Introduction: Dial Indicator Using Compliant Mechanisms
Hi, I’m SunShine,
In this Instructables I’ll show you how I designed my very own 3D-Printable Dialindicator in Fusion 360 (However everything I’m going to show you is applicable for any type of CAD software).
This will not be classical step by step guide showing you what buttons to push to get the exact same results as I, but rather a deeper look into how one can use compliant mechanisms to create a tool that can help you measure things at a higher resolution then what your printer can print. I have already made a video on the subject that can be found here:
If you want to try it out for yourself, the files for the dial indicator will be at the end of this instuctables.
Supplies
Fusion 360
3D-printer
Step 1: What Is a Dial Indicator?
Before we start with the design process, what even is a dial indicator? A dial indicator is a device that is made to “indicate” a change in relative height or runout. We can for example use a dial indicator to make sure that the bed on a 3d printer is the same distance relative to the nozzle at every position, or that the workpiece is centered in the lathe.
Modern dial indicators can be used to measure how much run out, or how much deviation there is in a surface, however the main function of an indicator is to “Indicate” and not to measure, ideally you would adjust the things you want “level” relative to each other until there is no “indication” on the indicator, and then you would be where you want to be (even though admittedly it is nice to know exactly how much one needs to move things to be completely even).
Step 2: What Is a Compliant Mechanism?
In this guide, I’ll use a so-called compliant mechanism to create a dial indicator. Usually when we design things, we want them to be as rigid as possible. A compliant mechanism is the exact opposite, with a compliant mechanism we design the parts to bend and flex to create a desired movement or function.
While there are lots of factors that go into designing a compliant mechanism, you basically want to design the bendable parts within the elastic envelope of your material. That basically means you want the part to bend and jump back into shape, rather then bend and stay bent(or break). This is as you would imagine a very material dependent parameter, so you want to keep your desired material in mind when designing something to be a compliant mechanism.
Step 3: Mapping Out Movements and Ratios
When creating a measuring tool, you should make a drawing illustrating what the desired function is, and how you want your tool to function.
In my case, I want a very small vertical movement to translate into a very large swiping movement:
Remember to always think twice of what movement you want out of your compliant mechanism, you want to simplify the movements as much as possible, I really wanted a dial indicator that spins around 100 times during its entire stroke, but during the design process I realized that that would be difficult. I settled on a +/-20 deg throw on my indicator.
In the pictures you can see one of my early attempts at making a dial indicator with gears, you can see its very bulky and complicated compared to the final design.
Step 4: Design the Mechanism 1
This is the step that takes the longest.
Now that you know that you want do design the part as a compliant mechanism. In my case, I want to transform a small movement to a large visible indication. I start things out with a (reverse) Archimedes lever, here we can see that for the largest possible indication from the smallest change requires a very short “short side”. So knowing this we “re-create” this system in a 3d-printable system.
Step 5: Deigning the Mechanism 2
In theory you now have a compliant mechanism that will through flexing of the material create a larger throw. But as you can probably imagine, this is the part where the material properties come into play. Printed in pla, the early prototype design shown in the last "step" will either not indicate anything, or just brake. This is because we have not designed the “hinges” to be flexible.
If you think of a metal spring (one of the most common flexible constructions we have), you can see that it is effectively a long coiled up piece of wire. Without going into too much detail, a coil spring, when tensioned, is exposed to a torsional load. So if you imagine how the wire deforms along its length, you will be able to see that a wire that only has half its length will only be able to deform half as much. And a thicker wire will require more force then the thin one to deform more. (see drawing)
Step 6: Optimizing the Mechanism
The system i showed in "step 4" is the equivalent of a very short and thick “wire”, so if we want an indicator that has a lot of throw and with light actuation force we would have to make the “wire” long and thin.
The thinnest thing we can print with a 3D printer is a single layer high line that has the with of the nozzle. And this is exactly what we will use to make our compliant mechanism.
When modelling for a printer that is going to print 0.2mm layer heights and use a 0.4mm nozzle, you must design the "wires" to be 0.5mm wide, or else the slicer will ignore it and not print it. The length of them are tested through a little bit of trial and error, I wanted to keep the final design as compact as possible, so I decided to keep them around 8mm long.
To be able to print the strains of filament closer to each other without having to be worried about them sticking together, I designed them to be on staggered layers, theoretically with this setup I could even cross the two strains of filament and thereby flipping the Indicator direction. see pictures.
Step 7: Optimizing for 3d Printing
Now that we have the main mechanism working as intended, its time to start thinking about making the part usable, printable, and as durable as possible.
For the usability I decided to design the “stem” to be compatible with already existing dial indicator holders, this will make it possible to use this tool for different applications and different printers, since mounting brackets for classical dial indicators already exists.
For this I decided to retain the “Feeler pin” into the stem with the help of 45degree slopes and a 0.3mm clearance. (I already wrote an instructables on how to design parts print in place, make sure to check it out if you want more ideas on how to design parts that move relative to each other. Link to the Instructables- Print in Place Spring Loaded Box )
As you would expect, just a few very thin strains of filament don’t have a lot of structural integrity, so to improve the durability of the dial indicator, I decided to ad another compliant mechanism to the entire construction, this serves as a second pivot point that keeps the stem straight, and offers some over all strength improvements.
Step 8: Ideas for Your Future Design!
And that is it! Its as easy as that to get a surprisingly functional dial indicator out of your 3D-printer! I focused a lot on increasing the movement from an actuation, however, you can use a lot of the same technique to make tools that move objects in very small increments. A good example of this would be a mechanism that can move things ever so slightly under a microscope, AvE on YouTube did just that, and he did that with aluminium! :
Thanks for reading, feel free to leave questions in the comments.
The files for the dial indicator can be downloaded here.
You can reach me and find my work on the following sites:
YouTube - Instagram - Thingiverse - Cults3D - Facebook - Patreon
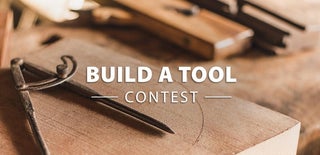
Participated in the
Build a Tool Contest