Introduction: Drone Design 101 - Part 1 CAD
Build! Fly! Compete!
Aerial Sports League Founder / Chief Designer and Autodesk Expert Elite, Eli DElia, walks you step by step through the basic principles and techniques of First Person Video (FPV) drone racer design.
Be sure to watch theattached15 minute Drone Design 101 CADvideotutorial.
Then apply your own creativity to create your own brand of racing drone!
For this Instructable you will need AutoDesk's Fusion360.
• Download your own free copy of Fusion 360 here:
• When setting up use the promo code:
MAKEYOURMARK
Step 1: Creating the Motor Component Plate - Motor Mounts:
1. Launch Fusion 360
2. In the Model Module / Sketch Menu / Create New Sketch.
3. Select the bottom plane so your view orientation is facing down.
4. Sketch / Center Diameter Circle. From world center draft a 210 millimeter circle. Drag out and input 210 mm in the diameter dialog box.
5. Sketch / Line Tool. Draft a vertical line from center to just past the top of the circle perimeter and hit “X” on your keyboard to convert the line to a construction line.
6. Sketch / Line Tool. Draft out a horizontal line from center to just past the right of the circle perimeter and hit “X” on your keyboard to convert the line to a construction line.
7. Measure out a 45 degree arc from the center vertical and horizontal lines.
8. Sketch / Line Tool. Draft another line tool between the two and type in 45 degrees. Hit “X” on your keyboard to convert the line to a construction line.
9. Select the Circle and hit “X” on your keyboard to convert the line to a construction circle.
Note: When drafting out a Motor Mount it is key is to assure that the motors are equal distance or square from each other.
10. Create the motor mount, Sketch / Center Diameter Circle. From the 45 degree line intersection draft out a new construction circle and input 25mm. (almost 1 inch)
11. Use the 25mm dimension line as a guide, adjust so it is perfectly vertical.
12. Create a center circle which will become a hole to allow the motor’s drive shaft to spin freely.
13. Sketch / Center Diameter Circle. From motor mount circle center draft out a new circle and type in 5mm.
14. Sketch / Center to Center Slot tool. Using the 25mm dimension line as a guide, draft a slot just off the center motor shaft circle. Type in 4mm in width.
15. Adjust the top and bottom arcs to allow distance from the top circle perimeter and the cent circle diameter.
16. Right drag select the motor mount slot.
17. Sketch / Circular Pattern Tool. From the tool’s dialogue box check to be sure all 11 elements of the slot tool are selected. Click on center point and select the motor mount circle center point.
18. Change the default setting from 3 to 4 and click ok.
19. The 1st motor mount is now complete with a motor screw layout to allow good wire flow from the motors to drone center where they will connect to the Power Distribution Board (PDB).
20. Right drag select the complete motor mount.
21. Sketch / Circular Pattern Tool. From the tool’s dialogue box check to be sure all 48 elements are selected. click on Drone Center Point, change the default setting from 3 to 4 and click ok.
- The result will be motor mounts that are perfectly square.
Step 2: Creating the Motor Component Plate - Component Plate and Motor Booms:
1. Sketch / Center Rectangle tool. From drone center draft a rectangle, type in the values of 160mm vertical by 45mm horizontal. click ok
2. Sketch / 3 Point Arc tool. From upper left Motor Mount, in line center with the bottom slot tool, draft a 3 point arc down to the bottom left motor mount, in line center with it’s top slot tool, click and drag the arc to just touch the center component plate rectangle.
3. Repeat the process for the right side.
4. For top and bottom arcs use the circle construction line as a guide. Draft a new arc from top left motor mount to the correspond position of the top right motor mount and drag the arc in to the center rectangle as illustrated.
5. Repeat the process for the bottom arc to complete the motor boom layout.
6. To add more creative control over your design it is good practice to now Tangent Constrain the arc tool points to their motor mounts.
7. Select an arc tool, from the Sketch Pallet click on Tangent Constraint and select a motor mount. Repeat the process for all remaining arcs by re-selecting the arc / tangent constraint, select the corresponding motor mount.
8. You may have to adjust your arc. Click the arc and drag it to the original position. Tangent Constraint allows the center to move independently of the top and bottom arc points, resulting in more fidelity of your design.
9. As a rule the motor booms width should not be much more than the propellers, for a racer of this size that equals 12mm.
Step 3: Creating the Motor Component Plate - PDB and Stand Off Hardware Holes:
Drafting the Power Distribution Board hardware holes:
1. Sketch / Center Rectangle Tool. From drone center draft out a square and type in the values 30.5mm x 30.5mm, click ok.
