Introduction: Dowel Jig
I wanted a dowel jig but i didnt want to buy one because they were more money than what made sense to me. I didnt want a self centering on. I just wanted a simple one for large 1/2" thick panel boxes. So i decided to make one.
FYI I made it at TechShop
Material:
Tools:
FYI I made it at TechShop
Material:
- 1/2" aluminum at least 2.5" x 2"
- #10 x 32 screws
- 1/8" thick plastic that is at least 2.5" x 4"
Tools:
- Saw
- Mill
- Parallels
- Center drill
- Edge finder
- 1/4" drill bit
- #32 Drill bit
- #10 x 32 tap with handle
- End mill
Step 1: Cut and End Mill to Size
i started by cutting my stock to the right size. I over size it by 1/16" so i have room to mill. If you stink at cutting give yourself more. You can always remove more material on the mill.
I then milled down my block to 2.5" on the end. The reason i did this is because my stock is "flat" on the ends touching the vise. This should give me a "Square" part. The reason for the quotes is because its all about what your tolerance is. I used parallels to keep the part level off the vise bottom. then i used my 3/4" end mill to side cut on it. I took 0.015" passes with conventional cutting. I used the Y axis which didn't have a power feed so i hand feed it at 6-7in/min. This gave me pretty good results since i would come back at a slower speed to cut a little more and remove any deflection i got on the initial pass. I used an RPM of 800.
I then milled down my block to 2.5" on the end. The reason i did this is because my stock is "flat" on the ends touching the vise. This should give me a "Square" part. The reason for the quotes is because its all about what your tolerance is. I used parallels to keep the part level off the vise bottom. then i used my 3/4" end mill to side cut on it. I took 0.015" passes with conventional cutting. I used the Y axis which didn't have a power feed so i hand feed it at 6-7in/min. This gave me pretty good results since i would come back at a slower speed to cut a little more and remove any deflection i got on the initial pass. I used an RPM of 800.
Step 2: End Mill the Top and Bottom
i end milled the top next to get it down to the 2" dimension. I took 0.015" thick passes with a feed rate of 6-7in/min again. just used the bottom of the cutter. for the last pass i took 0.003" and feed it at 3in/min. I used an RPM of 800 for all of the passes. gave me a much better surface finish. (I hate sanding)
Step 3: Drilling Main Dowel Holes
I put the part in the vise so i couldnt drill into the parallels when the drill bit went through. Many ways to do it. I then edge found the corner i wanted to start from. I ran the edge finder at 1000RPM. Then i moved the mill to the first hole location. I started with the center drill. I ran this at 1000RPM. this is just to start the drill bit in the correct location. Makes it so any alignment issues with the drill bit wont cause a problem. I then switched to my 1/4" drill bit. I ran this at 600RPM. I did peck drilling with some coolant. I didnt have any better cutting fluid on me so i used what i had. Worked like a champ. I then went to the next hole location and did it again.
Step 4: Drilling Holes for Tapping
I next drilled the two holes i needed for tapping. I rotated the part in the vise. So i used the edge finder again. Same RPM. Then i used the center drill again at the same RPM. Then used the drill bit i needed for my #10x32 tap. if you want to used a different screw because you dont want to buy one then just adjust according. I then moved the mill and re-center drilled/re-drilled.
Step 5: Tapping Holes
i used a #10 x 32 tap to tap the holes. I did this in a regular vise. I used tapping fluid too for this. If you were to make this jig out of plastic instead of aluminum i would use vegetable oil. Else tap magic works great. or WD-40 for those people too cheap to get the correct thing. Be careful to get the tap straight!!!! if you break your tap you will be pissed. I would also make sure to tap it all the way through. Makes the jig symmetrical and also makes it so you are not limited to one size bolt.
Step 6: Making Plastic Piece
You could make this piece any way you want. You could also use a lot of other materials. I chose plastic so it wouldn't mark the wood. I made mine on a laser cutter because i got lazy. You could easily make it on the mill. i would recommend that you use light weight materials for this. No reason to ding up your wood when you drop your jig on it. Also you can make spacers for this so you can center your jig on thicker material. Spacers could also be washers.
Attachments
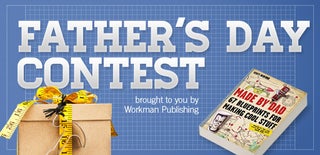
Participated in the
Father's Day Contest
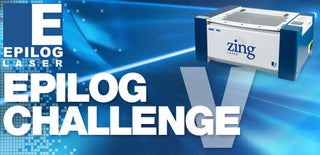
Participated in the
Epilog Challenge V