Introduction: DinoScope: Dinosaur Periscope - Made From Cardboard!
Combine the Science of Mirrors with the Rawesomeness of Dinosaurs - and you have the DinoScope!
This device not only allows the user to see around corners, above sofas, and under tables - but to do so in the persona of their favourite Jurassic terrible-lizard!
If you are a parent (or big kid at heart), this is a great project to take you through a whole bunch of cardboard modelling techniques I've picked up over the years of teaching workshops in Europe, through to making prototypes for some large companies you probably have heard of. More on that here: Design Modelling.
My love of cardboard started when I was a kid, and I recently filmed a TEDx talk about prototyping and design - and dug out an old photo from my family photos/cuttings - and it is shocking how much resemblance this DinoScope has to my first life-size T-Rex I made when I was 10 with my friend George.
Anyway, nostalgia aside, I hope you find those links useful and give context to why anyone would spend so much time working with cardboard. The answer for me is that it is a fast, abundant and cheap material to work in - and with a few techniques large builds can be done in a day or so that help you understand everything from ergonomics (how we use it), anthropometrics (does it feel right sized), feasibility (does it actually work) - and last but not least - is it fun!
Consider this Instructables a useful primer in how to model with card, to make sturdy toys/games/products, but also to enjoy the impermanence of it, and that after some good days or weeks playing, you may well remodel it again based on what you learned from making Version 1.0...
And lastly, without being too preachy, it's nice to give some life to cardboard boxes - and reuse/repurpose and avoid buying more short-lives plastic toys wherever possible. Please do also share any builds you make, and consider having a go at the DinoScope.
Supplies
Cardboard Boxes.
Ideally a mix of 2-ply corrugated (Apple Boxes, or White Goods boxes)
and 1-ply corrugated (Amazon boxes, etc.).
Suggested: A5-sized, 2-3mm thick PLASTIC Mirror (not Glass), Bosch Glue Pen, Cutting Mat and Scalpel.
Generic: String, Split Pins, Cocktail Sticks, Elastic Bands (optional), Ruler, Recycling stuff - plastic pots, etc.
*Safety Warning: Please do not make this project without adult supervision.
Although I can be seen working with my young son, I do not endorse this for any and all families to attempt. Although he is not left unattended with sharp or hot things, he has had years of growing up being used to 'not touching' certain things, and I'd suggest any parents new to this 'start gradually and calmly' and exert the same sort of rules you would if in the Kitchen around sharp and hot things also... You know your kids best - supervise as you see fit. I accept no responsibility for following this tutorial. But legal bit aside, I very much hope you enjoy it and find it bonding and/or insightful.
Step 1: Sketching & Thinking
You may not need to do this step, but whether you are a design student or a parent, I do recommend sketching out most ideas to think through how they will proceed.
Aside from it being a fun discussion with kids to discuss how the mirror will 'bend' light, it's still useful even for adults familiar with modelling to see how much they can accurately visualise and anticipate the steps...
...You may even notice in the sketch, I presume I'd use Elastic Bands to make the jaws open and close - only to realise that this is not actually necessary and actually impedes the play. Even LEGO-Alumni get it wrong! It's about the journey not 'being right' all the time ;o)
Also, if you look at many of my other Instructables - I do not use many measurements. This is not a lack of care to give you a PDF plan - but rather to illustrate how prototypers work at speed: The core 'technique' of speed-prototyping is to 'begin with the constraints'. So on this build, the 2x A6 sized mirror 'define the build', So I started with their dimensions as being the 'driving dimension' and everything else 'fits' around them.
(The alternative is to make everything else, and then have to carefully tailor the mirrors to fit - which will not only require more complex machinery, but also slow everything down).
From this, I build the scope, and from the 'Scope I built the Dinosaur head, from this I build handles, and so on. The core is the mirror(s) - the experience follows sequentially.
For more on this - also check out the Rocket Ship or Loop-the-Loop Instructables - here.
Step 2: Cutting a Plastic Mirror: Score 'n' Snap Method
This is a great technique to know, not just because it does not need a saw, but because it is arguably quicker.
The trick is to realise that you need to repeatedly score the plastic mirror enough times to be around 1/5 - 1/4 of the thickness, then place the score-line over the edge of a solid table, and press quickly and firmly down.
TIP: If you have never done anything like this, perhaps put on some gloves (DIY / Garden style), or place a tea-towel over it to avoid scratching yourself as the snap feels sudden if unfamiliar...after that it's like breaking a twig for a campfire - you know the 'feel' of it and it's easy.
