Introduction: Designing/Repairing Household Items Using Fusion 360 (IKEA Desk Runner)
Hopefully this guide can give you the basics of how to design a replacement for any broken bits you've got in your home. The example I've used is a bracket for a drawer runner on an IKEA desk.
The metal rod runs through this bracket which has broken. I had a 10 mm diameter IGUS bushing so based my design around that.
Supplies
- Something that's broken!
- Modelling software (I used Autodesk, who offer free licenses for makers/education)
- 3D printer (or access to one)
- Calipers (optional)
Step 1: Identify the Problem
The plastic runner on my desk had broken, and spares are no longer available. Fortunately I had a bushing that was the perfect diameter for the rod to run through it, so I'll base my fix around this.
Step 2: Design Concept
Do a sketch of what your design will be.
Then take measurements from the existing part (as best as you can if it's in bits) and apply them to your model. I find this makes the modelling stage easier.
Step 3: Modelling 1
Model your concept! I've used Autodesk Fusion 360 for this, as it also has an integrated slicer which makes the next steps easier. If you know what you're doing with modelling, then feel free to skip to the next step. Otherwise, I'll go over the steps I took in modelling in further detail.
I started by modelling the basic outline of my model, then cutting the groove for the bushing to fit in. I used the centre of the bushing as the origin, and made sure all extrudes were done with the "symmetrical" operation. This way my origin remains at the centre of the part. This makes mirroring operations easier.
In other modelling software this feature may be called "mid-plane"
Step 4: Modelling 2
I decided to clamp the bushing with two M3 screws and brass inserts. I modelled the holes for the inserts to fit, and included a chamfer to make them easier to inset. I can't recommend this enough, so I'm going to say it again! Add chamfers to your holes! Using the mirror tool, it's then easy to make the change on both sides.
Step 5: Modelling 3
The walls at the side of the bushing were looking a little thin, so using the "press/pull" tool on either side of the part was a quick way to thicken them up. This is a much faster method than doing a sketch on the surface and extruding it (though you can also do it that way and that would be perfectly fine).
In other modelling software this may be called "move surface" or "move face".
Step 6: Modelling 4
I created the holes for mounting the part to the desk by coping the original geometry measured in the first step. I did this by doing a sketch that defined the hole positions with points, then using the "hole" tool. You could also do a regular sketch of the holes and cut through the part, but I find that using the hole tool is easier as you can select the counterbore and through hole all in one step.
I then realised that the walls I thickened in the last step were getting in the way of the screw holes, so I cut away some of the material above the holes, and use a mirror operation to get the feature on all 4 holes.
Step 7: Modelling 5
To make sure everything fits, I imported a model of the bushing from the IGUS website. Many companies have models of products that you can get to check for fits, which is worth your while when modelling components that are meant to fit together.
I then modelled the outside of the bracket in the same way as the first part, and added counterbored holes for my M3 caphead screws.
Step 8: Printing in Fusion 360 - 1
Now move across to the "Manufacturing" workspace to start printing! Create a new setup, select "Additive" as the process and pick a machine from the list. Many common machines are already built in to Fusion 360 including but not limited to:
- Anet A8
- Prusa Mini
- Prusa i3 Mk2, Mk2s, Mk3, Mk3s
- Creality CR10
- Creality Ender 3, Ender 3 Pro
If your machine isn't included, don't worry! Just select "Autodesk Generic FFF Machine" and enter your machine details on the "Edit" tab.
Step 9: Printing in Fusion 360 - 2
Move your model to where you want it and get the correct orientation with the "move" tool, then pick your print settings from the menu on the right.
I selected the honeycomb infil as I want this to be a strong part when loaded in all directions.
Step 10: Printing in Fusion 360 - 3
When you're happy with your settings, hit "generate" to create the toolpath. This is what would probably be called "slice" in most other slicers.
I'd then highly recommend checking the simulation of the toolpath, which is something that Fusion does very well. Whilst doing this example, I realised I'd forgotten to hit the "Place parts on platform" only after checking the simluation, and seeing that the start of my print begun with a load of support material!
If you're happy with the simulation, hit "Post Process" to create the GCode file, then get printing!
Step 11: Printing!
Get your GCode file to the printer how you normally do (SD card, Octoprint, Duet) and get going!
Step 12: Assembly - 1
With the parts of the printer, I did a test fit before adding the brass inserts. Use a low temperature soldering iron and push them in. The chamfer helps get them in straight.
If you don't have a temperature controlled iron, you can just turn on your iron and start pushing in the inserts immediately, rather than waiting for the iron to heat to full temperature. If it gets too hot, you can unplug it and keep going as it cools.
Be careful not to burn yourself! The iron, insert and surrounding plastic will all be hot!
Step 13: Assembly - 2
With the inserts in, I clamped the bushing and gave it one final check before screwing it into the desk. I'd recommend doing test fits at every stage as it means you can fix something at the soonest opportunity if it doesn't work!
Step 14: Success!
With the bracket fastened to the desk, I put in the rod and it all runs smoothly!
Hopefully by following this general advice, I've helped you fix something that's broken in your home using nothing but bits you have in your house, your 3D printer and Fusion 360!
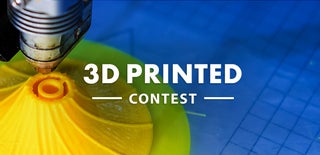
Participated in the
3D Printed Contest