the chord), this means that the root if at the same Reynolds number (same chord as tip) would stall first and thus the airplane would maintain role control. However since the root is twice the chord of the tip it will have twice the Reynolds number, and increasing Reynolds number tends to delay stall. Therefore I twisted the wing tips down so that they will stall after the root.
Attachments
Step 13: Design Validation
Once I had the design completed I wanted to validate the design before putting the time to build one from balsa. To to this I scaled down my plans to half scale. Using this new plan I made a glider version of the airplane out of foamcore. I began by cutting out the side view of the fuselage and then elevator. I then cut a slot into the fuselage for the tail to slide in. Note that the tail is mounting with the leading edge below the trailing edge ie. at a negative angle of attack. For a conventional configuration airplane with a wing in front of the tail this is critical for stability. To hold the two wing halves together I glued some small pieces of wire into the wing and slid them into the other wing half. Then i put the airplane together with packaging tape and added a ball of clay to the nose to get the CG at the desired location.
To test the airplane I threw it around outside beginning with simple tosses to see how it flew and trimmed. Then i began testing to see how it would recover from stalls, for stability the airplane should nose down and pickup airspeed. The scale model flew well even through it did have a high wing loading, and only a flat plate for an airfoil. With this in mind i proceeded on to constructing the full size model.
Step 14: Parts Listing
Attached is a and excel spreadsheet with the specific components, quantities, prices, and location where they were purchased from.
Attachments
Step 15: Order of Building
I have tried very hard to present this Instructable in a clear and logical order. However, you may notice that some pictures that I reference may be further along than described to that point. This has been done to allow similar construction processes to be grouped together since when building an airplane it is very difficult to build the entire wing, and then build the entire fuselage and have them magically bolt together. Therefore the steps my be slightly reordered to maintain a nice reading flow. So be patient and keep reading, the later steps will cover anything that may seem missing including how to finish the surfaces with fiberglass.
Step 16: Wing Structural Design
The wing must be designed to be able to support the weight of the airplane plus the additional forces caused by maneuvering. This is generally accomplished through the use of a central spar which is made up of spar caps, that are the upper and lower flanges on the beam, and the shear web, the thin sheeting that connects the spar caps. Although the shear web is thin it will greatly increase the wings bending strength by unifying the structure. Also very common are smaller drag spars in front of the trailing edge. These can take bending loads as well as serving to increase the torsional rigidity of the wing. Lastly the leading edge may be sheeted back to the spar creating closed cross section beam, this is called a D-tube and it is designed to very efficiently take the torsional loads generated by the wing. Shown are a few very common spar designs.
- The top wing has a I-beam spar, with the shear web located in the center of the spar caps, it also has a sheeted leading edge called a D-tube. The D-tube is designed to increase the torsional rigidity of the wing, and can be added to any of the other spar designs, as well as extended to the trailing edge to create a fully sheeted wing. On this wing the trailing drag spar is simply a vertical support. It also has a simple top hinged control surface, which is easy to fabricate.
- The second wing has a C-beam spar, with a stronger drag spar which is better able to handle the drag loads placed on it. It has a centered hinge, this hinge reduces the gap and thus the drag as compared to a top hinge.
- The third wing has a tube spar, these are usually made from carbon tubes, and are very convenient to build with, if the carbon tube is unidirectional/pultruded then wing twisting can be an issue, but this can be managed with the addition of a D-tube. Furthermore the drag spar is a C-beam which would greatly increase the rigidity of the wing. The hinge is a rounded control surface with the pivot point in the center point of the circular leading edge to minimize the hinge gap and to have smooth edges.
- The fourth wing has a fully boxed spar with shear webbing on both the front and back of the spar. The hinge features the same control surface as the previously discussed wing, but has fairing on the top and bottom of the wings trailing edge to close the hinge line.
All of these are common ways to built the spar and make the hinge line on a RC airplane. These are by no means the only ways to do it, and the various spar designs and hinge types can all be exchanged to create the desired wing.
Step 17: Wing Structual Design Continued
For the airplane that I am building I chose to use a wooden C-beam spar with a solid leading edge and a simple vertical drag spar. The entire wing is sheeted in balsa for torsional rigidity and for aesthetics.
Wood was chosen over a composite tube because the airplane is designed with 2 degrees of dihedral and the joint in the center of a composite tube wing would difficult to make strong enough to withstand the bending load. The I-beam was also less favorable than the C-beam since it would be much more difficult to fabricated, since a slot would need to be made running the length of the spar for the shear web to be installed into. This added complexity is not made up for by a noticeable increase in the strength to weight ratio of the spar. The box beam was not chosen because of the increased weight, however this would not have been more difficult to build and would also have been stronger. The simple vertical drag spar combined with the hinge fairing was selected since the entire wing is sheeted and would be strong enough without any additional supports.
- Spar- The wing spar is designed to carry the bending load created from the lift being generated by the wing. It is not designed to support the twisting caused by aerodynamic forces on the wing, that load is instead carried by the wing skin. This load sharing allows for a light and very efficient structure since each part is supporting the load that it is most efficient at handling.
- The spar caps are made from ¼ x ½ x 24” pieces of basswood. Basswood was chosen for the since it is a hardwood with a very straight grain, furthermore it is very strong for its weight. Convenient sizes can be readily purchased from craft stores which was important due to my lack of sufficient tools to cut strips of a wood from this hard of a material.
- The shear web is made from 1/32” thick basswood sheeting, and is glued between the upper and lower spar caps to join the structure. Shear webbing is absolutely necessary in a wing since it dramatically increases the rigidity and strength of the wing for very little weight.
- The trailing edge / drag spar is made from 1/16” thick balsa sheeting, it helps add to torsional rigidity while also unifying the wing ribs to allow the control surfaces to be mounted to the back of the ribs.
Step 18: Designing Wig Ribs
Creating ribs for a tapered wing can be challenging. A few methods are prevalent the first is cutting out a template for the root airfoil and the tip airfoil. These are then stacked at end of a pile of airfoil blanks and bolted together the whole stack is then sanded. This method is exceptionally good for creating straight wings. However the amount of taper that is achievable using this method is limited because of the angle that is created between the two templates grows with quickly with the difference between root and tip cord. This large angle will make it difficult to assemble the wing later on due to the large amount of excess wood and sharp angles on the edges of the ribs that will need to be removed. Therefore the only method that I had available to me was to make my own templates for each rib and then cut and sand each rib until it was the perfect fit. This is exceptionally challenging on this airplane since the root airfoil is not the same as the tip airfoil so all the airfoils in between those are a combination of those two. Additionally since the wing is fully sheeted the rib shape must be adjusted to compensate for the thickness of the sheeting. Below I present the method that I used to create my ribs templates, it is done using Autodesk Autocad 2012 Student Addition which is my preferred CAD software for designing RC airplane plans in, since I learned it in high school and have used it through out college. The pictures in this step are all labeled with the step that they go along with.
- To import an airfoil into autocad the fastest method that I have found has been to open the airfoil text file with excel so that it will organize the data(these files for many airfoils can be found on the UIUC airfoil database). Then insert a column between the x and y data and fill each box with a comma, and verify that the first point and the last point are in the same location so the the program creates a closed object. Then copy this data back into the txt file and save it. Once it is saved go back and highlight all of the data making sure not to include any headings. Then in Autocad launch the “spline” command and paste when it asks you for the first point. Hit enter and until the command prompt finishes the command. Airfoil data is generally formatted such that the cord is 1 unit as such it is very easy to scale the airfoil to the appropriate size simply by using the desired cord as the scaling factor.
- Draw the airfoils and align them as dictated by the planform. Note that the wing tip(the little airfoil) is set at 2 degree nose down in comparison to the wing root. The leading edge and spars must be carefully sized in the drawing since the end product will be the sheeting on the wing, therefor the the spars must be drawn narrower than they are. It is preferable to make the spars and the leading edge taller than required to make the drawing go smoother. Also the spar notches are located such a way that the entire spar will fit in the rib while remain square.
- Here the airfoil sections are shown at each end before they are lofted together to form the intermediate airfoil sections.
- The wing spar and the sub leading edge are lofted to allow them to be subtracted from the wing later on.
- Now the airfoils are lofted creating the shape of the wing while also having the location of the spar and sub leading edge visible.
- The spar and sub leading edge have been removed using “subtract” leaving the outer shape of the wing, minus the leading edge which is not part of the ribs.
- The wing is then hollowed out using “solidedit” and then selecting “shell”. The wing tip and root were then selected as the faces to remove, and what is left is the wing skin. Therefore the inner wall of the wing skin is the rib shape.
- Now using the “section plane” button at each of the wing rib locations a cross-section of the wing will be generated.
- Then under “section plane” select generate section. With this command the cross sections at all of the stations already made can be displayed by generating a section for ever rib. To aid in aligning the wing ribs during construction I highly recomend drawing a horizontal line from the trailing edge of the wing through the leading edge. This will allow you to correctly align the wing if it is being build with twist and will also help in making the wing straight.
- Again since these templates are actually the wing skin the inside of the innermost line is the correct one to cut on.
- Now with the ribs all labeled using the "text" command they are ready to be printed. Around each page of ribs I have made a print box to allow for easy repeatable printing. The box will not print since it is in a separate layer that is turned off from printing but is still displayed on the screen. I will be printing out all of the smaller ribs on resume paper since it is a heavier stock it will make for a nicer template. The larger airfoils will be printed on regular paper and then reinforced before the ribs are cut
Step 19: Wing Fabrication: Cutting Non-structural Wing Ribs
All of the non-structural wing ribs are made from 1/16" thick balsa wood with the grain running in the cordwise direction to provide rigidity from the leading edge to the trailing edge. I printed the templates that were made in CAD onto resume paper since it is thinker and produces a very nice template. I then put double sided tape on the back of the templates and cut them out, this ensures that double sided tape covers the entire backside and prevents having to cut the tape and wood at the same time with a razor. Once the first wing rib is cut put double sided tape on to the back of it and then stick it on to another piece of 1/16" balsa and cut out another rib, this will yield both the right and left rib.
With the ribs for both wings still stuck together and with the template still attached sand the ribs to the innermost line on the template. I recomend sanding across the grain or in other words through the template, or else the template will tend to roll up or bend instead of sanding. Sanding both the right and left wing together ensures a symmetric wing.
