Introduction: Dirt Cheap Forge
I thought I'd throw in a link to THIS VIDEO where I revisited this concept but didn't take any time to make it nice, so it turned out crude but effective. I had money this time, so I just bought charcoal.
If you read my Instructable about making charcoal, then you know that I am on the path of making a froe, for free. The forge is the heart, which I guess would make the anvil the lungs. . . or would it be the other way around? Either way, the forge is important so I set out to build a dirt cheap forge. I didn't want to spend any money, so making my own refractory from kitty litter and plaster of paris was out, I don't have a break drum kicking around, so that was out. However, I do have soil that is extremely high in clay content, and maybe it will hold up to the heat. Let's find out.
Step 1: Stuff You'll Need
Clay soil, I would highly recommend not using sandy soil as it won't hold its shape, nor would I recommend rocky soil as rocks can explode when heated due to trapped water. This forge is not very durable, if you are going to buy stuff to make a forge get supplies to make a refractory, there are tons of recipes, instructables, and videos on the 'net on how to make your own.
A Shovel, although, I guess you could dig with a stick
Something to haul the dirt in, I used what I call a rough tote, a bucket would work to
A beating stick, I used a leftover scrap from a sledge handle I had cut down
A place to put your forge, I used a piece of scrap plywood and two by fours to make it moveable.
A section of metal pipe, mine is from one of those canvas carports, it broke years ago; I think with some ingenuity a series of tomato paste cans could work, just cut both ends off
Something fire resistant, preferably round, and with a bit of height, I used a flower pot, that I mutilated. you could also use a soup can. . I think
An air supply, I used a shop vac, I recommend something lighter powered, maybe a hair dryer
A hack saw
A small piece of flashing
Tin snips, heavy scissors might work.
Tape, I used duct tape to attach the shop vac hose to the forge.
Optional:
A garden cart or wheelbarrow, it makes hauling easier
A lantern burning citronella oil, I was working in the evening and the mosquitoes are already starting up.
A file
Step 2: Dig!
I had a mount of nice clay based soil I dug up about a decade ago when trying to build a pond as a kid. I've spent quite a bit of effort filling that hole back in, but there was still some dirt piled up. I scrapped off the organic matter and tossed it into the hole, then dug out the dirt, a bit of organic matter won't hurt, just not too much.
I tried to keep the soil fairly level, but if you're just digging a pit have at it.
I filled my rough tote about half full, which was about twice as much as I ended up using.
Step 3: All About That Base, No Trouble
In addition to the tools and materials I listed earlier I used :
scrap 2x4, scrap plywood, some screws, impact driver, hand saw, vise, pencil, combination square, tape measure, and a snap line. I didn't list them before because this step if fully optional
Alright, a forge needs a base, but if you want you can plop it on the ground. My forge has to be able to move, I hunted through my scrap wood pile and came up with a partial sheet of 3/4" plywood and a 42" length of 2x4.
I cut the two by in half . . .no I didn't, half would have been 21 inches, I was so busy trying to take pictures I somehow managed to cut it 20" long, so I cut the other one the same length and it worked out, because the ply was about 20" wide.
set the 2x4s on the ground, set the ply on top and sunk a screw at each end of the 2x4 then snapped a line across the screws and put in a a few more screws. it probably would have been fine with just two screws each as it's only dealing with compression stress, I tend to either over build sometimes.
You might have noticed I inset the 2x4s a few inches on the sides, that way I have a grip all around the forge to pick it up.
Alright, the base is done! now for the hard part
Step 4: Building Up the Forge Underlayment
From here till I was done with the clay/mud I had to release my inner Hulk and smash.
Bassically, using fist sized clumps of mud/clay I set them on the board and pounded them flat. I started by using my fist but started getting tired quickly so I used a stick, actually a piece of a sledge hammer handle. I ended up with about an inch thick oval of compacted soil.
Step 5: Starting the Bottom of the Fire Pan
Continuing the smashing style of construction I built up a layer around the edge. I was kind of figuring this out as I went along, I had an idea of what I wanted to do with it, but I was kind of letting the materials guide me.
Step 6: Air to the Coals
I needed a place for the air to come up into the forge, I knew I was going to feed the fire air via a pipe, but I needed a place for that air to come up in.
I initially thought of using just plain dirt, but I wanted to lend some rigidity the structure here, so I chipped out a section of a small flower pot.
Step 7: Pipe It to Make It Hot!
I used a section of pipe I had laying around for this step, I also used a little bit of flashing material to make a blast gate. I will leave the pictures to do most of the explaining.
One neat trick I came up with, I needed to cut the pip half way through for the blast gate, so I took a piece of string, wrapped it around the pipe, marked a point on the overlap, then I took it off, folded it and marked the bottom of the fold. When I rewrapped the string, making sure my original marks met, I had two marks equidistant from each other and I sawed to them.
Step 8: Build It Bigger, and Make a Fire Pan
With the pipe in place I started laying down more mud/clay up to the level of the flower pot rim, then I built a wall around the whole thing to keep the coals in.
Step 9: Cleaning Up the Surface and Making a Fire Grate
I used a shovel to clean up some of the edges around the base, then I cut some hardware cloth to create a grate. I'll be honest, the grate was a waste of my time, the heat ended up deforming the grate and the coals were actually in the flower pot. I think that actually worked out alright though.
The takeaway, don't make a grate like I did, infact, maybe don't make a grate at all.
Step 10: Low Temp Heating
I wanted to dry out the clay/dirt as much as a I could before I fired up the forge for real. so I built a small fire and let it burn out. as I expected, the dirt cracked quite a bit, but not too much. success so far!
Step 11: Forging Ahead! Well, a Froe, But That's a Different Instructable
After itching to use the forge for a couple of days I gathered my forging supplies
railroad track Anvil
shop vac with blower
Leather boots, cotton pants and cotton shirt (synthetics can melt to your skin)
Quench bucket, preferably metal
And of course my charcoal of which I prepped a quad batch
It's really hard to take pictures of myself forging, so there is only one picture of me hammering. I was attempting to make a froe from an old lawnmower blade. I am hoping to finish up that froe, and maybe create an instructable for it at some point.
It's a good thing I had the blast gate because the shop vac was way too powerful for this little forge.
Step 12: Final Thoughts
The forge worked quite well, the only really important changes would be to remove the grate, and use a lower power blower.
I expect this forge will last a few more forges, but the flowerpot is already starting to melt.
I wasn't able to get a forge weld on the froe, but I think it's because it was too bright outside and I couldn't see the colors of the steel.
That thing ate charcoal like candy. I had about 2 gallons of charcoal I'd made and I burned through it in about 20 minutes, I think it might have been because of the air supply being so forceful.
This was my first forge build, and for the cost ($0.00) and time (about 2-3 hours) I put into it, I call it successful I did get steel hot enough to shape, and it was a decent sized chunk of steel too.

Participated in the
Apocalypse Preparedness Contest
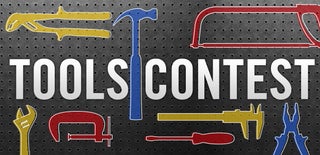
Participated in the
Tools Contest