Step 3: 45 Degrees
Continuing my 'no rules / measurements' philosophy, a simple way to avoid needing a protractor, is to just fold a post-it note (or piece of printer paper), as shown. This gives a nice 45 degree angle, and is useful to set the mirrors apart as shown.
The distance apart was simply a guess on what was practical for my son, and also what was convenient for the size of cardboard I had (ie no point in working in a 1.5x box size, as you'll have a lot of sticking together!). For the record, the distance was about 40cm.
Draw two parallel lines either side of the mirrors, and then draw perpendicular lines for the 'viewers' at opposite sides, as shown. Again, one can see this is done 'by fit', not by measurement - but its worth noting that the mirrors (outlines in black pen) have been given space of about 4mm around them - which is the thickness of the card.
Step 4: Flip 'n' Copy
With the 'Z' profile cut out, one could also carefully measure out, and duplicate, but for something this 'prototype-y', it's simpler to flip the card over and draw and cut around it to make the alternate side.
TIP: This also means if you have any imperfections, they are at least 'mirrored' so are less of a problem.
Step 5: OPTIONAL: Transfer Marks - Inside to Out
You may well have drawn the mirror markings/placement on the 'inside' of the card, and want to transfer them to the outside. This is because I realised the box had a lot of print on one side, and I missed this! So here's how to correct for that.
Simply 'stab' the edges of the mirror marking through to the other side. You can come back and cut these later. You might be wondering why not just cut the slot out now, but I feel this is a less 'stable' time to do it, so please bear with me, and it'll make sense later...
Step 6: Width of Mirror (Less 2x Walls)
Again no measurements - take the width of the mirror, and placing the two card 'side' flush with one edge, 'subtract' this dimension - and you're left with the width of the DinoScope.
This might seem obvious to many, but this sort of 'design around x' thinking, is key to making prototypes quickly when the dimension is not as important as the 'fit'. They objective here is for the mirror to fit flush with the outside of the 'box', no more, no less.
Step 7: Glue Together
Using your Gluegun of choice, apply a even bead of glue down one edge, and stick one of the walls to it.
Use a piece of paper, if you do not have a set-square for a 90 degree angle. Hold until set.
Repeat for the other side and add the back as well.
Step 8: OPTIONAL: Join Two Sheets of Card (to Make One Larger One).
As the first picture shows, you sometimes miscalculate things: Here I have a back of the DinoScope which is ~15mm too small. For a kids project, this is hardly a big issue, but it seemed an opportunity to show how to do an almost undetectable 'join' of two pieces of card. (I've used this in a recent Board Game mockup, and it was as strong, and almost impossible to see.)
- Gather your two pieces of card you wish to join. Ensure their corrugations (waved bits) are similar.
- Take some cocktail sticks and cut them in half.
- Apply glue to the inside of a corrugated 'hole'.
- Push in a cocktail stick, with the point facing outwards.
- Do this roughly every inch (or less frequent is fine).
- Check alignment.
- Push together - not all the way as shown.
- Apply glue quickly and evenly to the other side, especially around the areas where the stick inserts.
- Push together to set.
- Keep on a flat surface while setting.
You now have a larger / oversize sheet. And you can cut to the required size. Fit as shown.
Step 9: Complete Box Sections
You'll likely have offcuts left. Use these to add the final box sections as shown.
Note: You may notice that the corrugations are all in the same direction, but it does not matter too much, but is good to try if you can.
Step 10: Insert Mirrors
Cut the slots as shown. Insert Mirrors.
Tips: Hold knife as 'vertical' as possible, and cut from 'edges' first - inwards. It is better to have this a 'tight fit', as you can easily take off material, rather than add it.
Step 11: User Testing
This is what designers would call 'Proof of Concept' or 'Minimum Viable Product'....whatever you call it, the point is THIS is when you give it to your user to see how it works - before you commit a lot of extra work to it. You'll discover very quickly if something is wrong, feels weird, looks tricky, etc.
It's also not about always 'explaining it all' to them, but just observing how they interact - and play - with it to understand it...
...It was while doing this I expected my son to i) look above stuff, ii) look around stuff - but iii) look below stuff - I didn't actually expect! As a tall person, I had not considered the fun/merit in a 'bug's eye view'...THIS is why working with kids is great. You see new potential through their eyes.
Step 12: Coving Up
A little-known trick is that you can 'pull apart' the layers comprising corrugated card. The result is a strong high quality and flexible card top layer, which can be used to cover the edges of the mirror-slots, such that they do not fall out. (This also means that if you make a mistake you can remove the mirrors easily. Or if you wish to remove them to make a V2.0 or recycle it properly).