With the rib sets all stacked together it is easy to see why sanding between the root and tip ribs would produce issues. The steep angles made by the tip cord compared to the root cord would leave angles along all of the ribs with the worst being left at the leading edge and trailing edge. This would reduce the accuracy of the airfoil and also cause headaches when trying to build the wing since those angles would need to be sanded smooth across all of the ribs
Step 20: Wing Fabrication: Landing Gear Ribs Stage 1
The ribs that support the landing gear must be very strong since they will be required to withstand the full weight of the airplane, and likely many times that weight if the airplane lands rough. As such balsa would not be able to support the loads experienced by these ribs, so instead this ribs are made from 1/32" thick basswood and 2oz fiberglass to make a composite plywood that is incredibly strong and much less brittle than craft ply wood. The process that is being used to apply the fiberglass called a wet layup since the resin is being used to wet the fibers. These ribs will experience a large load in front of the spar however very little behind it, therefore to keep the airplane as light as possible the front of the rib will be much more heavily reinforced than the rear. Below is the first stage of building the reinforced ribs.
- First cut the rib shape from from 1/32" basswood and sand the rib as done on the previous ribs.
- Trace the wing rib shape onto 2 oz fiberglass leaving about 1/2" around the outside of the ribs as shown in the photos. it is important to have the fiberglass weave running from the leading edge to the trailing edge and from the bottom to the top of the rib. This maximizes the strength of the part by allowing for continuous fibers along the length of the part.
- Prepare a working surface by taping down a sheet of painter plastic to apply the fiberglass and resin on.
- Next prepare the surfaces which will be in contact with the parts as the cure. Here wax paper is covered with packaging tape to create a very smooth and nonporous surface. Then apply release wax to the packaging tape with a paper towel according to the packaging instructions. As a personal preference, I use Megular's Mirror Glaze Mold Release Wax, it works very well with the Z-Poxy finishing resin that I use and once cured the parts very easily separate from any smooth surface where the wax was applied. It also does not leave very much residue on the parts once separated.
- Now that all the surfaces are prepared make sure that there is plenty of ventilation, and that extra gloves and squeegees are easily available. I like to use either playing cards or the plastic from old clam shell packaging as a squeegee because they are either cheep or free and also disposable to avoid the harsh solvents required to clean a reusable squeegee
- Mix the resin which you will be using to laminate the wood and fiberglass with.
- Pour some resin onto the wood and use a squeegee to evenly spread it across the surface. Then remove any excess with the squeegee. This will aid in the fiberglass cloth laminating to the wood.
- Pour some resin onto the fiberglass cloth and use the squeegee fully coat the cloth. The cloth will change from white to a translucent color as it absorbs the resin.
- Squeegee off all the excess resin from the fiberglass cloth, being sure to only run the squeegee with the grain of the cloth.
- Now gently pick up the wetted piece of cloth, the squeegee may be needed to help peel it off of the working surface and place it on the rib blank.
- Squeegee the cloth again this will help to adhere the fiberglass to the wood, again you will see a change in color as the glass bonds to the wood.
- Now pick up the rib and place it fiberglass down on the waxed surface.
- Repeat the wetting process to the rib and to the fiberglass cloth and apply to to the other side of the rib.
- Once all the other ribs have been given similar treatment lay a second waxed sheet on top of the ribs. At this point you can use your hands or a dry squeegee to remove any air bubbles between the waxed surface and the ribs.
- Place something flat on top of the ribs, in my case it was a piece of foam core. Then place as much weight as you can onto the ribs. This will help to adhere the the fiberglass to the sub-straight, as well as squeezing out any excess resin.
- Let the resin fully cure, per the manufactures specs.
- Remove the weight and pull off the waxed surface. If the waxed sheet is not damaged it can be saved to use again.
- Wipe down the fiberglass with rubbing alcohol to remove any wax residue.
- Excess fiberglass around the edges can often be first cut with scissors.
- With gloves, a respirator, safety glasses and plenty of ventilation the remaining fiberglass can be sanded back to the size of the wooden rib. Additionally the entire surface of the rib should be roughed up so that more layers of resin will be able to adhere to the surface.
Congratulations if you have made it this far, you have just completed your first wet lay up, but there are more required to finish this airplane.
Step 21: Wing Fabrication: Landing Gear Ribs Stage 2
The next stage of reinforcing the landing gear brackets is reinforcing the front of the rib from where it attaches to the wing spar forward to where it attaches to the sub leading edge. This is accomplished by adding more layers of wood and fiberglass to turn the rib into a very solid piece of fiberglass reinforced plywood.
- Cut out the pieces of wood which will be laminated on. In my case I added a layer of wood with the grain running vertically and then a piece of wood with the grain running in the cord-wise direction on both sides of the rib. This makes the front 5 plys of wood thick with 6 layers of fiberglass.
- Next cut out the plys of 2oz fiberglass that will be needed for the laminate sandwich.
- Prepare the working surface as before with painter plastic and if reusing the waxed sheet apply a new layer of wax to it for good measure.
- Mix and prepare the resin.
- Coat the leading edge of the rib with resin and squeegee off the excess.
- Coat the wood with the grain running vertically with resin and squeegee the excess.
- Wet the fiberglass and apply to the to side of the wood with the vertical grain.
- Apply the vertically grained piece of wood to the rib blank ensuring that there is resin on the wood block being added to ensure proper lamination.
- Apply the fiberglass to the block just added to the rib and squeegee off any excess resin.
- Wet and apply the wooden block with the grain running in the cord-wise direction to the rib.
- Apply a layer of fiberglass onto the to of the cord-wise grained block.
- Place the fiberglassed side down on the waxed sheet.
- Repeat steps 5-11 to the other side of the rib and to all remaining ribs.
- Apply waxed sheet onto the top of all of the ribs.
- Compress the laminate as done previously.
- Allow the resin to cure and then removed from waxed sheet.
- Clean surfaces with rubbing alcohol.
- With the appropriate safety precautions remove the excess from the ribs. A coping saw can help to get close to the rough shape. It is also possible to carve the excess away with a very sharp razor. Sand to the final shape and rough the surface to that it can be written on easily.
- Using the rib templates determine the correct placement of the spar notches and cut them out using a razor saw, once cut a razor can be used to finely adjust the fit.
- Determine where the cross member must be placed to mount the landing gear on. Be sure to leave enough room for the landing gear to retract fully, as well as enough room in front of the spar to allow the wheels to not hit when retracting. Also it is important to take into account if the wing had dihedral since the gear will then either have to not extend 90 degrees or it will need to be mounted at an angle in the wing, in my case it is mounted in the wing at an angle.
- Once the location is determined a starter hole can be made with a small drill bit in my case 3/16" since the cross member running between ribs are 1/4x1/2".
- After the starter holes are drilled the rest will likely need to be done again with a very sharp razor. This will be time consuming but be patient since these must support the weight of the airplane and be carefully aligned so that the gear will retract into the wing and extend and be straight.
The landing gear ribs are now complete.
Step 22: Wing Fabrication: Building the Center Wing Ribs
The center rib along with the rib on either side of it are reinforced to support the mounting bracket for the fuselage. These ribs are build using a similar technique to the landing gear ribs. They are made with 3 plys of basswood with the center ply having the grain running in the vertical direction. The outer plys have the grain running in the chordwise direction.
- Cut out the rib blanks out of 1/32" basswood with the grain running in the chordwise direction leaving them slightly over sized they will be sanded to final size in a later step.
- Since basswood does not come in wide enough sheets to have the chord length fit with the grain running vertically through it, strips must be joint to create these sheets. Glue strips of 1/32" bass wood together to make a strip as long as the rib with the grain running vertically.
- Cut out the 2oz fiberglass cloth with excess to cover the ribs.
- Prepare for the wet lay up the same as was done for the landing gear ribs
- Lay up the fiberglass on both sides of the rib blank and then place on the waxed sheet.
- Next adhere the vertically grained core onto the the rib blank.
- Apply a ply of fiberglass to the layup stack.
- Apply the other rib blank to the stack being careful to align the rib with the one of the bottom since there will not be much margin.
- Use the same procedure for the remaining ribs.
- Cover with a waxed sheet.
- Compress with weight and allow to cure.
- Remove from the waxed sheet and clean.
- Using the appropriate safety measures cut and sand the ribs to match the template.
- Cut the spar notches using a razor saw.
- Place the ribs on a scrap piece of wood and then drill through them to make holes to run the servo wiring through. Make sure the holes are large enough to fit the standard servo plug through.
At last all the ribs for the wing are made and it is time to begin assembling the wing.
Step 23: Wing Fabrication: Wing Spar
The wing spar is the key structural element of the wing. The spar is the critical load path for the airplane, all loads generated from the fuselage are transmitted through it. As such it is of the up most importance that the wing spar is strong enough to withstand the loads it will be subjected to. The weakest point of any structure is a joint, do not take shortcuts to make it easier at the cost of strength. Therefore I will show how to build joints on the wing spar that will be as strong as the surrounding wood to ensure the integrity of the finished wing. These joints are called scarf joints.
- Make a jig to hold the spar stock while cutting.
- Line up two of the strips and the cut the angle the desired angle. You should use at least a 5 to 1, greater if possible) for the angle. The longer the angle the stronger the joint will be.
- Once the angles are cut then alight the cuts as shown to make the spar a perfect fit for the slot.
- Now use the wing jig to cut the scarf into the ends of the spar caps that will be joined.
- Check the joint of the joint to ensure that the boards do not twist along the joint. if needed correct the joint by carefully sand it down.
- Once the joint fits perfectly then mark the alignment of the joint with a pencil.
- Lay down a sheet of wax paper on a flat table.
- Pull the two haves apart and apply thick CA to the joint, then align the marks.
- Repeat as necessary for the rest of the joints in the spar.
Step 24: Wing Fabrication: Upper Spar Cap Dihedral Break
The dihedral break must be the strongest joint in the airplane because it is in the center of the wing. Therefore the scarf joint should be longer. It is also easy to make it longer because the joint is simply cut at the angle that you want the diheral to be. Note that the angle that is cut may not be the same for the top and bottom of the wings because if the wing is tapered the thickness of the airfoil is reduced. Therefore I recommend waiting until the wing is built to build the other spar cap.
- Using a ruler mark where the cut must be made to get the proper angle.
- Then cut along the line with a razor saw.
