Introduction: Diving Mask With Custom Add-on Lenses (V2.0) Made Using Photogrammetry
After having used my custom-made diving mask frame with the add-on lenses, I started finding that there was room for further improvements. These added features would facilitate the construction and make the overall use of the add-on lens frame more convenient to use while diving.
Thankfully, in recent times there have been great advancements made in the field of photogrammetry which have made this technology accessible to virtually anyone with a smartphone. Add to this the reduction in the costs of 3D printing and the combination of the two has offered the right opportunity to take my custom-made diving mask frame with the add-on lenses to the next level.
In the following steps I use some of the latest technologies that are now available to all to remix and transform the first version into a superior and more pleasing result!
The link to the first version: https://www.instructables.com/id/Diving-Mask-With-Add-on-Lenses/
Step 1: Remixing Version 1.0 to 2.0
In the previous version (1.0) I had found the following difficulties while making and also when using the mask frame.
Shortcomings in V 1.0
Construction difficulties:
- The 2D, flat, planar surface of the acrylic sheet provides limited possibilities to add more features and elements to it.
- The mask frame supports (Step 16) are designed by taking visual measurements and are therefore inaccurate. Because of these inaccuracies the shape of the supports don't match the shape of the mask and don't get glued properly. I had to re-glue the supports a few times before they got firmly stuck.
- Aligning all of the 4 frame supports on the mask which has irregularly shaped surfaces was challenging.
- Because the frame supports are permanently glued to the mask, the mask gets permanently altered and can't be used as a "regular mask".
Utilization difficulties:
- Moving and sliding the lenses up and down the slot in the frame requires the use of both hands - one hand to loosen the butterfly nut and the other to hold the lens frame.
Improvements in V 2.0
Construction improvements:
- By designing an add-on mask frame that closely matches the shape of the diving mask, we get a 3D shape which offers us many more surfaces and areas to add features and elements to the frame.
- An add-on mask frame that closely fits the diving mask does not need to be permanently fixed or glued to the mask as it's holds itself in place.
- The add-on mask frame can be added and removed without making any changes to the diving mask.
- The availability of larger areas on the mask frame, on the sides and the back of the frame, provides the space to add elements to fasten the mask frame to the diving mask and also add a mechanism to slide the lenses up and down the face of the mask.
Improved usage:
- A mechanism to slide the lenses up and down the face of the mask and with the use of just one hand has been added making the adjustment of the lenses extremely convenient.
Step 2: Using Photogrammetry
One of the challenges of designing an add-on frame to a diving mask is the irregularity of the shape of a diving mask. The shapes of a typical diving mask are mostly curved with complex three dimensional forms. This makes it difficult to take those measurements of a mask that would be required to design a closely matching frame.
The difficulty of taking measurements of a mask can be overcome with the use of photogrammetry where one can directly recreate a virtual 3D mesh of the mask that closely matches the real mask without having to take any measurements.
Moreover, photogrammetry has become greatly user-friendly and anyone with a smartphone or any other camera can take photos of almost any object and obtain a virtual 3D mesh of that object with the clicks of a few buttons. There are several software that offer photogrammetry for free and as this field is advancing so rapidly I suggest that anyone who wants to try it can look up the latest versions that are available online.
For the use of photogrammetry in this project, I watched a few videos on how to take the photos of my mask so that I could get a fairly accurate 3D mesh of the mask. Briefly, the important things to keep in mind are the lighting of the object, reflections from the object and making sure that there's sufficient overlap between successive photos.
I didn't bother too much about the lighting and just used the natural daylight light in the room while keeping all the lights in the room on. Some of the photos came out a bit dark, but it didn't seem to matter too much. To remove the reflections from the mask I sprinkled some talcum powder on it and spread it all over with a paint brush. I took as many photos as possible from all the angles, about 120 photos which were probably more than necessary, in order to make sure that the photos overlapped each other. The photos were then fed into the photogrammetry software which created a sufficiently accurate 3d mesh of the mask.
