Introduction: Desktop Monitor Stands
I had recently moved into a new cubicle after moving to a different facility. Bigger space huzzah! But my desktop monitor layout wasn't quite working. I have three 24" widescreen monitors and one normal sized monitor. With the three widescreens spanning along the corner walls, my 4th monitor had to go behind my center monitor and sit on top of a box for me to use. I didn't quite like it (and sorry for no previous picture), but I knew I could improve the situation.
All the cutting/assembling work was done at a coworkers house. I had just moved about a month prior, so my workshop is mostly non-existent at this point. He has a much better setup and more tools available, plus has more experience for when I was doing things not quite right. Many thanks to him for his help.
Step 1: Design/Ideas
To start, it was important to define my area and what I had in mind. Being a mechanical engineer, I have plenty of experience with 3D modelling programs, so I went there to put my idea into reality (sort of) and figure out what I could do. I used Autodesk Inventor, but it really doesn't matter. They all work the same for this low-level type of project. I just find the layout for Inventor to be easier to use.
For this project, my three widescreens will act as my "main" monitors and will be arranged in a arch along the cube walls. My 4th, smaller, monitor will act as my "aux" monitor and will (hopefully) go in front and below my middle widescreen, simply leaning against the stands. At least, that's what I've pictured in my head.
The first part of this is to model the defining space and boundaries. For me, it is the corner piece of the cubicle desk, which measures about 45in x 45in (first picture). This will define how much space I can allow for these stands, as anything bigger will interfere with the cabinet and then be pointless.
Initially, I went straight into modelling the stands. After a bit of work, I realized there was no way to check my work as I was going. So I took a step back and went ahead and modeled the equipment I had (monitors, laptop, dock, phone, etc.) This would allow to properly account for everything I wanted to incorporate.
After modelling the desk surface, I was able to start playing with the layout and ideas for the stands. Since I knew all three widescreens would go against the walls, I could easily model based off of that. Due to the length I'm aiming for, it wouldn't be feasible to have one piece, but rather have three separate pieces. One piece corresponding for each main monitor, plus an extra something for my aux monitor.
The second picture shows the 3D modelling finished. I've attempted to account for every monitor, my laptop and dock, and my desk phone. I'll explain more on the modelling and dimensions in the next step.
Step 2: Modelling/Dimensions
As I mentioned in the previous step, I started with the available space on my desktop and modelled that. From there, I defined the stands legs and back, as this would create the footprint and support for the tops. I decided to have the backs encompass the sides. In hindsight, I should have done opposite and made the sides longer to cover the back. That would have hidden the sides of the plywood better. I used a veneer strip, so no issue ultimately.
Since I have three main monitors that are to be the same height and simply in a arc, the stands would have 45deg angles for the top pieces. This will allow the three pieces to come together and be 90deg total, since it's going into a corner. Using this type of geometry, I modeled the footprints of the legs and backs. After a few iterations of design work, I settled on the four inner legs to be about 2 inches shorter. This is helpful, as before I had them meeting at a point, which would prove to be a nightmare when building. As an added bonus, cutting them shorter helps to route cables between the inner piece :)
After the layout for the legs and backs are done, I determined I wanted them to be a height of 9in. This height would allow for my aux monitor to lean against it at approximate 45deg. Honestly it's all subjective and I had no idea what would work. But 9in looked alright and was easy enough to design/cut.
To finish the main parts, the tops are modeled based off the legs and ends of the desk. This allows the tops to fully encompass the legs/backs. No point in designing something nice when ugly ends show through. And the top is the main focus and work area.
This next part isn't necessary, as the design is finished and able to be cut. For detailing, I added the trim around the border of the top and the outside legs. This hides the end of the plywood, helps gives stability, and provides with a more professional looking piece. For my goal, I had to also add cutouts in the backs of the stands to allow for cordage. The right stand has a square piece cut out to allow for my laptop dock and cables to fit and run properly.
As far as the aux monitor goes, I modeled something just to have something modeled. When you see the finished pictures, I deviated from what I modeled. Mainly I just wanted to use from the scraps I had created. It turned out to be a plywood base with a short piece of trim nailed to the top. This creates a stop for the monitor to sit against.
After finishing the models, create drawings of the parts. This is an art itself, honestly. Try to figure out the best references to show to allow for anyone to cut the parts and assemble together. All lengths/widths/depths, details for cutting features, angles, etc. Taking time here to get it correct helps during the cutting process. I've attached the drawings I created based off my models.
Attachments
Step 3: Materials & Tools
Materials:
- It's your choice on what species of wood to use for this. I had talked with a buddy of mine who's more experienced and he suggested red oak. It looks great when stained, is available at Home Depot, and relatively inexpensive ($50 for a 4ft x 8ft sheet. I wanted this to look good, so red oak works for me. My design only uses about half the sheet.