- Check the fit of the joint and mark the alignment.
- Put a piece of wax paper done on a flat table.
- Using thick CA glue the two pieces together.
Step 25: Wing Fabrication: Attaching Non Structural Ribs
Now the that upper spar cap has been made it is possible to being attaching the wing ribs onto the spar to make the wing. To make this process a lot easier I drafted a simple wing plan using autocad to build on. The drawing includes the wing spar, drag spar, subleading edge, trailing edge, as well as the location of each rib. While this is not the only way to do this, it does beat drawing a plan by hand or measuring as you go. By printing out the wing plan full size I will have a blue print to build on, which makes building a straight wing much easier.
Note: Wing twist is achieved by mounting the ribs onto the spar at the desired angle, the spar cap does not twist at all.
- Lay out the wing drawing, making sure if you printed it in segments as I did that they are all properly aligned and that the spacing is correct.
- Lay the top spar cap upside down on the drawing using spacers to support it along its length and especially at the center.
- Now transfer the horizontal line from the rib templates to the leading edge of the ribs. This is to allow you to build the wing with the desired amount of twist.
- Apply woodglue to the spar notch of the outermost rib. Then using the trailing edge and the mark on the leading edge mark align the rib so that the mark and the trailing edge are the same height above the working surface. In my case this alignment would give me the 2 degrees of washout that I desired. Once the elevation of the rib is set insure that it is square with the surface of the table, and that it is mounted in line with the ribs on the wing plan.
- Repeat for the other side of the wing
- Apply the inner most non reinforced rib similarly to how the outermost rib was installed.
- Repeat for the other side of the wing
By gluing these two ribs on each wing it is now possible to align the ribs angle of twist without the need to measure the height off of the table. T
- This is done by applying wood glue to the spar notch of the rib and then setting the rib square to the table with a triangle.
- Then verify that the rib is lined up with the wing plan.
- Now that the ribs is in position move to the end of the wing and look down the wing in such a was that the trailing edge of the wing tip is aligned withe the trailing edge of the root rib.
- Now adjust the rib that you are positioning so the its trailing edge is also aligned between these two ribs.
- This is an iterative process so check to verify that the rib is still square with the table, then aligned with the wing plan, and aligned between the root and tip trailing edge.
- Once the alignment is perfect allow the wood glue to set up.
Although this may seem like a tedious process it goes rather quickly since while one rib is setting up you can do a rib on the other side of the wing
Step 26: Wing Fabrication: Attaching Structural Ribs
Since the structural wing ribs on this airplane are a composite laminate of materials, wood glue would be a very ineffective way to attach them to the spar. This is because wood glue is a water based adhesive and would not be able to penetrate the resin to form a secure mechanical bond. Therefore different adhesives had to be used to attach them. Here I will describe how the center wing ribs were attached and then how the landing gear ribs were fitted to the wing.
- Verify the fit of the wing ribs on the spar, these ones can be difficult to fit since the material is so hard.
- Once the proper fit is achieved put on gloves and ensure that you have sufficient ventilation.
- Mix a small batch of 5 minute epoxy. Only a few drops will be needed for each spar notch.
- Apply a small amount of epoxy to the center wing rib and align it on the spar as done previously.
- The remainder of the structural ribs can be done at this point with the exception of the landing gear ribs.
The landing gear ribs must be fitted to ensure that they operate correctly on the airplane. In my case since the landing gear were retracting towards the center of the wing I had to remove material from the inner ribs to allow the landing gear to retract. I recommend waiting until this stage to do this because with the wing starting to come together it is possible to see if the landing gear must be angled inside of the wing. In my case it had to be because the wing had dihedral and my landing gear extends a full 90 degrees, therefore if they were not they would be bent outwards when extended. To do this I retracted the landing gear and repeated trying laying it into the slot that I was cutting until there was sufficient room for it to retract with a about 1/16" of an inch surrounding the landing struct. This was done to ensure that if the gear was damaged or moved during flight it would still be able to open or close. Once happy with the positioning of the wing ribs and landing gear cross members the ribs can be epoxied in place.
Step 27: Wing Fabrication: Lower Spar Cap
The lower spar cap can be challenging to install since it must fit into all of the spar notches in the wing with out being such a tight fit that it actually twists the wing, after all the effort was spent ensuring that it was constructed with the desired twist. The lower spar cap is installed as two separate pieces and is joined in the wing unlike the upper spar cap that was was installed as one piece. Below is how to install and join the two halves of the lower spar cap.
- Make sure that the wing is still being well supported and is not sagging in the center or along the span, if so add a few more supports under the wing. Improper alignment will result in undesired wing twist.
- Test fit one half of the spar cap. Note that I am leaving enough overhang of this spar cap over the center of the wing to attach the other half of the spar to. Things to look for include very tight ribs,very loose ribs, and that the spar cap is fully enclosed by the spar slot in the rib. It cannot be allowed to stick above the ribs otherwise it will show through the wing sheeting.
- Adjust the fit of the lower spar cap by carefully removing material or by adding in shimming material to the ribs until it is a perfect fit.
- The most challenging part of installing the spar cap is that since it is rigid it must be glued in all of the slots at one time. With that many joints its is impossible to hold and support all of them at one time by yourself. Therefore creative means had to be found to hold it in place as the glue set. To do this I positioned pieces of electrical tape and masking tape underneath the wing that were long enough to wrap up and around the top spar cap to firmly secure them in place while the glue set.
- All of the non structural wing ribs should be glued to the upper spar cap with wood glue while the center ribs and landing gear ribs must be glued in with epoxy. While doing this I recommend using a paint brush to paint the wood glue into the spar notches and then mix the 5 minute epoxy and apply it to the reinforced ribs, since the wood glue will take longer to set.
- Once glue has been applied to all of the joints insert the spar cap. Then secure it in place with the tape, and wait for the glue to dry.
- Begin test fitting the other side of the spar cap, in addition to checking and fixing its fit with the wing ribs. It is vital that the joint between the two halves of the spar cap is made to fit as closely as possible because as with the upper spar cap the center of the lower spar will be heavily loaded during flight operations.
- Once satisfied with the fit prepare to glue the spar cap in by placing the tape at the desired locations
- Apply the glue as before, for the connection between the two halves of the spar cap at the center of the wing use epoxy and once the rest of the tape is applied, hold or clamp this this joint until it has set.
Step 28: Wing Fabrication: Sub Leading Edge
The sub leading edge is a 1/4" think piece of balsa that is attached to front of the ribs. Its purpose is to be something for the sheeting to be attached to since sheeting would not be able to make the curve around the leading edge of the wing. It also provided the required thickness to allow the leading edge of the wing to be sanded to the shape of the airfoil.
- Sand the tips of the ribs very gently with a bar sander such that they all have the same angle and are perfectly straight in respect to one another.
- Next cut out an over sided strip of 1/4" balsa from a sheet. To make cutting a long strip of any material easier with a razor simply put double sided tape on the back of the straight edge and it will make the task incredibly easy since the edge will not move while cutting. Also do not try to cut through the material in one pass, because it increases the chances of splitting the wood. Instead make a few light passes to cut the whole way through.
- Use thick CA to glue the sub leading edge to the ribs. I found it is easiest to apply the glue to the end rib and then align the strip with the center rib. Once the glue has dried then apply glue to the next few ribs. Be careful to not bend the ribs that the sub leading edge is glued to while gluing it to new ribs.
- Work gluing sets of ribs until one side of the wing is covered.
- Align a straight edge along the side of the wing that does not yet have the sub leading edge attached, then trace its path on to the leading edge that is attached.
- Cut off and then sand the excess sub leading edge until it matches the path of the other wings leading edge.
- Glue the sub leading edge onto the other wing as previously done.Make sure it's centered as shown in the photos.
- Now that the sub leading edge is attached, begin carving (using a razor or a razor plane) it closer to match the contour of the upper and lower wing surfaces. It should not become rounded in the front, rather it should look like a trapezoid.
- Once the sub leading edge is close to the shape of the upper and lower surface you must prep the wing for sanding. Apply a piece of duct tape along the ribs that it will be sanded in front of. This will protect the ribs and serve as a guide for sanding.
- Using a sanding bar sand the sub leading edge to match the contours, being very gentle and paying special attention to the sound it makes as it sands. Chatter indicates that a rib may not be attached, you will also here a different sound when you begin sanding the tape.
- Remember that the ribs are the correct shape and therefore should not be sanded, the tape ensures that they will not be.
- To get the edges closer a thinner tape may be used such as masking or packing tape.
Step 29: Wing Fabrication: Shear Web Installation
The shear web is made of 1/32" thick basswood and is glued to the top and bottom spar caps, as well as the wing ribs. It is very important that the material used for building this is stiff because it will be compressed when the wing is under load. This allows the spar caps to form a beam rather than being small sticks.
- Cut sheets of basswood with the grain to be slightly wider than the spacing in between the wing ribs.
- Cut the bass wood strips to be slightly larger than the distance between the outside surfaces of the spar caps.
- Sand the side of each piece of shear web until it fits snugly between the ribs on either side.
- Glue the shear web onto the upper and lower spar using thick CA.
- Use a course sanding block to sand, that is narrower than the space between ribs, to sand the shear web down to the height of the top of the spar.
Step 30: Wing Fabrication: Landing Installation
Fitting the landing gear proved to be challenging due to the the wing being rather thin. To add to the challenge the shear web was installed on the leading edge of the wing, this had its own pros and cons. While it did produce a smooth surface for the landing gear to ride on if the alignment is off, it also reduced the size of the already small space it was being installed in. Furthermore I had mis-measured the space required for my landing gear so I had to adjust the size of the landing gear cross members that connected the landing gear to the ribs.
- Set the landing gear inside of the gear rails to see which ribs need to be hallowed out to allow the wheels to retract fully.
- Cut the required ribs so that the wheels are able to fully retract into the wing. Now determine the angle the landing gear will be mounted at.
- The gear can be mounted so that if looked down upon looks like it is slanted toward the front or back of the wing. However doing this will require the angle of the wheel to be adjusted or else the wheels will either point inwards or outwards when extended.
- Once the correct position is found mark one of the mounting holes and drill using the appropriate drill bit being careful to support the end of the wings so that the end ribs are not crushed.
- Place a bolt through through the landing gear into the drilled hole and then drill the remaining holes using the gear as the guide.