Lastly, the 'remainder' of the card is also a nice texture that can be used to create gears!
Step 13: User Feedback - Ergonomic Changes / Face Fitting
It's obvious when you see it, but a hard thin edge against your forehead is not that comfortable, and also means that a lot of light 'gets in', and makes the viewing experience less 'immersive'.
So it makes sense to borrow the 'face fitting' from VR headsets, and cut out a better profile.
To do this, I got a piece of paper and cut various profiles that iteratively fit correctly. From this I transferred this to the model, and cut out two sections. As you can see from the 2nd to 6th picture, the fit is far better.
Step 14: Handles
I also realised that although I had no trouble holding the DinoScope, my son's small hands couldn't manage this for long periods of time, so clearly handles were necessary.
Unlike the 'bug's eye view' moment, I was not surprised by this, and anticipated some form of grip would be necessary - but it was through watching him use it that I saw where he naturally *tried* to grasp the model. This told me where I should place them.
In truth, I would have assumed a little higher up, as this is closer to the 'centre of balance/gravity' of the model, but of course one thing you realise with kids is that they have shorter arms and bigger heads (relative to adults), so this is why the natural position is where it is.
I could go on here, but THIS is another reason I love working in card, as if I'd 3D printed this, I'd be less inclined to make such a change, as the work feels more 'finished', and would need reprinting, or would have needed the foresight to create adjustable position / screw locations, etc. In short: Card is quicker than pretty much any prototyping medium out there for models of this scale.
Step 15: Dinosaur Head - Investigation Prototype
"Investigation Prototype" - consider this the prototype for a prototype.
What I mean by this is that I wanted to get the proportions and mechanics/dynamics of the Head sorted out, but didn't want to risk using the thicker 2 ply cardboard, as I didn't have much left (hard to believe, but true).
So I used a cardboard packing 'envelope', from Amazon (not endorsed!), to sketch out an approximate shape of the head, and then checked it for fit to the Periscope I'd made already. The idea was to 'fit' around the top viewing port, and make this align with the jaws.
Teeth Tip: I realised that drew two sets of teeth, but actually it's better to cut from 1 line. Look at final pics and you'll see wha I mean. This means less cutting and a better end result.
I checked the jaw would open enough to 'see out of;, and also that the top jaws didn't get in the way. This soft of fine-adjustment is better done in a thin card, rather than 2 ply card!
I also realised that the upper port needed trimming to allow the jaws to open cleanly. See last photo. You may need to do similar.
Step 16: From Thin to Thick Card 'Dino Head'
With the Head prototyped in thin card, this meant I have a 'net' (plan) of what the form and fit should be. I transferred this into the 2 ply (thick) card - with a little extra room on the folds to allow the ticker card to bend around the corners.
- Net of thin card on thick card.
- Note rotation holes for lower jaw.
- Adding a 'Nose' to the top of the Head.
- Adding a 'gap' between Head//Jaw so they have some freedom to move (hatched line).
- I used a biro to 'score' the card so it folds more easily at the edges of the Jaws.
- Folding on the 'inside' to keep the outside clean.
- Final 2 pieces. Ready to fix to the Periscope...
Step 17: Test-Fitting the Head & Jaws
Although one could use measurements here, the 'teaching' I'd like to share is how to work symmetrically in a prototyping medium. The trick is to use simple references, and 'tests' to check fit.
- End result shown. Held in place with cocktail sticks.
- Checking viewing region around mouth.
- Checking view from Viewer.
- Take a half-cocktail stick and stab through the card jaw, into something soft like a cork mat, or tea-towel.
- Next insert this into the approximate position on the Periscope. Check how the jaw moves when open-closed. Mark max/min positions with pencil.
- Use these markings as a guide to fit the Head - with enough clearance not to 'jam' the Jaw.
- Take a post-it note, and make a reference of the hole, taking two other 'datum' marks as shown.
- Transfer this to the opposite side of the Periscope, and punch a second hole...now the side of the Jaw should align.
- This should now work on the other side.
- And teeth should align.
Step 18: Jaw Movement With Split Pins
Attach with Split Pins either side as shown.
I've pushed the 'legs' to the outside, and will later glue over with a layer of card...
Step 19: Glue Head
Attach the Head as shown.
Tip: I marked the overlap area with pencil first to avoid any mis-alignment issues.
Check everything moves nicely.
Step 20: OPTIONAL: Jaw Stop-Out
You might have noticed the saw looks a bit 'too open'. This is not a big deal, but one that is easy to fix with a 'stop-out' detail, using two cocktail sticks (or you could glue card also).