2. Select the lines of the rectangle and hit X on your keyboard to make a construction square.
3. Sketch / Center Diameter Circle Tool. From the corner of the construction square, draft out a 4mm circle. Click ok. right drag select the new circle.
4. Sketch / Rectangle Pattern Tool.
5. Select the horizontal arrow handle and type in a value of -30.5mm. Set the quantity value to 2. Select the vertical arrow handle and input a value of 30.5mm x a quantity of 2. hit return to complete the process.
Repeat the process for the stand off hardware holes:
6. Sketch / Center Rectangle Tool. From drone center draft out a square and type in the values 145mm x 45mm, click ok.
7. Select the lines of the rectangle and hit X on your keyboard to make a construction square.
8. Sketch / Center Diameter Circle Tool. From the corner of the construction square, draft out a 4mm circle. Click ok. right drag select the new circle.
9. Sketch / Rectangle Pattern Tool.
10. Select the horizontal arrow handle and type in a value of -45mm. Set the quantity value to 2. Select the vertical arrow handle and input a value of 145mm x a quantity of 4. hit return to complete the process.
-This completes the basic sketch for the Motor Component plate.
11. Next extrude the plate to create geometry. Adjust the view by click and dragging the View Cube.
12. Modify / Press Pull Tool. Or Q on your keyboard.
13. Select the Motor component plate. The selected elements will turn blue. Avoid selecting any hardware holes.
14. In the Press Pull Dialogue box enter a value of 3mm, click ok.
Step 4: Round Off the Corners and Hard Edges:
1. Modify / Fillet tool or use hot key F. Zoom into the sharp corner where the Motor Booms meet the Component Plate.
2. Select each corner of the airframe.
3. In the Fillet Dialogue box enter a value of 5mm. Click ok to complete the process.
4. Repeat the process rounding out the component plate’s sharp edges.
5. Hit Hot Key F and select all four corners of the component plate, in the dialogue box enter a value of 5mm. Click ok to complete the process.
Note: It is crucial to round off any sharp edges with a fillet of 5mm in order to add significant strength and durability to an airframe. Sharp corners and edges create potential breaking points in a harsh crash. Crashing is unavoidable in drone sports so take steps in the design stage to increase your airframe's longevity.
Step 5: Creating the Top Component Plate:
In the Browser Hierarchy Menu / Sketch, Right click the sketch and select Edit Sketch.
FPV Camera Bracket Slots:
1. Sketch / Center Point Slot Tool.
2. In the center forward section of the airframe use the construction guide lines to draft out a Center Point Slot. Input a value of 1.5mm. Hit return.
Battery Strap Slots:
3. Sketch / Center Point Slot Tool.
4. Using the construction lines on the right, center frame, draft out the center slot tool and make the thickness value 2mm.
5. Adjust the length to be 30mm. using the Center Slot control line adjust it so the center point rests on the airframe’s center construction line. Be sure to give it enough room from the the edge and away from the screw holes.
6. Right drag select the new slot tool.
7. Sketch / Rectangle Pattern tool. Select and drag the horizontal arrow handle into the airframe. In the Rectangle Pattern Tool dialogue box, enter a value of -39.5 and a quantity of 2.
8. Select the vertical arrow handle, drag down and enter a value of -50 and a quantity of 2. Click OK to complete the process.
FPV antenna hole:
9. Sketch / Center Diameter Circle Tool.
10. In the rear section of the airframe, from center of the construction guide line. Drag and enter a value of 6mm. Return to end the process.
Cut in additional holes to reduce airframe mass:
11. Sketch / Center Rectangle Tool.
12. From airframe forward center, draft a rectangle and enter the values of 25mm x 25mm. Hit enter to complete the process.
13. Right Drag select the new square.
14. Sketch / Rectangle Pattern Tool.
15. Using the vertical arrow handle drag and enter a distance value of -100mm with a quantity count of 3. Hit return to end the process.
This completes the Top Component Plate sketch. Use the View Cube to adjust your view to a perspective.
16. Modify / Press Pull Tool or hit hot key Q.
17. Select the new component plate sections. Extrude to a value of 1.5mm in the dialogue box, hit return to complete the process to create the new geometry.
18. Browser Hierarchy / open the Bodies menu and select Body #2.
19. Modify / Move Tool. Drag the new body geometry up to a value of 25mm.
Round out the sharp edges:
20. Modify / Fillet Tool.
21. Select all 4 corners of the new component plate’s perimeter. In the Fillet Tool dialogue box enter a value of 5mm, click ok.