- Now that all of the landing gear bolt holes are drilled the landing gear must be shimmed such that is parallel to the ground and thus perpendicular to the ground when extended. This is critical since mounting the landing gear so that it is angled in or out increase the stress on the gear when landing and thus the chances of the gear collapsing.
- Using a piece of basswood carve it down into a wedge to and then sand it until it is the perfect angle to mount the gear straight.
- Once the angle is correct use thick CA to glue the wedge in place.
- Flip the wing upside and drill through the back side of the mounting holes to put a hole through the wedge.
- Bolt the landing gear into the landing gear bracket. On the back side attach the gear with a washer and a nylon lock nut to ensure that the nut never comes off since it would be very difficult to replace and also could get stuck in the landing gear mechanism.
Step 31: Wing Fabrication: Drag Spar and Aileron Construction
To build the ailerons it is easiest to build them while the end of the ribs which will be used to make them are still attached to the wing. The flaps are not being constructed this way since the ribs in that section of the wing are the reinforced ribs that were made for the landing gear. The flaps will be constructed later on. Once the ailerons are constructed the trailing edge will be installed on the rear of the ribs. Lastly the hinge fairing is installed on the upper rear trailing edge.
- Square the wing off on the wing spar in such a way that it will stay.
- Measure from the leading edge back to where the trailing edge/ flaps will begin and mark it on the tip rib and the innermost rib on the flap.
- Place a ruler between the marks and then mark all of the ribs, additionally make the location of the center of the radius being made for the hinge.
- Now use a square to mark the trailing edge of all of the ribs from the bottom to the top, and the mark for the radius of the hinges.
- Cut off of the trailing edges off of the ribs that will not be part of the ailerons or the root section.
- Sand the the beginning of the ailerons so that they will fit tightly in the fairings, look at the photos for an example of what this may look at. Note that the sanding continued passed the hinge center point to make covering easier
- Using thick CA glue the 1/32" balsa sheeting to the aileron ribs. This will make it sanding the other side of the ailerons easier since they will no longer move while sanding.
- Now that the ailerons are secure sand the other side of them to thin then down to fit the fairing that will be installed later.
- Sand the trailing edge of the 1/32" sheeting on the side of the aileron that is covered down to a point from the end of the ribs to the trailing edge of the aileron sheeting.
- Using thick CA glue along the wing ribs to install the other side of the aileron sheeting.
- Cut along the line that makes the end of the wing to separate the aileron from the wing.
- Once the ailerons are separated from the wing drop thin CA into the aileron skin to glue the trailing edge together. Be careful to not add to much or else it will seep through the skin.
- With the ailerons and trailing edges of the ribs removed from the wing carefully sand the end of the ribs until they are all aligned.
- Attach the over sized drag spar made from a strip of 1/16" thick balsa to the trailing edge of the wing using thick CA.
- Use tape to protect the ribs as done on the leading edge to sand the drag spar down to size.
- Determine the size of the hinge fairing that fits the hinge that is being installed.
- Glue on a the hinge fairing using thick CA and again sand it flush with the ribs.
- Position a ruler between the drag spar segments on each wing and mark all of the center ribs, this is where the central drag spar will be installed. It provides the structure required to mount the fuselage to the wing.
- Cut the spar notches out of the ribs using a razor saw, by making multiple cuts down and then breaking away the material in between them, the closer the cuts the easier that this will be. Also ensure that the entire drag spar is inside of the ribs. This may require the out board ribs to be just slightly deeper because of the dihedral.
- Once the spar is properly dry fitted mix 5 min epoxy to use on the reinforced ribs and apply wood glue to any non reinforced ribs to secure the central drag spar.
Step 32: Wing Fabrication: Sheeting the Upper Wing Surface
All sheeted surfaces on this model are covered in 1/32" thick balsa wood. Since I am leaving the wood grain exposed when the model is finished it is important to match the grain and color of the board to the piece next to it. Furthermore it is important to make the seams as smooth tight as possible because wood filler will show up after finishing.
- Select the sheets of balsa that will be joined on the edge. Important considerations are the curve in the edge since no boards are actually cut straight, the wood grain, wood color, and hardness.
- If the two board needing to be joined have edges that do not perfectly match because the edges are not straight or are wavy use a long bar sander to very carefully sand them to fit each other, while maintaining a square edge on the sheets.
- Lay down a sheet of wax paper and tape it down to the work surface
- Lay a piece of packaging tape on the wax paper. This is to prevent the glue joint from sticking because CA will glue to wax paper.
- Lay the boards being glued face down on the the working surface with the edge being joined over the packing tape.
- Put on a pair of gloves and ensure there is adequate ventilation.
- Apply a thin bead of thick CA on the first 8 to 10 inches of the joint and hold the pieces together being sure to keep them flat on the table.
- Two alternate methods can be used at this point.
- The first option is to bend the remaining portion of the sheeting back and apply another bead of thick CA approximately the same distance and align.
- Hold the boards flat on the table and hold the seam together. Then apply a few drops of thin CA to the section being held. Be careful to not apply too much or else it will soak into the surrounding wood.
- Repeat this as needed until enough strips have been jointed together to cover one side of the the wing surface.
- Sand the sheet with a sanding block with between 120 and 180 grit sand paper on it to level out the surface where the joints are and to remove excess glue. Patience is needed while sanding or else the sheet can shatter.
- Determine how to position the grain of the wood on the wing. The wood will only be able to bend perpendicular to the grain. In my case I ran the grain along the leading edge, this will leave the center of the wing with a V where the grains of the wood come together, however since this will not be seen I can accept this.
- Lay the balsa sheet over the wing and with a pencil mark where excess can be cut away with a sharp razor to make the sheet more manageable. Leave at least an inch of excess around the edges.
- Lay the sheeting over the wing slightly ahead of the leading edge.
- Apply a line of Thick CA along the top of the sub leading edge and then carefully move the sheeting over the leading edge and work from the center out applying pressure to adhere it. Be careful not to "pull" or "push" the wood or else the sheeting my become wavy further back on the wing.
- Gently lift the sheeting up being carefully to not bend it to far and crack it. Then apply a bead of Thick CA to the the front half of the rib in front of the spar. Next fold the sheeting back over the glue making sure that it adheres smoothly without wrinkles.
- Repeat the previous step now going up to the wing spar.
- At this point you can proceed two ways.
- Keep lifting and applying thick CA to the ribs until you finish the wing.
- Flip the wing over and while supporting the skin from underneath use small drops of thin CA along the joints to glue the sheeting on.
- Trim away any excess wood from the edges with a sharp razor.
- Sand the sheeting at the center rib at an angle to allow a scarf joint to be made along it.
- Fit the other wings sheeting and trim off the extra.
- Continue dry fitting until the edge of the new sheet comes to end of the scarf joint on the sheet on the other wing.
- Place the root end of the sheeting on the edge of a table and sand in the scarf joint to match the one on the wing.
- Apply the sheeting to the second half of the wing using the same technique used on the first half.
Step 33: Wing Fabrication: Finishing Ailerons
Now that the shells of the ailerons are completed, the control linkages and hinges must be build into the aileron and into the wing. Since I have choosen to use the rotatory drive system to move the control surface the ailerons will not have any visible control horns but instead will have a slot in side of them where a bent wire will rotate to move the control surface. In this step I will describe how I made the slots, installed the hinge pockets and hinges, as well as how the leading edge was installed on the ailerons. Additional information on rotatory drive systems can be found at the link below.
http://augiemckibben.tripod.com/g2_instructions.html
- The rotatory drive system that I purchased did not include a set of pockets so they had to be fabricated. First i cut 6 sheets of 2oz fiberglass large enough to make make pockets for all of my control surfaces from.
- To prepare for the wet layup tape a waxed sheet to the working surface.
- Mix the epoxy and work it into the the first ply of fiberglass, once it is thoroughly wetted place it on the waxed sheet.
- Wet the next sheet of fiberglass and after squeegeeing out the excess epoxy place it onto the previously placed fiberglass ply. Then squeegee the plys together to remove any air bubbles. Repeat this until all of the plys are stacked together.
- Place a waxed sheet on the top side of the laminate stack and squeegee out any air bubbles to ensure that a flat smooth surfaces is created.
- Wait for the resin to cure.
- Using a razor saw strips out of the fiberglass plate approximately 3/4" of an inch wide. These will form the inner surfaces of the pocket that the drive shaft will rotate in.
- The pockets need to be large enough to allow the drive shaft to rotated freely within therefore I made mine 2.5" long. Again I cut the fiberglass with a razor saw.
- While wearing the appropriate protective equipment rough up what will be the outside of the pocket and also the outside 1/4" inch on the inner surface, this will allow the fiberglass to be glued while keeping a smooth inner pocket.
- Glue a 1/16" thick basswood backer to the back of the fiber glass liners.
- Now the gap must be set between the two plates I used a piece of 1/4x1/8" bass wood to make the spacer for the drive shaft. First glue the spacers onto the inside of once of the fiberglass spacers with thick CA.
- Sand the spacers and then place the other pocket halve on the spacers and check the fit with the driveshaft. The fit should be tight, but not to tight as to where it does not rotate freely and smoothly.
- Once the desired fit is achieved glue the top piece of fiberglass onto the lower assembly to make the pocket.
- Glue thin strip of balsa onto each side of the pocket till it is the thickness of the opening in the aileron. Then sand the balsa until the pocket fits perfectly in the aileron, but also importantly the pocket must align with the hinge line in the center of the control surface.
- Once the desired fit is achieved for the pocket assembly install it into the aileron with wood glue.
- The hinge pockets are made from a 3/8x3/8" rod of balsa with a hold drilled length wise into the rod.
- Then a notch is cut in the top side of the hole so that the set screw can be installed.
- Dry fit the hinges until they fit well into the pocket and are centered.
- Glue in the hinge pockets and then the hinge block into the aileron.
- Mark the upper and lower surface where the hinge is located so that once the leading edge is attached, it will be easy to locate the hinge.
- The leading edge is made from an over sided piece of 1/4" thick balsa, use thick CA to glue it onto the aileron being careful to not twist the aileron.
- Using a razor carve down the leading edge until it is close to circular, then use a sanding bar to achieve the desired curvature.
- Lastly cut out the leading edge in front of the hinges.