Step 3: Reverse Engineering the Mask's Profile
Once you have the 3D mesh of the model of the mask, you can use the mesh to recreate and reverse engineer the exact 3D shape and model of the mask in a CAD software. It is not necessary to be extremely precise while modeling and deviations in the range of +0.5 mm to 1.0 mm are acceptable. The model of the mask has to be larger than the mesh because otherwise he frame will not fit the mask.
It is important to bear in mind that the mesh of the mask is not to scale. To scale the 3D model that has been created so that it matches the actual mask, I used the same method of scanning, tracing and creating a 2D sketch that I used in steps 2 and 3 in the V 1.0. The 2D sketch is to scale and the 3D model of the mask frame that has been created can be scaled so that it matches the 2D sketch.
Step 4: Creating the 3D Model of the Mask Frame
Once the 3D model of the diving mask has been created, it will serve as the base model around which the mask frame can be modeled. The mask frame has to make contact with the front and on all of the sides of the diving mask, with the allowance of a few millimeters. The mask frame can be attached to the mask either with a strap or with an attachment that is fitted at the back of the mask frame and which holds it onto the mask.
The mask frame can be modeled by offsetting the surfaces of the diving mask by about 1 mm so that we are sure that the mask frame is larger than the diving mask. These surfaces can then be thickened externally to create the solid 3D model of the mask frame. One can use one's imagination and design sense while creating the mask frame.
For instance I tried to maintain the design and profile of the original mask as much as possible and I added some space for a hole at the top so that a mount for a compact underwater camera such as a GoPro can be fitted onto the mask frame.
While modeling the mask frame, it is not necessary to be too precise as long as the 3D model of the mask frame is larger than the diving mask. A few millimeters here and there in excess don't matter that much. The idea is to make an external frame that fits onto the diving mask.
Step 5: Linear Guide Mechanism for Lens Movement
To improve the ease of moving and sliding the lenses up and down the frame, a geared mechanism with a pinion that moves on a linear guide with a rack, was conceived. Essentially, by turning a knob which is connected to the pinion, the lens can be moved up or down the rack, with just one hand. To keep the lens sliding mechanism in its place a locking mechanism has also been incorporated along with the knob. This has greatly simplified the minute adjustment and positioning of the lenses.
The travel length of the linear guide mechanism is determined by the position of the eye in relation to the mask and also the shape of the mask, in my case I needed a travel length of 3 cm. This was covered in steps 2 to 6 of the V 1.0.
Step 6: Materials Needed
- 3D Printing Filament (PLA) - as the parts in this project won't take much load I would recommend to use PLA due to its facility of printing. One can choose their preferred colour of filament, I decided to go with black as it would seamlessly integrate with the colour of my existing mask.
- 3D Printer - Creality Ender 3 highly recommended.
- M5 Bolts x 8 - I tried 3D printing the bolts but they were not strong enough. I would advise using stainless steel bolts as seawater is unforgiving and will quickly corrode any other metal. You will require 4 bolts to be of length 1 cm and the other 4 to be of length 3 cm.
- Clear Acrylic - 3 mm thick clear acrylic sheets will be required for encasing the lenses, as was done in V 1.0.
Step 7: 3D Printing Specifications
All the parts have been modeled with respect to ease of 3D printing. A considerable amount of time went in designing the parts keeping in mind the structural strength of the parts as well as the feasibility of 3D printing. Ideally, I would have liked to print fewer parts, but I had to split some of the parts into smaller units because it was not possible to print those parts in one go.
I have sliced the model in a way that no component has any overhangs and thus can be printed without supports. The complete list of the parts with their 3d printing specifications (stl's and g-codes) are in the file above.