- The trim is also red oak, simply a 1x4 8ft length that was ripped into two pieces at 1.5in wide. Home Depot had this as well, about $15 for the board. And had leftovers.
- Both plywood and trim board are 3/4" thick. Plenty strong enough for this application. 1/2" could have worked probably, but I like to over-design. Easier to work with everything being the same 3/4" thickness.
- Oak veneer edge strips. Already had a roll of the iron-on type. It's a tad wider than 3/4" to trim to match the thickness of the pieces.
- Plastic grommets (for cord management in top pieces (I purchased four, approximately $4? each I think).
- Cabinet door bumps (the name escapes me right now). They're to ensure the unit doesn't slide on the desktop surface.
- Pocket screws, I think I used the 1.25" long ones.
- Stain/paint of your choice.
- Poly sealer, if you decide to stain.
Tools: (not an exhaustive list)
As I mentioned, I was at a buddy's house working on this. He has a nice setup and plenty of tools at our disposal. What we used isn't meant to be a definitive list, but rather a guide.
- table saw (circular saw w/ guide could work for breaking down the plywood pieces)
- miter saw, for trim pieces
- hole saw, for the cable holes
- bandsaw (helps with the cable holes)
- random-orbital sander
- oscillating sander (helps with the cable holes/edges)
- brad nailer (18 gage brads at 1.5" long)
- Kregg pocket hole jig (I use the simple one that your clamp to the work pieces)
- Drill/Driver
- Iron and chisel for the veneer strip
- Squares/rulers/tape measure/etc.
I also used the program CutList to layout the parts on the plywood sheet to minimize the waste
Step 4: Cutting & Assembling
Sorry in advance for no pictures. It's all the same as any other woodworking project. Measure/cut/sand/assemble.
Using the drawings and cut layout created, roughly note where the pieces will go and break the pieces down into smaller, almost finished pieces. Finish all the pieces to their proper size.
I will note that we didn't follow the drawing dimensions exactly. Simply due to the geometry while modelling, some of the dimensions came out to fractions of 32nd. Which isn't practical for this. So we improvised and got close :)
I used pocket screws to hold all of the pieces together. Three on each leg to secure the back. Two on each leg to secure the top. Pocket screws are really easy to use and make a solid joint.
Iron-on the veneer on the exposed plywood edges of the inner legs and back pieces.
Initially, I wanted to use cam and dowel fasteners to join each of the three pieces together. This would make for easy disassembly/assembly of the three separate pieces once installed at my desk. However, after trying to layout the required dimensions for the pieces, it became impractical with what we had. So I used pocket screws, which means a little work to assemble the whole unit. Essentially, the legs/back of the center stand has to be taken off the center top so that the pocket screws can be screwed into the other top pieces. Then the legs/back assembled back into place.
When doing pocket screws for joining the three units together, ensure the tops are clamped flat to each other to ensure the pocket screws fasten and create a flat top surface.
The trim was cut piece by piece, ensuring each piece fit properly against the piece before it. The center stand was the first piece.
Step 5: Finishing & Detailing
From the beginning, I had planned to stain my finished product. I wanted to show off the wood grain of the red oak wood I used. But they could have been easily painted instead. Or neither and simply just sealed with poly sealer. That is completely at the discretion of the builder.
No matter what, proper detailing must be done to ensure a good finish. Sanding all the parts is important. Since most of the wood was relatively smooth to begin with, all I did was a pass with 150 grit on the sander, and then finished with 220 grit.
I used (funny enough) Red Oak colored stain from Minwax, as I already had it and loved the darker color it produces. I did two coats everywhere, except for the top surface of the tops. Those I applied an extra coat to hopefully give it a bit richer color.
After the stain dried properly (follow stain/sealer instructions), I applied three light coats of sealer, hand sanding with 220 grit between coats. This has given it a great reflective surface.
Install cable grommets into the tops to manage cordage from the monitors. Stick cabinet bumps onto the bottoms of each piece (I used 16 small clear pieces). This helps it not to slide everywhere.
Step 6: Final Product
All stained, sealed, and assembled at my cube at work. It all turned out great and has greatly improved my desk layout. Now everything is contained within these new stands and within reach, which has freed up desk space elsewhere.
First pic is the left stand
Second pic if the center stand
Third pic is the right stand
Fourth pic is the aux monitor piece
Fifth pic is the whole unit with everything rearranged in its place
-------------------------------------------------------------------- END --------------------------------------------------------------------------
I hope you've enjoyed my little project. I appreciate it if you've read through it all. If you have any questions about what I've done, or if I need to detail something I didn't mention, please let me know. Above all, thanks for looking and reading!
I have entered this project into the "Wood" contest, so if you really like it and think it worthy, please vote for me there!
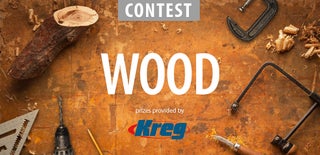
Participated in the
Wood Contest 2016