Step 34: Wing Fabrication: Installing Aileron Servos
When using a rotatory drive system to move the control surfaces the servo installation is much more critical than for a traditional control horn and pushrod setup.
- Depending on the surface being moved the angle of the bend in the drive shaft will vary. In this case it is close to 45 degrees.
- The servos are installed on a shelf in between the ribs made from 1/16" balsa with 1/8" inch balsa strips around the edge to reinforce it.
- Drill the necessary holes to allow the drive shaft to exit out the trailing edge.
- Test fit the shelf with the ailerons installed. The angle and vertical height of the shelf is vital for smooth operation. Once the ideal location is found mark the location and then glue it in place with thick CA.
- Test fit the servo again with the aileron to verify that the shelf position is correct. If it is off a spacer between the shelf and the servo may be required.
- Reinforce the hole the driveshaft exits the trailing edge of the wing through by drilling a slot through a small piece of fiberglass plate. It is good for the shaft to have play in the vertical direction, however lateral motion should be minimized. Once the plate is aligned glue it in place with CA.
- Using sand paper rough up the side of the servo that is being glued in.
- Mix epoxy to glue the servo in place.
Step 35: Wing Fabrication: Hard Point Installation
Hard points are installed on each of the wings just outside of the flaps. They are designed to allow any payload to be securely held in place with a pin and then be released when the pin is pulled. The blue block is an 1/8" thick block that fits inside of the mount. with the hole aligned with the pin
- Reinforce the rib that will be supporting the hard point with 1/16" thick balsa, being sure to attach it securely to the spar.
- The pocket is also build using 1/16" inch bass wood with the edge of the bracket being supported with 1/8" inch basswood.
- Once the bracket is complete use it as a guide to drill the hole in the wing rib for the pin to go through
- On the center rib a small shelf is made for the release servo from 1/16" balsa with the edges being reinforced with 1/8" inch balsa, just like the aileron shelves
- Epoxy the servo onto the self. As a side note I originally set this mechanism up with a GWS pico fast ball bearing servo, but the gears stripped after operating only a few strokes. As a result I replaced it with a Futaba S3114.
- Thin carbon rods are run through the wing ribs to the pin pull.
Step 36: Vertical Stabilizer & Rudder Fabrication
The vertical stabilizer is fabricated very similar to the wing but is much simpler and faster to fabricate. This is because it is
- Using the same technique used to make the wing rib templates draft the rudder rib templates (NACA0010).
- Print out and use double sided tape to attach the templates to the 1/16" inch balsa stock.
- Cut out the ribs and then sand to the final shape.
- Cut the spar notches.
- Draw the blue print to build on and then cover with wax paper.
- Cut the rudder spar made from 3/16x1/8 basswood to length. Then place the rudder spar on the blue prints being sure to prop the tip up so that the center of the rudder is horizontal.
- Glue on the ribs, while verifying that ribs are square with the table.
- Once the ribs are all installed dry fit the other spar half making sure it will not twist the rudder. Once the fit is correct glue in the other spar cap.
- The shear web is made from 1/16" balsa. Cut and install it as done on the wing.
- Sand the leading edge with a straight edge to properly angle the ribs for the installation of the sub leading edge.
- The sub leading edge is 1/4" thick over sided balsa strip that can be glue on to the ribs with thick CA.
- Use a razor to get the sub leading edge close to following the angle of the ribs. Once the shape is close use the tape technique that was used on the wing to protect the ribs as the sub leading edge is sanded.
- Mark on the vertical stabilizer where the rudder will begin then glue one side of the sheeting on to the part that will be the rudder.
- Sand the trailing edge of the sheeting as done on the ailerons and then glue the sheeting on the opposite side.
- Cut the rudder off of the vertical stabilizer using a razor saw.
- Attach the drag spar and sand as was done of the wing.
- Attach the leading edge of the rudder as done on the aileron.
- Sheet the first side of the vertical stabilizer using one of the methods used on the wing.
- The leading edge of the rudder and hinge pockets are fabricated exactly they were on the ailerons.
- Build a servo shelf as was done for the wing and fit it.
- Check that is is properly installed for smooth operation and then epoxy in the servo.
- Drill a hole down through the ribs to allow the servo wire to exit out the bottom of the vertical stabilizer.
- Cover the other side of the vertical stabilizer by slowly working your way from the leading edge back, by bending the sheeting up and applying thick CA to the ribs.
Step 37: Horizontal Stabilizor & Elevator Fabrication
Once again this control surface is constructed very similar to the wing. The main differences are that the servo is set up to use a control horn and push rod setup rather than a rotary drive system, this was done because the elevator is equipped with a standard size servo for increased reliability and control authority. Additionally the elevator is solid rather than being build up as all of the other control surfaces were, this was done because there elevator is very thin at the tips and the difficulties in building a build up elevator that would be strong enough is not worth the weight savings.
- Using the same technique used to make the wing rib templates draft the horizontal stabilizer rib templates (NACA0010)
- Print out and use double sided tape to attach the templates to the 1/16" inch balsa stock
- Cut out the ribs and then sand to the final shape.
- Cut the spar notches.
- Draw the blue print to build on and then cover with wax paper.
- Cut the elevator spar made from 3/16x1/8 basswood to length, note that this spar is 4 pieces and that they will come together in a V. Then place the stabilizers spar on the blue prints being sure to prop the tip up so that the center of the stabilizer is horizontal.
- Glue on the ribs, while verifying that ribs are square with the table. Do not install the center rib at this time.
- Once the ribs are all installed dry fit the other spar half making sure it will not twist the elevator. Once the fit is correct glue in the other spar cap.
- The shear web is made from 1/16" balsa. Cut and install it as done on the wing.
- The two sections must now be joined together with a structural carry though. To accomplish this I cut and sanded three pieces of basswood that would be large enough to completely fill the gap between the upper and lower spar cap. These pieces not only replace the shear web in this section but also serve to unify the right and left wing.
- Now cut the middle rib so that it can be installed in two pieces on the spar.
- Sand the leading edge with a straight edge to properly angle the ribs for the installation of the sub leading edge.
- The sub leading edge is 1/4" thick over sized balsa strip that can be glued on to the ribs with thick CA.
- Use a razor to get the sub leading edge close to following the angle of the ribs. Once the shape is close use the tape technique that was used on the wing to protect the ribs as the sub leading edge is sanded.
- Since the stabilizer is swept the leading edge will need to cross as done on the wing.
- Mark where the elevator will begin on the ribs and then cut off the excess rib material with a razor saw.
- Attach the drag spar and sand as was done of the wing.
- Note that the structure of the elevator is made mounting points must be installed before the stabilizer is sheeted. I chose to install two brackets. The front bracket is made to connect to the upper and lower beams on the truss in the fuselage. The aft mounting bracket mounts only to the upper beam since the lower beam does not extend the entire length of the fuselage. They are both made from 1/8" thick hobby plywood.
- Sheet the first side of the vertical stabilizer using one of the methods used on the wing.
- Hinge pockets are fabricated exactly they were on the ailerons.
- Cover the other side of the horizontal stabilizer by slowly working your way from the leading edge back, by bending the sheeting up and applying thick CA to the ribs.
- The wingtips are made from solid pieces of 1/4" balsa stacked together to be the thickness of the surface.
- Once the balsa pieces are stacked to form the tips, cut out the top view of the tip into them. Trace that view onto the other tip and cut it out.
- Glue the tip blanks on to the stabilizers tips.
- Use a razor to thin down the tips until they are close to the desired shape.
- Use progressively finer sand paper to finalize the shape of the tip.
The elevator on this airplane is split by the fuselage, but is only articulated with one control rod. To allow the motion to be transmitted between each side a dowel rod was added onto the solid wood elevator blank. At this point I recommend drilling the hing holes in the elevator blank in case they do not come out well very little work will be lost. Begin carving the elevator blank into a streamlined shape that follows the curves of the stabilizer. Once the elevator is sanded to shape the center section can be cut out so that it will clear the fuselage. Additionally on the control horn side the balsa is cut back further to allow a piece of basswood to be installed. This basswood is to provide a solid material that a slot can be cut into to mount the control horn into.
Step 38: Fuselage Design
This fuselage is designed to carry flight loads through a truss, like a bridge. Therefore most formers are not designed to take any load. The formers are simply attached to the truss to allow a streamlined fuselage to be build over the truss.
The fuselage had been preliminary designed in CAD as a side view. From this I had to determine the cross-sectional shape at each location along the fuselage. To do this I printed out the side view from CAD and then taped it onto a sheet of foam core. Then using poster board I began cutting out every other cross section, from there I cut out the intermediate cross sections. Then I was able to use the model to size the fuselage truss. I was able to do this by laying a ruler along the length of the fuselage and using that to determine the height of the truss, then I measure what the maximum width of truss could be to fit inside on both ends. By dividing the difference in size by the number of formers that were between the end points I was able to check to see if the truss would fit in the remaining formers. You can see the final truss design marked out on the fuselage cross sections as boxes. It is a two part truss with the joint near the middle of the cockpit. This allowed me to maximize the size of the truss and thus strength, while also minimizing the number of joints between truss sections.
Step 39: Fuselage Fabrication: Building the Truss
Building the structure of the fuselage as a truss proved to be a rather fast and easy process, that produced a light yet very strong framework. To save time constructing it I had purchased strips of 1/2x1/16x36" hard balsa to make the corners out of, however it was challenging to find enough straight pieces. The vertical members of the truss were made from strips of hard 1/4x1/16" balsa, while the diagonal members were the same size but made from a lighter and softer balsa.
- Lay down wax paper over the working surface and apply a strip of packaging tape along the length of it to protect it from glue.
- Use double sided tape to stick a long straight edge to the wax paper. This will be used as a guide while gluing the two pieces together into the beam.
- Stand one strip of balsa upright in front of the straight edge and then lay down the second piece flat on the table to hold the other piece in place.
- Hold the two pieces tightly together and with the joint over the tape. Work from one end to the other applying thin CA to the joint to bond the two pieces together. I have tried making beams like this previously with wood glue and have found it to be a headache because the water in the glue will swell the wood along the joint which will bend the beam. From there it is luck as to whether it will return to being straight once both the wood and then glue have dried thoroughly.
- To make assembling symmetric trusses easier, I drew a quick side view of the truss in Autocad which showed the location and spacing of the truss members when looked at from the side. Note that you will need a different drawing for each side since they are mirror and not a copy of each other.