Step 8: Tolerance Test Sample
The key to a well functioning mechanism, is finding the right tolerances. It took me several prototypes, from fits being too tight to components being too loose, to finally achieve the correct tolerances. Unfortunately tolerances depend on the precision of the 3d printer being used and thus might need to be altered for specific printers. I used the Creality Ender 3 to print the parts using tolerance of +0.25 mm while friction fit parts were of +0.1 mm. These settings lead to successful results.
Therefore to analyse and gauge the required tolerances I have prepared a test print file of the section of the mechanism. This way one can prototype faster and have less waste. Once you have achieved the wanted results you are ready for the next steps.
Step 9: Mask Frame From Photogrammetry
Thanks to the advancements in photogrammetry and its increased user-friendliness I was able to create a sufficiently accurate add-on frame for my mask that fitted it closely. Additionally, I find that it also looks better than the acrylic frame in V 1.0.
Step 10: Mounting the Guide Rails on the Frame
Press fit the four threaded inserts on either side of the frame, by gently tapping the inserts with a mallet. Once the insert is flush with the side of the frame, screw on the Linear Guide Rails on each side of the frame with the M5 3D printed screws.
Step 11: Assembling the Linear Mechanism
The rack can be slid into the Linear Guide and held in a place with a bit of CA glue.
The Lens Slider is prepared by inserting the knob in its hole and joining it to the pinion. The locking bolt is then inserted through the knob and joined to the locking plate.
Step 12: Gluing the Lens Holder
This step is identical to Step 10 of V 1.0 and the photos are self-explanatory. It is important to ensure that the lenses and lens covers are clean before gluing because once glued the lenses and the inner surfaces of the lens covers are inaccessible. One should also be careful not to smear epoxy on the lens covers because it is virtually impossible to clean it later on.
Step 13: Assembling the Lens Rotating and Blocking Mechanism
The assembly of the Lens Rotating and Blocking mechanism is similar to Step 14 of V 1.0 except that I have now given the provision to add two more of the movable, sliding teeth that block the gear in place. This has been done to reduce the amount of play that there was in the V 1.0 and to make the lens frame more firm. Although in V 2.0 I can fit 4 teeth I found that the mechanism worked sufficiently well with just 3 teeth.
The Lens Frame with the Rotating mechanism is then assembled to the Lens Slider mechanism.
Step 14: Attaching the Fastening Blocks
The modular Fastening Blocks that are required to attach the mask frame onto the mask are best fitted from the front of the mask frame with the 4 M5 stainless steel bolts.
I chose to have modular blocks instead of having blocks that are an integral part of the frame because the modular blocks can be modified to have side mounts for a torch or an accessory that one may want to add to the side of the mask frame. Modular blocks can therefore be easily interchanged and they add greater versatility to the mask frame.
Step 15: Mounting the Frame to the Mask
The mask is now ready to be inserted into the frame and the two can be fastened to each other by bolting the two straps to the fastening blocks at the back of the mask. The bolts are tightened till the frame is firmly fixed to the mask.
Step 16: Assembling and Using the Lens Frame and Sliding Mechanism
The lens frame with the lens sliding mechanism can then be inserted into the linear guide. The ends of the linear guide can then be closed with the plugs to prevent the slider from sliding out of the linear guide.
The last image describes the lens sliding mechanism and how it's used.
Step 17: The Modular Mask of the Future
The creation of a customized mask frame with the use of photogrammetry has allowed me to increase the functionality of my ordinary, conventional diving mask. I can now add movable prescription lenses and various kinds of accessories such as mounts for cameras and flashlights which add greater value to the experience of diving.
Step 18: Acknowledgement
This project would not have been possible if I was not introduced to the latest developments in photogrammetry that my son, Satya, shared with me. Moreover, his invaluable experience in 3D printing was indispensable for the execution of this project. Finally, his photographic skills and documentation also came in handy.
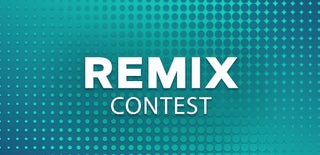
Participated in the
Remix Contest