22. Repeat the process for the corners of the square within the Top Component Plate w/ a Fillet radios of 5mm.
Step 6: FPV Camera Bracket Slot and Making Revisions Without Modeling New Geometry:
1. Browser Hierarchy / Sketches, click the light bulb to make the sketch visible.
2. Use the View Cube to orientate the window to view the sketch looking up words the bottom forward of the airframe.
3. Modify / Press Pull Tool or Hot Key Q.
4. Select the forward FPV Camera Bracket slot and drag up so a red ghosted slot cuts through the bottom airframe. Hit Return to complete the process.
Modifying the model’s geometry
The bottom Motor Component plate is now complete however there may be feature you wish to add or adjust to your airframe design. This is a very simple process to accomplish. By simply modifying the sketch your geometry will update accordingly. For this example adjust the FPV Bracket Slot from one long slot down to two short slots.
5. Browser Hierarchy / Sketches / Sketch1 right click Edit Sketch.
6. Select the forward most line of the FPV Camera Bracket slot and hit hot key D to Dimension the slot. Drag out the Dimension box and enter a value of 6mm and hit enter. The slot then updates in size.
7. Right drag select the slot.
8. Sketch / Rectangle Pattern Tool. Select and drag the horizontal arrow handle and enter a value of -15mm and a quantity value of 2. hit return to complete the process.
9. Stop Sketch. Notice how the model has updated with the new, modified slot.
10. Use the View Cube to orientate the perspective looking up from the sketch.
11. Hit Hot key Q and drag out the new slot so it cuts through both top and bottom plates. Hit return to complete the process.
Step 7: First Person Video (FPV) Camera Bracket:
1. From the Browser Hierarchy turn off the light bulb icons for the geometry.
2. Sketch / Create New Sketch. Select the Forward view Plane.
3. Sketch / Center Rectangle Tool.
4. From world center click and drag out then enter a value of 23.614mm x 27.014, hit return.
5. Sketch / Center Diameter Circle.
6. From rectangle center, drag out and enter a value of 16.789mm.
7. Sketch / Center Rectangle Tool.
8. From the top center of the rectangle click and drag out, enter a value of 4mm tall x 10.16mm wide.
9. Repeat this process for the bottom center of the rectangle.
10. Sketch / Two Point Rectangle Tool.
11. From the top right corner click, drag out and enter values 2mm x 3.58mm hit return.
12. Repeat for the remaining three corners.
13. Sketch / Center Rectangle Tool.
14. From top center of the rectangle drag out so it cuts through bot the top rectangle and center diameter circle, tab down and enter a value of 3mm. Hit return to complete.
15. Hit Hot Key Q for the Press Pull Tool. Select the new Bracket sketch drag and enter a value of 1.5mm. Hit return to complete.
16. From Browser Hierarchy select the new bracket body.
17. Modify / Move Tool.
18. Drag the new Bracket into place so it fits into the top and bottom plate bracket slots. Adjust geometry to fit.
Step 8: Done!
Your new 210mm FPV Racing frame design is complete and ready for CAM or 3D printing. Be sure to save your work!
For 3D printing select a frame body model and click the Make menu button / 3D Print to send it to your 3D Printer's set up software or Autodesk's Meshmixer. Repeat this process until all 3 airframe parts are ready to print.
Next Instructable will cover CAM set up specific to this project.
I hope to have inspired you to expand on this with your own designs and compete your own FPV Racers.
Do watch the video for any clarifications. Please Subscribe, like and share.
This 210 FPV Racer is best fitted with the power train components listed below
Drone Power train:
- 4 x 2204 / 2100 kv Motors by RCManChild
- 4 x 22 Amp RCManChild ESCs
- Power Distribution board w/ built in BEC
- Naze32 Flight controller w/ "Borris B." firmware programmed on Clean Flight.
- Orange 6channel RC
- FPV kit (Camera, 5.8gHz Transmitter, Antenna)
- Turnigy 3cell, 1800 Lipo Battery.
Additional Drone Hardware:
Pilot:
- FatShark FPV Goggles
- Orange 6 Channel Radio Controller
- Lipo Battery Charger
- Metric tool kit
- Drone Back Pack
Next episode, Drone Design 101 Part 2 - CAM, will walk through the steps taking this airframe into Fusion360 CAM module and prepare it for carving with the CNC router.
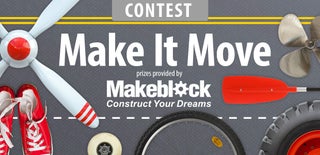
Participated in the
Make it Move Contest 2016
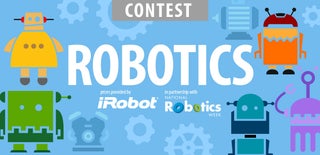
Participated in the
Robotics Contest 2016