- With the drawing printed out and taped on the working surface and covered in wax paper, apply double sided tape to hold the long corner members of the truss in place.
- Start installing the vertical members, which are made from the harder balsa, following the template.
- Once all the vertical members are installed then install the diagonal members. The easiest way I have found is to sand one end of the strip into the required shape so it fits in the first corner by the vertical member and then line the strip up to pass through the opposite corner. Then cut it diagonally across with a razor saw and sand to fit the second corner.
- Now that the sides of the truss are formed they must be joined. to prepare for this I drew a very simple blue print on poster board that shows the correct taper to mount the trusses at.
- Carefully align the trusses with the blue prints, and again double sided tape can be used to help hold them in place.
- Starting from the bottom install the horizontal members between the vertical members on the side and then install the diagonal members.
- Once the bottom is finished, flip the part over and do the horizontal members. Once a sufficient number are in place the truss can be moved into a more convenient position to fit the diagonal members. Do not forget to leave areas to allow access into the fuselage for batteries and electronics.
- To join the truss sections together I first tacked them together with CA, then installed a balsa doubler inside the truss at the joint between the sections.
Step 40: Fuselage Fabrication: Installing Formers and the Firewall
The formers are basically the ribs of the fuselage, they provide the base shape to attach the balsa sheeting too. They are all made from 1/16" balsa, with the exception of a few structural ribs that are made from 1/8" plywood. Two of these structural formers are located at back of the canopy for the rear wing mount, the other two are located in front of the wing mount where the fuselage is connected on both sides in between the canopy cover and the engine cover. The firewall is a fiberglass reinforced plywood that the motor mounts onto. It must be extremely stiff or else vibrations from the motor can cause it to flex which will cause the vibrations to grow until either something breaks or the throttle is reduced. Additionally the firewall must be attached very well to the fuselage truss so that it can pull the airplane through the air as well as withstand any vibrations.
- Using the templates made from the plan cut out all of the formers out of the desired material. The balsa formers are made in two halves and then glued together while the plywood ones are cut out as one piece.
- Dry fit all of the formers to ensure they fit the truss well since the marks on the template are really just an approximation of the parts that were actually made.
- Once all of the formers fit appropriately begin by installing the solid plywood formers from the widest point on the fuselage to the narrowest using wood glue.
- Install the remaining formers to the fuselage one half at a time. A drop of thin CA can be used to join the two halves together in the center. Note: because of the orientation of the grain in these pieces they can be very fragile. If any break during the build they can simply be glued back together with CA since they are not carring any load and are hidden.
- The firewall is made from a fiberglass reinforced plywood that is made from 8 layers or 1/32" basswood with a 2oz ply of fiberglass in between each layer of wood. This is made by wetting the bass wood and the fiberglass and then applying the glass to the wood just as was done on the reinforced ribs. Ensure that this piece receives adequate compression to ensure there are not voids in the layers once cured.
- Using the appropriate safety measures cut the firewall to shape using a coping saw, leave a little excess along the inside of the cut too allow the part to be sanded
- Now find the center of the firewall and mark it. Then use that to help position the motor mounting plate. These markings can be seem on the first picture of the fuselage with the firewall mounted, sorry I missed getting a picture of it before it was installed. Once the position is found drill the holes for the mounting screws. An additionally hole may need to be drilled depending if the motor has a drive shaft extending out the base of the motor.
- The fuselage must be prepared to accept the firewall. To do this I squared the front of the truss by standing the fuselage on a perfectly flat table. I then suspended a make shift plumb bob from the center of the tail pylon. By carefully sanding the fuselage trusses I was able to get it to align to the center of the fuselage, which would make the firewall square to the flight path (0 degrees right thrust) as desired. The top section of the fuselage truss is flat in respect with to the direction of flight, therefore once this was trimmed to be perpendicular to the table the firewall could be set with 0 degrees of down thrust. Adjustments to the thrust angle will be made as required by flight testing.
- Note: The thrust line is conventionally measured in degrees right from the center line and degrees down from center line. The right thrust offset is to counter the torques being generated on the vertical stabilizer from the propwash, commonly known as P-Factor. Down thrust is include to reduce the airplanes tendency to climb as the throttle is increase.
- Rough up the back of the firewall so that it can be glued to, then tack the firewall to the fuselage using thick CA.
- Reinforce the front of the fuselage by gluing in a second set of lower truss beams. They can be seen since they produce a gap between the outer and inner truss beams. These are to increase the rigidity of the nose of the airplane.
- Continue reinforcing the fuselage by gluing a 1/16" thick piece of basswood to the top of the truss at both the engine cover and at the canopy. Note that the excess former material was removed from the engine cover to allow a door to be placed there. The new edges of these formers were connected with a strip of 1/16" balsa. These reinforcements both help strengthen the structure but also help to protect the truss while the airplane is being worked on and readied for flight.
- Mount the firewall to the reinforce fuselage, for this I used 1/8x1" strips of bass wood to go around the entire perimeter of the fuselage. These are glued to the fuselage and to the firewall with 5 minute epoxy to create a very strong bond.
- The truss is a very strong and light structure all together, but if a large load is applied to a single point it will break. Such loads are not actually generated in flight but by people just touching the airplane to work inside it perhaps to install a battery, therefore from the firewall back to one former behind the canopy need to be reinforced. To protect the truss from this 1/32" balsa sheeting was applied to the inside of the truss. The floor was reinforced with a sheet of 1/16" balsa since it will have to support the battery and the weight of any of the other components and distribute it across the structure. Hindsight being 20-20 shows that these really should have been installed when the truss was made and was in pieces.
Step 41: Mounting the Wing to the Fuselage
The wing mount for this airplane had to allow the wing to easily be removed so that airplane could be transported. Even though the wing and fuselage will remain two separate pieces it is critical that when they are assembled for flight that there is no slop in the connection, and that the mount will support the full weight of the airplane while it maneuvers. Therefore a three point of contact system was designed.
- The front of the wing mount is a rectangular peg that attaches to the center reinforced rib and to the sub leading edge. It is made form 1/4x1/2" basswood and is glued to the rib using epoxy. Then gap between the two rods is filled with a piece of basswood to make a solid peg.
- The rear wing mount is made by drilling two holes through the center drag spar, in which a blind nut is installed. Over the blind nut is glued a strip of basswood with a hole aligned over the bolt hole, this piece ensures the nut never moves out of place in the wing. On the upper surface of the wing a plate is then placed above these wing bolt holes. This plate serves a a solid point of contact to prevent the wing from twisting in reference to the fuselage.
- The reinforced former in front of the wing has a hole cut into it to accept the peg from the wing. It was then reinforced with basswood frame on the front side of the former to prevent cracking. This hole must be the a tight fit for the peg or else the wing and fuselage will be able to move in flight.
- Once the hole is trimmed to fit the peg the location of the rear wing bolts must be found on the fuselage. To do this the airplane was placed nose down on a flat table. Then the distance from the wingtips to the table was measured. When the measurement from both wingtips were equal then the wing was aligned. I used a drill bit to mark the on the underside of the fuselage where the wing bolts would go.
- To secure the wing bolts into the structure of the fuselage required substantial reinforcements. First the underside of the truss was covered in 1/16" basswood, then a second reinforced former was installed just forward of the bolt location.
- Then a 1/4x1" basswood bar was epoxied to the reinforced formed and to the truss work. It can be seen in the photo as the darker piece of wood that is on the fuselage
- To securely hold the bar in place a 1/2x1/4" strip of bass wood was cut to go over it and through the reinforced former to lock in the bar.
- Lastly a rectangular piece of basswood was used to fill in the center section created in this lattice to provide a solid point for the wing bolt plate to be tightened against.
- Once again the wing was placed nose down on the table to ensure that the wing was mounted straight. Then the wing bolt holes were drilled through the wing and into the fuselage.
Step 42: Tail Assembly
The vertical and horizontal stabilizer must be mounted precisely to ensure that the correct angles are achieved. The angle of the horizontal stabilizer must be slightly nose down to ensure the stability of the airplane, otherwise it will be unflyable. The mount must also be made as lightly as possible since it is difficult to compensate for a tail heavy airplane with out adding a lot of weight to the nose.
- At this point the vertical stabilizer is a self contained structure that needs to be connected into the truss that makes up the fuselage. To do this the segments of the spar that are sticking out had to be very firmly attached. I began by making preliminary holes in the upper deck of the the truss to allow the surface to be test fitted.
- Then a mounting bracket had to be made to take the loads from the spar and transfer them into the balsa truss. It is made from 1/8" thick plywood and has lightening holes in it to reduces excess weight. By dry fitting it it is possible to mark the location of the spar holes.
- Once the vertical stabilizers mounting bracket has been dry fitted it can be glued in place with wood glue.
- Make and install a second mounting plate on the lower truss members to allow the vertical stabilizers spars to attach to it, as well as making a solid mounting point for the horizontal tails front bracket.
- Install the tail wheel support beams. There are made from 1/8x1/4" bass wood. thought difficult to see they run from the front of the upper tail bracket and extend well past where the wheel will mount.
- The horizontal stabilizer already has mounting brackets attached directly to its spar, however they will need to be fitted to set the correct angle with respect to the wing. This is a repetitive dry fitting process where the angle is set by sanding the rear bracket.
- Once the brackets were set to the correct size position the horizontal stabilizer inside the airplane. Then cover the tip of the vertical stabilizers spars with the lead from a pencil. Gently side the vertical stabilizer into position keeping it the angle it will be mounted at. The lead will transfer on to the skin of the horizontal tail and will show the location of the holes that must be made to allow the vertical tail's spar to pass through.
- Repeat this process to mark and drill the hole location on the underside of the elevator.
- Apply finishing glass to both the horizontal and vertical stabilizers, this process will be covered in later step.
- Double check the angle the tail is mounted at. Glue the horizontal stabilizer in place using 5 minute epoxy, since it will produce a very strong bond while also filling any gaps that my be hard to see.
- Double check the angle the tail is mounted at, and that the holes in the horizontal stabilizer still align. Glue the vertical stabilizer in place again using 5 min epoxy.
- Glue in a second tail gear support that comes from as far forward as possible. It will likely not be as long as the upper member since it will hit the horizontal stabilizer.
