Introduction: Desktop Ferris Wheel
To complete this project you will need the following items:
(3) Pieces of 12 in. x 12 in. sheet metal, any gauge will do
(2) Bearings with an inside diameter of 3/8 in. outside diameter of 7/8 in. and thickness of 1/4 in.
(2) Pieces of 12 in. x 12 in. plastic, any type will do
(1) Power drill with 1/8 in. and 3/8 in. and 7/8 in. drill bits
(1) 72 in. long piece of 1/8 in. brass rod
(1) 12 in. long piece of 3/8 in. brass rod
(1) Vise or clamp capable of making hems in sheet metal
(1) Band-saw or other cutting device to cut the plastic sheets
(1) Plank of wood 12 in. x 12 in. or larger to mount the Ferris wheel to
(1) Pair of aviation snips/sheet metal shears
(1) Hacksaw to cut the brass rod
(1) Bottle of super glue
Recommended:
Sheet metal brake to bend the sheet metal more accurately
Foot shears to make more accurate cuts in the sheet metal
Step 1: Cutting the Brass Rod to Length
Step One:
First, mark out (8) 5 in. long pieces of 1/8 in. brass rod. Cut out all 8 pieces using a hacksaw or another cutting instrument.
Next, Mark out (1) 7 1/2 in. long piece of 3/8 in. brass rod. Cut out the piece using a hacksaw or other cutting instrument.
Optional: Use sand paper or another sanding instrument to make the ends of the pieces smooth
Step 2: Cutting the Sheet Metal: Part One
First, take (1) piece of 12 in. x 12 in. sheet metal and mark out (12) 4 in. x 3 in. rectangles.
Next, use aviation snips/sheet metal shears to cut out the squares you just marked out.
After you have cut out the squares make the extra cuts using the diagram provided.
Next, make a 1/2 in. hem at the top of the piece (The bottom of the "T" shape) you just cut out and then fold up the sides.
Finally, check to make sure the hem is correct by suspending the piece from 1/8 in. brass rod. If the piece swings freely you have made the hem correctly.
Optional: Use a foot shears to cut out the squares more accurately.
Step 3: Cutting the Sheet Metal: Part Two
In this step you will cut the remaining pieces of sheet metal into 11 in. x 11 in. octagons. You will need to make (2) octagons.
First, cut the sheet metal into a 11 in. x 11 in. square using an aviation snips/sheet metal shears.
Next, cut the corners of the square so it forms a 45 degree angle, when the corners are cut they should look like the image. Cut all corners so the piece forms an octagon.
Next, Check to make sure all parallel sides are 11 in. away from each other.
Next, Mark out the 1/2 in. wide braces. The braces run through the center of each side straight to the center.
Finally, drill pilot holes using a 7/8 in. drill bit into the inside areas that form triangles. Be sure to avoid drilling where the 1/2 in. wide braces run through to the center. These holes will be used later for cutting out those triangle areas.
Optional: Use a foot shears to the piece to 11 in. x 11 in.
Step 4: Drilling Holes in Sheet Metal
First, drill a 3/8 in. hole in the center of each octagon. The center of this hole should be 5 1/2 in. from each side.
Next, take a ruler and mark out a line between where the sides form an angle on the outside and where the sides form an angle on the inside, use a pencil to do this so it can be erased later.
Next, drill a 1/8 in. hole using a 1/8 in. drill bit on the center of these lines. There should be (8) holes, each hole should be in line with another hole on the opposite side of the octagon.
Repeat these steps for the other octagon.
Step 5: Cutting Out the Plastic
First, Mark out two triangular supports on the plastic, the support is 8 in. x 7 in. cut out (2) supports from the 12 in. x 12 in. plastic sheet
Next, Cut out the supports using a band-saw or other cutting instrument
Next, Drill a 7/8 in. pilot hole using a 7/8 in. drill bit into the interior triangles formed by the sketch.
Next, Using a sharp cutting instrument cut the other interior triangles on the support.
Next, Using a 7/8 in. drill bit, cut a 7/8 in. hole at the top of the support, the hole is 6 3/4 in. from the base of the support.
Notes: The outside beams of the supports running up the sides are 3/8 in. wide. The beam running along the bottom is 1/4 in. high.
The top of the interior triangle is at 6 1/4 in. from the bottom of the support. The center beam runs from the center of the bottom beam and is 3/4 in. wide.
Step 6: Putting in the Bearings and Assembly
First, take the bearing and press it into hole you drilled into the plastic support. It should firmly grip the plastic, if not, you will have to find a way to secure the bearing in the hole, i.e. carefully gluing the bearing.
Next, begin assembly by sliding a side piece of the Ferris wheel onto the 3/8 in. brass rod. Leave this side 1 1/4 in. from the end of the 3/8 in. brass rod and super glue the side in place. Now, take the other side and slide it onto the 3/8 in. brass rod and super glue it 1 1/4 in. from the other end of the 3/8 in. brass rod.
Next, slide the 1/8 in. brass rod through the 1/8 in. holes in the sides of the Ferris wheel and super glue them in place.
Next, take the assembly you have created and slip each end of the (center rod) 3/8 in. brass rod into the bearings on each of the supports. Slide on the supports so that the end of the center rod sits flush with the face of the bearing. (So, that the rod end is even with the plastic support).
Next, glue the center rod as close to bearing as possible to prevent it from detaching from the supports.
Finally,Rest the sheet metal seats you made before onto the 1/8 in. brass rod so that they swing freely.
Notes: Glue the sides so that 1/8 in. holes line up on each side, this is most easily done by putting the assembly on a flat surface before gluing so that both the sides are in the same position.
Step 7: Final Step: Attaching the Ferris Wheel to a Surface
This step can be done multiple ways:
1. Super glue the structure to a surface of your choice, a wood plank is recommended so that the whole assembly can be moved later.
2: drill holes through the support directly into your surface.
3. using duct tape, this would not look good but it would work if nothing else is available.
Once the Ferris wheel is attached the project is complete and you should have a Ferris wheel that actually spins and should fit on the average desk.
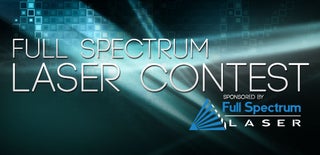
Participated in the
Full Spectrum Laser Contest