Introduction: Do Nothing Box EZ 3D Print
Some don't get it. Others laugh hysterically when they see this machine in action. It is a simple project to build, and watching others enjoy the absurdity of this box is as pleasurable as it was to build. Enjoy. Vote. Share.
I saw one of these "Useless Box" years ago. I thought it was one of the funniest things I had ever seen. Recently I was introduced to 3D printing and my first idea was "I can now have a Do Nothing Box of my own."
After a few attempts at hiding the hinge failed, I designed it without a hinge. Now, by just looking at the outside it is not as telling what the power-on switch will do.
Step 1: Purchased Parts
Purchased parts are as follows.
Battery Pack: Purchased from Amazon; http://www.amazon.com/uxcell%C2%AE-Battery-Holder...
I paid $1.93 US, The current price as of April 2016 is $3.65 US. For 5 parts.
Motor/Drive: Tamiya 72004 Worm Gearbox High Efficiency Kit, Amazon.com. $10.51 US. Free shipping. Slow delivery. (I didn't include a link here because so many options come up with the search, I couldn't remember where I ordered from, save that it was China, I think)
The fastest (not the cheapest) came from Hobbylinc.com (Never any problems with these folks)
Micro Switch: Purchased for a different project in bulk. APX $0.88 each. Lots of available options. (Note: Some options only have one pole. Be sure it is a Normally closed pole)
Toggle Switch: Purchased from Radio Shack $3.99 US. Radio Shack part #275-0666 Catalogue # 2750666 (Best search criteria on radioshack.com)
Grommets: Purchased from McMaster Carr Bulk. Pack of 100 @ $4.68 =.0468 A piece Part # 9600K38
Total purchased parts price for this project: $15.82 US.
I used speaker wire for the wiring and two screws from my junk drawer that are not included in the above list. You will see that explained in the following steps.
Step 2: 3D Printed Parts
The external box and components of this build are designed to be printed with minimal support material if oriented in their proper axis.
3D print the components needed to assemble the "Do Nothing box".
These components are:
(1) Body 01.stl
(If needed, the optional Body no text 01.stl is included. It has the raised text removed so it will lay flat on the build plate)
(2) Lid 01.stl
(3) Finger 01.stl
(4) Batt box 01.stl
(5) Base 01.stl
Step 3: Assemble the Tamiya Gear Box
Assemble the right angle drive gear box, Tamiya 72004 Worm Gearbox High Efficiency Kit, for
the lowest gear ratio and most torque as per directions. 336:1. Using the Green, Red, and Gray Gear.
After the gear box is assembled, you will have to remove one side of the drive shaft. One way to do this is with a cut off wheel of a Dremel tool. Take care to do the cut slowly with intermittent cuts so as to not overheat the drive rod so that the plastic stays cool and maintains structural integrity of the plastic frame.
Step 4: Mounting the Finger Part One
Place the serrated pin into the shaft and Mount the plastic
indexing piece (Part A2 Drawing 6)
Note: I left the DC motor unconnected to allow me to turn the shaft freely until I assembled all of the parts to the drive.
Step 5: Mounting the Finger Part Two
Using the extra screws, not needed from the motor kit, attach the Finger 01 to the part A2 Drawing 6. Pay special attention to the direction of the finger that will correspond with the switch. For the distance Between the part A2 and the housing of the gear box, I used the width of a nickel. This will insure the finger hits the switch properly. Another reason for leaving the motor unattached until the distances are correct so that you will be able to adjust, with the set screw, the side to side to strike the toggle switch properly.
Step 6: Mounting the Drive to the Box
Mount the drive to the underside of the box.
Using, again the screws left from the motor assembly. Decide the proper drill to use to create a tight fit for the motor to mount to the underside of the box. (The holes are purposely printed small to allow for drilling to any screw available, plus the small amount of heat created should shore up the edges of the hole for better retention.)
Step 7: The Micro Switch
The micro Switch.
The design of the print is set up to place the micro switch in the proper orientation. The design of the part is also set up to use as little support material as possible. The indent holes (2) on the outside of the box are included in the build to help guide a drill to allow room for the tool (A Phillips screwdriver) to reach the screws straight-on so that the micro switch can be tightened and assembled for maximum efficiency. The two screws for mounting the micro switch are the only two, that will have to be sourced. I was lucky enough to find two in my junk drawer that were the same thread as the included nuts with the drive kit. (McMaster Carr has the part needed, but only in a pack of 100. It would benefit you to find a compatible screw from another source even if you have to drill a little bit larger hole, in order to save a buck or two.) Pleas note the orientation of the micro switch in the video for proper mounting.