- I chose to install the tail wheel bracket backwards as opposed to the intended direction. This was done to create a tighter rear of the airplane to allow it to come down smoothly into a point. It is epoxied onto a block of basswood that connects into the tail wheel beams that extend out of the fuselage.
- The rudder had to be reinforced with a strip of basswood at the bottom to be able to support the wire going into it that moves the tail wheel. Unfortunately there was no way to capture a picture of the final bent wire since it had to be done while the tail was mounted. However if looking at the photo of the rudder and the tail wheel bracket the wire is bent 90 degrees down just forward of the hinge line. Then it travels down to the level of the brass tail piece where it bends 90 degrees to the right to go though a hole in the brass cap. On the other side of the brass cap it bends up 90 degrees to lock it into place, and then the excess is cut off.
- The control rod for the elevator needs to be made now while there is still easy access into the fuselage. It is made from a 4mm carbon tube with 2-56 threaded rod epoxied about 2 inches deep into the tube on either end. This setup reduces the weight of the control rod verses a comparable metal one and is easier to set up than the plastic tube control rods. Additionally the carbon tube is very stiff which reduces the slop in control setup with out having to add guides inside the fuselage. The clevises are threaded on to the rod, one of which with tread lock to prevent the pushrod from being able to rotate and unscrew out of the clevis.
- Build a mounting shelf as done for all the other servos in the aft section of the fuselage and epoxy the servo into place on it, being sure to line up the control arm with the control horn on the elevator.
Step 43: Fuselage Fabrication: Engine Vents
During flight electric motors can consume large amounts of energy, while most of this energy is transformed into spinning the propeller, a portion of it turns into heat. This heat must be dissipated, and therefore airflow must be maintained over the power system, ie the motor, battery, and ESC. On the engine cowl there will be an air scoop, therefore exhaust outlets must be made to allow the warm air to escape.
- Cut oversized vent fins from a sheet of 1/32" thick balsa.
- Cut spacers approximately 1.5" long from 1/4x1/16" thick balsa.
- Using a piece of piece of 1/2x1/16" balsa as a base set the angle of the fins and glue the first one on with CA.
- Glue a spacer after the fin, then glue on the next fin. Repeat until the desired length is created.
- Sand the top of the fins until they are all the same height.
- Glue spacers in between the tops of the vent fins.
- Glue on a base made from the same material as the bottom, being sure it is aligned with the bottom piece.
- At this point the fins will probably look rough and will not all be the same height. Sand the fins until you hit the bottom and top rails.
- Cut the formers where the vents will be installed.
- Glue in the set of vents.
- To achieve the serrated look on the fins I sanded along the length of the vents using a bar sander, with the firewall and the first reinforced former as a guide.
Step 44: Fuselage Fabrication: Wing Saddle
The wing saddle is the part of the fuselage that takes the contour of the wing and makes a seamless transition between the fuselage and the wing. Due to the complex curves that need to be matched this can be a challenging piece to construct.
- Glue on the remaining formers along the canopy section. They can be sanded using the reinforced formers on either end as a guide.
- Install the wing on airplane.
- Measure the thickness of the wing tape that is being used then divide that by two and add 1/8" to it. Mark this height on all of the formers above the wing.
- Remove the wing.
- Cut the formers as marked.
- Using strips of 1/8x1/8" balsa strips begin making the the saddle by bending the strips to fit along the underside of the formers. Because of the complex contours being made strips were the only way to achieve the desired result.
- Once the rear portion is glued together, sand along the underside of the saddle.
- Test fit the wing, the wing saddle may need sanded further to allow the wing to flight with a uniform gap.
- The front of the wing saddle is made from solid pieces of balsa that were then carved and sanded to the desired shape.
Step 45: Fuselage Fabrication: Sheeting
In comparison to the wings sheeting the fuselage is an entirely different challenge. The fuselage has contours in more than one direction at a time, and the curves are much tighter than the relatively flat surfaces that were covered on the wings. The first rule is that edge joints are no longer an acceptable way to join sheets because they will be impossible to align and will easily brake on the tight curves being made.
- Add any remaining formers, for me these were in the tail region.
- Us a sanding bar to very gently sand the formers. The goal is not to change the general shape but to ensure that they all align with one another. This step will prevent the skin from being wavy and going up and down between formers.
Sheeting must be done in either smaller pieces for where there are complex curves to negotiate or in large sheets when the lines of the airplane permit it. The key to smooth sheeting and tight joints is to dry fit again and again, and to lightly draw alignment marks on the pieces being sheeted to help align the work when gluing it. Additionally all joints must be scarf joints with at least a 1/4" overlap. This overlap allows the joints to come together smoothly and also allows them to be sanded after the sheeting is in place. If the contours are too sharp you will find that the skin will try to bubble up somewhere else. It may still be possible to cover this area however it will likely require more than one piece of covering. For very tight corners solid balsa will need to be used, such as the very end of the lower fuselage where the elevators pushrod comes out, or the fairing from the razorback to the rudder. When sheeting a sharp corner it is best to install a backing to glue onto, an example would be just aft of the firewall in front of the vents the sheeting comes to a "V" and under the sheeting is a piece of balsa sanded to a "V" that I could glue to for support. Be patient and be gentle with the covering at this stage it is very easy to crack it
Step 46: Wing Fabrication: Landing Gear Door
The landing gear on this model is concealed by two doors when the gear is retracted. The inner doors are articulated with a micro high torque servo to ensure under any condition that they will open. The outer gear doors are attached to the landing gear and move with them. In order for the landing gear to function properly a landing gear sequencer must be used otherwise the inner doors would close faster than the landing gear and only bad things come after that. The sequencer allows you to set up a time delay between each stage of extending and retracting, while also allowing for flexibly in the setup of the doors. Mine operate as follows starting from the landing gear up position.
- Inner door opens
- Landing gear opens
- Inner door closes
- Inner door opens
- Landing gear closes
- Inner door closes
That is enough about how the gear works lets get to how to build them.
- Design the outer landing gear doors, they must be long enough to cover the landing gear legs but have to be short enough that when the landing gear and the soft wheel are fully compressed that the door will not strike the ground. They should also leave sufficient margin in front of and behind the gear and if the gear somehow twists that they will not strike the wing sheeting.
- With the shape determined cut the door out of 1/8" thick balsa.
- Install the gear door and hinge onto the rib on the outside of the landing gear using CA.
- A spacer is used to prevent the gear from striking the door as it opens. Additionally small rubber band is used to secure the gear to the landing gear strut.
- Next design the inner gear door, allow extra length on the door to allow it to overlap the outer gear door. Again it must provide the necessary clearance for the wheel. Also it may be designed to use only one servo to operate both doors. (Initially I set up the landing gear to use two GWS pico servos, one for each door. However towards the end of the door fitting one of the servos had an electrical glitch and would no longer respond. At that point I replaced the two pico servos with one high torque micro servo)
- Cut the inner gear doors out of 1/8" balsa.
- Install the hinges and the inner gear door. The hinge that I used has the control horn build into it, the advantage being that it had a very small footprint, however it does require more torque than it really should to open and close the doors.
- With both doors installed sand the ends of the door so that the inner door overlaps the outer door.
- Drill a hole through the center rib to allow a push rod to connect between the door and the servo arm.
- Bend the push rod, note that I included a zig-zag in the push rod, this is to increase the flexibility of the rod and will help prevent the servo from binding, also it it allows the pushrod length to be easily adjusted.
- Lastly Install a neodymium magnet on the tip of the inner door, as well as underneath it. This magnet will offload the servo when the landing gear is retracted.
Step 47: Wing Fabrication: Flaps
Since the trailing edges of the ribs that the flaps would align with were made with different materials I chose to make the flaps from scratch.
- Print out the rib templates for the ribs required to make the flaps.
- Cut the trailing edges of the rib out of 1/16" balsa.
- Sand the triangles down below the line that was normally used. This is so that they will match the ailerons which are thinner than the wing.
- With the ailerons installed on the wing lay a piece of balsa sheeting on the underside of the wing. Then trace the outline of the wing and the tip of the aileron onto the balsa sheeting. Then cutout the sheeting and verify its fit in the position of the flap. There should be about an 1/8" of clearance between the flap and the aileron.
- Measure out the spacing of the ribs and glue them into place.
- Make the control horn pockets and the hinges as done on the ailerons.
- Install the leading edge onto the flap. Since the flaps are thicker than the ailerons an additional layer of balsa may required to make the front of the flap circular.
- Shape the leading edge as done on the ailerons.
- Install the flap servos in the wing as was done on the ailerons.
Step 48: Fuselage Fabrication: Engine Cover
The engine cover is made from balsa to allow access to the forward compartment. It is attached with a series of bolts.
- Measure the forward and rear edge of the engine compartment.
- Cut out a rectangle of balsa that is at least as tall as the channel that the engine cover is going in.
- Cut a strip of balsa the length of the engine compartment and glue the end plate on to it.
- Cut the remaining formers into rectangles and glue them onto the frame.
- Place the frame inside the fuselage and sand using the firewall and the top of the fuselage as a guide.
- Once it is sanded to shape fit a diagonal cross member into the engine cover, this will prevent twisting when covering the piece with balsa.
- Remove the cover from the airplane and cover with balsa.
- Install backer pieces where the bolts will go through the cover.
- Drill through the skin and the backing pieces to allow the bolts to mount flush.
- Place back into the airplane and then drill through the truss to make holes to install blind nuts in the airplane.
Step 49: Fuselage Fabrication: Canopy
The canopy is constructed similarly to the engine cover with the exception that a pre-made bubble was added into the construction process to be the shape of the canopy.
- Use a piece of 1/4" balsa to match the curves of the side of the airplane.
- Cut a piece of 1/16" balsa for the front former of the canopy.
- Glue together 4 layers of 1/16" balsa to make a piece of plywood for the rear former of the canopy.
- Use the fuselage as a guide to sand the formers to shape.
- Glue the formers onto the bottom rails with CA.
- Cut the canopy to the desired shape and then rough out the part of the canopy that will be glued.
- I wanted to had the canopy appear to be fogged, to achieve this look I simply sanded the inside and outside the the bubble with 400 grit sand paper to scratch the surface and remove the shine.
- Glue the canopy to the rear former using epoxy.
- Add in any additional formers.
- Sheet the formers using 1/32" balsa working from the edges in towards the bubble.