Step 21: Nose Job
Finishing up the profile of the nose, you can see I cut some card to size, and then bent it to fit nicely. I removed the edges for a better fit. If you're interested, here's how to do the technique. LINK.
I also reinforced the nose with some small pieces of card as shown.
Step 22: Back of the Head
Here I needed to add some more card to the back of the Head.
You can used the 'flush join' method, as shown in earlier steps, or just simply glue another piece on and not worry about the details.
The key tip if to 'mirror'/copy the left and right sides, so it is equal.
Add some 'cross braces' to the back of the Head also, as it will help on the next step...
Step 23: Dino Dome
To create a 'curved' surface you may want to pre-flex the card, over your leg, or a tube - it makes the whole process easier. A Pro Version of this can be found here: LINK. I suggest switching to 1-Ply Card now...
The trick is to glue a little at a time - but on both sides. So apply glue for say 50mm / 2" on either side, and then glue down. Follow this from the 'Nose' to the back of the head. I suggest 'fitting' the Nose-to-Head join first, as this needs to be glued as shown, by scribing and fitting (ideally - but not critical). Add a fillet of Glue to close any gaps.
Step 24: Here's Looking at You
The eyes are a pretty expressive part of a character, and I confess I'm nowhere near as skilled as some of my friends who are illustrators, but I went for a Walt Kelley -inspired look from Pogo. (EG). With the eyes in the 'human' position, rather than at the sides, like on a real crocodile. It's odd to contemplate how many cartoons 'tweak' such features like this without us giving it a second thought...
Anyway, these are made using techniques shown here: LINK. And are done using 1 Play Card.
The 'Eyes' are made form toilet tubes, and have a recessed section of about 5-7mm deep. This is useful if you want to do the 'googly eyes', (see later steps after painting), but are not essential.
Step 25: Original Punk
Adding some nice 'spikes' is a nice and easy detail.
Pro Tips: You may notice that by 'alternating' the cuts, I have no waste, and this is an efficient way to cut a lot of things out quickly. Secondly, I've tapered the strip (2 Ply), so as to make the spikes get smaller. Thirdly, I've aligned the corrugations such that the glue will flow into the 'base' of the spikes, and also that this is a stronger orientation to glue on. These are all 'non-critical' tips, but I point them out for those wanting to dial it in a bit more to make better models.
Step 26: The Big Belly, Jaws and Tongue Finishes
Using the earlier technique of 'peeling off the top layer' of card, this is a cool way to make a 'feature' of the card to add texture.
The leftover is now used to cover up any imperfections - like the 'legs' of the Split Pins.
Likewise, I made a Tongue too.
Step 27: Roooooooooaaaaawwwww!
Done.
This is good to play with, and I'd suggest you let kiddo play with it vigorously - as it will expose any weaknesses or limitations of your design, before you commit to painting it.
Step 28: Extra Details: Nostrils, Jaw Details, Arms
The Nostrils are similar to the Eyes, in build technique.
I removed the excess from the Jaw to emphasise the teeth more.
And added some 'Arms' to cover the handles slightly and make it more 'realistic'.
...Ready to Paint?!
Step 29: Pre-Painting Tip: Cover the Mirrors!
I strongly recommend covering up the Mirrors with some paper and masking tape.
Even if you're painting it yourself - but especially if you have kids doing it!
Step 30: Painting!
Even if you had to do a lot of knife-work yourself, this is where I let my son go wild!
No rules, just have fun.
Two coats are advisable. I used basic 'school pre-mixed paints'.
Step 31: Roawsome!
Left to dry near a warm radiator etc.
But is it missing something? Does it need to be more characterful??
Step 32: DIY: Googly Eyes!
I used some clear plastic from packaging, and a black plastic coco powder lid. But any clear/black combo will do.
I cut out 2 small and 2 large circles as shown.
TIP: I traced the clear circles as shown with a pen.
I glued these in with Hot Melt as shown.
Step 33: Careful Now - Don't Get Eaten!
Have fun, and if you enjoyed this, please check out more here:
http://www.judepullen.com/designmodelling/
and
https://www.instructables.com/member/Hey%20Jude/in...
Thanks
Jude
PS - If you liked it, please consider voting and/or sharing a picture if you made it!
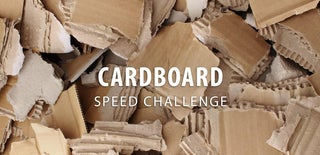
First Prize in the
Cardboard Speed Challenge