Step 8: Wiring
This is the most difficult part of this project, and is yet still pretty simple.
Using the DPDT (Double pole Double throw) switch allows the reversing of current flow. The soldering skills needed for this project are minimal, but because of the tight fit between the bottom of the toggle switch and the micro switch, plus the home position of the finger, the tabs will have to be bent down after the wires are soldered in place. No room for sloppy soldering here.
For different levels of skill and experience here, I am including pictorial and schematic pictures, plus a long winded description. Choose your favorite method for interpretation.
Wire (4) The crossover.
Cut to length, a wire to create a diagonal path across, Blade (4) to Blade (3) Solder with Wire (3) at Blade (3) and solder the single end at Blade (4)
Wire (1) Micro Switch Common.
Cut to apx 3". Solder one end to Blade (1)
Wire (2) Motor Red
Solder the Red wire from the motor to Blade (2)
Wire (3) Micro Switch (NC)
(See "Wire (4) The Crossover")
Wire (5) Motor Blue.
Solder the Blue wire from the motor to Blade (5)
Wire Connection (7)
Wire (6) Joins to Wire (7) at the micro Switch terminal (NC) to Batt (-)
Connections to the Micro Switch:
I used female Blade connectors with a crimp end to make these connections. You can do the same or simply solder the connections.
Wire (7) with Wire (6) to Micro switch terminal (NC)
Then Wire (7) to Batt (-)
Wire (1) from toggle switch to Micro Switch (Common)
Step 9: The Battery Pack
Using the four way drive from the drive kit and the extra screws, assemble the Batt Box 01 as shown. This unit will slide into place and be secured when the base is in place. Again the screw holes are printed small to give you the choice of screw size, and will need to be drilled accordingly.
Step 10: The Test Run
Do a test run. With the toggle switch in the Off position. Activate the switch to the ON position. The motor should start and the finger deploy to push the toggle switch into the off position, reversing the current. The motor should continue to operate until the cam of the finger hits the micro switch to open the circuit and come to a stop.
Step 11: Install the Lid and Base
The sliding lid is of a delicate nature, and should be inserted gently. Pushing the "legs" gently inward until they snap into place. An earlier version had a tighter tolerance and required a little sanding and lubrication to fall back into place. I have solved this with the wider lid as you may notice the original video shows a bit smaller opening than the lid with this print.
My first installation was an excited, exuberant hurry that led to a broken part. I learned from my mistake and have not had a problem sense.
One more test run before installing the base, along with the grommets that will need to be pushed into the four holes at the corners.
The bottom has a detent for a screw to insure the screw will not be higher than the grommet feet.
Step 12: Final Step Final Thoughts
I have not included every step, such as installing the batteries. The short video is much better than I, at explaining the assembly of this super fun box. If a picture is worth a thousand words then a video must have an exponential ratio to words. Being a maker, I am sure you were a step or two ahead of me before I got to the point.
After designing this box, I saw a kit that uses a different setup than I do. At first, I thought the compact design of the kit was an ingenious design, until I remembered the reason for my design (where the finger hits the micro switch as a cam) was to prevent the momentum of the gear drive from pushing so hard on the switch that the flex of the plastic would quickly fatigue, causing failure. My design allows for the drive to come to a stop without putting pressure on the micro switch mount or pressure on the drive gears within the transmission. It is my opinion that the cam design will add many more cycles of this box than a design that slams the finger into the micro switch. However, with the cam design of this box, it is very important that the cam on the finger strike and engage the pin on the switch as fully as possible and the micro switch be mounted firmly. If any current change apparatus fails at any point in the cycle, I would imagine it would make a horrible sound as the drive gear attempts to tear the box apart, causing embarrassment to the party intent on impressing their friends with this DIY machine and its humorous absurdity. I sincerely hope you have fun with this project, and can carry it even further.
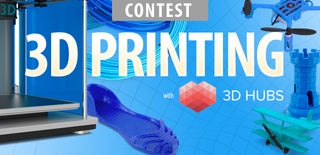
Participated in the
3D Printing Contest 2016