- Once sheeted drill 2 holes into the lower balsa rails and install a wire into the holes. A hole shall be drilled in the fuselage to match these hole locations.
Step 50: Fuselage Construction: Engine Cowl
The cowl provides an aerodynamic fairing for the motor. Additionally it contains an air scoop to cool the motor. It is molded from a piece of insulation foam and then covered in fiberglass
- Stack together enough layers of insulation foam to reach the required thickness.
- Epoxy the foam together. Do not use CA it will eat the foam.
- Hollow out some of the foam so that is can fit over the motor, then bolt it onto the airplane with the spinner.
- Once attached to the airplane a coping saw or a razor saw can be used to carve out the rough shape.
- Use 60 to 120 grit sand paper to finalize the shape of the cowl.
- Remove the cowl from the airplane and cut enough 75oz fiberglass to put at least 4 plys over the entire cowl. I used 3 pieces per layer: top, left, right side.
- Prepare for a wet lay up with the appropriate safety measures.
- Mix the resin and wet down the foam mold, otherwise the glass will not stick to it.
- Begin laying pieces of fiberglass around the cowl building up one layer at a time. Be sure to remove any air bubbles with either a squeegee or hand.
- Once the cowl has cured put on the appropriate protective equipment and sand the outside smooth.
- Carve out the inside of the cowl with a dremel leaving approximately a quarter inch of foam on the inside, I have found the the carbide wheels with the burrs on them work the best for quickly removing material.
- Using a razor cut out the fiberglass for the opening for the air scoop.
- Sand the inside of the scoop smooth.
- Around the back edge remove all of the foam down to the fiberglass so that it can slide over the forward section of the fuselage.
- Spray the cowl with primer, be careful to keep the can far away from the piece because the propellant will eat the foam.
- Sand the primer and reapply as needed.
- Spray the cowl with the desired paint color, sand and repeat as needed.
- The motor cowl screws into the firewall to hold it in place.
Step 51: Wing Fabrication: Sheeting the Underside
Sheeting the under side of the wing is slightly more challenging than sheeting the top of the wing. This is because the underside of the wing has doors, hard points and also holes to be drilled for the set screws that hold on the hinges.
- Glue the sheets of 1/32" balsa together as was done for sheeting the top of the wing.
- Starting with the center of the wing cover the section the is inboard and forward of the gear doors. Be sure to run any of the wires out of the wing.
- Next dry fit the remaining wing sheeting and cut out the part that would be in front of the landing gear doors.
- Glue the sheeting on starting at the leading edge and working your way towards the trailing edge by applying small amounts of thick CA to the wing ribs and then laying the balsa over the glue.
- Be sure to cut out the required holes for wiring as well as for the hard points on the wing.
- Now sand the edges where additional sheeting must be sanded down to an angle extending at least a quarter of an inch.
- Dry fit the sheeting and glue it in place.
- Since the landing gear doors are thicker than the sheeting on the wings they will stick out beyond the skin, therefore a fairing must be made. Using various thicknesses of balsa as required to build up the required thickness up to the door on both the front and rear side of the door.
Step 52: Wing Fabrication: Wing Tips
The wing tips are simple to make however they can be rather time consuming to achieve the desired shape on both wing tips.
- Cut out the top view of the wing tips from the thickest balsa that is available, this will reduce the number of layers that must be glued together.
- Stack and sand all of the wing tip blanks together so they are all the same
- Glue the bottom wing tip blanks onto the wing tips, if desired the center of the blanks can be hollowed out to save weight. I hollowed out the centers but do not thing it made a noticeable difference.
- Use a razor or razor plane to roughly shape the wing tips to the desired shape
- Once the shape is close switch to progressively finer sandpapers untill the final shape and smoothness is achieved.
- Repeat the fun on the other wingtip
Step 53: Wing Fabrication: Fuselage Fairing
The fuselage fairing is made to allow a smooth transition between the fuselage and the underside of the wing. With out it there is a large gap.
- Install the wing onto the airplane.
- Using the fuselage as a template sand the formers match the contours of the fuselage
- Add in any additional formers.
- Cut notches in the formers to allow any wiring to run through. The wires you see are from the landing gear.
- Cut pieces of sheeting to cover the formers.
- Sand the edges of the sheeting to to a sharp edge this will allow for a seamless transition between the wing and the fairing.
Step 54: Finish Glassing
Nearly all of the airplane is sheeted balsa covered with .75oz fiberglass. While this may be intimidating to do the first time it is actually a very simple and easy process once the technique is presented.
- Sand the surface smooth with 180 grit sandpaper.
- Use a paper towel to wipe any remaining dust off of the part.
- Lay down a piece of painters plastic to protect the working surface.
- Cut out fiberglass sheets with a few inches of excess around the edge of the part.
- To go around sharp corners the cloth should be laid 45 degrees off of the grain direction.
- Try laying all of the fiberglass pieces on the part while dry to ensure that they will cover the entire piece.
- Ensure there is ventilation.
- Put on gloves and mix the resin.
- Use a squeegee to wet the surface with resin. It should be just a light coat with no drips.
- Lay the piece of fiberglass on the wetted surface and brush it smooth.
- Apply more resin as needed across the glass so that the all of the strands are wetted.
- Now wet the next section.
- If laying another piece of fiberglass down there should always be at lease 1 inch of overlap with all of the pieces that is touches.
- Let the resin cure.
- Put on a respirator and gloves.
- Sand the part with 180 grit sandpaper to remove any strands and runs.
- Prepare the working environment like you were going to do another wet layup but do not cut out any fiberglass
- Mix up resin.
- Apply a very light coat of resin over the fiberglass. Be sure to minimize running by just using the thinnest coat possible.
- Lightly sand the surface with 180 grit sandpaper to remove any runs.
- Sand the surface with increasingly fine sandpaper until at least 400 grit paper is used.
The resulting surface from this method will be very smooth to the touch, and the second coat of resin will greatly increase the shin and quality of the finish with very minimum weight increases.
Step 55: Finish Glassing Vertical & Horizontal Stabilizor, Rudder, and Ailerons
Just as important as knowing how to apply fiberglass is knowing how to properly handle the part while it is curing. For these components I used the hinge pockets as a handle to hold them while they cured by inserting a wire into the pockets. Additionally from these pictures you can see how the cloth was cut for each of the pieces.
Step 56: Finish Glassing: Fuselage
The fuselage proved to be the most challenging piece to fiberglass on the entire airplane. This was a result of its large size and complex curves. I began the layup by wetting the empennage and then glassed the upper tail cone on both sides. Then I glasses the underside of the tail cone. From there I wet the aft fuselage and then applied the right and left side pieces. Using a paint brush I then painted resin onto the engine vents so that the color would match the rest of the airplane. Lastly I wet and applied the glass to the nose of the fuselage. All told this layup which was done in one night took about 3.5 hours to setup and complete, the tail was barely tacky by the time I finished the nose.
Step 57: Finish Glassing: Wing
The flaps were easy to cover since they were small and identical to covering all the other control surfaces. The wing was time consuming to cover however since it is a relatively simple sheet it was rather easy to cover. It was completed in four pieces in one wet layup: right top, left top. right bottom, left bottom. I started with the top and allowed the fiberglass to wrap over the leading edge about 2 inches onto the underside of the wing. There was about 6 inches of overlap in the center to reinforce the skin for mounting against the wing saddle. The under side of the wing was covered in two large pieces. I applied the glass straight over the landing gear doors and then cut the gaps with a sharp razor while the resin was still wet. I did have to clean the joints after the resin cured, this was done by very carefully running a razor saw though the gaps until the doors moved freely.
Step 58: Finish Glassing: Engine Cover, Canopy, and Fuselage Fairing
Covering the remaining pieces were all as easy a wetting the surface and then laying the glass down on them. One precaution that was used on the canopy was wrapping it in tape to preserve the frosted look by ensuring that resin would not get on the bubble.
Step 59: Path Foward
The airplane is flight ready as it sits, and has been for the past week, however as I have said I am a college student. With moving three times this summer and working an internship I have struggled to find the time and the tools required to build this airplane. Therefore, in order to finish this Instructable I had to put off taking her out for the maiden test flight. This coming week I hope to let her spread her wings and take to the sky.
In regards to the Epilog Challage
If I were to win a Zing laser cutter it would be my most prized and used tool in my arsenal. It would allow me to rapidly design and test new ideas and building techniques. It would also allow me to share my passion and love of aviation with others. The love of building and designing has been in my blood since i was just a boy, the privilege to have a laser cutter would ensure that that continues to grow for a lifetime.
In regards to the Remote Control Contest
The thought a GoPro being mounting under the wing of this airplane brings a smile to may face just thinking about it. The prize of a macbook and GoPro would help this airplane to reach its full potential.
Building this airplane has been a tremendous learning experience and am glad that that this has allowed me the forum to share this experience with fellow creators. I know that I did not post every single drawing required to build this airplane but I hope that i have described every step and challenge in enough detail to allow someone design and build a beautiful airplane of there own. If I can give one person the tools or motivation to take his/her craft to the next level then this has been a successful Instructable. This Instructable is entered in the Epilog Challenge VI and radio control contest, and please feel free to comment with questions I will be more than happy to help.
Step 60: Let It Do What Airplanes Do Best
Sorry that it has taken so long to finally publish a video if it flying, but i did not have access to a paved runway while I was at college. Here is a video of the maiden flight of the airplane. I took it pretty easy just to get a feel for how it would fly. It had substantially better low speed performance than i was expecting, and was very maneuverable. All that is left is to hone in expo and duel rates to make it a little less twitchy, especially at low speeds. I hope you all have enjoyed the instructable and the video.
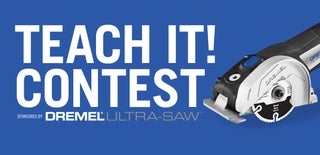
Second Prize in the
Teach It! Contest Sponsored by Dremel
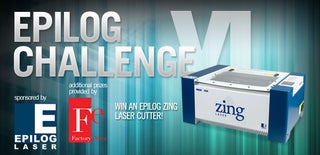
Participated in the
Epilog Challenge VI
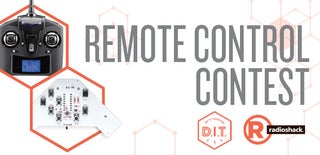
Participated in the
Remote Control Contest